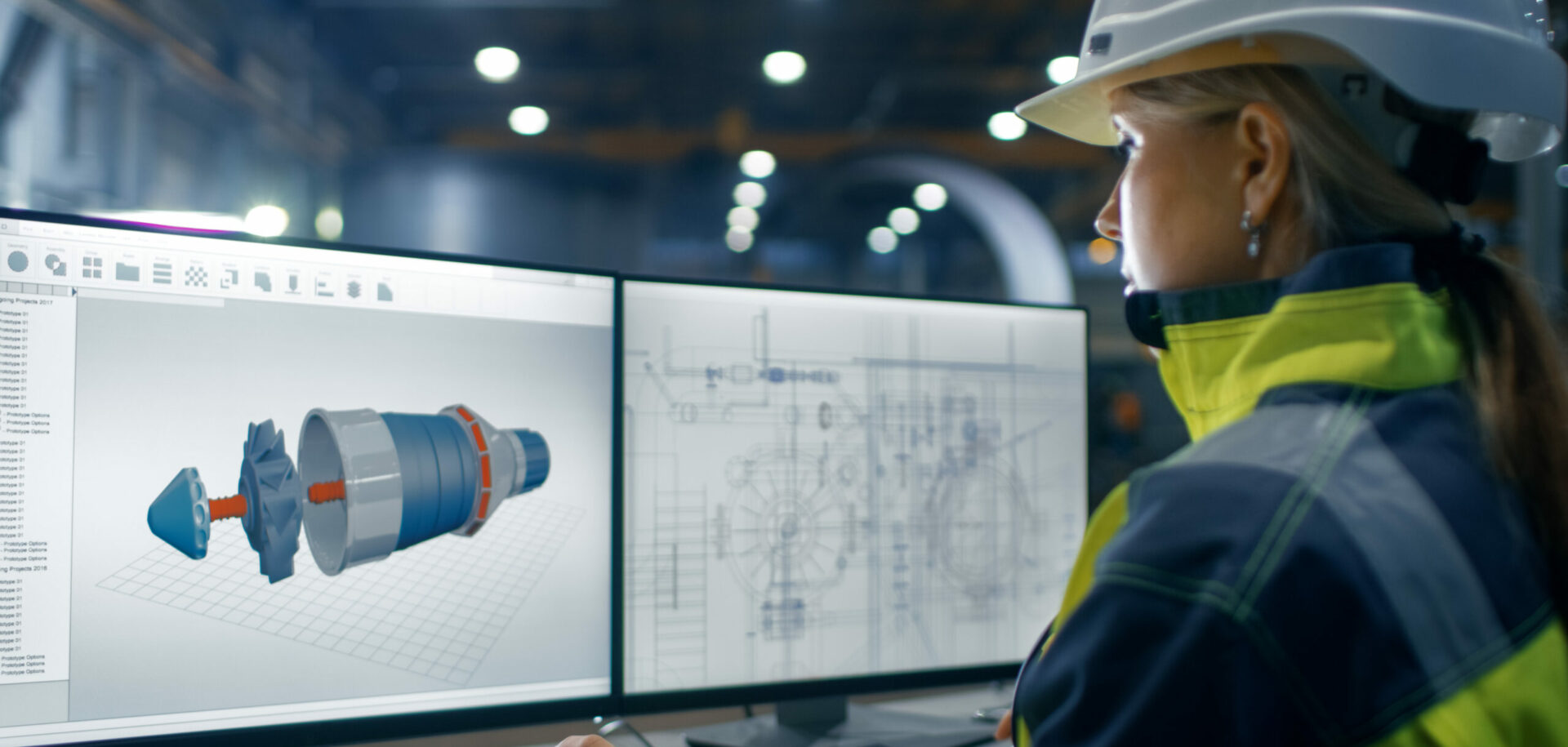
New technology lowers cost per aircraft passenger
Composites and titanium are increasingly replacing aluminium and steel in aircraft. This and fly-by-wire technology are two routes to more cost-efficient operation.
Reducing the cost per passenger is a major goal for all aircraft manufacturers. Weight savings for structure and consumption efficiency with flight by-wire systems are the two main ways. They offer greater fuel economies and lessen the environmental impact. The use of alternative materials to aluminium and steel, such as composites and titanium, and the fly-by-wire concept are a growing part of the strategy for aerospace companies to achieve the savings they need to make to offer airlines cost-efficient operation over the lifetime of the aircraft.
The industry faces continued pressure to produce aircraft that have less environmental impact and, for commercial designs, in particular, that have lower operating costs over a longer operational life. Integration and collaboration between companies in the aerospace industry has been increasing because of the high cost of developing new technologies for the sector.
Any company competing in the global aerospace sector needs to have both technical competence and a support network that can reach around the world. Three years ago, SKF created its own dedicated aerospace group, bringing together five subsidiaries that offer key technologies for present and future aircraft designs.
Within SKF’s aerospace group, SARMA is a company that offers a range of products and specialized technologies that are designed to support the industry’s overall aims. It is, for example, the leading European player in special and integrated bearings for civil and military aircraft programmes. SARMA, which has origins that go back to 1932, has been a member of the SKF group since 1975.
SARMA concentrates on three broad product ranges that are used throughout the aircraft frame. They are:
- Metallic and composite rods and struts for structural, flight control applications and facilities;
- Ball, roller and spherical plain bearings for landing gears, flight controls, wings and engine links; and
- A wide range of mechatronics, including position and force transducer units, and linear and rotary actuators for cockpit, flight control and utilities actuation.
Supporting these technologies is an emphasis on materials and processing technologies to support its product development. More recently the company has established new facilities with the latest technology for production, R&D, testing, quality and information technology at its head office in France.
Process technologies underpin the company’s business. SARMA holds a decisive lead in composite technology. The resin transfer moulding process, RTM, is a process that the company has developed for the manufacture of composite rods from carbon fibre and a polymeric resin. Such materials (i.e., composite) have good mechanical properties and a low density, which has made them an alternative to steel and aluminium.
Components are initially designed using a CAD system that takes into account design and stress calculations. The cutting of the carbon fibre material is carried out automatically to reduce dimension errors; this is followed by pre-forming and moulding steps. The resin needs to be injected into the mould to make sure that the liquid resin propagates uniformly throughout the mould. A vacuum pump system on one side of the mould draws the resin uniformly across the material. Following removal from the mould, the component is polished, machined, inspected and packed. RTM enables full control of complex shapes, repeatability and high-quality surface finishing.
For metal components, SARMA also uses a forming method called swaging, which reduces a regular or irregular section of tube to a pre-determined diameter using dies, which surround the tube. Two swaging techniques are used: plunged swaging and stationary spindle swaging. Plunged swaging, which is used for diameter reduction, results in feeding the tube into an axial working position with fully open dies. Then the dies are plunged and the forming operation is carried out. In the alternate technique, the tube is fed axially at constant speed through oscillating dies, and the tube rotates. Applications include creating internal profiles to insert and fix parts to the tube.
Applications for airframe rods, both metallic and composite, include flight control actuation, landing gear actuation and the wingbox. The wingbox is integral within the fuselage and is held in position by front and rear spars. It is subjected to tensile as well as compressive loads. Additionally, the wingbox also acts as a fuel tank, so the rods, which support the structure, are saturated with kerosene fuel. SARMA engineers have investigated the potential for weight saving using composite as well as aluminium. They found that the use of composite rods as struts in the wingbox results in a 40 % weight saving.
SARMA was initially set up to develop bearing systems. Today that range covers swaged spherical plain bearings, split ball plain bearings (SARMA patented) and slotted entry plain bearings. In 2004 SKF announced the development of a range of lightweight, titanium plain bearings that offer a weight saving of up to 40 %, with applications in landing gears, pylon attractions and wing assemblies. Ten different applications have been defined, including a pylon-to-wing attachment bearing, a spigot bearing and, for the aileron reaction, a strut rod end. The first application of this bearing will be in the Airbus A380, due to go into service in 2006. By adopting this design, the A380 will achieve a 45 kg weight saving per landing gear and 110 kg weight saving per aircraft, including the nose landing gear.
The introduction of the bearing involved adapting the surface properties of titanium to overcome the difficulties of working with titanium. This resulted in a certain amount of re-engineering work, a new manufacturing process and an advanced coating and alloys, adding up to a patented split ball bearing design.
The third major product area for SARMA involves fly-by-wire technology. The company was one of the first equipment manufacturers to invest in fly-by-wire technology as a partner in the development of flight controls for the Airbus A320. The functions that the equipment can provide include: acting as the interface between the pilot and the flight-control computers; control of the aircraft during taxiing, take-off and landing; forward and reverse thrust power control of each engine; spoiler and speedbrake operation; and utilities actuation, such as controlling doors and air cooling. For example, the company has developed a door actuator for two business jets, the Dassault Falcon 900 and 2000, which forms part of the door-lifting mechanism.
The actuator replaces a mechanical system that required intensive maintenance, had too much friction and operated at a speed that was too fast for the application. The unit is in two main parts. The first part is the main assembly, with a four-stage reduction gearbox, a three-phase brushless motor and a potentiometer, which monitors the door position. The second section is the line replacement unit, which controls the motor current and, consequently, the speed of the door opening and closing.
The products that SARMA uses to realize these applications include fly-by-wire technology, position and force transducer units and linear and rotary actuators. One example includes SKF’s throttle control unit, which transmits the pilot’s control movements to the engine. This plug-and-play unit combines analogue and digital control technology and interfaces with the engine control computer and monitoring systems and includes auto-throttle capability and many other ergonomic functions.
To be used on the new A380 is a horizontal tail plane system that is part of the tail assembly and enables the tail to beadjusted from +2 ° to -10 ° to maintain aircraft stability. The system consists of a bearing assembly that provides the hinge, and attachment points for the trimmable horizontal stabilizer that controls the horizontal attitude, or pitch, of the aircraft. An actuator controls the hinge in rotation slowly, to adjust the angle of the horizontal stabilizer to trim out any deflection of the elevator in response to commands from the pilot or autopilot. When this happens, the horizontal stabilizer pivots on the two horizontal spherical plain bearings.
The bearing assembly for the horizontal tail plane consists of a fail-safe hinge assembly and a metal-to-metal spherical plain bearing. The main body of the fail-safe hinge assembly is made from titanium and is anodized for protection against galvanic corrosion. It must withstand compressive radial loads, tensile axial loads and fatigue due to these loads. The maximum load for the outer hinge is 1,300 kN, and the axial load for the hinge rod is 500 kN.
As this horizontal tail plane system plays a vital role in the stability and safety of the aircraft, a fail-safe system has been incorporated to enable a dual load path for the hinge assembly and the spherical bearing.
Stability and control are also issues at the front of the plane.
The Airbus A320 and A330/340 families employ a nose wheel steering control unit developed by SARMA. This equipment is used to steer the aircraft before take off and after landing on the runway and replaces a mechanical system. The “wire” control is more accurate and offers weight saving because it eliminates the mechanical link between the cockpit and the hydraulic system.
There are two units per aircraft. The unit transmits the hand wheel position to the braking and steering computer system, which gives the order to the servo hydraulic actuators, which drive the nose wheel. For the A330/340 family, the Sarma engineers have also developed a damping version of this equipment that is designed to reduce lateral tail movements, which otherwise would make the ride uncomfortable for passengers as the aircraft moves along the ground.
The adoption of many of the technologies and products developed by SARMA for the A380 generation reflects the depth of knowledge the com-pany has in the aerospace industry. It is also working with a number of other major players (Boeing, Embraer, Bombardier) within this sector, whose aims are to develop and improve the operational features of its aircraft designs.