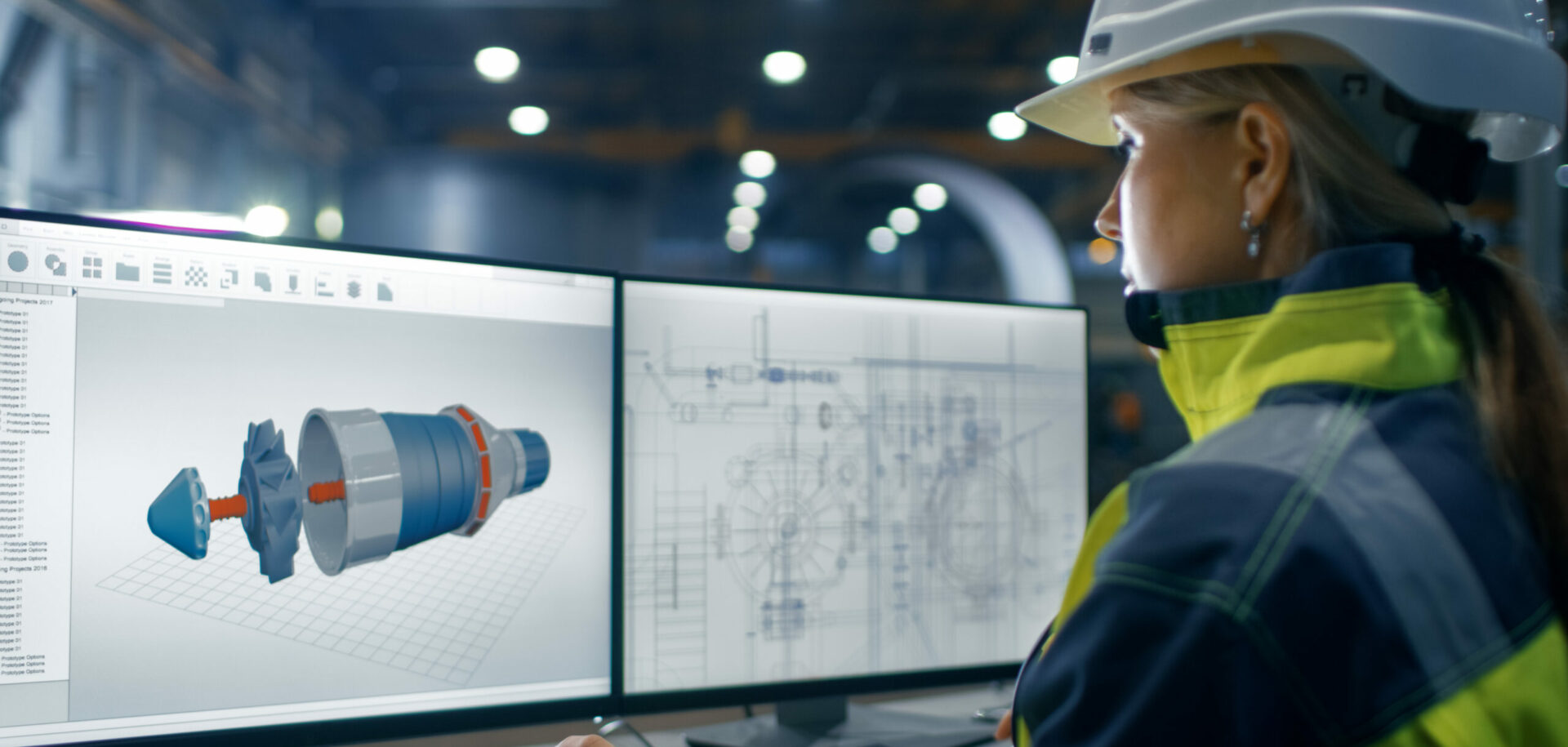
Sviluppi nelle sfere in ceramica per cuscinetti
La necessità di trovare soluzioni nelle turbine a gas di tipo avanzato aveva inizialmente portato allo sviluppo di corpi volventi in ceramica da impiegare sui cuscinetti. Ora tale impiego si sta sempre più estendendo ad altre applicazioni, quali i mandrini per macchine utensili e i motori e i generatori elettrici.
Sintesi
Più di 400 anni fa le prime sfere non metalliche prodotte in larga scala erano quelle usate come palle da cannone, come zavorra o per i giochi dei bambini. Con l’avvento negli anni ‘60 e ‘70 delle nuove ceramiche tecniche, questi prodotti per umili impieghi si sono trasformati in sfere ad alte prestazioni per cuscinetti destinati ai motori a getto e commercializzati per i mandrini delle macchine utensili, i motori elettrici, le auto di Formula 1 e le pompe.
Recenti impieghi dei cuscinetti ibridi li troviamo nell’industria ferroviaria e nei generatori eolici. La SKF resta in prima linea nello sviluppo, nell’industrializzazione, nell’applicazione e nella standardizzazione delle sfere in ceramica per cuscinetti. Il lavoro di sviluppo è tuttora in corso, specialmente per quanto riguarda le sfere di grandi dimensioni. Sfere in nitruro di silicio con diametro fino a 47,625 mm di diametro sono già disponibili in commercio. Per quanto riguarda i nuovi materiali ceramici, esiste l’opportunità di adattarli alle specifiche applicazioni, con vantaggi in termini di costi e di ambiente grazie ai processi meno energeticamente dispendiosi, previsti per le nuove unità produttive che devono soddisfare le crescenti richieste di questi nuovi materiali.
Contatto vendite
Oscar Schöppl, Oscar.Schoeppl@skf.com
I cuscinetti ibridi, che sono caratterizzati da corpi volventi in ceramica, si impiegano in svariate applicazioni molto impegnative. Quelle più recenti le troviamo nell’industria ferroviaria e nella costruzione dei generatori eolici.
Il nitruro di silicio, Si3N4,, è il materiale standard, conforme alle norme internazionali attualmente impiegato per i cuscinetti volventi; i metodi di prova e ispezione previsti (fig.1) tengono conto della tendenza verso sfere di grandi dimensioni. Oggi sono normalmente disponibili in commercio sfere di alta qualità in nitruro di silicio con un diametro di 47,625 mm (1 7/8”) (fig. 1, nel riquadro).
Le sfere in ceramica, pietra e marmo hanno una lunga storia di impiego, dalle palle da cannone alla zavorra e, naturalmente, ai giochi dei bambini. Lo sviluppo della ceramica tecnica sintetica negli anni 60 e 70 ha portato alla fabbricazione di sfere in nitruro di silicio per cuscinetti ad alte prestazioni, destinati a vari prodotti, dai motori per aerei, ai mandrini per macchine utensili, ai motori elettrici, alle vetture di Formula 1, alle pompe, ecc. L’attività di sviluppo è tuttora in corso, specialmente del campo delle sfere di grandi dimensioni.
Sviluppo e applicazioni delle sfere in ceramica per cuscinetti
Alla base dello sviluppo delle moderne ceramiche tecniche c’è stata necessità di creare motori per turbine a gas veramente efficienti. Le condizioni di lavoro dei cuscinetti dell’albero principale sono estremamente gravose, con velocità di rotazione superiori a 30.000 giri/min e temperature che possono superare i 650 °C [1]. Con temperature del gas oltre i 1.100 °C, sono accettabili solo materiali ceramici ad alte prestazioni più duri degli acciai per cuscinetti o anche della stellite ad alto tenore di cobalto o delle leghe di acciaio con alto tenore di tungsteno. L’impiego principale delle turbine a gas è quello sui motori a reazione, applicazione che richiede materiali leggeri (di bassa densità), ma altamente resistenti e in grado di far fronte alle alte temperature oltre che di soddisfare ulteriori esigenze quali rigidezza, lavorabilità e disponibilità.
È noto che i materiali ceramici soddisfano i primi due requisiti, ossia bassa densità e resistenza alle alte temperature, ma è altrettanto noto che sono deboli e fragili. Nelle ricerche condotte nel settore spaziale e della difesa si è cercato di scoprire il perché di tali punti deboli e il modo per superarli. Le teorie, i metodi e i processi che ne sono derivati hanno portato a ceramiche migliori e a nuovi materiali sintetici, quale il nitruro di silicio. L’SKF Engineering and Research Centre (ERC) in Olanda ha lavorato intensamente sui materiali in questione sin dai primi stadi di sviluppo.
Il nitruro di silicio è uno speciale materiale ceramico con proprietà autorinforzanti. Le sue due fasi, la fase alfa e la fase beta, presentano una forma cristallina diversa, una delle quali costituita da aghi allungati (fig. 2). Durante la lavorazione, per ottenere un materiale tenace, si può regolare l’equilibrio tra le due fasi. Il primo nitruro di silicio disponibile commercialmente, dotato di una robustezza e di una tenacità idonee alle applicazioni dei cuscinetti è stato il nitruro di silicio HIP (Hot Isostatic Pressed, ottenuto da pressione isostatica a caldo).
Nel corso degli anni 60 e 70 la società SKF Marlin Rockwell Corp. (MRC) progettò i primi cuscinetti in ceramica. Nell’ambito di un programma sperimentale, finanziato dal governo degli USA, la MRC fabbricò un cuscinetto ibrido con anello interno diviso. Nel 1984 la SKF dimostrò la possibilità del nitruro di silicio di operare a lungo in un cuscinetto esposto a temperature oltre i 500 °C con l’impiego di lubrificanti solidi [1].
Attorno agli anni 90, in parallelo con i programmi spaziali sperimentali, l’industria delle macchine utensili iniziò a sfruttare i vantaggi offerti dalla leggerezza e dalla capacità di affrontare alte velocità delle sfere in ceramica. A metà degli anni 90, nei motori elettrici, a seguito dell’impiego dell’elettronica a commutazione rapida nei convertitori di frequenza, si verificarono danneggiamenti nei cuscinetti standard dovuti a passaggi di corrente. Per tali casi i cuscinetti ibridi rappresentarono una solida alternativa alle soluzioni tradizionali di isolamento. Quasi nello stesso tempo molte soluzioni con cuscinetti ibridi vennero introdotte nelle vetture di Formula 1, per sfruttarne la robustezza in presenza di lubrificazione marginale e carichi elevati. L’impiego dei cuscinetti ibridi nelle pompe e nei compressori arrivò attorno al 2000, permettendo condizioni di lavoro con lubrificazione marginale e applicazioni in cui sono ammessi lubrificanti con viscosità inferiore a quella degli oli, quali i refrigeranti. Inoltre, l’eccellente resistenza alla corrosione della ceramica ne ha favorito l’impiego nei compressori di gas con alto tenore di zolfo. Recentemente, la ceramica ha trovato impiego nei generatori eolici, applicazioni in cui si richiedono sfere con 47,625 mm di diametro (fig. 1, nel riquadro). Nell’industria ferroviaria si sta estendendo l’impiego di corpi volventi in ceramica nei motori di trazione (fig. 3); in tali applicazioni l’isolamento elettrico e la migliore prestazione di questi componenti in presenza di carichi relativamente leggeri aumentano la durata del grasso, in quanto si genera meno calore per attrito.
Valutazione delle sfere in ceramica per alte prestazioni
Una vasta gamma di applicazioni possono trarre beneficio da cuscinetti con sfere in ceramica. Per essere certi che i materiali ceramici per le sfere dei cuscinetti assolvano il loro compito in maniera ottimale è necessaria molta attenzione e a tale scopo sono state previste particolari procedure di prova.
In generale, una prima valutazione si può fare controllando la macrostruttura (fig. 4, in alto), la microstruttura e l’omogeneità (fig. 4, al centro) su campioni sezionati di materiali grezzi o finiti mediante lucidatura. Anche la durezza (fig. 4, in basso) e la resistenza alla frattura causata da impronte possono essere determinate con relativa rapidità.
Per determinare la resistenza delle sfere in ceramica finite sono stati elaborati nuovi metodi. Specialmente nei materiali ad alta resistenza, si è visto che influisce molto la qualità superficiale, e quella delle sfere per cuscinetti è molto migliore di quella di una barretta campione da sottoporre a piegatura. Il test con sfere incise (notched ball test, fig. 5) ha il vantaggio di consentire la valutazione su un componente reale anziché su una barretta come previsto dalla norma ISO 26602:2009. Le sfere vengono incise e caricate verticalmente e si comportano in modo analogo alle barrette. Per i particolari sulla prova vedere [2, 3]. Si è notato [4] che i difetti superficiali quali le impronte di tipo hertziano “C” hanno una sensibile influenza sulla resistenza delle sfere.
Per una valutazione iniziale della fatica ciclica da contatto volvente si può utilizzare un banco prova Polymet (fig. 6), in cui una barretta viene caricata tra due dischi rotanti in acciaio. Normalmente vengono compiuti 40×106 cicli con pressioni di contatto di 3 o 4,8 GPa. La fatica ciclica da contatto volvente delle sfere finite può essere verificata su una macchina a quattro sfere modificata. La sfera in ceramica posta in alto fa muovere tre sfere sistemate in un vano sottostante per simulare un cuscinetto molto semplice (fig. 7). Una prova similare si può anche eseguire su un banco a cinque sfere, usando inferiormente quattro sfere. Per valutare la fatica da contatto volvente sulle sfere in ceramica si può anche impiegare un banco dotato di anelli scanalati a V (fig. 8). Una sfera viene caricata tra i due anelli con pressioni di contatto tra 1,5 e 5,5 GPa. Con una velocità standard dell’albero le sfere con 28,6 mm di diametro devono resistere a circa 6 milioni di cicli di sollecitazione all’ora.
La durata dei cuscinetti ibridi viene verificata con diverse condizioni di lubrificazione. Il cuscinetto normalmente usato nelle prove è un tipo obliquo a sfere 7209, avente sfere con diametro di 12,7 mm. In fig. 9 è illustrato un banco prova con lubrificazione a grasso per la prova di cuscinetti obliqui 7318, con sfere da 31,7 mm di diametro.
Conclusione
Tramite i metodi sopra citati di valutazione dei corpi volventi in ceramica dei cuscinetti ibridi è possibile accertarsi delle prestazioni che i materiali potranno offrire nelle applicazioni più impegnative. Con lo sviluppo costante di materiali appositamente studiati, è assai probabile che i cuscinetti ibridi continueranno a trovare nuovi impieghi nell’industria.
Bibliografia
[1] Pallini, R.A.: “Cuscinetti per altissime temperature nei motori a turbina”, Rivista dei Cuscinetti SKF 234, Anno 63 – Aprile 1989
[2] P. Supancic, R. Danzer, S. Witschnig, E. Polaczek, R. Morrell, ”A new test to determine the tensile strength of brittle balls — The notched ball test”, Journal of the European Ceramic Society 29 2447–2459 (2009)
[3] P. Supancic, R. Danzer, W. Harrer, Z. Wang, S. Witschnig, O. Schöppl, “Strength Tests on Silicon Nitride Balls”, Key Engineering Materials Vol. 409 pp 193-200 (2009)
[4] P. Supancic, R. Danzer, Z. Wang, S. Witschnig, O. Schöppl, “The Notched Ball Test – A New Strength Test for Ceramic Spheres, 9th Symp. on Ceramic Materials, Shanghai (2008)