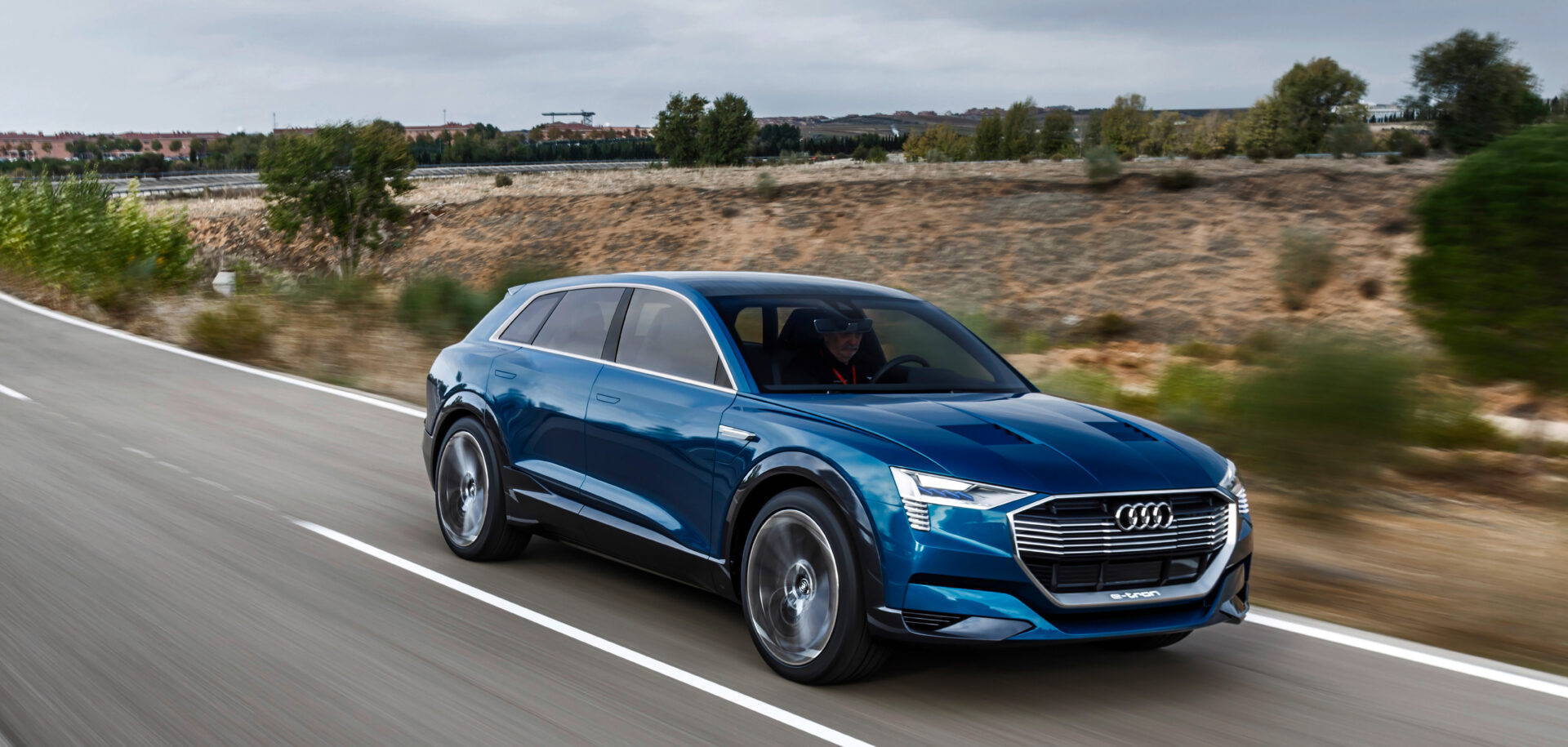
On the electric frontier
In 2018, the Audi car manufacturing plant in Forest, Belgium, will take on a new mission. It will be repurposed to produce Audi’s first fully electric vehicle, the e-tron.
We are excited to showcase our technology in the capital of Europe.
Andreas Cremer
secretary general
The plant in Forest (Vorst) has flourished ever since. “It was originally established by the Belgian D’Ieteren family, who seized the opportunities offered by Belgium’s post-war tax breaks for car assembly to encourage employment,” says Andreas Cremer, secretary general of Audi Brussels. “Indeed, it was one of many car plants that sprang up during that time, making Belgium the world’s leading car producer per capita back then, producing 1.5 million cars per year for a country population of some 9 million.”
The Forest plant in figures:
- 54 hectares
- 1.7 kilometres in length
- 2,525 employees
- 16/5 operation (16 hours a day, five days a week)
- 500 Audi A1 vehicles produced daily
SKF at the Forest plant
SKF provides the Forest plant with lubrication systems for the conveyors on its production lines. The systems are automated, regulating the dose of lubricants according to the needs. Sensors measure the quality of the injection at the point of contact to make sure that the lubricant has been correctly delivered at the right place. This information is sent back to the software designed by SKF and integrated by Dürr. Through this lubrication solution, every lubricant point in the production lines is permanently observed and monitored to ensure smooth operation, without disturbing production.
Until the 1970s, the Forest factory assembled American cars and also had a contract with Volks-wagen to produce Beetles, Golfs and Transporters, amongst others. On 1 January 1970 the D’Ieteren family sold the plant to VW. Then in 2006, when VW underwent a major production reorganization, Audi took over the factory and dedicated it to the production of its A1 model. The factory prepared for production of this Audi model in 2007, and it was launched in 2010.
“Since then, we’ve been producing the Audi A1, the Audi A1 Sportback, the Audi S1 and Audi S1 Sportback for all international markets, representing around 100,000 units annually,” Cremer says. “The A1 production is due to stop in Brussels in 2018, which is when we go over to producing Audi’s flagship full-electric vehicle, the e-tron.” Production for the next generation of A1 vehicles will be moved to Spain.
The Audi e-tron is a sporty SUV, equipped with a long-range battery and three electric motors, offering a range of more than 500 kilometres and quick-charging capacity. The car was first presented at the Frankfurt motor show in 2015. The Forest factory will initially produce the e-tron model, but it will introduce the e-tron Sportback, an elevated sports sedan version, in 2019.
“It’s very prestigious for us to be tasked with producing this flagship range,” says Cremer. “E-mobility is very much in vogue. It’s the technology of the moment as well as a key to our future business and to achieving our emissions goals. We are excited to showcase our technology in the capital of Europe and show how dedicated we are to clean driving.” For employees of the Forest plant, production of the e-tron will provide an opportunity to gain experience and skills related to this important new technology.
The challenge now is phasing out the present models and phasing in the new ones. Since January 2016, a team has been working on the transformation process, building new assembly lines, tearing down old buildings and constructing new ones. It’s a complicated process, says Cremer. “Imagine flying a plane from London to New York and having to change the engine mid-flight – that’s a little like what we are doing right now,” he says. “We might be sleeping a little less because the planning is very tight, but Belgian expertise, improvisation and creativity are key to the success of this new project, and we have that in spades.”
The Forest factory is relatively small, with fewer than 3,000 employees. In comparison, Audi’s headquarters in Ingolstadt, Germany, has 30,000 employees, and the second-biggest production plant, in Neckarsulm, Germany, has 25,000 employees. But, says Cremer, the small size works. “We are speedy, and we get stuff done, which is why the group selected us for the e-tron,” he says. “We are motivated, we’re flexible, and we’re dynamic. This is a family you want to be part of.”
And what of the future for the Forest plant? “I hope that after the e-tron and the e-tron Sportback, we’ll be assembling the next generation of e-cars, and maybe even the first generation of fuel cell vehicles,” Cremer says. “But one thing is clear: We must be flexible, and we must apply for each new project on offer, without resting on our laurels. The board won’t come bearing gifts, even if we are successful with the launch of the e-tron. We need to go to them and show them the quality that we can offer here. The future is a very exciting place for us.”