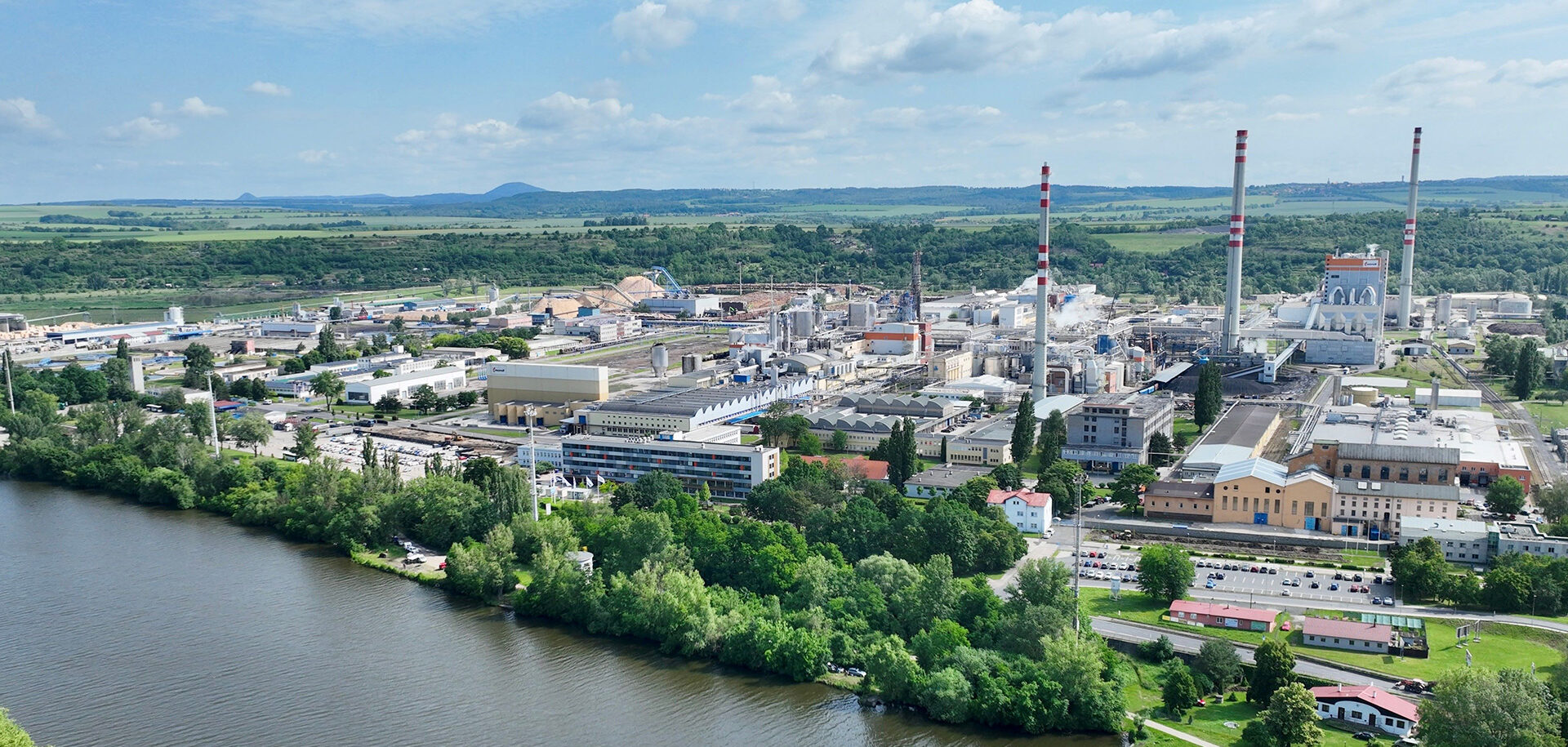
Savings in the bag
Remanufactured SKF bearings are cutting costs and carbon emissions at the Mondi Štĕtí paper mill.
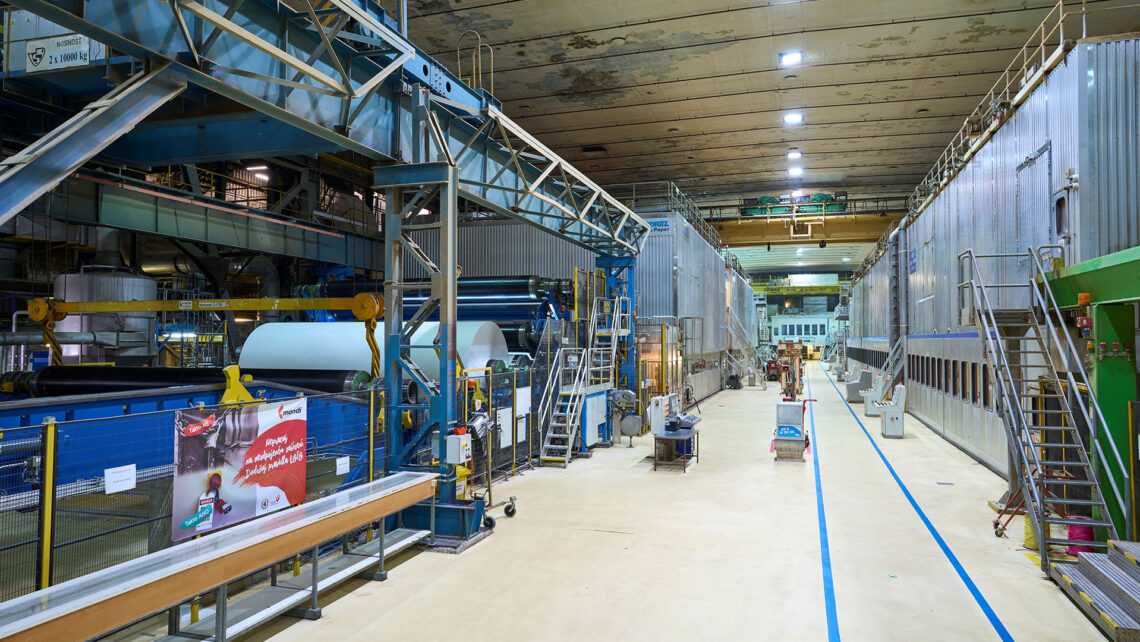
Productivity equals sustainability
For Mondi’s front-line operations team at Štĕtí, improving the environmental performance of the mill’s operations goes hand-in-hand with efforts to improve the performance of its equipment. Paper mills are large consumers of wood, energy and water, and production and maintenance personnel are always looking for ways to use these more efficiently.
Paper mills are also big users of bearings. Zdenĕk Podhorský, head of mechanical maintenance at the Mondi Štĕtí mill, estimates that the mill’s equipment relies on about 12,000 bearings to move, process and handle material through the various stages of pulp and paper production.
Remanufacturing is more cost-effective than buying a new bearing, and SKF also calculates the carbon emission savings from remanufacturing, which our procurement and sustainability teams highly value.
Zdenĕk Podhorský, head of mechanical maintenance at the Mondi Štĕtí mill
Keeping these bearings in good condition is a top priority for the Štĕtí maintenance team. Smooth-running bearings are essential for product quality and process energy efficiency, and bearing failures can mean costly and disruptive unscheduled production stops.
Deciding when to replace bearings, however, involves complex trade-offs. Avoiding failure is always top priority, but the largest bearings used in paper machines are high-cost, precision parts. In addition, the steel used to make them is a contributor to the mill’s indirect carbon emissions.
Depending on the machine and bearing application, Štĕtí uses a variety of methods to make bearing replacement decisions. It operates a sophisticated online condition monitoring system, developed over many years in partnership with SKF. With almost 3,000 measuring points across the site, the condition monitoring technology helps staff identify potential problems earlier and plan appropriate interventions at the time that best suits the plant’s production and maintenance schedule.
Less critical bearings are replaced according to a carefully planned schedule. The Mondi Štĕtí maintenance team includes one person dedicated full-time to managing the bearing inventory and the monitoring and maintenance schedules.
Some of the trickiest bearing replacement decisions come from unrelated maintenance activities. The big paper rolls inside the paper machines run at high speeds in challenging conditions, and that environment takes its toll.
“We may have to take a roll out because of surface damage or another reason,” explains Podhorský. “When we do that, we have to decide whether to reuse the bearings or replace them.”
A detailed inspection of each bearing is a standard part of the roll replacement routine, but maintenance teams can be reluctant to remount an old bearing on a new or rebuilt roll. “The bearing may have no visible signs of damage, but no one wants to be responsible for a machine stoppage caused by a part they replaced a few weeks or months earlier,” says Podhorský.
Circular economy
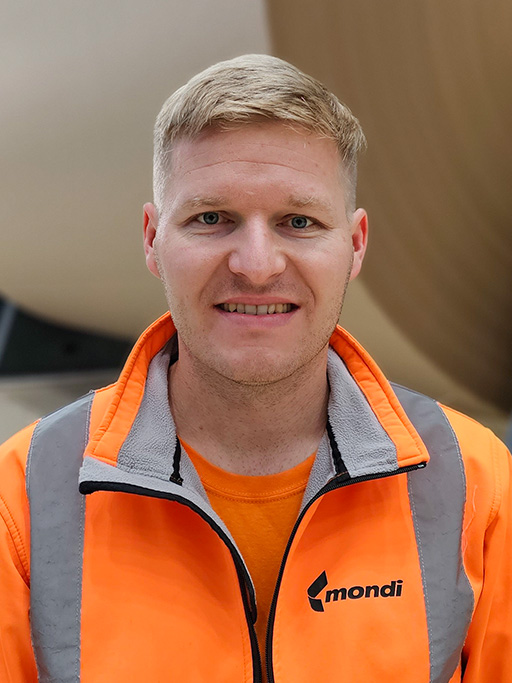
head of mechanical maintenance at the Mondi Štĕtí mill.
The drive to solve the competing demands of cost, reliability and carbon emissions led Podhorský to take a different approach to inventory management. Over the past three years, he has worked with SKF to integrate remanufacturing into the life cycle of high-value critical bearings at the site.
Today, when suitable bearings are removed from a machine, they are not retired but sent for remanufacturing. Bearings without major damage are shipped to an SKF service centre. There, the used bearings are cleaned, inspected, disassembled and fully remanufactured. The process includes surface finishing and replacement of components with severe damage. The finished bearing is warranted by SKF to have the same performance and longevity as a brand-new product.
“We receive a detailed report from SKF describing the condition of the bearing and the work required to remanufacture it,” explains Podhorský. “Remanufacturing is more cost-effective than buying a new bearing, and SKF also calculates the carbon emission savings from remanufacturing, which our procurement and sustainability teams highly value.”
These savings, in both cost and carbon, can be significant. Remanufacturing typically produces about 90 percent less greenhouse gas than manufacturing an equivalent new product, according to an SKF analysis1 . Since 2020, in Europe alone, Mondi has had 47 bearings remanufactured; in 2024 the Štĕtí site had eight bearings remanufactured.
For the very large, specialized bearings used in papermaking equipment, remanufacturing can also streamline supply chains. “The lead time from order to delivery for some bearings can be several months,” says Podhorský. “Remanufacturing lead times are faster than that, which could allow us to keep fewer bearings in our on-site maintenance inventory.”
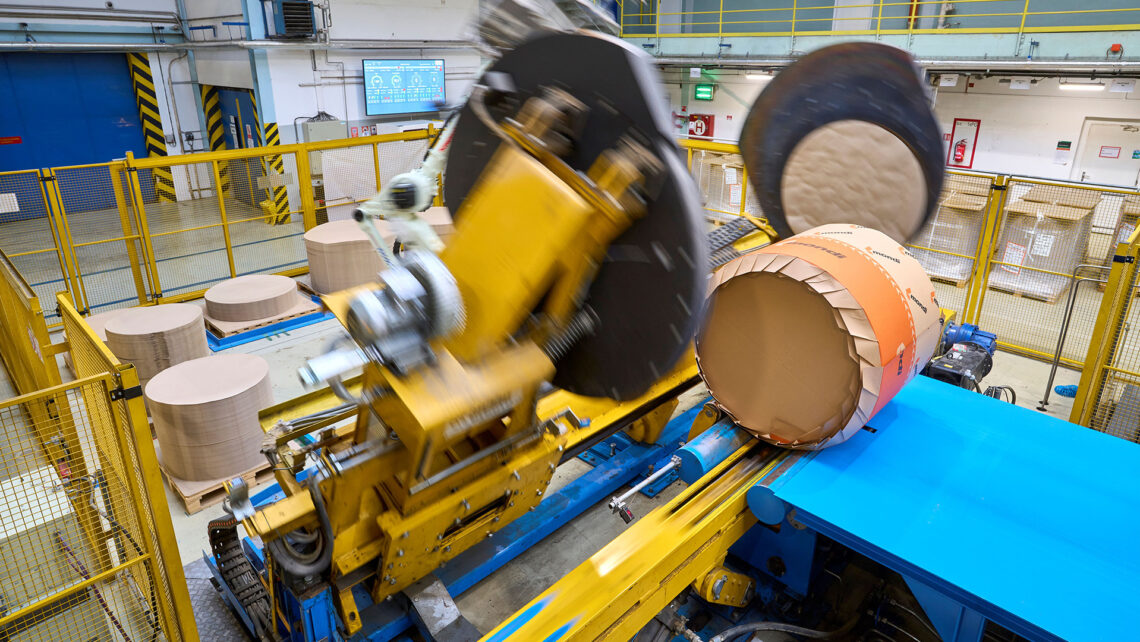
Old bearings, new processes
Introducing remanufacturing into Mondi Štĕtí’s high-pressure production maintenance environment has presented challenges, Podhorský says. “Of course, we had to convince our production colleagues that remanufactured bearings offer the same performance as new ones,” he says.
The site also had to implement a new maintenance and inventory control process to manage the flow of bearings from the shop floor through remanufacturing and back into inventory. This process had to accommodate the work of specialized outside contractors who perform off-site repairs on rolls and other machine parts.
As remanufacturing becomes more widespread, the Mondi Štĕtí team is considering changing the way it manages its spare parts inventory. “Eventually, I think we will need systems that can track individual bearings through their entire life cycle, which may include multiple rounds of remanufacturing,” says Podhorský.
For now, the team has plenty of room to expand its current remanufacturing approach. “We estimate that about 10 percent of the bearings we use in the field are candidates for remanufacturing,” Podhorský says. “Right now, we only have a fraction of that number in the remanufacturing programme.”
Fact box
Mondi Štětí’s operation covers the entire paper production process, from raw wood to finished product. The mill has two pulp lines and five paper machines. A sixth is scheduled to start production in 2025.
Mondi Štĕtí produces a wide range of paper products for packaging solutions, including high-quality paper bags used for building materials, food products and, increasingly, for e-commerce consumer packaging.
In Mondi Štĕtí, waste heat from the mill provides energy to local homes and businesses through a district heating system. The plant’s wastewater treatment plant also does double duty, treating municipal wastewater as well as on-site wastewater.