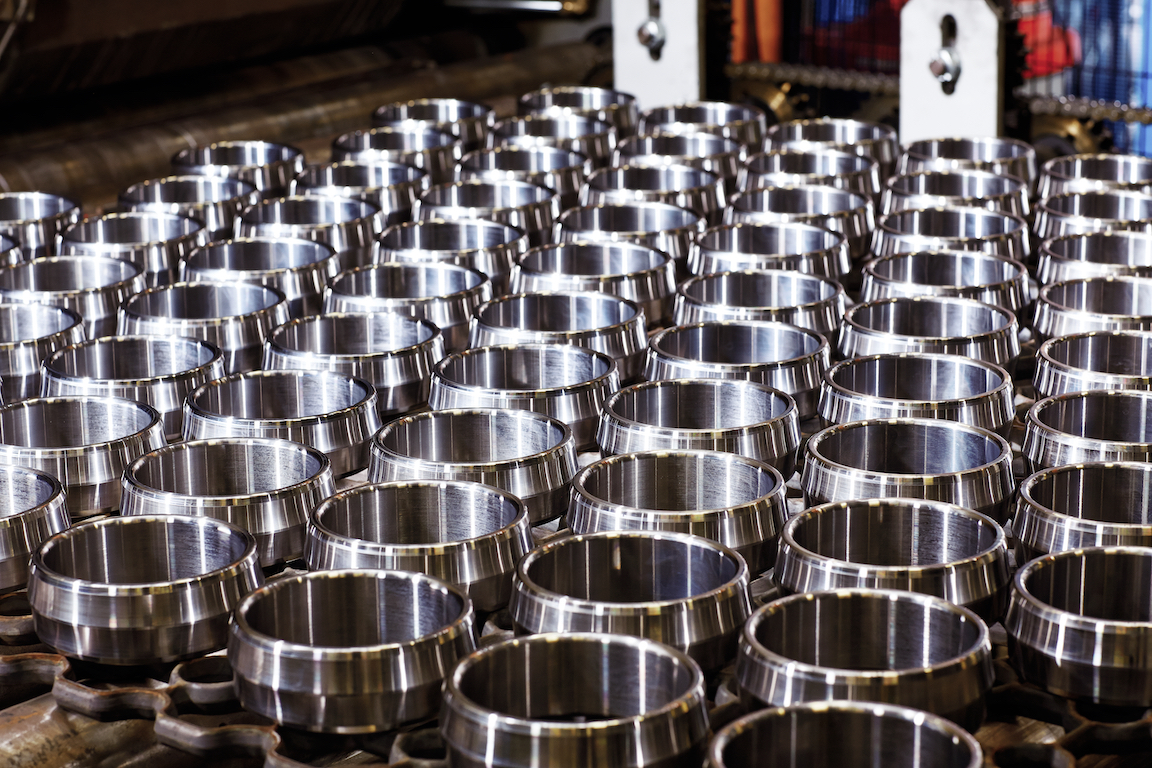
Mechatronics – from fuel injection to robotic soccer stars
Mechatronics systems are typically mechanical devices under intelligent electronic control. A pilot moves a steering lever, a computer registers the movement and orders a hydraulic actuator to lift a flap on the wing. Yesterday’s complex systems of mechanical pistons, levers and pulleys are being replaced by mechatronic systems involving sensors, microprocessors, electronic actuators and other elements, which are simpler, lighter and more intelligent.
Some hail it as the mechanical engineering of the 21st
century. Others have not yet realised its potential. Regardless, the relatively new field of mechatronics is here, and experts and engineers say it is starting to change the way we think about machines – and how we build them.
A decade ago, the term “mechatronics” was generally unknown. In fact, in 1994 the Journal of the Institute of Electrical and Electronics Engineers published an article, “Mecha… what?,” describing the phenomenon. Today, however, companies such as Bosch, Honda and Delphi have whole mechatronics divisions, and universities around the world offer mechatronics-specific curricula.
Mechatronics systems are typically mechanical devices under intelligent electronic control. A pilot moves a steering lever, a computer registers the movement and orders a hydraulic actuator to lift a flap on the wing. Yesterday’s complex systems of mechanical pistons, levers and pulleys are being replaced by mechatronic systems involving sensors, microprocessors, electronic actuators and other elements, which are simpler, lighter and more intelligent.
Fly-by-wire, drive-by-wire and other “by-wire” technologies are already firmly in place in the aircraft industry and are emerging in other industries. In the automotive sector, for instance, an electronic throttle is now built into virtually all automobiles, doing away with the mechanical connection between the throttle and the fuel-injection system. “Once you’ve got electronic signals by wire, then you can much more easily integrate the data with the electronic engine management system,” says Roger Bishop, editor of the engineering journal European Automotive Design. “This has big implications for emissions control, fuel saving and optimising output.”
Only legislation and market acceptance are holding back the next two big automotive areas, steer-by-wire and brake-by-wire. Current law says that there has to be a solid connection between elements of the steering system, but an industry group is working on new European legislation, Bishop says. “One of the big issues surrounding both brake-by-wire and steer-by-wire is whether the market – the driving public – will accept them,” he says. “And if so, when?”
Across the board, mechatronics benefits include higher productivity, higher quality, lower operating costs, more safety, more efficiency and a greater flexibility than mechanical and hydraulic designs alone could ever achieve. The potential market is huge. Analysts of the US-based Allied Business Intelligence Inc estimate that by 2010 drive-by-wire subsystems will be a business worth 21 billion Euro, according to reports in EBN Online, an internet business and technology news magazine for the electronics industry. Another 2001 study, backed by the Economist, projects that the trend towards factory automation alone is projected to boost the mechatronics market from 87 billion Euro in 1997 to 210 billion Euro in 2008.
Borders eroding
Mechatronics is forcing a new way of thinking on the engineer of the 21st century. “We are witnessing a lot of changes in the information age. The borders between different disciplines are eroding very rapidly,” says Okyay Kaynak, chair of mechatronics for UNESCO (the United Nations Educational, Scientific and Cultural Organisation) and professor at Bogazici University, Istanbul. Co-development means knowing not only the limitations in one’s own discipline, he says, but also in the other elements. In other words, a mechanical engineer must know the limitations of the software, and the software developer must know what the mechanics can or cannot do. This is not easy, because the different disciplines in the world of engineering do not use a standard language.
“These guys are brought up in one discipline, and they speak the language of that discipline,” says Jelm Franse, vice president of Philips Centre for Industrial Technology (CFT) in the Netherlands. “The symbols for stiffness are different, whether you’re a mechanical engineer or a chemical engineer. So they all have a completely different frame of reference that they bring along for solutions.”
Just look at the difference between how a mechanical engineer and an electronic engineer view whether a system is considered to be fast, says Franse. For the mechanical engineer, a device with an adequate response up to 1,000 Hertz is a very fast system, whereas the electronic engineer is used to controlling data at rates in the order of mega or even gigaHertz.
“Depending on the backgrounds of different people, some things are easier in one technology than in another,” says Franse. “That means you have to train these people to understand these differences and the opportunities that stem from them, and then develop a common language in order to realise the potential synergy.” Philips CFT sends its mechatronics team to a range of courses to learn a type of unifying mechatronics “Esperanto” that the company has developed that applies to all sectors. “This is not something you do overnight. It really takes a decade to build up,” he says.
RoboCup
Kaynak says one of the most exciting areas of cross-discipline teamwork is the development of the complex decision-making processes that enable machines to adapt themselves, acting upon different environmental conditions and parameters. Some of the most ground-breaking developments are happening through a global league of robotics soccer.
At RoboCup 2002, 127,000 people congregated in the indoor sports arena in Fukuoka, Japan, to see robots ranging from wheeled devices to two-legged humanoids compete sensor-to-sensor. While many of the contestants are the work of college students, multinational companies are also involved in the annual bout. Dutch Philips is one of them.
“There were several enthusiastic people who wanted to build a team at Philips CFT,” says Franse. “We told them it was a great idea. They simply had to win.” Originally, he says, the RoboCup team had been feeding on CFT’s advanced development programme. But after two years, the tables turned. “We are now starting to learn from our RoboCup area,” he says.
The robots must learn both individually and as a team, fusing streams of widely different data in order to make decisions. “If a ball is in flight, the robot has to determine it’s a ball and not the head of a person, and then determine what type of action to take,” Franse says. “This requires effective analysis and integration of information from various sub-systems at a very, very high bandwidth. Our RoboCup area pushed our vision-
integration capability into a completely different arena than where we were before. This led us to develop a motion-vision
system.” And, he says, this in turn has enhanced the company’s ability to place electronic components on variable surfaces such as flexible foils in real time.
The RoboCup organisers have the ambitious goal of developing a team of robots that can beat the human world champion soccer team in 2050. Notes Kaynak: “If you think that is really far fetched, just think where we were 50 years ago.”