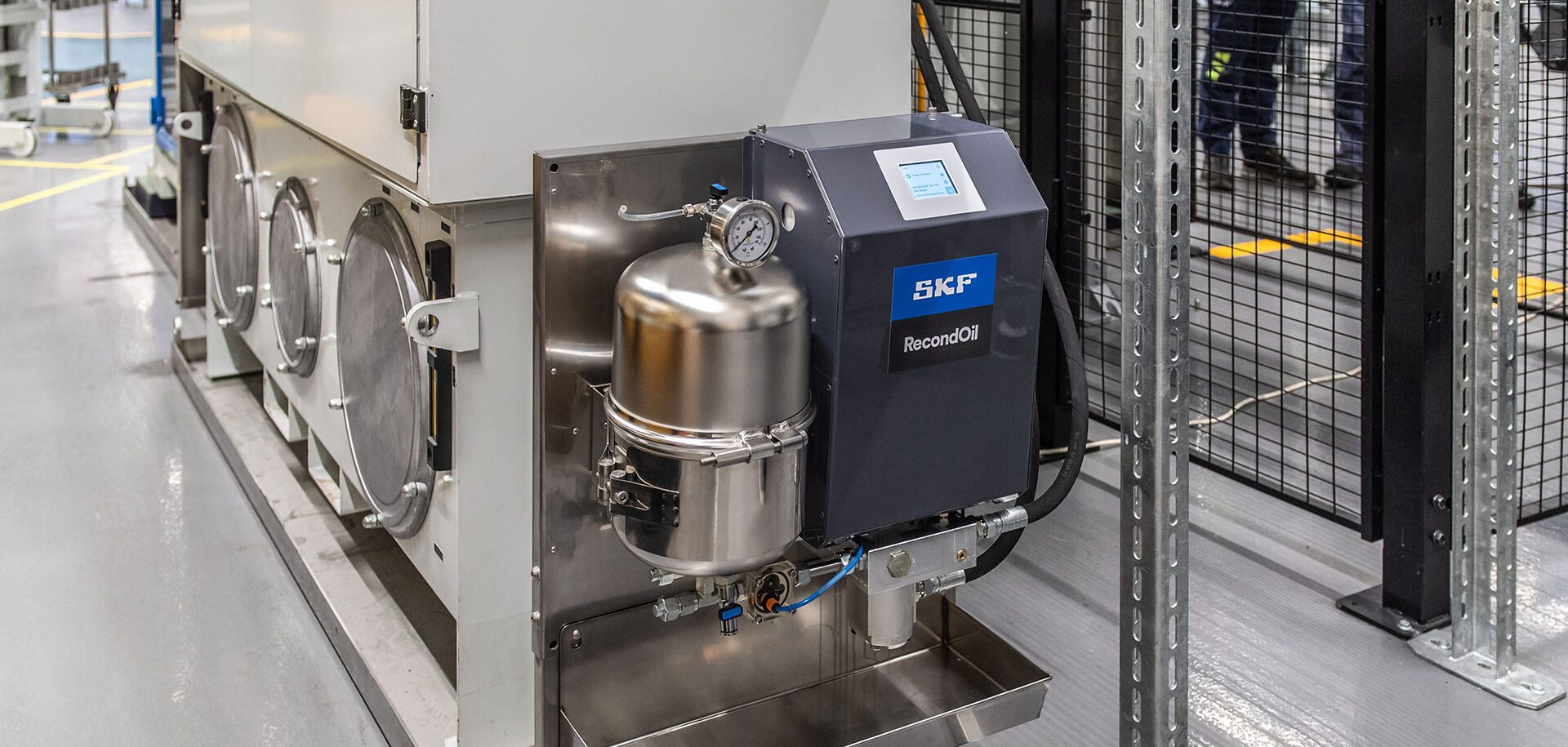
Lubrication management: the way to improve performance
Lubrication, though often viewed as routine, gains importance with diligence. Alain Noordover, SKF lubrication management development manager, stresses its pivotal role for substantial efficiency gains, sharing insights from his extensive experience.
Lubrication is critical to manufacturing, yet it is often treated as an afterthought – something so basic that it seems unworthy of anybody’s time. This is despite knowing that without lubrication, machinery can quite literally grind to a halt. Poor lubrication practices and contamination account for around half of all premature rolling bearing failures, and even more if we consider equipment such as industrial chains. Over time, very little has changed. While there are new lubricants, tools and even some lubrication management software tools, this dismissive approach remains.
Inappropriate lubrication can lead to huge waste, in terms of both capital and resources and humans and the environment, at a time when environmental concerns (such as CO2 emissions) are at the core of everything.
A study from 2017 in the journal Friction estimated that 20 percent of the world’s energy is used to overcome friction losses. While partly inevitable – we don’t live in a frictionless world – imagine how this figure might be reduced with more effective lubrication. It follows that every year a portion of any country’s GDP will be expended on replacing worn parts.
It is clear that a targeted approach in the form of lubrication management can help raise efficiency. By doing this correctly, lubrication can be transformed from its current status as a kind of liability into a true asset.
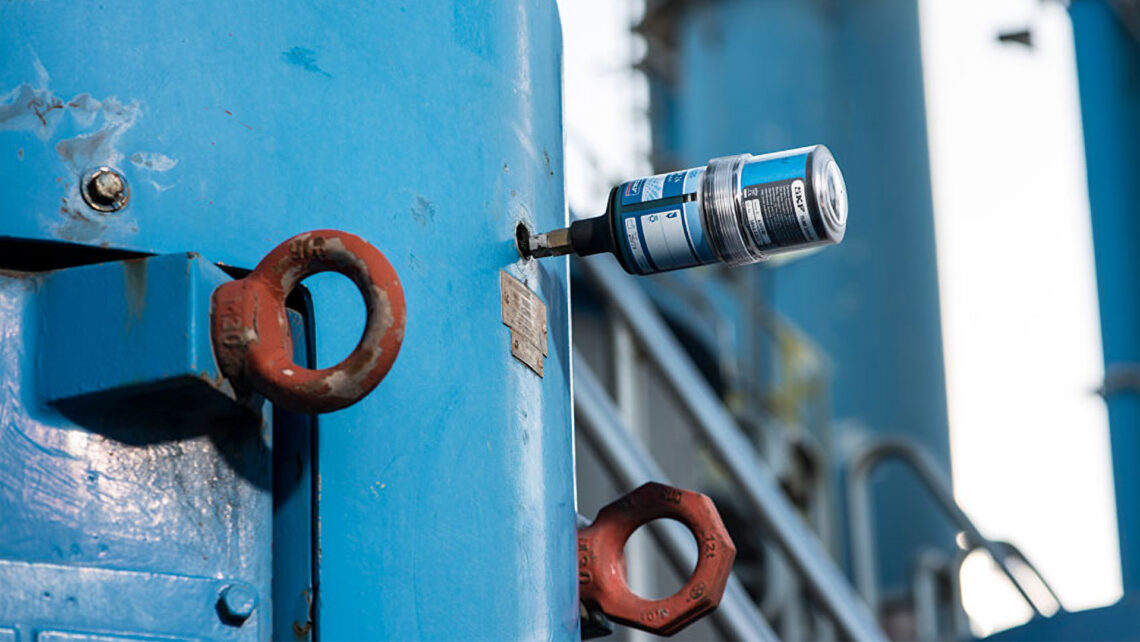
Poor performance
With all these potential upsides to correct lubrication, it is worth considering some of the reasons why it is widely managed so poorly.
- It’s a dirty job that’s not much fun. Lubricants are not the nicest materials to handle, and applying them involves lots of walking and routine activities.
- Lubrication forms a small part (usually around 10 percent) of a firm’s maintenance budget so it tends to be neglected or seen as a cost rather than an opportunity.
- There is a need for more knowledge and skills, at both the operational and management levels, when it comes to lubrication.
- It involves countless tasks at each lubrication point, which all need skills and best practices to be accomplished.
The most likely reason why lubrication is still performed poorly is that all the above play a role, in degrees that vary from company to company. While many would agree on the significance of proper lubrication, the execution often falls short. Lubrication should not be seen as a set of dissociated tasks but more as a kind of living process, and it should be treated as such.
When things go wrong
The best way to show the effects of poor lubrication is with actual examples.
Poor lubrication practices and contamination account for around half of all premature rolling bearing failures, and even more if we consider equipment such as industrial chains.
Alain Noordover, lubrication management development manager, SKF
In one case, in the cement industry, the end user saw repeated failure of expensive spherical roller bearings (SRBs). Looking deeper, four different lubricant names were attributed to the different parts of the lubrication management programme. The wrong lubricant, with one-twentieth the necessary viscosity, was being added to the bearing. Metal-to-metal contact then led to premature failure. Overall, different aspects of lubrication management that were not addressed properly led to catastrophic failure.
A second example involved a salt press in the food and beverage (F&B) industry. Here, a vintage lubrication system dispensed grease into medium-large SRBs and this then leaked into the final product. The grease should have been F&B approved, but it was not. There was also salt ingress into the bearings, so they had to be cleaned every two weeks.
These are two examples, but there are many more, possibly on your own site. They show that “small” lubrication issues can lead to high costs, lost production and extra work, all of which affect the top and bottom lines of any company.
Lubrication management
Lubrication management can minimize the waste of capital, resources and time, improve health and reduce environmental impact through lower CO2 emissions and material release. There is also a formal definition of lubrication management:
“The proper organization of resources to effectively and efficiently improve reliability, reduce inefficiencies and costs and increase safety and environmental compliance.”
The SKF lubricant life-cycle model can be used to help visualize the seven different parts of lubrication management:
- Selection: choosing the right product. This can be a delicate process, but tools such as SKF’s LubeSelect can help by incorporating real bearing performance.
- Purchase: choosing a small number of reliable vendors that offer consistent product quality.
- Storage: storing lubricants that are not likely to be used immediately at the right temperature and humidity, and avoiding exposing them to contaminants.
- Transfer: colour-coding tools and lubrication points, to avoid factors such as cross-contamination. Having clean tools is of course also important.
- Application: checking quantities and relubrication intervals regularly, whether the lubricant is applied to assets manually or via an automated system.
- Monitoring: analysing oil or lubricant use to understand if a lubricant is performing as it should.
- Recondition/disposal: disposing of lubricant correctly. A system such as SKF RecondOil allows recirculation of oil, but lubricant is typically replaced, and thus disposal is necessary.
After this, the loop is closed and we are back at lubricant selection.
Both the cement works and the salt press cases were solved by applying lubrication management. At the cement works, the answer was common sense. By documenting the process we overcame the main failure in the system, that of using the wrong lubricant. For the salt press, correct lubricant selection and application, proper sealing and monitoring of the asset via vibration and grease analysis helped to solve the problem.
Fuller picture
This describes the lubricant life cycle, but the full lubrication management model has four more crucial parts: planning & scheduling, procedures, training and personal development, and management and KPIs. Putting these together provides a fuller picture of lubrication management.
Planning & scheduling
Many tasks must be accomplished in a plant. First we must ascertain whether the right tasks are designed: do we have the right lubricant, in the right amount, using the right method, at the right time, to the right lubrication point? If not, could they be removed or replaced? Second, how do we schedule tasks so the workload stays manageable? Dedicated lubrication management software can help here.
Procedures
To ensure job consistency, procedures must be developed and made available to all. Digital documentation is easy to update and is accessible remotely. Usually, technicians carry out activities based on their own knowledge, whether this is good or bad. Another issue is loss of information when skilled technicians retire or leave.
Training & personal development
The earlier points mean little without looking at the people who carry out lubrication. It should be seen as a skilled job and treated as such, with training and development plans. Replacing routine, mundane tasks with proactive, problem-solving work makes a job more stimulating. Sometimes, outsourcing lubrication tasks can be appropriate.
Management & KPIs
Lastly, what must we measure to know we are heading in the right direction? For this, we must set up thoughtful and pragmatic KPIs. Lubrication management software can help monitor and visualize critical information. Typical goals might be to improve efficiency of lubrication execution, to reduce the number of unplanned tasks or to cut oil consumption without hurting the machine. All of these can be tracked and measured.
Using the model
Lubrication management comprises many elements, encompassing tribology, filtration, oil analysis and management, and it may appear overwhelming. However, significant improvements can be made in small steps with simple, pragmatic actions such as the ones below.
- Assess the situation
How does your plant measure up? If action is required, a lubrication audit can help by employing tools, such as the SKF Client Needs Analysis, that evaluate and set benchmarks for effective lubrication management. Alternatively, individuals can use online self-assessment tools, such as the SKF QLR (Quick Lubrication Review), to evaluate their own lubrication practices. - Build a business case
Use known issues and try to put a price tag on them. Use literature or the results from a lubrication audit to estimate the positive impact of proper lubrication. - Develop people’s skills
Move people away from “pushing grease” and towards proactive, problem-solving tasks. If relubrication is automated, technicians can spend more time inspecting machines. - Follow best practice
Apply this in all parts of lubricant management and devise a pragmatic activity plan. It sounds daunting, but think of it like cooking a family meal. The aim is to end up with a meal on the table, having made various selections, purchases and other decisions. - Set targets
One possible target might be to cut lubrication-related bearing failures by a set amount. Clever lubrication management can also have knock-on effects: Lubricants are often 2 to 3 percent of a maintenance budget, but lubrication errors can influence 40 percent of the budget (such as spare parts and labour).
Conclusion
Making these changes requires a change of attitude and adopting a lubrication management mindset – accepting that action is needed in order to raise efficiency.
The first step, and the most important one, is awareness. This can be achieved with an awareness campaign, a visit or training. Everybody gains mutual understanding and can communicate equally. The next step is to clean up the mess, but by now it has been acknowledged and can be acted on. Start by addressing visible problems, such as the storage room, as this sends a signal that the problem is being taken seriously.
Lubrication needs to enter a new era, and it can do this thanks to industry knowledge, new devices, digitalization, artificial intelligence and reconditioning. Ultimately, lubrication management will help reduce consumption of resources and energy while maintaining our standard of living.
There is no magic solution, and it will not be solved overnight, but accepting the problem and making a commitment to solve it is within everybody’s reach.
What is lubrication – and how does it work?
In simple terms, lubrication reduces friction and wear of surfaces by avoiding metal-to-metal contact by placing lubricant between the surfaces. A lubricant can be solid (such as graphite), liquid (oil), semi-solid (grease) or gas (air). Each has a specific viscosity (resistance to flow) that, combined with the relative speed of the mating surfaces, the load and the wedge created by the geometry of the components, will create a thin lubricant film.
The lubricant film is typically in the order of microns or sub-microns that the human eye cannot usually detect. Oils and greases are the most important lubricants used today. Additives can be incorporated into them to add, or remove, certain properties, such as extreme pressure, anti-wear and anti-oxidant. For greases, a thickening agent holds the oil together and gives the lubricant a consistency that enables it to stay in place.
Most things that move within our society, from trains to vacuum cleaners, only operate thanks to a micron-thick lubricant film between bearings, chains and other machine components.