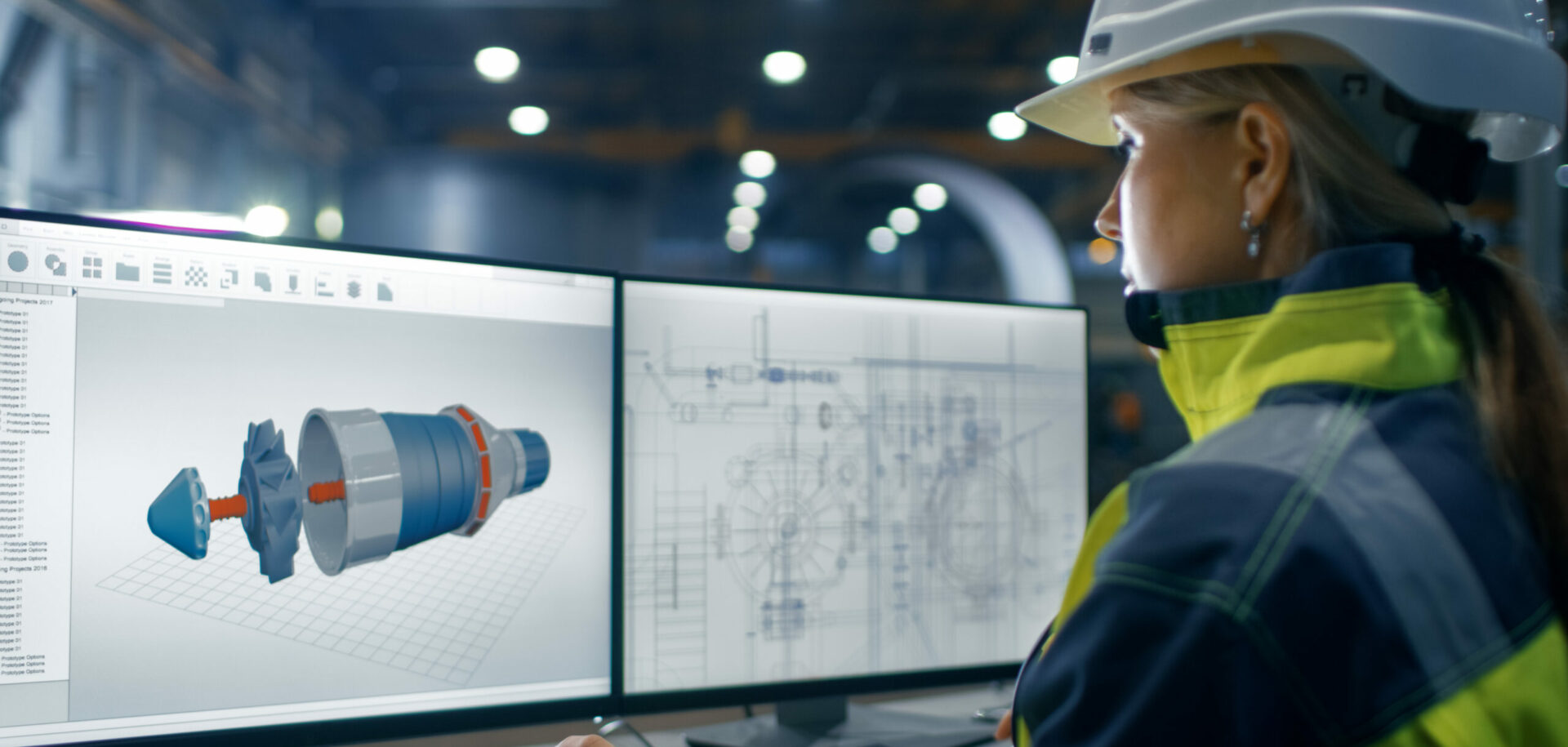
Labyrinth seal for Pop Release
The new SKF Pop Release bearing unit has a reinforced labyrinth seal designed to give high performance while operating in heavily contaminated environments.Rubbing seals are the most common type of seals for bearings mounted in bearing housings. Lip seals are usually made of nitrile rubber or polymer material, although felt seals are still commonly used. The benefit of this type of seal is that it is very effective in preventing dirt from entering the bearing. Its disadvantage is that the seal generates a great deal of heat due to the high frictional torque between the seal lips and the part with which they are in contact, such as the shaft. The high friction causes a rise in temperature in the bearing housing and results in higher energy consumption.
The new SKF Pop Release bearing unit has a reinforced labyrinth seal designed to give high performance while operating in heavily contaminated environments.Rubbing seals are the most common type of seals for bearings mounted in bearing housings. Lip seals are usually made of nitrile rubber or polymer material, although felt seals are still commonly used. The benefit of this type of seal is that it is very effective in preventing dirt from entering the bearing. Its disadvantage is that the seal generates a great deal of heat due to the high frictional torque between the seal lips and the part with which they are in contact, such as the shaft. The high friction causes a rise in temperature in the bearing housing and results in higher energy consumption.
Since the maximum operating temperature that the seal materials and the grease in the bearing can withstand is around 100 –C, the peripheral speed at the seal contact point, i.e. the speed of rotation, must be restricted. As a result, the maximum permissible rotational speed of the bearing is also restricted. The highest admissible peripheral speed of a radial lip seal is normally around 7-8 m/s.
In order to use rolling bearings at higher speeds, i.e. up to the ratings specified in the SKF General Catalogue, non-rubbing seals must be used, mainly gap type or labyrinth seals.
Reinforced seal
In its standard version, the latest Pop Release bearing unit is supplied with a double-lip seal made of nitrile rubber known as TriGard. The seal is reinforced with an outer sheet guard to enable it to withstand environments which are highly contaminated with hard and abrasive particles, such as gravel, sand and wood chips. Good sealing performance requires the seal to operate at high contact pressure, which generates a large amount of frictional heat. The peripheral speed at the contact surface should not exceed 8 m/s. For higher speeds, SKF developed a radial labyrinth seal. Demands on the seal were high, requiring a seal able to perform effectively even if the shaft is misaligned up to 1.5 degrees. The permissible misalignment of labyrinth seals is normally around 0.5 degrees. An additional requirement was that it should be possible to displace the seal axially by around 2 mm.
Dirt particles are stopped
After rigorous tests at the SKF laboratory in King of Prussia, Pennsylvania, the seal design found to be best suited is that shown in figures 1 and 2. The seal consists of three parts which are made of sheet steel and are pressed together. One of these is stationary and is a press fit into the bearing housing, whereas the other two are mounted on each side of the first and rotate together with the inner ring of the bearing. When dirt particles come into contact with the seal, they are stopped by the stationary part and are flung off from the bearing unit by the outer rotating sheet steel part.
It is important that labyrinth seals should be periodically lubricated to ensure that there will always be clean grease inside the labyrinth. For the Pop Release bearing unit, this takes place at the same time as lubrication of the bearing through the grease nipple mounted on the bearing housing.
Photo 1shows the SYT 45 FTS Pop Release bearing unit incorporated into a wood working lathe for handicrafts. In order to minimise the frictional torque and the bearing temperature, the customer decided on a labyrinth type seal, in spite of the harsh external environment, which included dust and sawdust. The lathe has now given more than a year of trouble-free service. Contaminants have not entered the bearing, and the suitability of the Pop Release bearing unit for operation in harsh environments has once again been proved.
Sture Östling,
SKF Mekan AB,
Katrineholm, Sweden