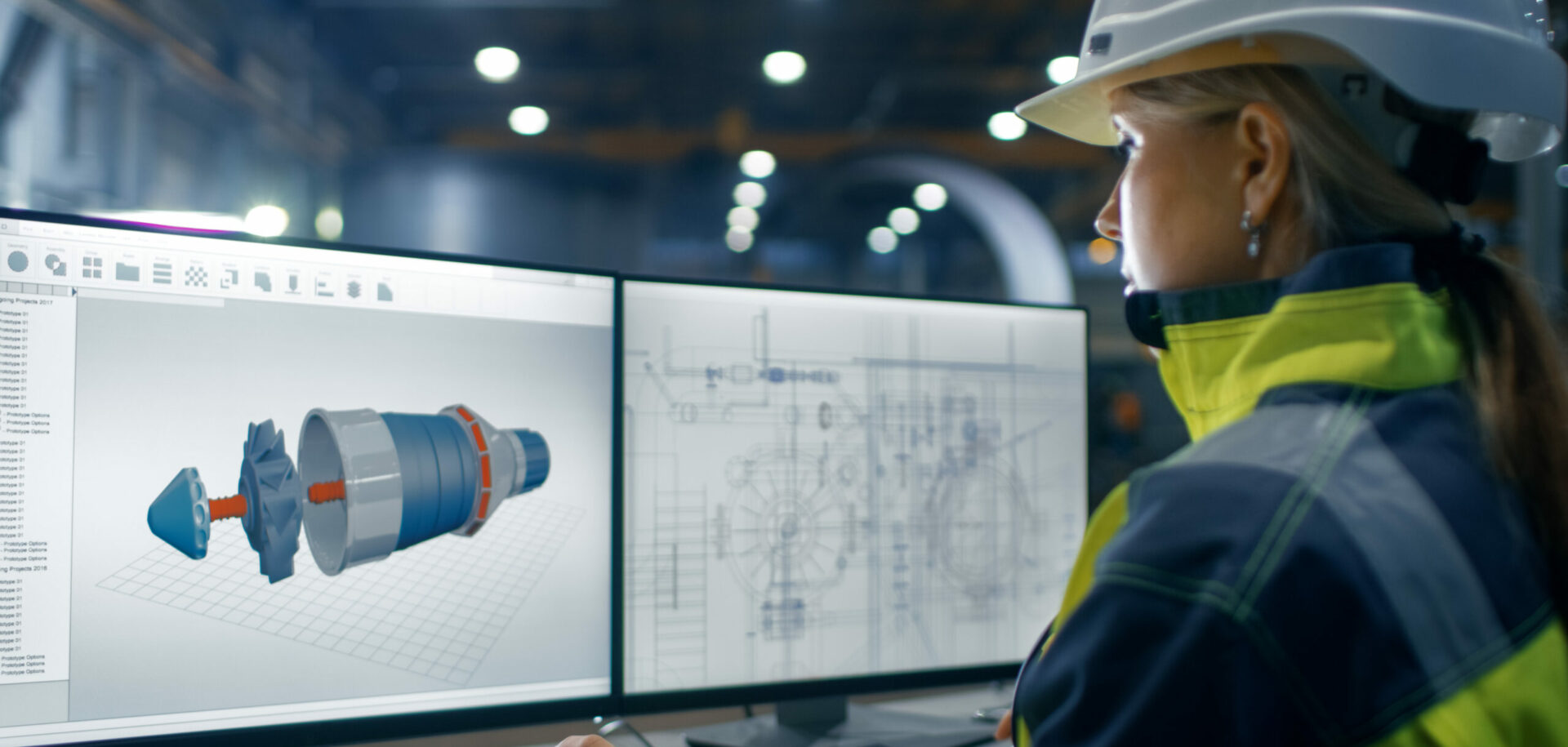
Optics made to measure
A Belgian high-tech optical/mechanical company sets its sights on the stars – and other heavenly bodies.
In 2004, when astronomers first observed the planet 2M1207b, the first directly imaged planet outside our solar system, it was through the tele-scopes at La Silla Paranal Observatory in Chile. In one of its facilities, the observatory is using optics made by Advanced Mechanical and Optical Systems, or AMOS, for its 3.6-metre telescope. Now another telescope with a 3.6-metre-wide mirror, made for ARIES, the Aryabhatta Research Institute of Observational Sciences in northern India, is about to journey from the AMOS plant in Belgium to Devasthal, a 2,500-metre-high mountain in Uttarakhand, where ARIES is situated.
“It is not only technical requirements that must be fulfilled,” says Jean-Pierre Chisogne, sales and marketing director at AMOS. Chisogne has test-driven the last 400 kilometres, right to the location of Devasthal. “We have to find out how our products can be transported to their destinations, and that has an impact on the design and the lead time.
“At every curve my colleague said ‘no way’,” he continues, remembering the trip up the mountain, “but it will work, despite the narrow roads and the cows blocking the way.
“AMOS is located outside the city of Liège in Belgium,” Chisogne explains. “We have the river Meuse almost outside our windows and can ship our equipment for satellites and professional astronomy anywhere via the harbour of Antwerp.”
AMOS has about 80 employees, more than half of whom are engineers or technicians – mostly graduates from the University of Liège and the prestigious Institute of Astrophysics.
“Our engineers want challenging problems,” Chisogne says, as he escorts his visitors from Evolution through the silent, open-plan office where spectacular 3D designs show up on every screen. “The workforce is quite young and at the very front edge of the field of designing and manufacturing optical instruments. They are eager to solve new problems or else they get bored.”
Most of the products from AMOS are custom-manufactured for a specific purpose. The prototype is what’s sold, which makes it difficult to predict where problems (not always linked to the technology) may appear.
“When producing unique pieces, pricing is an issue,” explains Chisogne. “How do you know what something will cost when you have never made it before? Occasionally we don’t earn enough money, and sometimes our estimates are too low. But preparing offers and always having the latest technology at hand makes my work very interesting.”
We enter a workshop filled with people, huge devices, laptops, plans, and screwdrivers. The majority of the projects have been running for many years, Chisogne says. The Indian project, for example, has been ongoing for six years. He gestures to a 3.6-metre-wide liquid mirror that is mounted in the workshop. Unlike the mirror used in Chile in 2004, which was made of glass and was almost flat, this mirror, part of the newest generation of telescopes, looks like a giant bowl and will be filled with 400 to 600 kilograms of mercury. The advantage of a liquid mirror is that, compared to a glass mirror, it takes a couple of months instead of years to be manufactured.
Considerably smaller are the telescopes AMOS designs and manufactures for satellites and space shuttles. The telescopes made for ESA (the European Space Agency) and NASA (the US’s National Aeronautics and Space Administration) weigh less than two kilograms. Always the challenge is to make the instruments as light as possible because it costs about 15 euros per gram to send materials into space.
“Until now our clients have been non-commercial – institutes, universities and astronomy centres – but lately discussions have started with owners of telecom satellites who are interested in testing equipment in our vacuum chambers that imitate the outer space environment,” says Chisogne.
These vessels, which are made to simulate flying pressures and temperatures, can be as much as seven metres high and almost as wide. The thermal panels can accommodate temperatures ranging from –269 to +100 degrees Celsius. Fake stars can also be simulated. With a collimator (another AMOS product, similar to a reverse telescope) a light source is created that behaves like a star. By using a collimator, certain measures can be taken to adjust data picked up in real space that are used to, for example, estimate the mass of a star.
“During the past 10 years, some 400 new planets have been discovered within a few light years from us,” says Chisogne. “Half of them have been tracked down with products from AMOS. Altogether, mankind has knowledge of approximately 4 percent of the material in universe.”
Thus, there is still 96 percent to discover. “Unfortunately there is not a lot of margin in this for commerce, and therefore it does not attract many players,” says Chisogne. “I think the market will remain more or less like it is today
for many years.”
Minimal movement with SKFs actuators and bearings
AMOS telescopes move with a very high precision, and the balance between stiffness and low friction is extremely important since a minimal movement of the telescope results in a dramatic change in the angle out in space. In addition, the telescope movement must be impervious to changes of temperature (the telescopes are often situated on high mountains where temperature changes are extreme). SKF provides AMOS telescopes with actuators and bearings that perform to the utmost accuracy.