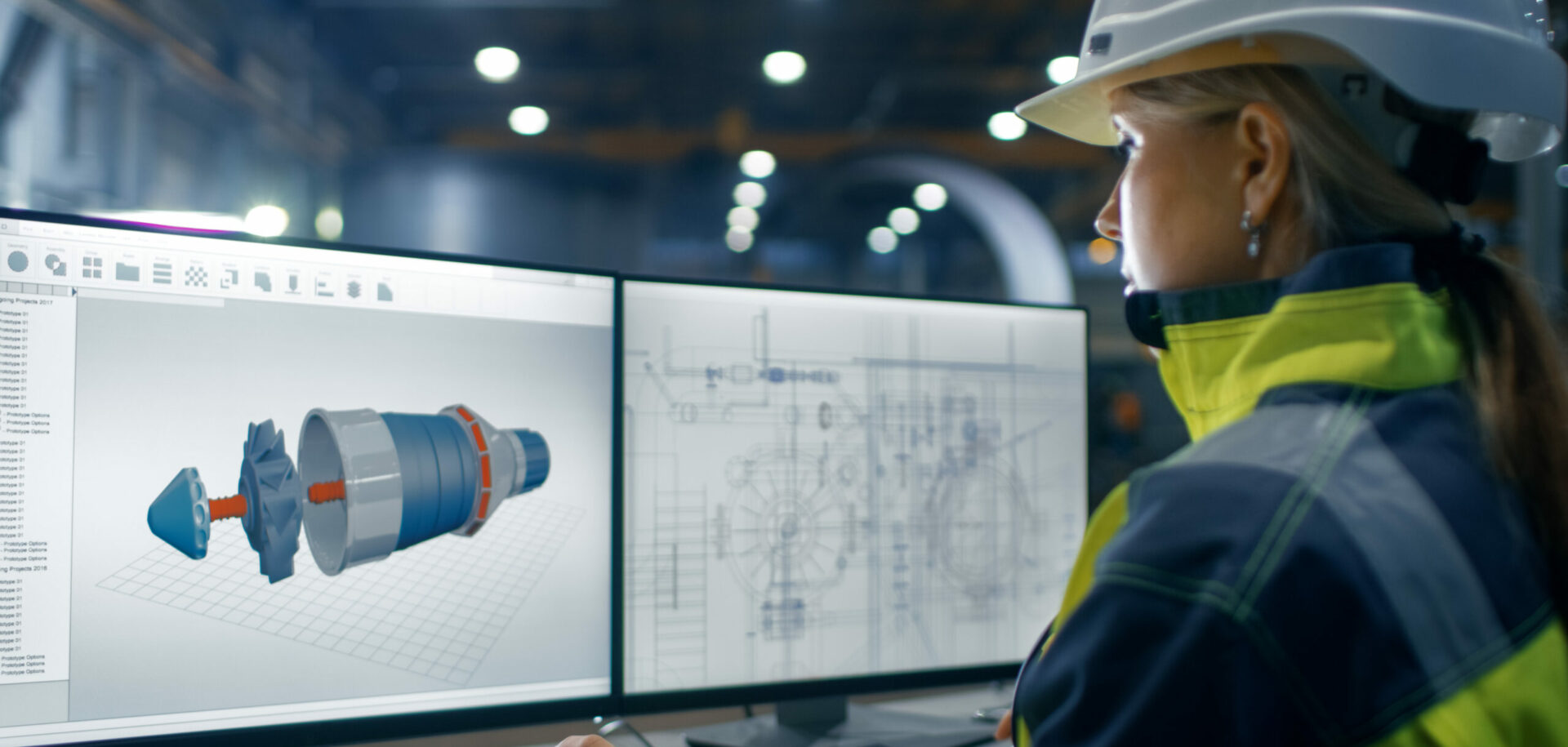
New perspective to motor design
A British company has developed a type of induction motor based on an axial air gap concept. Sporting an unusual, compact shape, the new motor offers a range of integrated solutions to customer applications.
Summary
Major motor manufacturer
Electrodrives is a major British manufacturer of squirrel cage induction motors used in a wide variety of industrial applications. As a member of the Brook Hansen group of companies within BTR, a leading international engineering group, Electrodrives has a large share of the British market.
It has an annual turnover of around £30 million (US$49 million) and a work force of 480.
BTR acquired Electrodrives as part of Hawker Siddeley in the early 1990s. It lies within the group’ s £1 billion turnover Power Drives division that produces high-performance electric motors, industrial gear units, couplings, roller and conveying chains. In total, this business division has 56 manufacturing facilities in 15 countries and a work force of 15,000.
Credibility from cars
Electrodrives has developed an axial air gap motor that offers the possibility of new, integrated solutions for customer applications. In designing the motor, Electrodrives engineers had to take a close look at bearing solutions.
For an axial motor design, the bearing must be able to cope with higher thrust loads than conventional squirrel cage designs. In the fan application, the SKF hub unit sits in the very heart of the rotor. Its main role is to maintain the uniform air gap that guarantees the motor’ s electrical performance.
Having experimented with one bearing arrangement that proved unable to deliver the high levels of reliability required, Steve Hurley and his Electrodrives team rethought the design. Hurley realised that, like the integrated solutions he was seeking for his customers, he too needed an integrated solution. He asked SKF if it was possible to incorporate Hub Unit 1, as used for automotive applications.
It worked. In essence Hub Unit 1 is a double row angular contact bearing with a split inner ring and is sealed and greased for life. This unit is a proven design that is a standard component on a number of car models.
Adapting the motor to accept the hub unit was relatively straightforward. It sits tightly on the rotor shaft and is pre-loaded with a set torque sufficient to maintain the specified air gap.
As automotive applications require high reliability and volume production, the bearing unit had the right credentials for use in the fan application. “It is a well-engineered solution that gives credibility to new products,” says Hurley.
This was particularly reassuring to the fan customer.
A British company has developed a type of induction motor based on an axial air gap concept. Sporting an unusual, compact shape, the new motor offers a range of integrated solutions to customer applications.
In a highly competitive market, Electrodrives Ltd., based near Birmingham, is a company that has dared to be different. It has spent £2 million (US$3.25 million) on the research, development and construction of a new automated plant for the production of an unusual type of electric motor that is already proving its worth by providing novel solutions to customer applications.
Within the first year of volume production of the axial air gap induction motor, the design was incorporated into a fan unit for air-conditioning systems and many thousands were installed. Other applications have not only been identified but are planned to be introduced at the rate of at least two a year, according to Steve Hurley, engineering manager of Electrodrives and the man who developed the air gap concept.
For Electrodrives, the new type of induction motor not only sets the company apart in a keenly competitive market, but it gives company designers the opportunity to integrate the motor into customer applications. Increasingly, original equipment manufacturers are seeking greater integration of key components in machine design. Integration adds benefits in terms of savings on components, weight and cost, and in addition, customers get a tailored solution to their particular design problems.
The axial air gap motor puts Electrodrives into a stronger competitive situation in its markets while offering its customers a motor with particular attributes. Traditionally, the induction motor is the workhorse of industry. Hurley explains: “The benefits of using the axial air gap motor include a shorter case, a unit that is easier to package and distribute, easier assembly, better motor cooling and higher outputs.”
The concept of the axial air gap motor is not entirely new. The idea was first proposed in Switzerland in the 1940s but was used for only limited application. Electrodrives has designed the motor so that it can be mass-produced and meet the full rigours of industrial operation across a wide range of applications.
Flat as a pancake
Conventional induction motors power many industry applications; their squirrel cage rotor construction provides better reliability and value for money than other types of motors can provide. In the axial air gap version, the principle is identical but the shape of the motor is radically altered. Here, the rotor and the stator are both flattened, rather like pancakes. The rotor does not sit inside the stator but lies adjacent to it. Magnetic flux passes across the narrow air gap that separates the stationary and moving components of the motor.
Therein lies the key to the development of the motor commercially. Hurley explained that the width of the air gap is critical. It must be large enough to keep the rotor and stator apart but narrow enough to provide satisfactory performance. Another characteristic of this air gap is that it must be uniform across its entire plane. Without a uniform air gap, flux density varies, which adversely affects performance and increases motor noise. In production, this means a tolerance of about 0.025 millimetres.
In operation, the motor’s air gap also must be kept close to its tolerance limits. This is achieved through the bearing arrangement that was supplied by SKF.
The result of the development work is a thinner motor, not unlike the cartoonists’ image of a flying saucer, which offers original equipment manufacturers and other machinery producers new design opportunities. Typically the air gap model would be one-third the length of a conventional induction motor of equivalent power.
The company took a cautious approach. They identified four major market sectors for their traditional markets – pumps, fans, hoists and floor polishers – that they felt could benefit from the air gap design. After consulting a number of customers in these markets, they created joint development projects, of which one of the first was a fan application for air-conditioning equipment.
Normally an air-conditioning plant is situated on a rooftop. This motor design offered fan manufacturers the possibility of reducing the overall profile of fans in this limited space. For Electrodrives, this meant giving customers that extra selling edge in a highly competitive market.
It was also important that Hurley and his team provided a solution that would live up to the expectations of high reliability and performance normally associated with its traditional products. “We offer high-quality products and service to sustain price levels and fend off cut-price imports,” he says. So the axial air gap motor design was put through an extremely rigorous series of tests specified by the customer. So far, the motor has exceeded the expectations of the clients with few failures.
In the end, Hurley says, “know-how is the key.” It is all about “exclusivity and building relationships with customers.”
Elaine Williams
Evolution’s technology editor