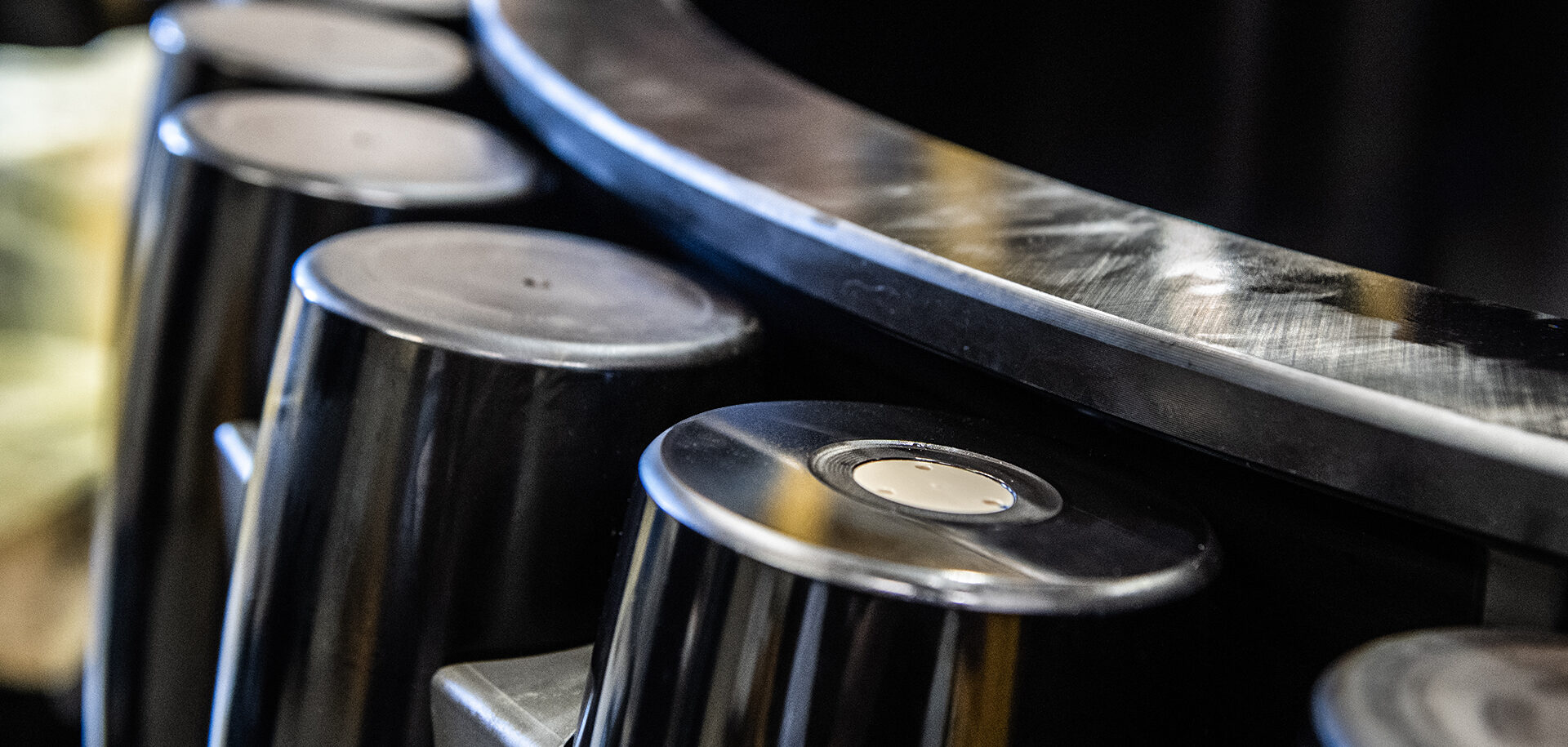
Raising the bar for collecting bearing data
SKF’s Sensor roller system uses sensors embedded inside rollers to gather operational load and other data in order to instantly determine the state and performance of a piece of machinery. Measuring all relevant parameters helps to understand the application in greater detail. By developing a fully commercial version of its sensor roller, SKF offers more detailed information from large bearings such as those used in wind turbines. This makes it easier to control operations, improving both reliability and efficiency.
Increasingly this is being accomplished by smart components that gather, analyse and transmit the data. For bearings, critical data such as load, roller rotation speed and temperature can be used to develop real-time bearing-life models, which helps to improve the performance and lengthen the life of key assets.
Bearing rollers embedded with sensors
One system that can collect load, roller rotation speed and temperature from inside the bearing is SKF’s Sensor roller system, which is typically used in large bearings. It uses bearing rollers embedded with sensors to gather data, which can then be transmitted wirelessly to operations and maintenance staff, allowing them to determine instantly the state and performance of a piece of machinery.
SKF’s Sensor roller system is currently an advanced prototype that is being used in customer pilots for design and validation as well as troubleshooting. The aim is to commercialize the sensor roller product to last as long as the bearing itself, with two accompanying offers for the wind industry: design and validation for OEMs, and process control and troubleshooting for the aftermarket.
The SKF Sensor roller system has been tested rigorously over the past few years in a variety of bearing types and sizes, from specialized test rigs at SKF’s Sven Wingquist Test Centre to customer projects.
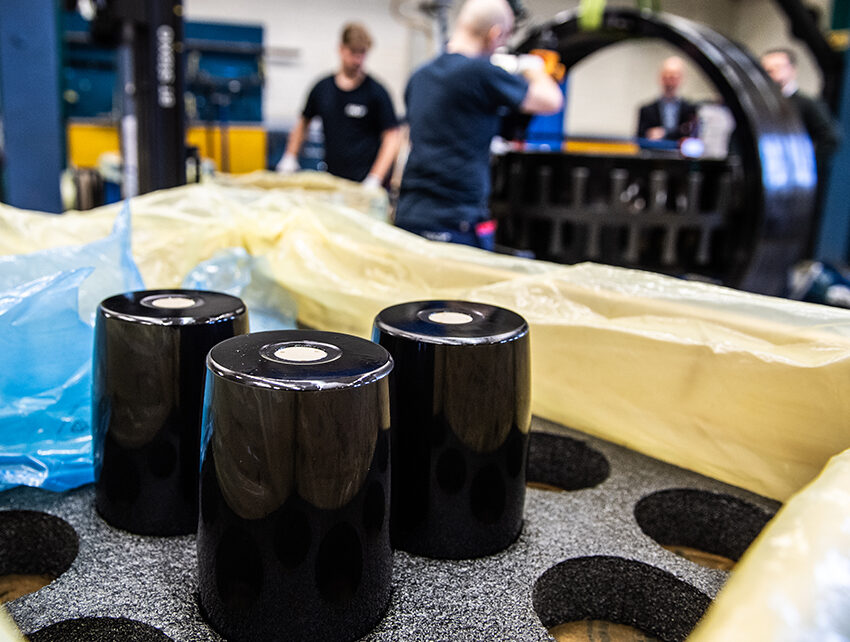
Piloted for wind turbine main shaft
In one example SKF and a customer have extensively piloted the SKF Sensor roller system for a wind turbine main shaft bearing validation campaign in northern Germany. The system has captured the behaviour of the main shaft bearing and how the surrounding structure affects it, which can help the customer validate its design load assumptions and understand better how, for example, seasonal variations in weather affect the bearing’s performance.
However, the sensor roller of the future will do more than simply gather data. It should be able to determine the remaining lifespan of a bearing by feeding precise data into a bearing-life model. This will help operators to schedule maintenance or order a replacement bearing, thus avoiding unplanned shutdowns.
In addition, that future sensor roller system will help OEMs validate wind turbine drivetrain designs even better than the system does today, and at the same time it will help operators control the process of production and service life much better, by providing a digital twin to estimate bearing service life and assess loaded conditions versus design in order to find out answers to questions such as whether more energy can be harvested during high winds.
With electronic components continuing to shrink in size, these rollers will one day become available for smaller bearings and for every bearing position along the wind turbine drivetrain. For now, though, the immediate aim is to commercialize the SKF Sensor roller system for large bearings.
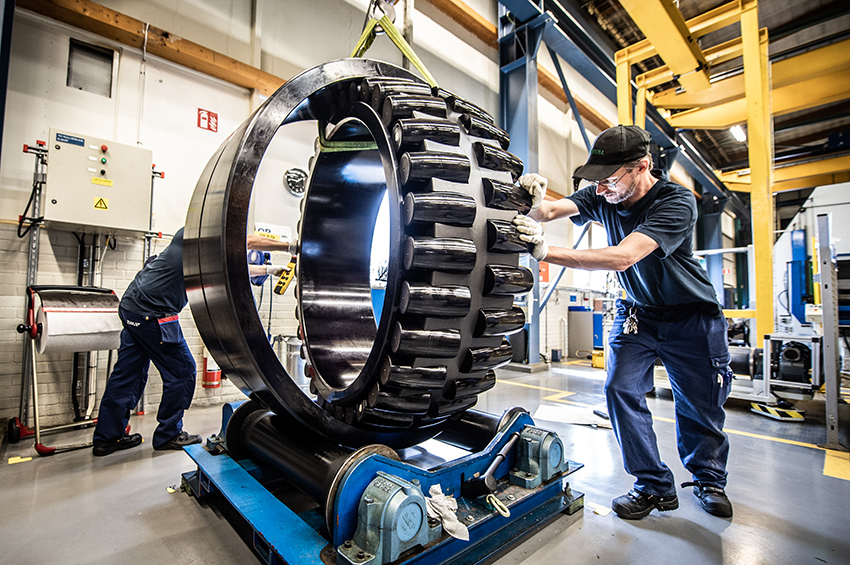
How the SKF Sensor roller system works
An SKF Sensor roller comprises a hollow roller and an inlet containing measurement sensors and associated electronics to transmit the data. The sensors measure three types of data: load, temperature and roller rotational speed. All three are critical in determining bearing life, contact pressure, thermal effect, misalignments and much more, each of which has a direct effect on asset life. While temperature and rotational speed both influence bearing life, the effect of load is far more significant.
The sensor roller inlet has three accelerometers that measure acceleration in three directions, plus a tri-channel gyroscope that measures rotational speed on three axes. Together, these show the complete motion of the roller. Accurate measurement of rotational speed can reveal if the roller is moving or sliding, both of which can cause overheating and deterioration.
Measuring temperature is relatively simple, but it is critical for lubrication management. If bearings run too hot, the lubricant thins out, which reduces the levels of protection, potentially causing metal-to-metal contact between raceways and rollers.
The roller itself is long enough to accommodate three separate load measurement points. This allows it to detect a variety of different effects. For instance, a mismatch between loads along the roller can highlight a misalignment of the raceway. This can result in serious problems if not corrected. A polar plot of the load can show whether the bearing is loaded correctly and can even pinpoint imperfections in the design of the bearing and/or the surrounding structure.
The way that load is transferred in large bearings depends a lot on the system in which they are installed. Large bearings for wind turbines can be as broad as four metres in diameter; their size means that the rings are relatively thinner than those in small bearings. This in turn means that the ring stiffness is lower, so understanding the load conditions helps to understand how the structure is influencing the bearing performance.
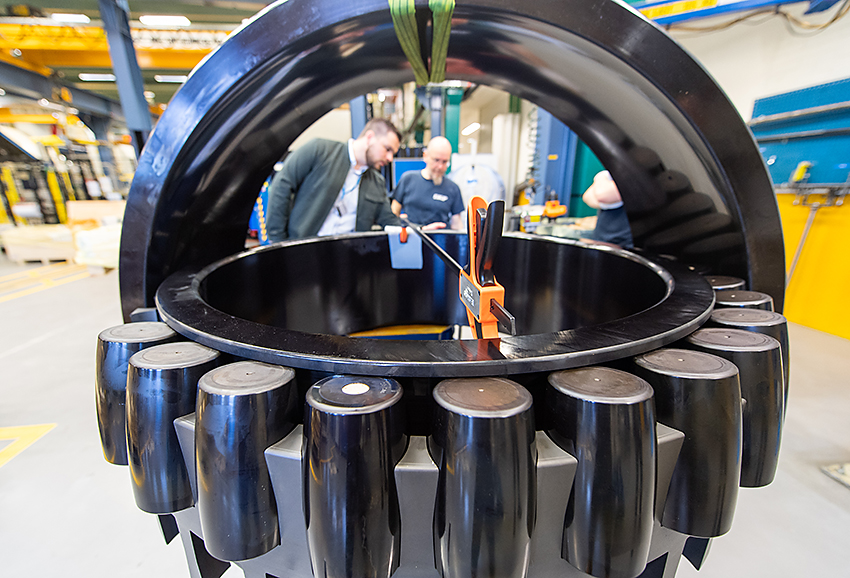