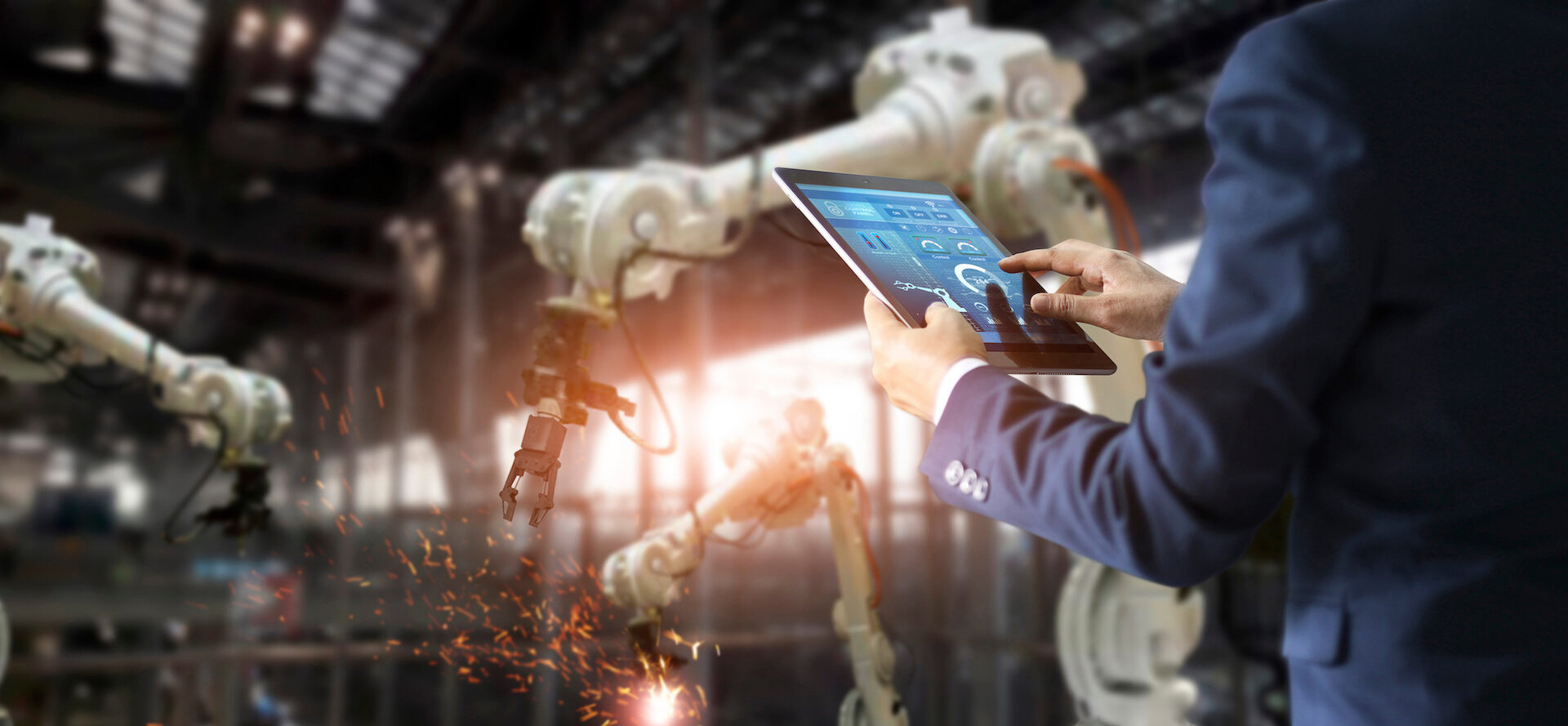
Proactive reliability transforms maintenance
There are profits to reap by moving from a replace-it-when-it-breaks approach to a proactive-reliability programme. But be prepared to change company culture.Asset-performance management is slated to be the new technology frontier as we head into the 21st century, much as advanced process control and optimisation revolutionised the process industries in the 1990s. For operation and maintenance executives, this development makes perfect sense. Advanced process control and optimisation can only work when plant equipment is available and operating at peak performance.
Manufacturing and heavy process industries are being driven to change their approach to operation and maintenance, due to such factors as reduced resources and staff, environmental concerns, stronger competition and overcapacity. Manufacturers need to manage plant assets efficiently and wisely – not just to achieve economical production but also to avoid fines and regulatory judgements. Manufacturing operation executives are continually asked to do more with less.
An elusive goal
Under these pressures, better management of assets is gaining greater credence among senior industry executives as a way to stay competitive and cut costs. Yet getting plant equipment to operate at peak levels remains an elusive goal for many. Christer Idhammar, founder, president and CEO of IDCON, Inc, in North Carolina, US, says he has seen an increasing number of companies create new corporate-level positions, such as “director of reliability and maintenance.” Some of these attempts at increasing reliability of operations and maintenance have been extremely successful, says Idhammar, who has been in the business since 1972; others have failed because they did not take a long-term approach.
A long-term approach, in Idhammar’s view, requires moving beyond simply replacing equipment when it breaks to preventive maintenance (replacing it before it breaks), then to predictive maintenance, which involves replacing equipment just in time, often through technologies such as condition monitoring, and ultimately to proactive reliability. Proactive reliability involves using the information gained, for example, from condition monitoring, to replace equipment just in time and find the root causes of a problem. It addresses repetitive failures and implements processes to prevent recurrence.
Such a strategy enables companies to take complete control over what is happening on the plant floor, and that is where the biggest savings can be made. It is estimated that unplanned equipment and manufacturing process down time eats up at least 5 percent of planned operating time. For typical heavy process industries, this loss in productive operating time can represent 1 to 3 percent of revenues annually. Adopting a more proactive approach to maintenance operations and technology can therefore result in substantial savings.
Changing corporate culture
Yet maintenance has long been looked at as a cost centre rather than a profit centre. This has led to reactive maintenance. The advent of preventive, predictive and now proactive maintenance, supported by the right processes and technology, is expected to change that perception in coming years. This new way of thinking can contribute significantly to productivity and therefore to overall profitability.
For Idhammar, it comes down to a few basics. “It is important to distinguish between generating results and cutting costs. That is why we call our concept ‘results-oriented maintenance.’ You can’t say, ‘Let’s see what increased reliability we get at a lower cost.’ Equipment doesn’t cost money when it operates properly. It costs money when it breaks down.”
More than anything, says Idhammar, moving from a replace-it-when-it-breaks approach to proactive reliability requires a transformation in company culture. It is important to have a corporate culture that is willing to embrace the need for change. Often, the required changes involve shifting responsibilities, so a company must be able to invest the time and energy to re-train staff members and keep them informed.
Giving the operator control
An important factor in reliability maintenance, says Heinz Bloch, an expert in the field of operation and maintenance, is operator-driven reliability or ODR. “ODR is a vastly overlooked approach,” says Bloch, who is the author of 13 books and the reliability editor for Hydrocarbon Processing magazine.
“Anyone who attempts asset management without including operator-driven reliability will be leaving some opportunities uncaptured.”
The ODR concept is simply a framework for organising the activities of plant operations personnel in concert with a company’s reliability maintenance practices, Bloch says.
Operators are the people who are closest to plant machinery on a daily basis, and typically they are the first to notice the smallest changes in machine operations. Involving them as key resources in a plant’s reliability effort is a logical and highly cost-effective means to improve machine and process operation.
As Bloch explains, there are always three job functions in any plant: operating the machinery, maintaining the machinery, and technical procurement of the machinery.
Work together
“Unless those three functions work together, the machines will not function reliably,” he says. “What some of the leading-edge companies are discovering is that giving equal responsibility to the people in those three functions results not only in better-performing machinery but in more motivated individuals. The trend is to clearly give the operator proper recognition, responsibilities and accountability.
An important part in moving towards proactive reliability is building a commitment to the inspection process through involvement and introduction to a culture of continuous improvement.
“It’s a matter of changing people to work in a more disciplined way and to work better with the resources they have,” says IDCON’s Idhammar.
In addition to revamping company culture in certain fundamental ways, a successful proactive maintenance programme needs a willingness to adopt new technologies and the ability to commit the financial, training and manpower resources necessary to make the best use of technology initiatives. Finally, technology is not an answer in itself; it requires updated maintenance processes. Incorporating new technology into the data collection, knowledge management and decision-making processes is critical to achieving its full potential.
Technology offers shortcuts
Idhammar agrees that the importance of technology in operations and maintenance should not be underestimated. Machines can be assessed using condition-monitoring technologies. Shutdowns are scheduled based upon machine problems identified, using sophisticated vibration and condition-monitoring equipment. Unplanned shutdowns are significantly reduced.
“Electronic handheld devices allow maintenance and operations people to accomplish a great many more tasks without additional time spent,” Idhammar says. “And we can expect that the younger generation in the operations and maintenance field won’t be asking for a paper system for maintenance checks; they’ll expect a computerised, high-tech solution.”
In the quest for proactive reliability in operations and maintenance, simplicity is the key, Idhammar says. The first step is a matter of actually carrying out preventive maintenance:
getting the right alignment, the right balance, the right operating practices and the right equipment, which should be based on long-term ownership, not the lowest purchase price. The second step is executing the remaining maintenance more effectively. This means finding problems early, through condition monitoring, planning and scheduling to effectively carry out an action, and when the action is performed, always finding out why it happened in the first place.
“There’s no magic formula,” he says. “Breakdown maintenance into a process of maintenance and activities of maintenance, and it will all be the same, no matter what three-letter acronym you give it. It’s a matter of getting the basics right. The best performers actually execute, and the others just talk about it.”
Amy Brown
a business and technology journalist
based in Stockholm