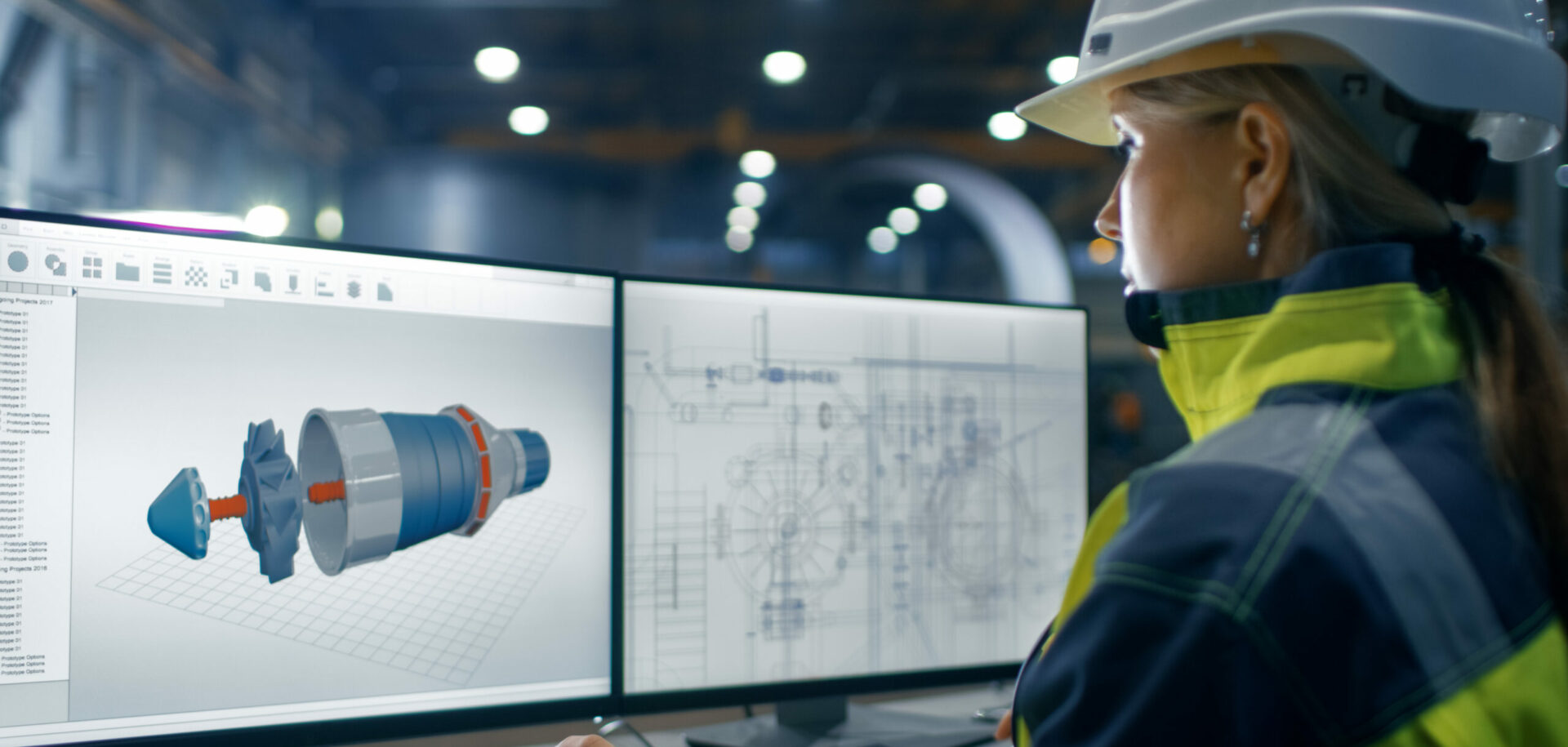
Monitoring the winds of change
Unpredictable loads and speeds are some of the challenges in the geographically scattered wind power industry. Applying condition monitoring to wind turbines required SKF engineers to add new skills to their technical armoury. SKF WindCon, the solution for monitoring the operation of these power-generating turbines, comes with sophisticated features that can relay complex information about their performance.
Unpredictable loads and speeds are some of the challenges in the geographically scattered wind power industry. Applying condition monitoring to wind turbines required SKF engineers to add new skills to their technical armoury. SKF WindCon, the solution for monitoring the operation of these power-generating turbines, comes with sophisticated features that can relay complex information about their performance.
Wind power has continued to build steadily, with capacity rising to 60 gigawatts worldwide as of December 2005, of which 20 % of that total was installed in 2005 alone. As this installed wind power base grows, the focus is shifting from development to operation and maintenance.
Thus, condition monitoring becomes an important aspect in maintaining wind turbines, much as it does in other industrial sectors. Due to the nature of the conditions under which these machines operate, applying condition monitoring demands its own unique solutions.
Although condition monitoring may be a proven technology, it cannot simply be copied and installed in a wind turbine.
For this reason SKF has developed WindCon to monitor wind turbines that operate under constantly fluctuating wind conditions with rapidly changing loads and speeds. To cater to the geographically dispersed nature of the wind power industry, WindCon incorporates a unique set of communication features that make it able to communicate in every type of network, from old, copper-wire phone networks to the most advanced wireless solutions or even within heavily protected company networks.
Using SKF WebCon, data can be delivered to any Internet PC using an Internet browser as software, removing the necessity for com-plicated software and opening up the information stream to a wide range of parti-cipants or third-party service companies.
Turbine Diagnosis using three unique WindCon features
As wind is unpredictable, its speed, direction, air moisture and temperature create the constantly changing working conditions to which a wind turbine is subjected. Monitoring machinery that is unpredictably changing its loads, power and rotational speed requires engineering excellence to create early detection of the smallest developing damage at low winds, while, at the same time, avoiding false alarms resulting from sudden wind gusts. In a geographically dispersed industry, bringing cranes, crews and replacement parts to remote turbine sites is very costly – particularly when the sites are offshore. Being able to predict failure requires building reliable trends from data that are comparable. SKF WindCon can build reliable trends of comparable data from wind turbines that are designed to adjust constantly to their ever-changing working conditions.
Constantly changing loads
A wind turbine sees constantly changing wind conditions. Sudden high wind gusts will generate high peak loads on the bearings, gears and generator. A monitoring system should not be fooled by these high peak loads and associated high sensor values. In addition, the system should be able to safeguard flawless operation at all times by detecting even the smallest bearing or gear fault development at times of low winds. SKF has developed intelligent diagnostic tools to take care of this complex aspect of wind turbine operation; in SKF WindCon, alarm level settings float and follow the actual wind conditions and power output. These floating alarm levels can be set to avoid other false alarms such as, for example, resonance frequencies that occur during acceleration.
Constantly changing rotational speeds
Frequency analysis is a standard identification tool in condition monitoring of rotating equipment. Frequencies are directly related to rotational speed. The challenge here is that a modern wind turbine reacts to changing wind conditions by adjusting its blades to optimize yield. As a result, its rotational speed will change. These unpredictable speed fluctuations pose unique challenges to the identification of damaging phenomena or faulty machine parts. SKF WindCon takes into account the bearing geometry and the gearbox design to recalculate permanently all the possible fault frequencies according to the real and actual rotational speed of the turbine.
Forecasting
Although SKF WindCon can be used for root cause analysis of damaged turbines to enhance repair and maintenance so as to avoid a reoccurrence, by far the most important savings can be made through forecasting. This requires knowledge of trends built up from comparable data taken under comparable circumstances. Order analysis, a standard technology used to monitor accelerating or decelerating rotating equipment, should not be used in wind turbines, as it may lead to faulty conclusions. Instead, WindCon can use several process signals to carefully choose the data that is suitable for storage in trends. So, although SKF WindCon constantly makes measurements to match against alarm settings, it only stores data in trends that are comparable with previously taken data.
Remoteness
Turbines are found in the most remote corners of the world. Extracting data from the turbines may prove a challenge. The fleet of WindCon units in Europe, Asia, the United States and Australia gets its data to server computers every day using FM radio signals, copper-wire telephone cables, wireless GPRS, satellite, ADSL, ISDN and more. Sometimes the WindCon units operate in heavily secured company networks. For others, the units are directly exposed to the hostile environment of the Internet, with its hackers and viruses. While rolling out WindCon, SKF became a communication technology expert by accident.
SKF WebCon
Condition monitoring is perceived as a complicated technology, even for experts. Using SKF WebCon, condition monitoring results can be made accessible and understandable for employees without special engineering backgrounds. SKF ProCon Expert software runs on an engineer’s computer to make the complicated analysis and calculations, but WebCon provides access to all data through the Internet, using a browser. No special software is required. All possible alarms that could occur on a given machine part occur as tick boxes on the PC screen. When “ticking” a box, the associated identifier appears and the status of the machine part can be interpreted. Keeping an eye on turbines is now no longer limited to a small group of trained condition monitoring experts. Making data easily available, accessible and understandable to employees without a special engineering background will increase the number of eyes and ears in the company that can monitor the turbines.
An unusual application
At one UK company, a novel approach to condition monitoring truly paid off.
A WindCon unit was mounted on a 600kW wind turbine that had known damage on the low-speed part of the gearbox. A gearbox replacement was already being planned when WindCon was first installed. WindCon not only registered the damage, but it also determined that the damage was stable, so the gearbox replacement could be postponed and the damaged turbine kept in production, with WindCon closely watching its damaged part. After
11 months and three weeks, WindCon detected a rapid increase in the damage pattern, and the machine was taken offline for the planned gearbox replacement.
By postponing the gearbox replacement for almost 12 months, the owner was able to accrue interest on the money needed for the overhaul, which was almost enough to pay for the WindCon installation. But more important in terms of cost savings, the owner was also able to plan effectively for parts delivery, shipping, personnel and cranes for the replacement, something that would not have been possible with a rushed operation accompanied by several weeks of downtime.
Whereas the traditional objective with industrial condition monitoring is to predict failure and to replace the part before it fails or to take the machinery off-line when the failure is detected, in this case monitoring was used to keep damaged equipment running in a controlled manner for as long as possible, getting another year’s oper-ation out of a damaged gearbox.
Overall, condition monitoring is proving to be a cost-effective tool, thanks to the combined power of communications coupled with sophisticated software that simplifies the interpretation of turbine performance.