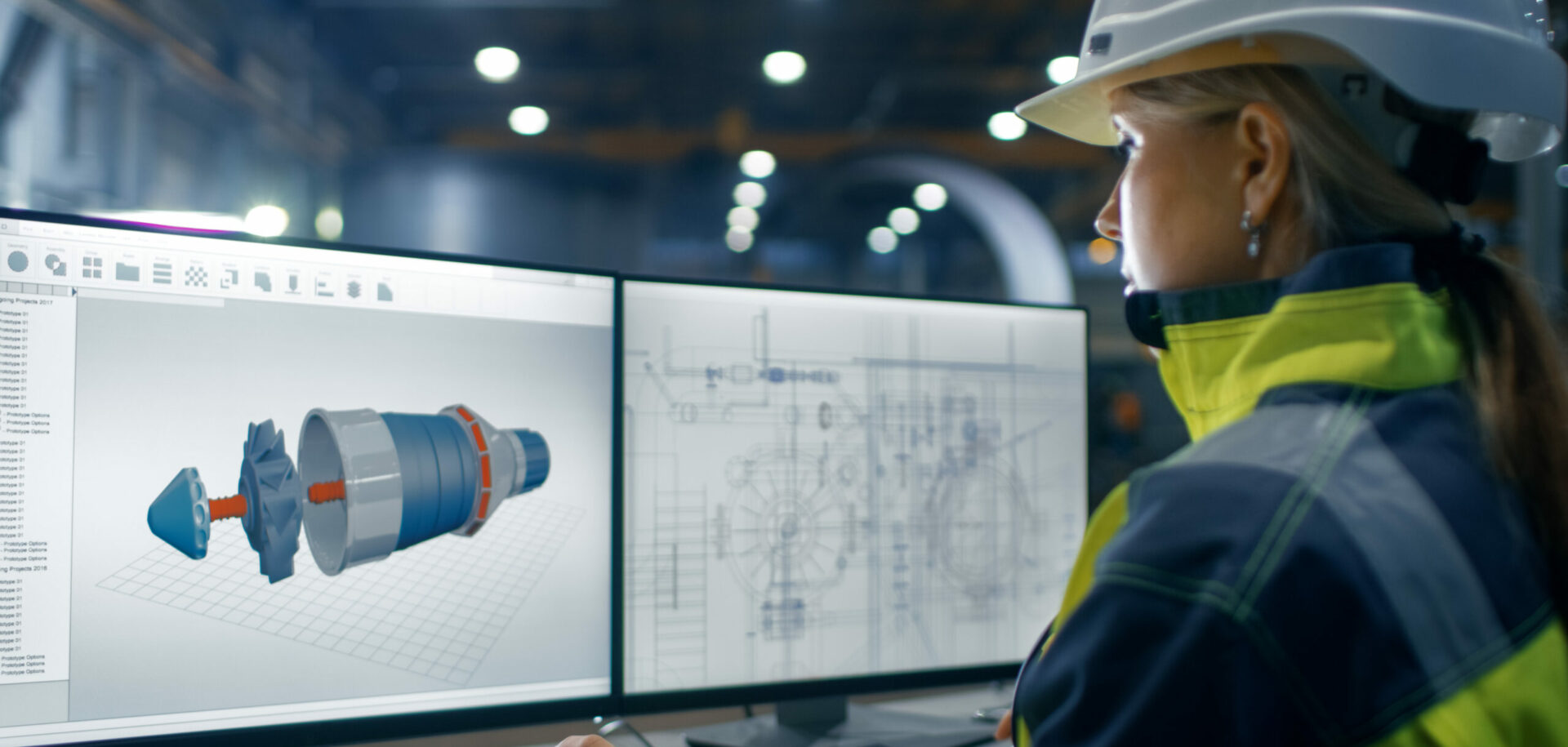
Preadjustable non-locating bearing unit
The SKF Panloc is a non-locating bearing unit that allows the internal clearance or preload to be adjusted to specific values.
In the area of high-precision non-locating bearings, there are numerous applications where the non-locating bearing of the shaft must have a specific internal clearance/preload in operation. In such applications, great value is placed on a precisely defined shaft position. In addition, there is an optimal operating condition for each bearing that represents a compromise between service life, rigidity and heat generation in the bearing.
Today, these application demands have more or less satisfactory bearing solutions. They include cylindrical roller bearings with a cylindrical or a tapered bore and needle roller bearing with a cylindrical bore.
In the case of a cylindrical roller bearing with a cylindrical bore, a design with a suitable interference fit, as well as an appropriate selection of the internal clearance before mounting, can greatly affect the operating clearance of the bearing.
However, a certain tolerance of the internal clearance remains that cannot be affected. In addition, a certain internal clearance is required before mounting, since mounting a cylindrical roller bearing with preload carries the risk of damaging the raceways before the bearing is used.
For a cylindrical roller bearing with a tapered bore, pushing on the inner ring and thus expanding the inner ring raceway can adjust the internal clearance/preload precisely.
This procedure is the standard solution in precision bearing technology (for example, machine tool spindles). However, it has disadvantages in that manufacturing tapered shafts is cost-intensive and the adjustment procedure is cumbersome.
For needle roller bearings with a cylindrical bore, a precise internal clearance/preload can be set very accurately by selecting the correctly dimensioned needle roller and cage assembly, i.e., a specific needle diameter.
This pairing procedure, however, is time-consuming and involves a certain risk. It is also cost-intensive, because of the stocks required.
These shortcomings have led SKF development engineers to create a new solution: the SKF Panloc non-locating bearing unit.
The SKF Panloc consists of:
- A bearing housing adapted to its service location, generally with a flange;
- A flangeless outer ring with a slightly tapered raceway that is mounted in the bearing housing;
- A single-row tapered roller set with cage;
- A flangeless inner ring with a cylindrical bore and raceway that can be mounted on the shaft separately from the roller set and housing; and
- A shoulder ring designed as an adjusting ring with an outside thread by which the set of taper rollers can be variably adjusted against the slightly tapered raceway in the outer ring up to the pre-adjusted clearance or preload, respectively.
Operating principle
The SKF Panloc is supplied as a complete non-locating bearing unit for which the required non-locating bearing movement takes place within the bearing without force. Each unit is preadjusted to fit the actual operating conditions.
When they leave the factory, the units are provided with a slightly larger internal clearance than intended. After installation, the shoulder ring of the roller set, which is designed as an adjustable ring, is turned to position it against the slightly tapered raceway in the outer ring.
A scale positioned on the flat side of the bearing housing and a mark on the shoulder ring make it possible to adjust the internal clearance/preload on site.
The scale is calibrated by SKF according to the respective interference fits of the bearing rings on the shaft and in the housing. Rotating the shoulder ring by one scale division changes the amount of internal clearance/preload by a specific measure – for example, by 5 µm.
The difference in temperature between the inner and outer rings during operation must also be taken into consideration when determining the internal clearance/preload.
SKF has developed a program for this purpose that can be used to calculate the internal clearance/preload, taking all parameters into consideration.
Advantages of the SKF Panloc bearing unit include:
- Simple and precise adjustment of the internal clearance/preload;
- Non-locating bearing movement within the bearing;
- A tight cylindrical fit for the inner ring;
- Bearing unit is complete, thus mounting is simple and saves time;
- High level of rigidity;
- Low operating temperature;
- Easy replacement; and
- Designed for grease and oil lubrication.
In addition, using the SKF Panloc results in reduced overall costs for the customer, primarily because:
- There is no pre-mounting/no pre-adjustment;
- Mounting time is shorter;
- The unit is complete so there are fewer parts; and
- Less time and money are spent on logistics.
Design and rolling conditions
The design of the SKF Panloc bearing unit was based on the high-precision double row cylindrical roller bearings of the NN and NNU design and the NAO and NKI series of needle roller bearings, due to the importance of a defined internal clearance/preload in these bearings.
The external dimensions of the bearing housing are manufactured according to customer specifications. A special flange design can also be made available. The internal geometry of the bearing is designed according to the operating load.
The product line is based on actual customer requirements. The focus, however, is on bore diameters with d=40/80/100/120 and 170 mm.
The rolling conditions of the SKF Panloc are similar to those for taper roller bearings. Because the inner ring raceway is straight (angle 0°) and the outer ring is slightly tapered (overall angle of the tapered roller), the resulting rolling conditions are somewhat less favourable than for a standard taper roller bearing in which both raceways are manufactured under a specific angle.
Since the angle of the outer ring raceway of the SKF Panloc is very small, however, there is no effect worth mentioning on the bearing. Thus, there is no reason to expect smearing and reduced service life because of this. Practical tests under actual operating conditions have confirmed this theoretical knowledge.
In addition, the taper of the roller set and the outer ring raceway result in an axial force in the bearing. However, this can be easily absorbed by the shoulder.
Rigidity
The SKF calculation program BEACON can be used to perform calculations regarding the rigidity and service life of various non-locating bearing types.
The two diagrams in this article serve to illustrate a qualitative comparison of different types of non-locating bearings. They do not represent any absolute comparison of values. In this example, a non-locating bearing based on a needle roller bearing was selected as test bearing 1, while a non-locating bearing based on a cylindrical roller bearing with the same bore diameter was selected as test bearing 2.
Diagram 1 illustrates the rigidity in relation to internal clearance/preload of these different non-locating bearings. It shows that with the same external load the rigidity of the SKF Panloc lies in between the two test bearings in the cases of internal clearance or low preload.
The advantage of the SKF Panloc is that its preload can be greater, since it is adjusted after mounting. Because of this, the SKF Panloc has greater rigidity than the two test bearings in the area of high preload, or the preload can be increased as an easy way to increase rigidity in SKF Panloc non-locating bearings, taking the required service life into consideration.
As described earlier in this article, conventional bearings are not ideally designed for high preload, for reasons related to mounting.
Diagram 2 illustrates service life in relation to preload and shows that the longest nominal service life can be achieved at a specific preload. With the SKF Panloc, this optimal point of operation can be precisely adjusted in relation to the rigidity. For both test bearings, the optimal operating point falls in a tolerance range that is difficult to affect.
Tests have confirmed the theoretical findings. A detailed description of the tests would exceed the limits of this article. Only a brief summary is presented here.
The following general results were noted:
- Low vibration level and very quiet running;
- Low operating temperature (oil temperature measurement);
- Low friction;
- Simple adjustment of the internal clearance/preload; and
- Easy change of the internal clearance/preload between individual test runs.
Many applications
One of the most important areas in which the SKF Panloc bearing units can be used is in printing machines. In these, a high level of rigidity and running accuracy are important, and compensation for length expansion must take place without force within the bearing unit.
These units have already demonstrated in practice that they are suitable for use in the non-locating bearing side of print cylinders in a sheet-offset machine.
The SKF Panloc can also be used for bearings on plate and rubber cylinders in offset print machines. In addition, further application areas include military technology, compressors, generators, calenders and stirring mechanisms.
The SKF Panloc is a technologically efficient and cost-effective system for all applications that require a defined bearing clearance/preload with simultaneous non-locating bearing functionality.