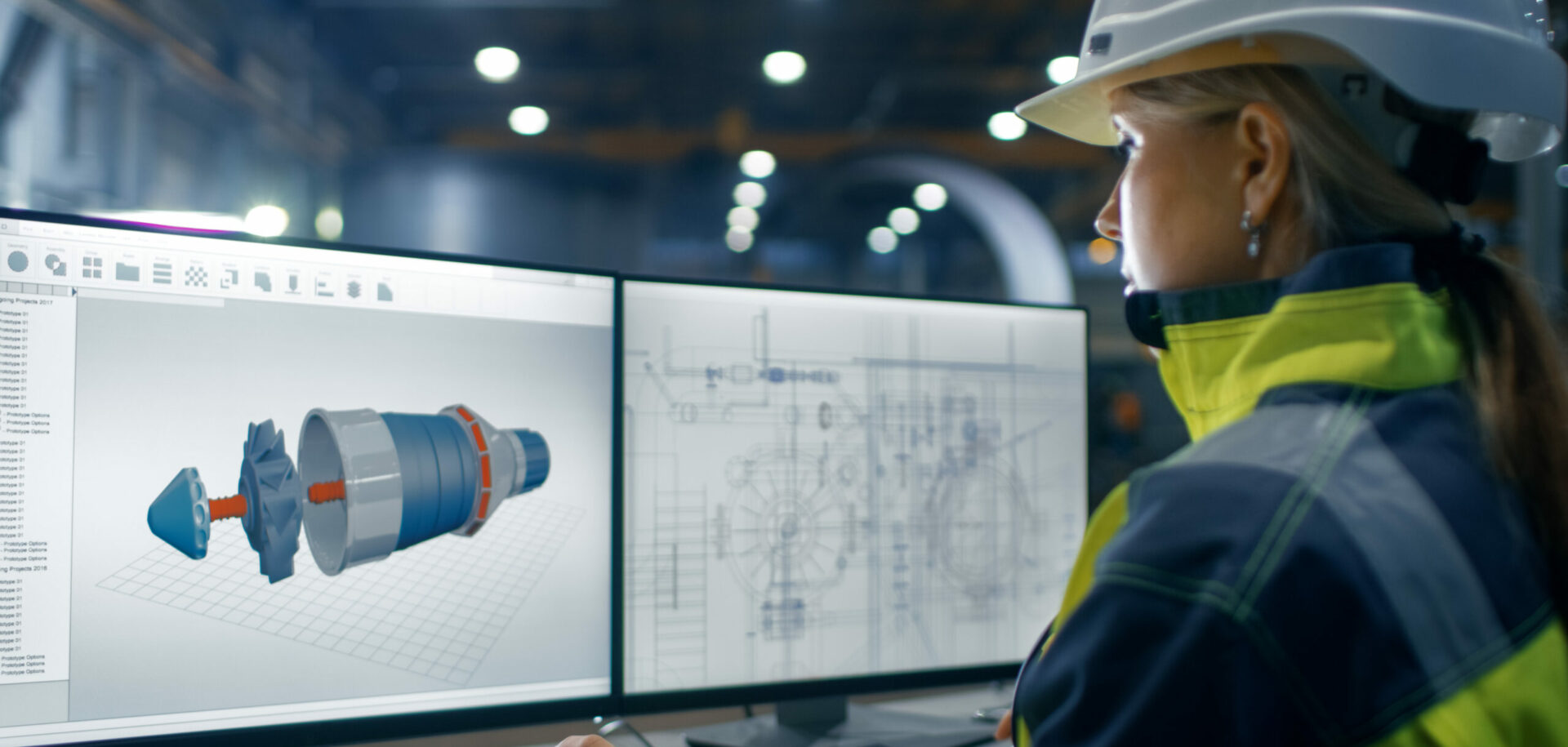
New axlebox concept for heavy loads
For many years the trend in the railway industry has been to carry heavier loads at faster speeds. Today, most railway freight cars in Europe are built to run with axle loads of 25 tonnes. SKF has developed a new Y25 axlebox concept that is equipped with compact tapered roller bearing units. This design offers opportunities to achieve lower life-cycle cost through longer maintenance intervals, simplified maintenance operations and improvements in performance and safety.
The European freight railway traffic is in a period of transformation due to the need to move freight, that is now transported by truck on crowded motorways, to rail. This long, ongoing process goes hand in hand with greater environmental sensibility. To gain more freight for rail transportation, an improved customer service is needed. The main issues are more flexibility in logistics and customized technical designs for rolling stock. New freight operators offer extended services, especially shuttle trains, which operate as a fixed block without time-consuming shunting operations of single cars. Transportation time can be reduced dramatically. Special freight cars are tailored to customer needs, e.g., to increase the payload, to achieve an easier loading process or to improve the protection of the load against damage. In addition to container cars, special freight cars are designed for truck-trailer transportation, such as advanced pocket cars for combined road and rail transportation.
Railway freight operation requires technical and economical solutions with low life-cycle cost. As a consequence axlebox bearing designs must be developed that will result in less or even no maintenance requirements. Axlebox bearings must be able to operate under fully loaded cars and under extreme climatic conditions. Even if locomotives with a very high power rating are used, the frictional moment resulting from the axleboxes has to be as low as possible to save energy consumption.
European railways use both two- and four-axle freight cars. For heavier loads a four-axle version is more suitable. In most cases these cars are equipped with two Y25-type bogies. In principle two different bogie frame designs can be used, based either on welding or on casting production techniques. This Y25 bogie design is also used by some railway operators in Asia and is state-of-the-art now for more than three decades. The new Y25 bogie design is equipped with axleboxes guided with special wear plates and supported by steel coil springs on both sides.
In the past there were several different axlebox designs used to accommodate spherical, cylindrical or tapered roller bearings. These open bearings must be protected against contamination and grease losses. A full-bore housing needs to be applied with a sealing system located close to the wheel. On the opposite side a front cover is fitted with several screws on the axlebox body. This design is relatively complex, and the performance relies on a proper mounting. Bearings must be greased manually and installed in a very clean environment to avoid contamination.
SKF developed a completely new axlebox design. This has been made possible by incorporating the SKF Compact TBU. The axlebox matches the same mechan-ical interface of the body frame and the coil springs. This makes it possible to upgrade existing bogies with the new SKF axlebox design as well.
The key to a lower life-cycle cost is design. The compact design of the TBU offers new opportunities to achieve longer maintenance intervals and to improve perform-ance and safety.
The compact design consists of fewer parts and offers mass- and space-saving opportunities as well as housing design simplifications. The new SKF bearing design for Y25 bogies is based on the new CTBU 130 x 240. This bearing unit fulfils the requirements of the European standard EN 12 080, focused on the bearing material and quality requirements, as well as the EN 12 081 standard concerning bearing grease lubrication specifications. Furthermore, the CTBU 130 x 240 has passed the endurance testing requirements in accordance with the EN 12 082 standard. The SKF testing methods are much tougher than the real running conditions in the field (see Evolution 3/1997).
Compared with previous designs for Y25 bogies, the main user benefits of the compact TBU bearing units are:
- Shorter axle length for new bogie designs, reducing axle bending under the bearing and unsprung weight.
- Improved safety and performance through the use of polyamide cages instead of the traditional steel cages, resulting in less wear and reduced grease contamination.
- Avoidance of fretting corrosion in the inner ring/backing ring contact zone, achieved by the use of a polymer spacer.
- Improved protection against contamin-ation due to the incorporation of a newly designed low-friction contact seal that rides on the inner ring shoulder.
- Longer lubricant life, using a new long-life grease.
- Simplified and easier mounting.
The sensible greasing process for previously used unsealed axlebox bearings is done at the workshop of wheelset producers or overhaul facilities. Cleanliness, the proper grease quantity and distribution are compulsory operations. In case of a sealed and greased bearing unit such as the CTBU, this process is incorporated into the bearing production where these requirements can be achieved with a very high reliability.
In the new Y25 axlebox design,SKF has redesigned the Y25 housing completely to achieve simplified mounting and extended maintenance intervals, resulting in lower life-cycle cost. The CTBU design principle no longer requires the traditional full-bore axlebox housing with an integrated sealing system and a front cover. This helps to save weight and to simplify the axlebox housing design by reducing the number of parts.
The R&D work started with a complete design review of the existing Y25 axlebox; further design reviews were made during the complete development process. Several finite element method (FEM) computer calculations were made to achieve a lighter design with reduced machining requirements. Especially at the lower part of the axlebox body, two specially designed larger holes have been incorporated that help to save mass without increasing mechanical stresses. The validation of the new design was done by fatigue testing before starting field-testing under real operating conditions.
The one-piece axlebox body transmits the radial load via the upper part directly to the bearing unit. The axial forces are transmitted in both directions via the fully integrated shoulders of the axlebox body.
There are no loads transmitted via the lower part of the axlebox. SKF has used this opportunity to exclude machining of this area and to design a larger axial gap, which serves to mount the bearing unit into the newly designed shoulders of the upper part.
To prevent movement of the bearing out of the shoulders of the axlebox during handling of the assembled wheelset in the workshop, a special locking wedge is applied. This fills the radial gap between the bearing unit outer ring and the lower part of the axlebox body and protects the complete assembly. The locking wedge is screwed axially onto the axlebox housing.
The CTBUs are axially located on the wheel axles by newly designed end caps, which protect the sealing systems against contamination and other damage.
The main user benefits of the new SKF Y25 axlebox design are:
- Weight saving, around 20 kg per axlebox or 160 kg for a four-axle wagon, in comparison with previous designs. This reduces the unsprung weight of the wheelset by around 4 %, which contributes to the running performance as well as to reducing wheel and rail wear.
- Simplification of the axlebox assembly, fewer parts of the two main components – bearing unit and axlebox housing.
- Simpler and easier mounting, disassembly and maintenance.
- Lower life-cycle cost due to longer maintenance intervals.
- Increased safety and performance.
Applications
The positive field experience of this design for challenging railway applications in passenger and freight applications has led to very positive results (see Evolution 3/2004).
SKF has received several orders for the new Y25 axlebox design from freight car builders and railway operators. The largest order is for 14,000 axleboxes and CTBUs for a new generation of freight cars from AAE Ahaus Alstätter Eisenbahn AG. AAE is a European market leader in the rental of standard freight cars for combined and conventional rail freight. The order includes a service package based on bearing inspection and overhaul. This new axlebox design is expected to become the standard for AAE freight cars.