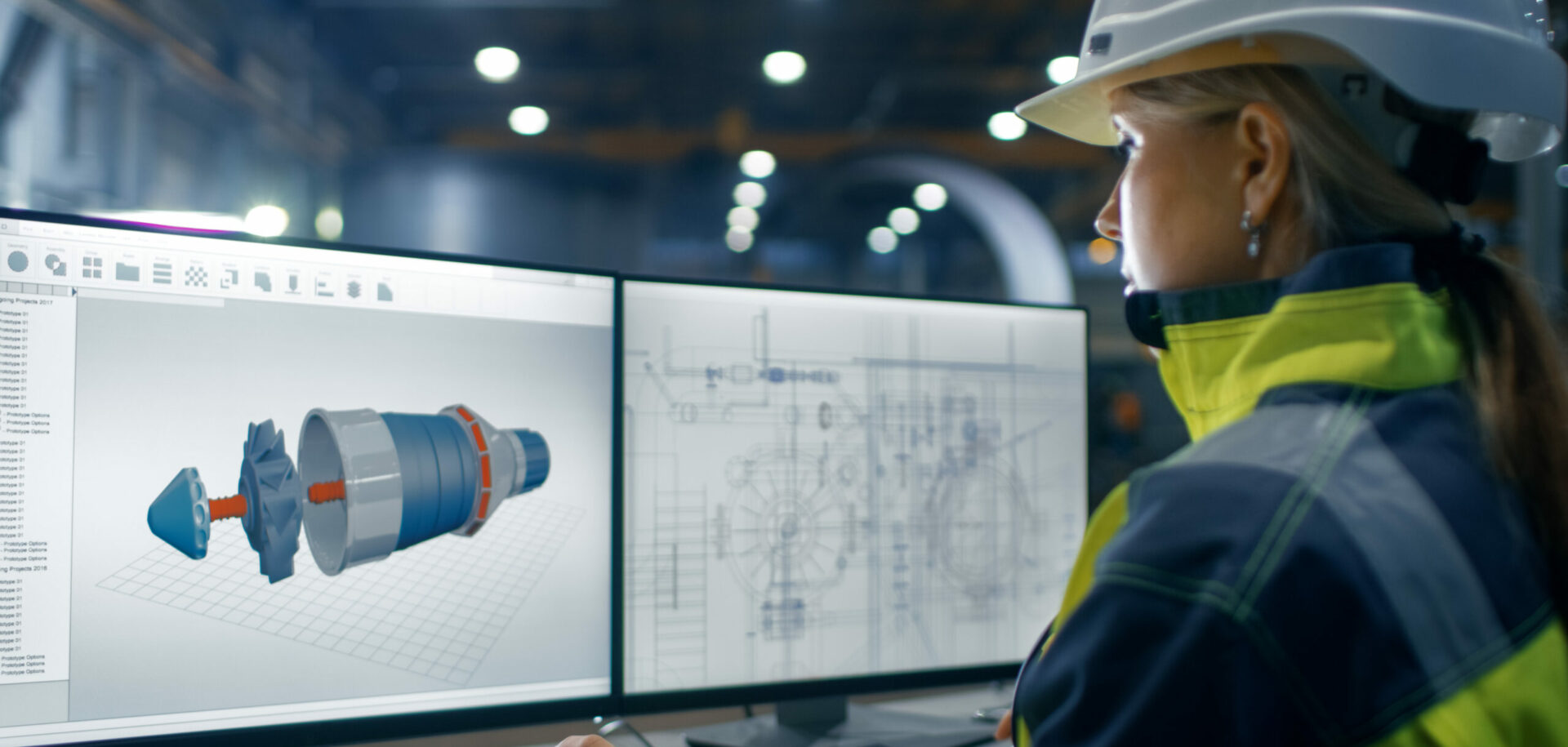
Long-term grease lubrication in printing machines
Highly tailored and customer-specific solutions for long-term grease lubrication in printing machines are the wave of the future.
Grease lubrication today
Relubrication in printing machines
Currently in the lubrication in printing machines, the main cylinder bearings are lubricated with oil, grease – or one with oil and the other with grease. Grease must not only lubricate, but it must also prevent entry of any contaminants. This includes infiltrating detergents or thorough cleaning processes that may wash grease out and damage the bearing.
If the service life of the lubricating grease has expired, the anti-friction bearing must be relubricated. In principle, a precise prediction of the relubrication interval for an individual bearing is not possible, as grease life is based on statistical rules. In fact, the relubrication interval depends very much on the application conditions, it can on average be estimated at six months.
A good approach is described in the SKF General Catalogue. The relubrication interval is calculated rather conservatively and applies to a high-quality grease with a lithium thickener at an operating temperature of 70 °C.
The SKF relubrication interval indicates the moment at which 99 % of the bearings are still adequately lubricated, i.e., they correspond to a lubricating grease service life, L1.
This relubrication should always be carried out at a moment when there is still a reliable lubrication effect from the existing grease. Relubrication is performed either by hand or with lubrication systems. In modern lubrication systems, fresh grease is pressed directly through relubrication lines and replaces used grease, which can flow out into specially designed repositories.
The required amount of lubricant depends on the geometry and design of the bearing units to be lubricated.
Both the base oil and the thickener of a lubricating grease are subject to an aging process. If the soap structure is destroyed, its base oil can leak out and be lost, making lubrication impossible. If the base oil is aged, it cannot optimally contribute to the lubricating film structure. Both effects work out negatively and finally result in damage to the bearing.
Various analytical tools and facilities are available to assess the condition of used lubricating greases. These are used to classify and identify the condition of the grease after use. One standard test is infrared spectroscopy.
The additives applied in a grease are selected on the basis of the various characteristics required, such as oxidation resistance or protection against corrosion and wear. These additives are also subject to an aging process. In order to quantify the effects of these additives, there are tests for studying protection against corrosion of bearing steel (ISO 11007) and for copper corrosion (DIN 51811/ASTM D130-04) and also for testing of compatibility with polymeric materials.
These methods involve quantifying contamination and impurities. The data ultimately decide upon the further usability of the grease and bearing. Fig. 2 shows the example of a Printing Cylinder Bearing Unit (PCU) after running on a test bench. The condition of the grease was investigated after the test.
Grease lubrication tomorrow
Printing Cylinder System – Long-term grease lubrication
Based on a specific application or loading case, detailed predictions can be made on the widest variety of tailored system solutions, called Printing Cylinder Systems (PCS) (Figs. 3 and 4). Grease life predictions for these PCS show that under optimal conditions very long relubrication intervals can be achieved, and in special cases even lubrication for life is possible.
On the basis of the bearing dimensions and operating conditions such as speed, load and temperature, grease life can be estimated from Diagram 1.
If the grease life (as L10) is not the critical factor, compared with other elements in the printing machine, then relubrication is not needed. In the other case, the relubrication interval (L01) can be derived from the diagram via the approximation L01=L10/2.7 . The diagram is valid for selected greases in properly sealed and clean systems. The effect of the bearing temperature on grease life is clearly visualized in the diagram. It shows that it is attractive to aim for a low self-induced operating temperature. This can be achieved by the grease type, the filling quantity and the initial distribution inside the bearing.
Diagram 2 shows a continuous low operating temperature of 40 °C (only 20 °C above ambient), after a relatively short runningin process. When conditions are not optimal, the temperature can stay high permanently, with a very short grease life as a consequence.
With regard to sealing, appropriate precautions must be taken, on one hand, to keep the grease in the roller bearing and, on the other, to guard against contamination from external sources.
Safeguarding the long-term service life of grease creates the basic requirement of bringing the roller bearing-grease-sealing system concept a step closer to a long system life.
Lubrication of Oscillating Bearing Units (OBUs)
Just as with the Printing Cylinder System, the roller bearing grease-sealing system concept was accommodated in Oscillating Bearing Units (OBUs) and corresponding development work undertaken.
The simultaneous occurrence of rotation and oscillation produces a particular demand on the system’s grease and sealing. The result of these comprehensive studies is that long-term grease lubrication, as shown in Diagram 1, is possible in principle.
The maximum relubrication interval for the first relubrication can be five years after the printing machine has been operated for the first time. This can be put down mainly to the aging of the grease in the lines.
The second and all subsequent relubrication interval comprises 60 % of the interval between the initial start-up of the printing machine and the first moment of relubrication, but no more than three years.
An OBU (Fig. 5) is lubricated in the factory, to make sure that the correct amount of the right grease is in the right part of the oscillation bearing. Moreover, this unit is mounted inside the factory, with particular care to keep it clean, with minimized risk of contamination.
Central Lubrication System
Simple and cost-effective central lubrication systems represent a new kind of possibility, bringing the day of oil-free machines closer, and, at the same time making printing machines more reliable and easier to maintain. The single-pipe central lubrication system (CLS) is an excellent example (Fig. 6).
Like progressive lubrication, single-pipe lubrication can be used in nearly all types of printing machines. Areas of application are roller bearings and curve controls, both primarily on the operator side.
Unlike progressive lubrication, single-pipe grease lubrication can be adapted in a modular fashion to the number of printer units because a main distributor is not necessary. Assembly is easier with more direct methods, which also means that most of the overall conduit lengths are smaller. Especially positive is the noncritical use of complex lubricants, which may tend to leak in progressive systems.
Grease lubrication in the future
The merging of expertise in bearing technology, sealing systems, lubricants and lubrication systems results in interesting future prospects in continuing the system concept for the long-term aim of “oil-free” machines.
Integrated product solutions can make a substantial contribution to providing innovative and effective support to customers. An excellent example is a lubrication system integrated into a bearing (Fig. 6).
The lubricant for the lubrication cartridge – optimally chosen for the operating conditions and harmonized with both the lubrication system and bearing – is continuously supplied to the lubrication point. The right dose of grease, tailored in turn to the particular application case and coupled with the large volume of the lubricant container, enables long-term lubrication that can last for three to five years, depending on the particular case.
As soon as the amount of lubricant in the lubricant container appears to be reaching an end, the lubrication cartridge can be easily and quickly replaced with another.
With this stand-alone solution, any bearing point can be individually laid out and lubricated.
A self-contained bearing-sealing lubrication system such as this aims, on one hand, to help the original equipment manufacturer to make assembly of its printing machine easier, but, on the other
hand, to support the printing machine operator in reducing the amount of required maintenance work.
Forward-looking products, complete systems, customer-specific system solutions and services provided for such as roller bearings, seals, lubrication systems, mechatronics and assembly will have a
lasting influence on the printing industry.
Enclosed and sealed Printing Cylinder Systems and Oscillating Bearing Units comprise a bearing, seals and grease. Special design features for the components are specified in the operating conditions at printing shops. A few years ago, it was unrealistic to expect grease to last longer than five years. Significant progress over the past few years in the development of bearings for modern printing machines, including seals and grease, has resulted in significant extension of the service life. The results of simulations, calculations and tests have shown that even more tailored and customer-specific solutions can be created in the future. Further development of central lubrication systems can also help lower costs and improve service for customers.