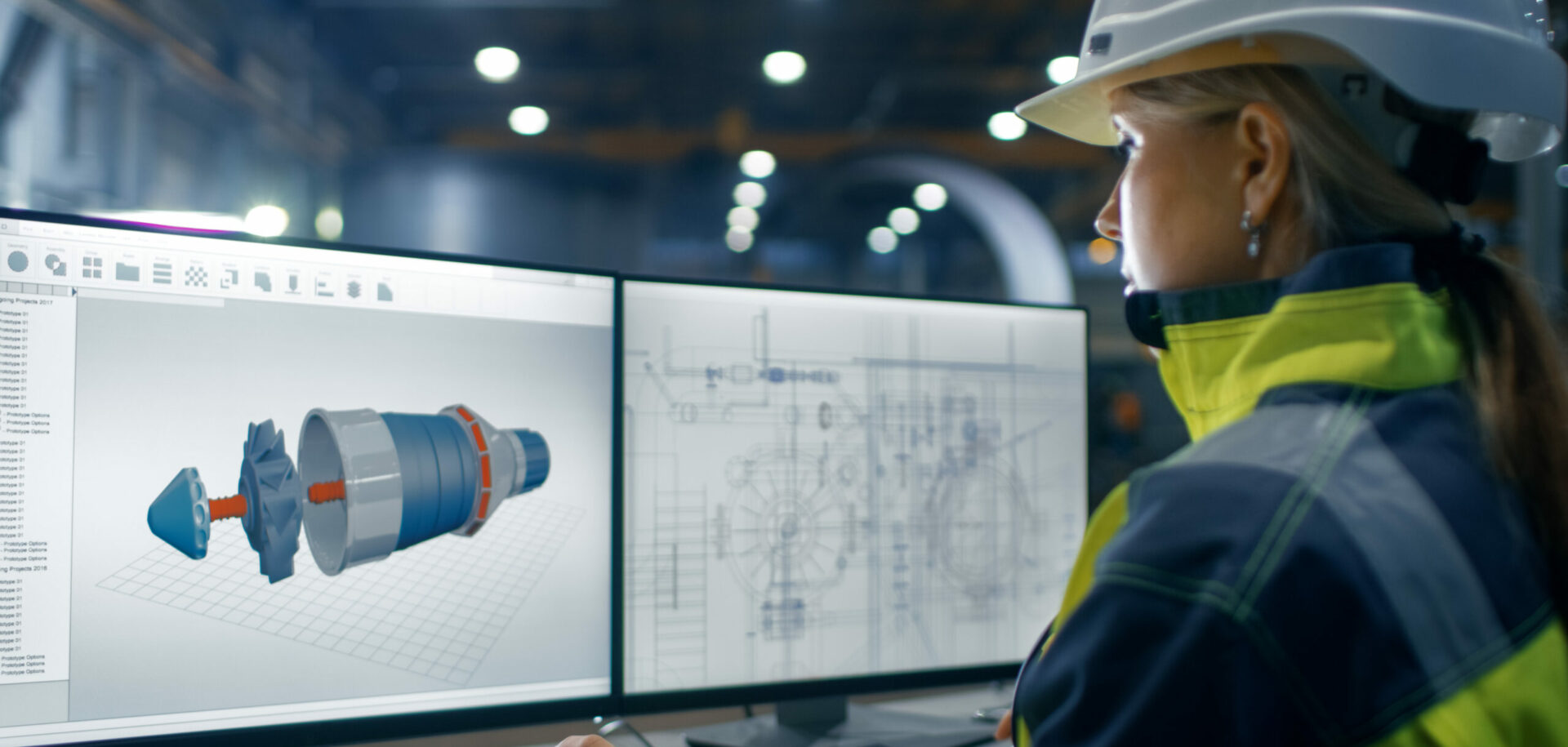
Running accuracy simulations for complete arrangements
The major bearing parameters that can be considered are:
Accurate three-dimensional simulation can now be provided for a range of bearing applications, ensuring that a rolling bearing has reliable performance in actual operation.Supplying customers with bearings that have optimal tolerances for specific needs requires not only an understanding of how a bearing works on its own, but also how the bearing behaves in a specific application. This demands consideration of all the interactions between the machine components. For complex arrangements, computer simulation can speed up considerably the derivation of appropriate tolerances.
Originally, the SKF simulation tool ORPHEUS was developed for analysing and minimising machine vibrations, (see related technology article in Evolution 1/2000). In ORPHEUS, shafts and bearings can be simulated under rotating conditions, making it an excellent tool to study the running accuracy (runout) of bearing-spindle arrangements – including elastic deformations of shafts, housings and bearing rings, as well as dynamic effects at high rotational speeds.
The major bearing parameters that can be considered are:
- internal geometry.
- loading conditions, clearance, preload.
- raceway waviness and runout.
- waviness and diameter spread of rolling elements.
- distance of rolling elements.
- flexibility of bearing rings.
Some non-bearing parameters that can be simulated are:
- bearing mounting errors (misalignment etc.).
- inaccuracies of housing bore and shaft seating (e.g. ovality).
- flexibility of shafts and housing.
- interaction between bearings and other components.
The application can be demonstrated by looking at a specific case study – a revolving tailstock centre. Fig. 1 shows a tailstock centre manufactured by Röhm, an SKF customer, for interchangeable inserts on lathes. The centres are used for turning workpieces over their entire length without reclamping. The manufacturer demands high bearing accuracy to keep the radial runout of the rotating centre tip below 5 microns. With the help of a computer simulation, the role of the bearings delivered by SKF should be clarified.
Benefit of modelling
The computer model of the rotating spindle is shown in Fig. 2. It consists of a flexible shaft supported by a double row angular contact ball bearing, a thrust ball bearing and a needle roller bearing. A calculated vibration mode shape is shown in Fig. 3. The bearing-shaft arrangement is rather complex and statically indeterminate. Therefore, a reliable judgement of the effect of bearing quality or mounting errors is only possible with the help of simulations (or excessive measurements).
In the theoretical study, whirling orbits of the rotating shaft tip (as shown in Fig. 4) were calculated for the following parameters: shaft and/or bearing ring ovality, raceway runout, waviness of raceways and balls, ball diameter spread, co-axiality of raceways, flange normality, misalignment of rings etc. Due to the advanced solver used in the simulation tool, the CPU time needed for computing a shaft orbit is less than one minute. Typical results of the parameter study are shown in Figs. 5a and 5b, where the shaft runout is given in terms of the radial runout of the inner ring raceway of the double row angular contact ball bearing and the misalignment of the thrust ball bearing, respectively. An important result of the study was that shaft runout is strongly determined by the interaction between the angular contact and thrust ball bearings, because the perpendicularity of the inner ring face of the double row angular contact ball bearing strongly affects the loading of the adjacent thrust ball bearing.
Based on the simulation results, optimised specifications for manufacturing accuracy of the bearing components were established and implemented in the quality specifications of SKF and the production unit in Austria. This allows SKF to produce these bearings in an appropriate production environment, at lower cost and with fewer quality checks needed on the line.
Flexible bearing rings
A unique feature of the simulation tool is the possibility of modelling bearing rings as flexible bodies. In Fig. 6, a calculated vibration shape of a rotating ball bearing with flexible outer ring is shown. In the computer simulation, the rolling elements are rolling across the complex surface of a deformed and wavy raceway. This feature was extensively used to derive optimised manufacturing tolerances for all bearing components and to design new quality test procedures for production.
Another calculation case where the bearings were modelled with flexible bearing rings is shown in Fig. 7. A shaft is supported by two spherical roller bearings in plummer blocks. The excitation of shaft vibrations as a function of bearing quality, design and loading conditions was studied. The simulations were performed in order to verify the proposed new waviness specifications for these bearings.
Paul Dietl and Ferdinand Schweitzer, SKF Österreich AG
and Henk Mol, SKF Engineering & Research Centre BV, the Netherlands