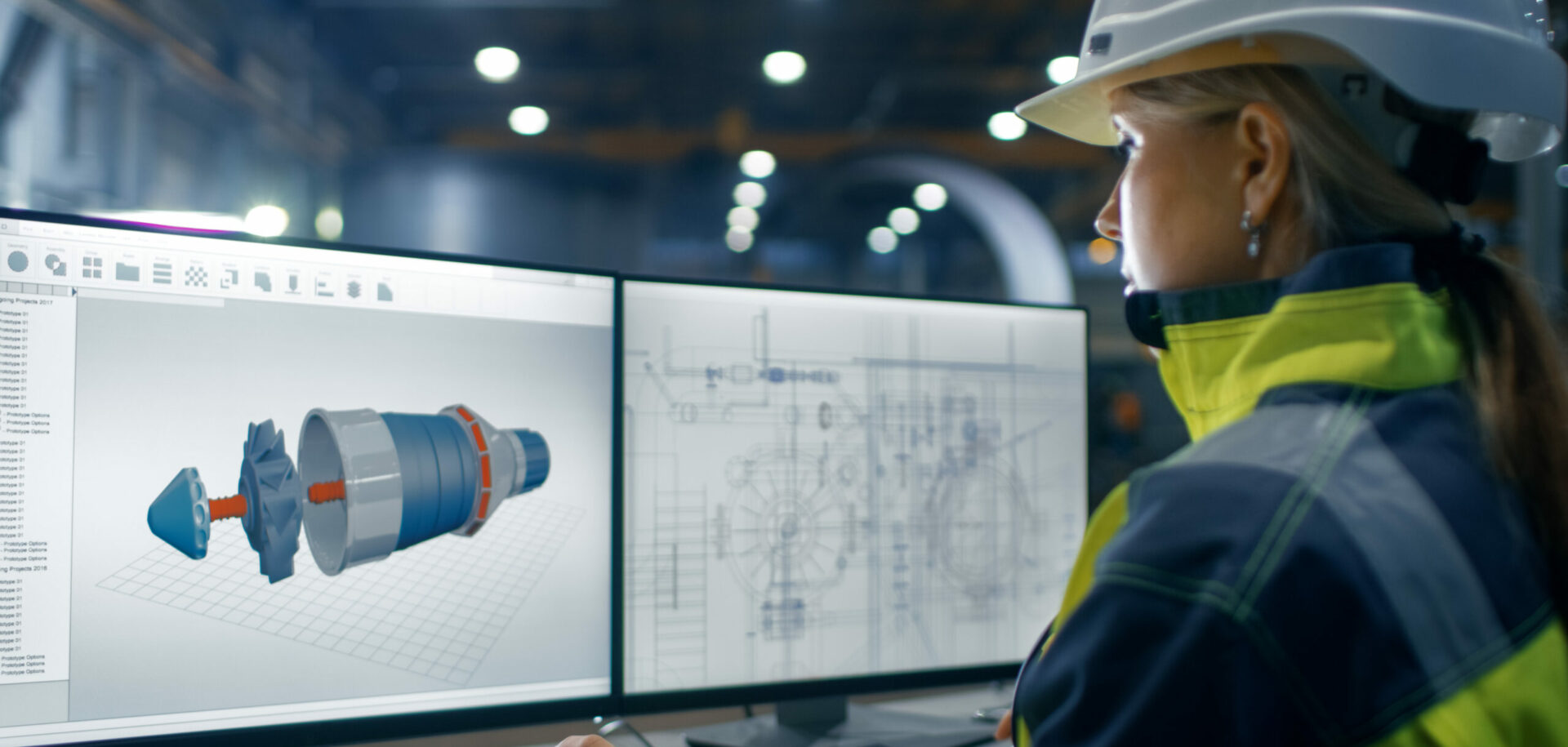
Maintenance-friendly designs
New oil injection reduces down time and improves safetyIntroduced in the 40s, the use of the oil injection method to make equipment maintenance-friendly has been gaining popularity. But there are still many original equipment manufacturers who have ignored the competitive benefits of making their equipment injection-friendly.
New oil injection reduces down time and improves safetyIntroduced in the 40s, the use of the oil injection method to make equipment maintenance-friendly has been gaining popularity. But there are still many original equipment manufacturers who have ignored the competitive benefits of making their equipment injection-friendly.
Oil injection entails the introduction of oil between the mating surfaces of an interference fit for the purpose of mounting or dismounting bearings or other equipment. The oil is pressurised and delivered via connecting ducts in the shaft to a shallow groove that circles the shaft. The thin oil film reduces the friction and thus the required mounting or removal force to a miminum. When the applied oil pressure is reduced after mounting is complete, oil is forced back through the supply duct by the surface pressure so that direct contact is made between the mating surfaces and full power-transmitting capacity obtained. Depending on the bearing size, dismounting via oil injection may require only 10 percent of the time needed to dismount the same bearing when using conventional methods. As a guide, down time in the steel industry can cost $20,000 or more per hour and costs in the paper making industry can run as high as $15,000 per hour.
An additional benefit of the oil injection method is that it reduces the potential of damaging adjacent components during the mounting and dismounting process. For example the use of oxyacetylene torches or grinding wheels can damage the shaft while it is being removed.
Oil injection specifications
Provisions for equipping a machine with oil injection capabilities should be made early in the application design process or retrofitted during a maintenance period. The oil injection method is not limited by the size of the component, but is particularly well suited for larger bearings which present greater mounting/removal forces that need to be overcome. The oil pressure needed is somewhat higher than the surface pressure in the tight-fitted component. In some exceptional cases, the surface pressure can exceed 250 MPa. In most cases it is found to be between 80-150 Mpa. For bearings the surface pressure is lower, 20-50 MPa. The oil injection method requires a pump that has the capacity to reach and exceed these pressures. All pipes, hoses and connection nipples must be rated for these high pressures. For extra safety, the pump should be equipped with a pressure gauge for continuous monitoring of the pressure during pumping.
Dismounting procedures
For machines equipped with the correct ducts and fittings, oil injection is the preferred method of dismounting bearings. The procedure does not require the use of a puller or other device.
When dismounting a tapered bore bearing you loosen the securing locknut and back it off about one quarter of an inch (6 mm). Connect the oil injection pipe securely to the duct in the end of the shaft, and pump until the bearing literally shoots off.
Cylindrical bore bearings can also be removed using the oil injection method. Since there is no taper to aid the dismounting process a small force is required to withdraw the bearing from the shaft. The use of a self-centering puller is recommended to avoid bearing misalignment and metal-to-metal contact.
The mounting process
Oil injection is also an efficient way to mount bearings, especially those with tapered bores. Tapered bore bearings can be mounted directly onto the shaft with the required taper pre-machined on the journal. Oil injection facilities need to be machined into the shaft at the production stage. Alternatively the bearings can be mounted on parallel shafts with the aid of tapered adapter or withdrawal sleeves. The adapter and withdrawal sleeves can be supplied already pre-machined to accommodate the use of oil injection.
Whether using a tapered shaft or pre- machined adapter and withdrawal sleeves, the procedure for mounting a tapered bore bearing using oil injection is similar. Put the tapered bore bearing on the tapered shaft sleeve, push it up the taper until it is hand tight and position the securing locknut or retaining devices so that they abut the bearing. Connect the oil injection equipment to the application and inject the oil while pushing the bearing up the shaft with the lock nuts or securing devices. The bearing is driven up the shaft, sufficiently to achieve the correct residual internal clearance.
Marketing advantages
Large machines that are designed to use the safe, efficient oil injection method are easier to maintain, and enjoy a considerable marketing advantage over equipment without the capability.
Ian Knight,
SKF Maintenance Products,