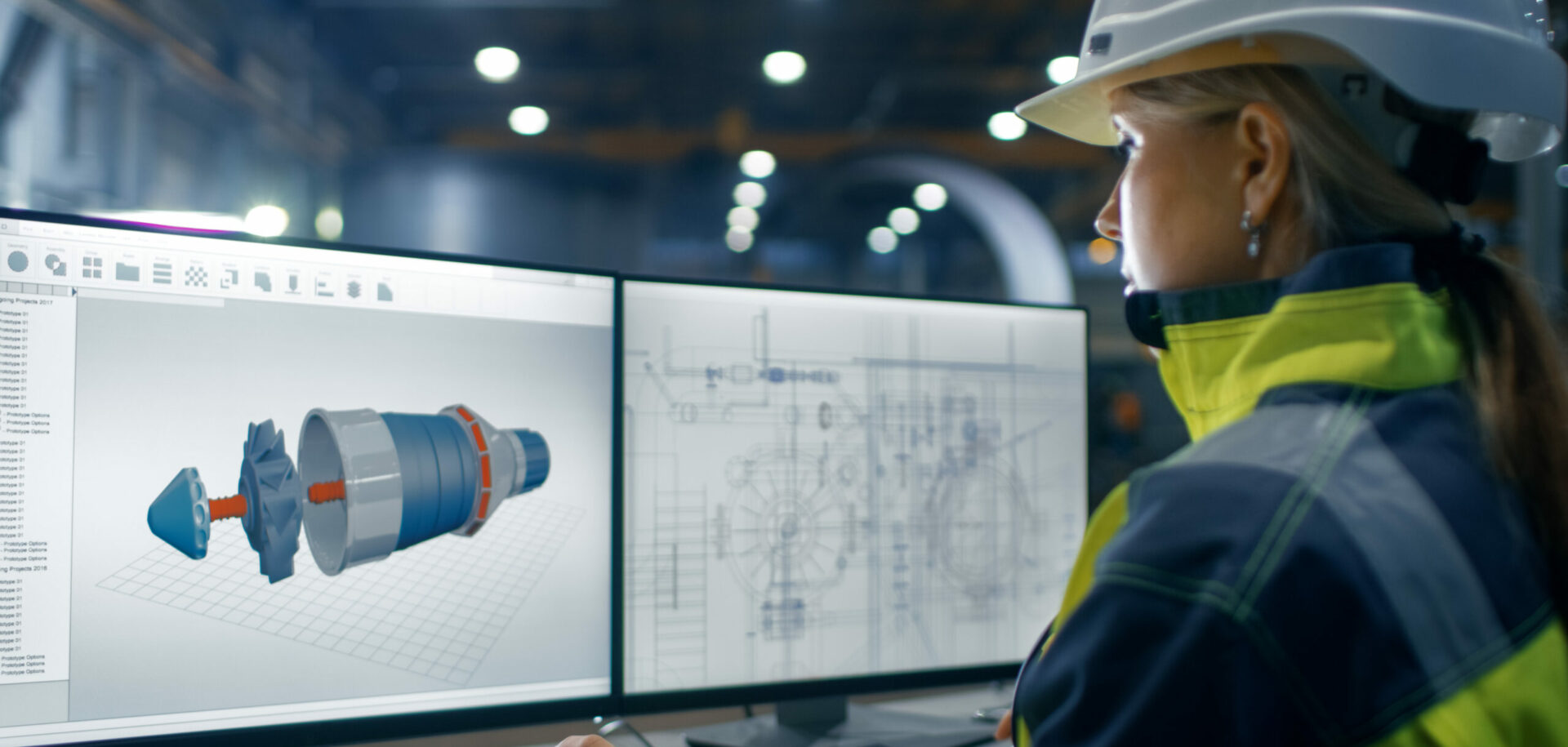
New generation of super-precision bearings: a tradition in evolution
A collaboration between SKF and SNFA engineers has led to new series of super-precision bearings that can be used for machine tool and related applications.
Summary
Machine tool manufacturers inhabit a world where productivity, precision and performance are bywords.
With the push for higher-speed operation, while maintaining process stability, SKF has introduced new series of super-precision bearings with machine tool and related applications in mind. These new series are the result of collaboration between SKF engineers and their colleagues at SNFA, specialists in machine tool bearing design, who became part of the SKF Group in 2006.
A collaboration between SKF and SNFA engineers has led to new series of super-precision bearings that can be used for machine tool and related applications.
Machine tool builders can now benefit from new series of super-precision bearings. Already demonstrated at major inter-national machine tool exhibitions, the new series are now rolling out.
The new bearings are the result of a collaboration between engineers from SKF and SNFA, following its acquisition by the SKF group. The new series have been designed to meet machine tools builder’s demands for bearings that are able to run at the highest speeds, with a high degree of accuracy, high rigidity, long service life and low energy consumption. All these features are contained in the new products, with different degrees of emphasis as a function of the series.
This has been achieved by combining the expertise of SKF and SNFA, using the best technology from each.
NEW 718 (SEA) SERIES SUPER-PRECISION ANGULAR CONTACT BALL BEARINGS
SKF-SNFA super-precision angular contact ball bearings in the 718 (SEA) series offer an optimal solution for those applications where space is very limited. They have a very slim bearing cross section (se bild . 1), especially in comparison with bearings belonging to other ISO Dimension series, coupled with a high degree of accuracy (according to ISO 4, ABEC 7 as standard and ISO 2, ABEC 9 on request) and rigidity. These bearings can be used successfully, not only in machine tool applications, but also on robotic arms and measuring systems.
Bearings in the 718 (SEA) series are avail-able as single bearings, sets of prematched bearings, universally matchable bearings and sets of universally matchable bearings. Bearings are available as standard with a 15° or 25° contact angle.
The basic features of the new series can be summarized as follows:
-
product range: from 10 mm to 160 mm bore diameter
-
large ball size for high carrying capacity
-
optimized corner radius design for improved mounting accuracy (se bild . 2)
-
three preload classes and two different preloading methodologies to meet different requests in terms of speed and rigidity
-
high speed capability (on average 3 % more than previous series)
An application example is shown in se bild . 4.
NEW S719.. B (HB ../S) AND S70.. B (HX ../S) SERIES SKF-SNFA SEALED SUPER-PRECISION ANGULAR CONTACT BALL BEARINGS
Two bearing series, S719.. B (HB ../S) and S70.. B (HX ../S) series, have been conceived with the specific purpose of being sealed. It is well known that the operating conditions of machine tools, in terms of cleanliness of the working environment, can be rather severe for the bearings. Field tests have shown that premature bearing failures are most often linked with contamination. Dust, chips, water or coolant liquids entering the contact area between raceways and rolling elements can result in indentations or inhibit the formation of a good lubricant film. Both can lead to shorter bearing service life. Bearings in the S719.. B (HB ../S) and S70.. B (HX ../S) series are fitted with seals made of acrylonitrile-butadiene rubber (NBR) to act as an effective barrier against contaminants. The main features and benefits of these bearings are summarized in the adjacent table.
Bearings in these series are manufactured as standard according to precision class P4A (ISO 4 for boundary dimensions and ISO 2 for running accuracy). Bearings are available as standard with a 15° or 25° contact angle. Bearings with an 18° contact angle are available on request. Three preload classes are available. These bearings, as with the other super-precision angular contact ball bearings, can be supplied as single bearings, single universally matchable bearings, sets of universally matchable bearings and prematched bearing sets.
In addition to the basic sealed version (se bild . 3a), an open version is also available (se bild . 3b). For applications where speed is extremely high and oil-air lubrication is to be used (se bild . 5), the “L”-execution featuring two lubrication holes and two grooves for O-rings in the outer ring (se bild . 3c) can be supplied.
An application example is shown in se bild . 5.
NEW HIGH-CAPACITY 72.. D (E 200) SERIES SKF-SNFA SUPER-PRECISION ANGULAR CONTACT BALL BEARINGS
Machine tools and other precision applications require superior bearing performance. Here, high system rigidity is one of the main performance challenges, as the magnitude of elastic deformation under load determines the productivity and accuracy of the equipment. Parallel kinematic machines (PKM), for example, are known for their ability to provide high structural rigidity and high dynamic capacities. But, this is only possible when the bearings incorporated in these machines step up to the challenge.
The ability of the new design of the super-precision angular contact ball bearings in the 72.. D (E 200) series to accommodate heavy loads and still provide a high degree of system rigidity makes them an excellent solution for these and similar applications.
SKF-SNFA bearings in the 72.. D (E 200) series are characterized by:
-
large ball size
-
high load-carrying capacity
-
high degree of stiffness
-
extended bearing service life
-
low heat generation
-
low noise and vibration levels.
The bearings provide high reliability and super-ior accuracy for applications such as PKM, lathe spindles, grinding and boring machines, high-speed dynamometers and turbochargers.
The extended range of bearings in this series now accommodates shaft diameters ranging from 7 to 140 mm. And, a relubrication-free, sealed bearing series is available on request. To accommodate the diverse
operating requirements of precision applications, bearings in the 72.. D (E 200) series are manufactured to two tolerance classes and with two contact angles (15° and 25°). Those suitable for universal matching or mounting in sets are produced to four preload classes to meet almost all application requirements in terms of speed and rigidity. Matched bearing sets with a special preload can be supplied on request. Most bearing sizes are available, standard, with a choice of two ball materials, and the most common sizes have a polyetheretherketone (PEEK) cage (se bild . 8) to accommodate extended operating temperatures.
An application example is shown in se bild 6.
All super-precision angular contact ball bearings are nearly always adjusted against a second bearing to balance the counter forces. To accommodate heavier loads and axial loads in both directions, the bearings are used in sets typically consisting of up to four bearings (se bild . 9).
NEW N 10 SERIES HIGH-SPEED SUPER-PRECISION SINGLE ROW CYLINDRICAL ROLLER BEARINGS
Precision applications demand a high degree of system rigidity, as the magnitude of elastic deformation under load determines the productivity and accuracy of the equipment. Another performance challenge is keeping the amount of friction and heat generated by the bearing to a minimum during high-speed operation.
To meet these demanding performance criteria, the N 10 series cylindrical roller bearings have an optimized internal geom-etry and a redesigned cage, enabling them to accommodate a speed increase of up to 30 %.
The bearings are characterized by:
-
high-speed capability
-
high load-carrying capacity
-
high stiffness
-
low friction
-
a low cross-sectional height.
The non-locating bearing position is typically at the non-tool end of a spindle. If this bearing has a loose fit, it can have a negative influence on the total rigidity of the bearing arrangement. Therefore, for a high degree of stiffness at the non-tool end of a spindle, an N 10 series cylindrical roller bearing with a tapered bore should be used. It accommodates axial displacement within the bearing and is mounted with an interference fit on the outer ring, while the inner ring is driven on the tapered shaft to reach the wanted preload or radial clearance. N 10 series bearings provide high reliability and superior accuracy for applications such as high-speed milling machines, machining centres and lathes.
SKF-SNFA bearings in the N 10 series can accommodate shaft diameters ranging from 40 to 80 mm. They are available with a tapered bore only and are manufactured to two tolerance classes. To accommodate increased operational speeds, the bearings are available in a hybrid variant.
The bearings are based on the ISO Dimension Series 10 and have a low cross-sectional height. They are able to accommodate relatively large diameter shafts to provide the necessary system rigidity within a relatively small bearing envelope. When compared with a set of angular contact ball bearings with the same load-carrying cap-acity and the same degree of rigidity, an N 10 series bearing requires a much smaller radial space. This enables compact spindle bearing arrangements.
Super-precision single row cylindrical roller bearings in the N 10 series are designed for bearing arrangements requiring increased speed capability, high load-carrying capacity and a high degree of radial stiffness. Their features include an optimized internal geom-etry, a flangeless outer ring and a high-speed cage. The bearings are separable, making it possible to separate the inner ring and roller and cage assembly from the outer ring to facilitate mounting and dismounting.
N 10 series bearings are equipped with an outer ring centred, window-type cage made of carbon fibre reinforced polyetheretherketone (PEEK). The symmetrical, self-centring design enables the cage to be better guided on the raceway of the outer ring, compared with previous designs. The cage also offers excellent guidance for the rollers and provides access for the lubricant (typic-ally oil-air) to reach the contact areas between the cage and the inner ring flanges. The exceptional properties of PEEK provide a superior combination of strength and flexibility at high operational speeds. PEEK can also accommodate high operating temperatures while providing high chemical and wear resistance. Compared with previous high-speed design bearings, the new, optimized cage can accommodate a speed increase of up to 30 % in grease-lubricated applications and up to 15 % in oil-air lubricated applications.
An application example is shown in se bild . 7.
THE MAIN FEATURES AND BENEFITS OF BEARINGS IN THE SKF-SNFA S70.. B (HX ../S) AND S719.. B (HB ../S) SERIES ARE:
Features
Non-contact seal on both sides
Benefits
High-speed capability and low temperature rise
Efficient sealing against contaminants
Grease retention, preventing lubricating problems independently by axis orientation
Features
Pregreased for life
Benefits
Precise grease quantity
Eliminate risk of incompatibility between grease and washing fluids
Avoid possible contamination during spindle assembly
Do not need regreasing
Specific high-speed grease
Ready to mount unit
Features
Small ball size
Benefits
High speed, due to low centrifugal forces and high rigidity
Features
Outer ring guided cage
Benefits
High-speed capability
Features
Ball material
Benefits
Mainly ceramic, to accommodate high speeds
Steel balls also available.