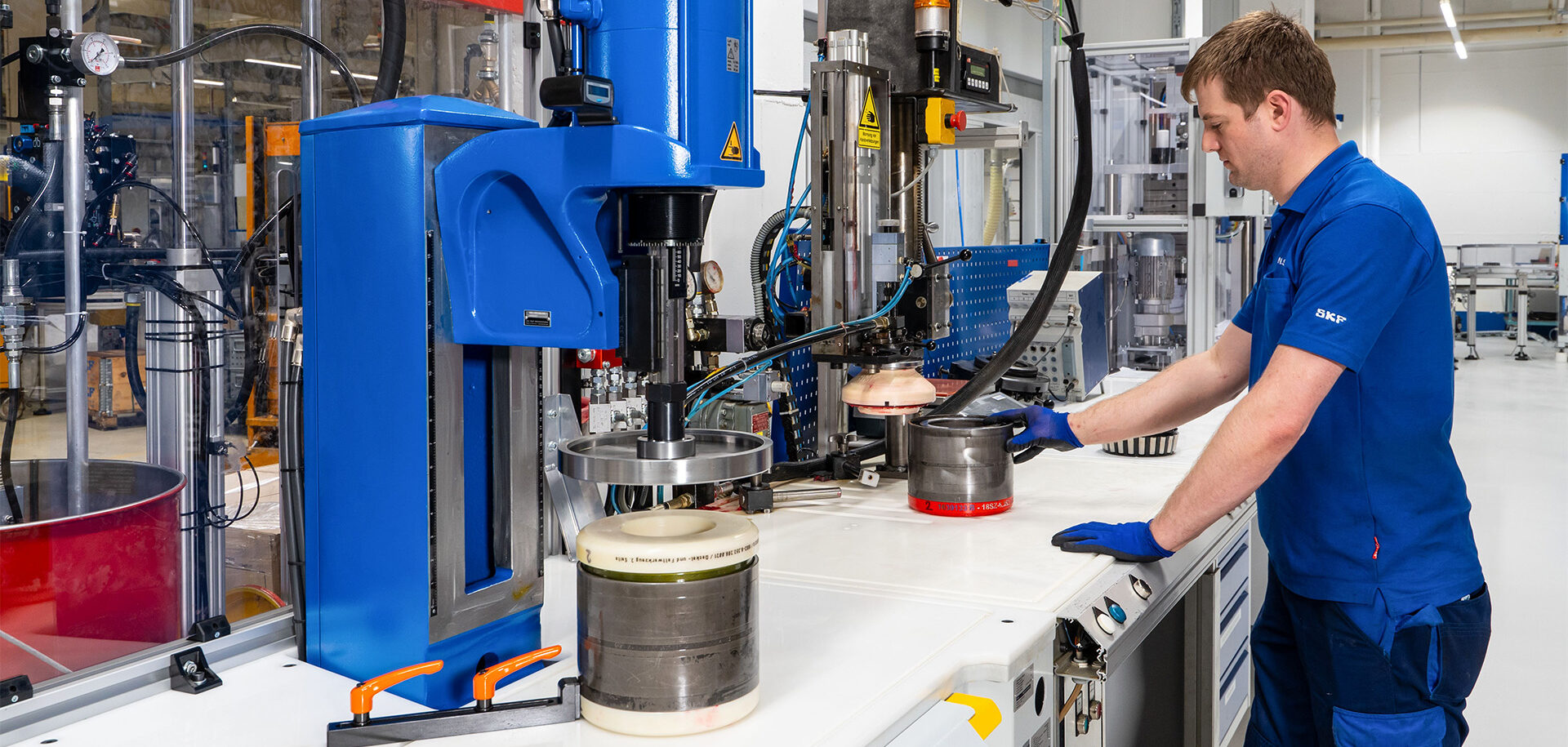
Bearing remanufacturing cuts costs and CO2
Bearing remanufacturing plays an essential role in the global railway industry. The benefits are many, including shorter stops, faster overhaul turnarounds, reduced maintenance costs and lower CO2 emissions.
Railway operators are increasingly seeking sustainable solutions for their equipment operations, maintenance and repair. Bearing remanufacturing can offer a more environmentally friendly approach while delivering significant benefits, such as reduced total cost of ownership through lower maintenance costs, as well as increased operational safety and reliability plus higher energy efficiency.
In the time-driven railway world, rapid response and overhaul times to keep rolling stock on the rails is important. Reducing scrap rates is also desirable to cut costs further.
Why remanufacturing?
The cost of remanufacturing is much less than the cost of a new bearing. In addition, it consumes less energy, requires fewer resources and produces less waste than producing a new bearing. Remanufacturing a bearing for train applications saves more than half the cost of a new bearing. In addition, it cuts CO2 by 85 percent.
Tailored solutions
“SKF has built up a global network of 20 railway service centres with around 220,000 wheelset bearings reconditioned each year,” says Alfredo Monetti, railway remanufacturing product line manager and business development manager. “To be as close as possible to customers, SKF has a widespread footprint with five centres in the Americas, seven in Europe, one in Africa and seven in Asia Pacific.” The volumes managed are very different, with small centres dealing with perhaps 1,000 bearings a year and large ones managing as many as 100,000. Whatever the demand, the work is carried out to the same consistently high standards.
Digitization of processes is important to support future improvements.
Alfredo Monetti, railway remanufacturing product line manager and business development manager, SKF
SKF offers replacement sealing systems with new parts and components upgrades to increase the overall bearing performance according to the latest design change implementation. “Furthermore, SKF can offer the 100/100 business models, where scrapped damaged bearings are replaced by new bearings in order to return to the customer the same quantity of units received by the railway service centre,” explains Monetti.
Crucially, SKF uses the same standards, quality assurance, knowledge and competences as for the manufacture of new bearings. These sites have built up significant competence in the analysis of bearing damage, which is coupled with carefully planned remanufacturing processes to suit each bearing application. By understanding the conditions in which the bearing is operating, the remanufacturing process can also include improvements or upgrades to lubrication, enhanced sealing solutions and improved coatings. The wheelset bearing back in service can also be coupled with the use of monitoring and sensing technology, which can further prolong its operational life.
Before any work starts, SKF gives the customer a clear idea of the work and cost involved in remanufacturing and the potential savings to be made compared with buying a new bearing.
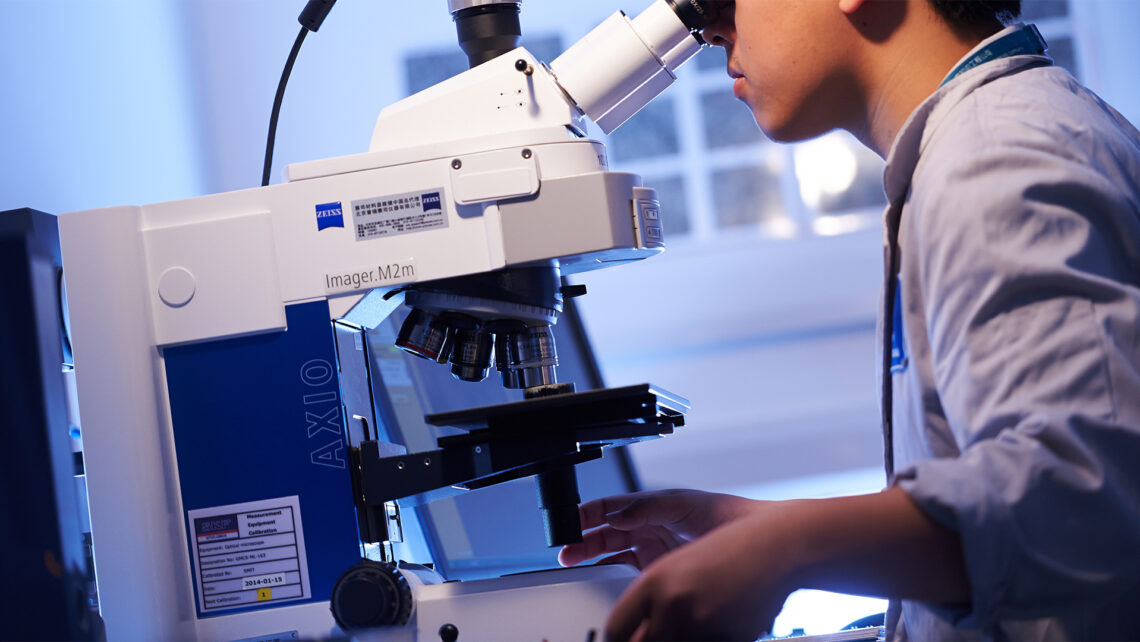
The steps to remanufacturing
Each SKF site is certified to offer a comprehensive process carried out by experienced personnel with the latest processing knowledge. SKF has an advanced management system to provide a unique identification during remanufacturing. This ensures that the bearing can be fully traced throughout its current and future life cycle. “Digitization of processes is important to support future improvements,” says Monetti.
Each bearing is disassembled, degreased and cleaned. The components are inspected and an analysis report is produced. Bearings suitable for remanufacturing can be repaired using polishing, grinding and component replacement. Any bearing that during the following service interval in the field will not exceed its calculated service life is suitable for remanufacturing, which means that the cost savings that can be gained through remanufacturing are substantial.
Continuous improvement
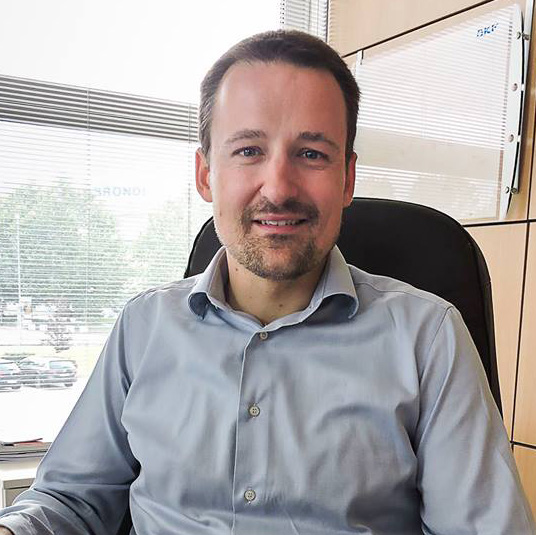
By providing professional and detailed feedback about bearings that have been returned from the field, areas of improvement can be identified for the application and the bearing design. Railway customers are increasingly turning to Rotating Equipment Performance contracts where SKF can support continuous improvement programmes for design through SKF railway engineering data and application performance information.
SKF continuously develops its own processes with new technology, for example by looking at how to carry out raceway repairs economically to reduce scrap rates.
“SKF is also looking at automation of the visual inspection process using artificial intelligence [AI],” says Monetti. “AI would standardize the visual inspection process across the different railway service centres, avoiding any possible human subjectiveness.” He adds that increasing automation is also a feature of SKF’s operations.
As well as providing its own dedicated services, SKF is working in partnership with other organizations and customers to provide training, support and services. By the end of 2022, the first SKF automated remanufacturing line will be operational at a customer’s facility in Brazil.
For SKF, the demand for railway remanufacturing services is growing rapidly, and it is expected that the business will grow by 50 percent by 2023.
Knowledge of bearing manufacturing and the particular applications in which a bearing operates has been crucial to the development of suitable remanufacturing processes that support customers’ need to reduce total cost of ownership through reduced bearing purchase cost, optimizing spare parts inventory and minimizing waste. It is also making an important contribution in reducing overall environmental impact, giving new life to used parts. “In essence, wheelset bearing remanufacturing is a circular economic pillar that ensures lower total cost of ownership of fleets around the world,” Monetti says.
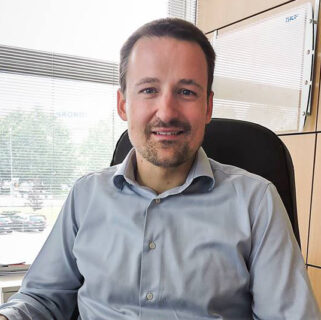
Continuous improvement
By providing professional and detailed feedback about bearings that have been returned from the field, areas of improvement can be identified for the application and the bearing design. Railway customers are increasingly turning to Rotating Equipment Performance contracts where SKF can support continuous improvement programmes for design through SKF railway engineering data and application performance information.
SKF continuously develops its own processes with new technology, for example by looking at how to carry out raceway repairs economically to reduce scrap rates.
“SKF is also looking at automation of the visual inspection process using artificial intelligence [AI],” says Monetti. “AI would standardize the visual inspection process across the different railway service centres, avoiding any possible human subjectiveness.” He adds that increasing automation is also a feature of SKF’s operations.
As well as providing its own dedicated services, SKF is working in partnership with other organizations and customers to provide training, support and services. By the end of 2022, the first SKF automated remanufacturing line will be operational at a customer’s facility in Brazil.
For SKF, the demand for railway remanufacturing services is growing rapidly, and it is expected that the business will grow by 50 percent by 2023.
Knowledge of bearing manufacturing and the particular applications in which a bearing operates has been crucial to the development of suitable remanufacturing processes that support customers’ need to reduce total cost of ownership through reduced bearing purchase cost, optimizing spare parts inventory and minimizing waste. It is also making an important contribution in reducing overall environmental impact, giving new life to used parts. “In essence, wheelset bearing remanufacturing is a circular economic pillar that ensures lower total cost of ownership of fleets around the world,” Monetti says.
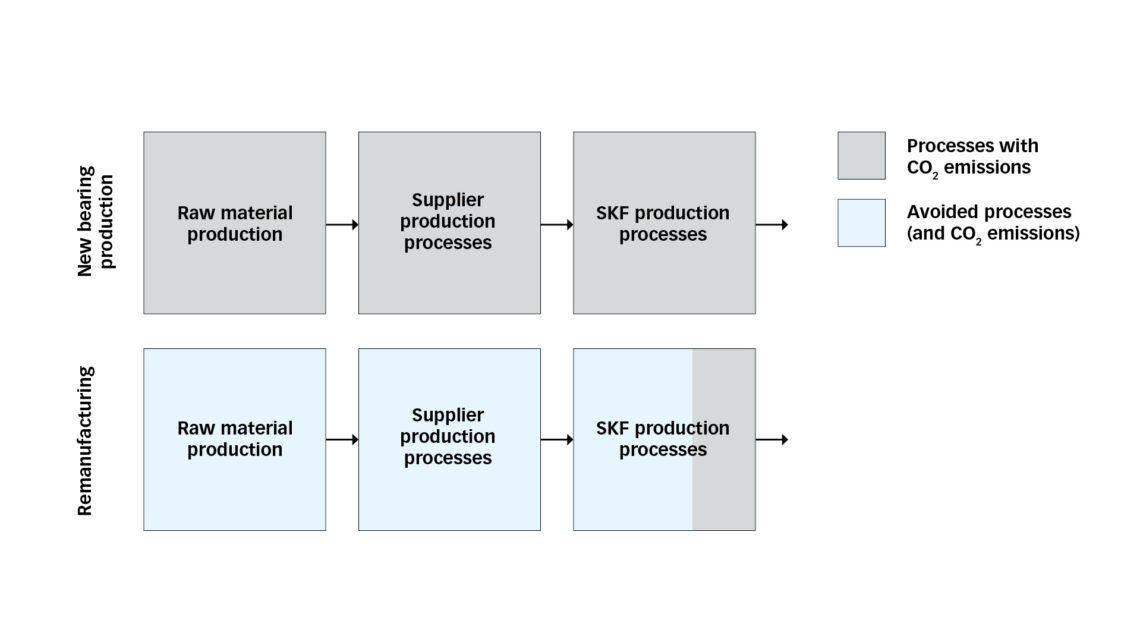
Calculating the cost of sustainability
“In 2018, the SKF Group total energy use was 1,814,000 MWh,” says Alfredo Monetti, railway remanufacturing product line manager and business development manager, referencing SKF’s Annual Report 2018. “Of this, approximately 1,350,000 MWh is estimated to be related to new bearing manufacturing. The total weight of all new bearings produced was 457,000 tonnes. The energy use per kilo bearing can be calculated as 2.9 kWh/kg bearing by dividing 1,350,000 MWh by 457,000 tonnes.”
Energy is also used in upstream processes (e.g., suppliers to SKF). “Assuming 60 percent of the total energy is used in upstream processes and 40 percent by SKF, the energy use per kilo bearing increases to 7.25 kWh/kg bearing,” Monetti explains. “If we assume that 85 percent less energy is used by SKF during remanufacturing than manufacturing of a new bearing, the energy per kilo remanufactured bearing is about 1.1 kWh/kg bearing.”
This means that 6.1 kWh/kg is avoided. By assuming that the average CO2 emissions from this energy is the same as the SKF average, we can calculate the avoided emissions (SKF average emission factor based on annual report is 0.273). 6.1 kWh/kg bearing x 0.273 kg CO2/kWh = 1.7 kg CO2/kg bearing. If we consider an average mass of approximately 20 kilograms per bearing, the result is a CO2 saving of approximately 34 kilograms for each bearing.
“Currently we are refurbishing approximately 220,000 bearings per year,” Monetti says. “Therefore, the global annual saving of CO2 currently provided by SKF railway remanufacturing is 7,480 tonnes per year, and this value is going to increase following the volume growth.” (The above is a conservative figure as it only considers emissions related to energy use and excludes all transports.)