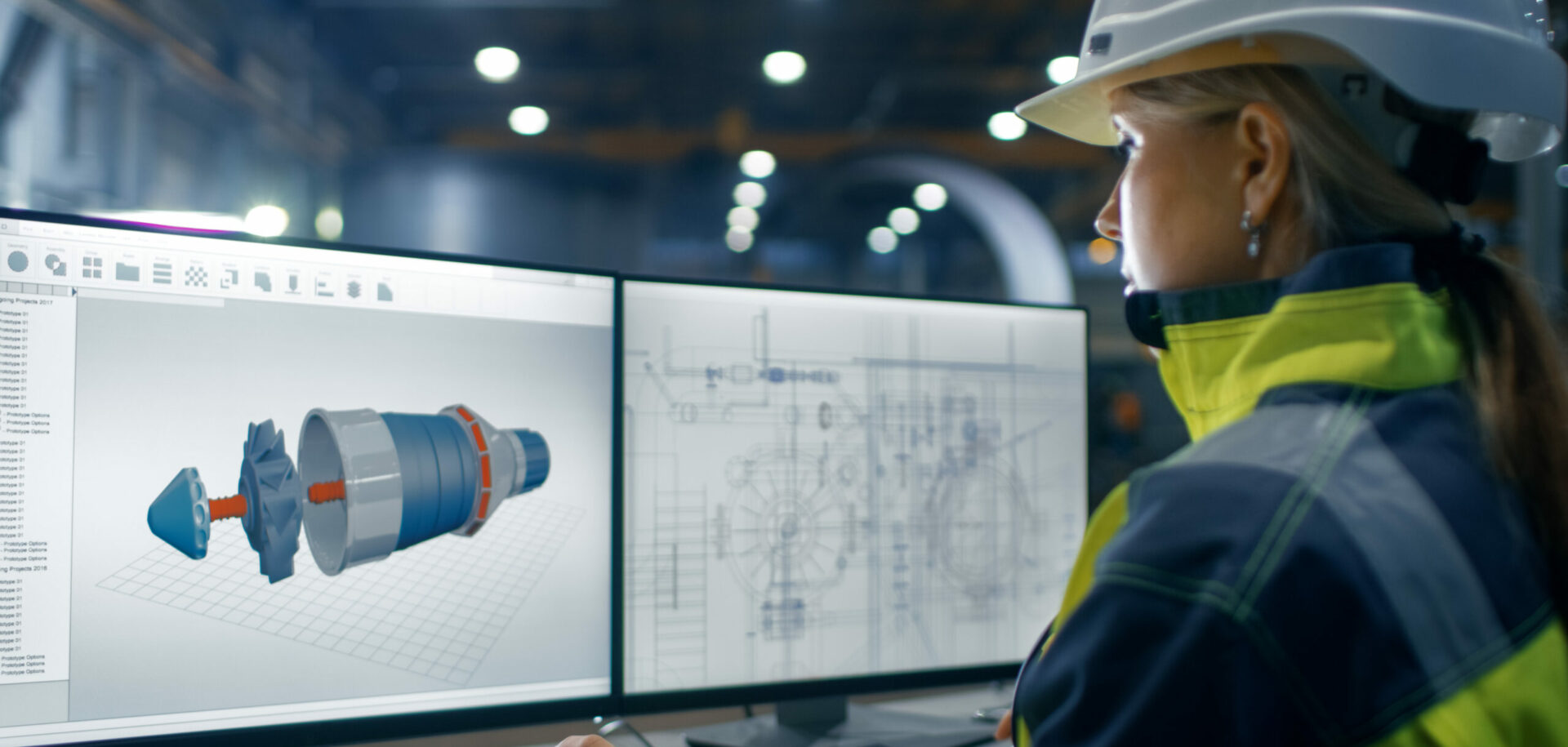
Sealed and delivering
SKF is extending its range of sealed spherical roller bearings, thus broadening the use and benefits of this high-performance design beyond current niche applications in harsh or challenging environments.
Facts
The launch of a full range of sealed spherical roller bearings from SKF marks a new era for this robust bearing. Wherever reliability, long operational life, reduced need for maintenance and lower operating costs together with environmental savings are needed, these bearings have a role to play. This is a reliable bearing solution that offers significantly reduced need for mainten-ance, coupled with prolonged service life and fewer unplanned breakdowns and production stops.
SKF has developed a comprehensive range of sealed spherical roller bearings with some 100 basic variants (se bild . 7), covering bearing sizes up to a 320 mm bore diameter, to benefit both OEMs and end users. Sealed spherical roller bearings provide:
-
improved uptime and higher efficiency
-
maintenance freedom – generally no need for relubrication
-
grease saving and thus environmentally friendly.
Sealed spherical roller bearings are intended for applications where uptime is critical and where the need for bearing maintenance needs to be cut significantly. Squeezing the last bit of productivity and performance out of equipment to save money is a major preoccupation for most industries these days. In some applications, it is absolutely vital that the machine equipment does not break down during operation. A harbour conveyor breaking down when unloading or loading a ship has a breakdown cost of 80,000 euros compared with only 800 euros if repaired when the conveyor is idle. For continuous casting plants, unplanned stops can cost 30,000 euros an hour.
Sealed spherical roller bearings are also seen as overcoming contamination problems caused by grease leakage where envir-onmental concern is a key issue. Grease use and disposal is increasingly important, and sealed spherical roller bearings can make a difference. For applications with large grease use, consumption can be reduced by 90 % or more over the bearing life. For one SKF customer, the grease use was cut by 100 kg per year for each bearing position, by replacing open spherical roller bearings with sealed spherical roller bearings. The investment paid off in a year while the operational costs associated with each bearing position were halved. This can add up to considerable savings, considering that the disposal cost of grease can be up to three times higher than the purchase cost.
The sealed spherical roller bearing has been designed to provide reliable bearing solutions that offer significantly reduced need for maintenance, extended service life and fewer unplanned breakdowns and production stops. That adds up to longer maintenance intervals with consequent savings in operating costs and staff time.
Being a greased for life concept, the sealed spherical roller bearing has good environmental attributes. It reduces the exposure of potentially polluting grease and cuts the cost of waste grease disposal. In many applications, the bearing housing can be filled with biodegradable grease, which combined with SKF’s three-barrier solution (se bild . 2: housing seals, grease in the housing and a sealed bearing) results in a clean arrangement even for bearings working in tough environments.
The function of the bearing will be as good as it gets, since the bearing grease has been developed by SKF to maximize performance of the sealed spherical roller bearing. In addition, the bearing is filled in a clean factory environment with the right amount of grease, using the right procedure. These prerequisites make it possible to utilize the full potential of the bearing. They provide opportunities for downsizing, since the internal surfaces are protected in a clean environment, which improves the service life of the bearing.
THE SEALED SPHERICAL ROLLER BEARING DESIGNS
Both open and sealed spherical roller bearings have been subjected to significant performance enhancement according to SKF Explorer specifications. This has been achieved through improved steel quality that enables longer service life at heavier loads, new heat treatment processes to improve wear resistance, refinements to manufacturing processes that create smoother-running bearings with improved lubrication and changes to internal geometries of bearings that result in better stress distribution.
The inherent design features of the spherical roller bearing provide the following benefits:
-
self-aligning ability – can accommodate 0.5° misalignment without increasing friction or reducing bearing life
-
high load carrying capacity and robust design – can accommodate heavy loads under difficult operating conditions
-
easy mounting – bearings with a tapered bore provide the possibility to cut installation time, thus reducing maintenance operations and costs.
Essentially, this bearing can be enhanced by a three-barrier solution (se bild . 2). That is using a sealed spherical roller bearing in an SNL housing with standard seals and the housing cavity filled to 60 –100 % with grease (preferably with environmentally friendly SKF LGGB2 grease). The design of the sealed spherical roller bearing (se bild . 3) includes a double- lip reinforced sheet steel seal made of nitrile rubber or hydrogenated nitrile rubber. The seals have been specially developed for spherical roller bearings and effect-ively prevent contaminants from entering the critical rolling contact area. This applies not only during operation, but also during bearing installation, thus contributing to a long service life. The bearing grease fill depends on the operating conditions. The sealed spherical roller bearing with standard seals and grease is designed for operating temperatures up to 110 °C. For higher operating temperature (150 °C), bearings can also be supplied with high temperature grease. Furthermore, the seals have been designed to open with internal pressure, making relubrication possible if the grease life is restraining the bearing service life.
Sealed spherical roller bearings are delivered as complete, lubricated units ready to use, smoothing the path for longest possible service life. Most bearings in the expanded range have the same boundary dimensions as the open bearings (except for those in the 222 E- and 223 E-series that have a slightly larger width) and as such can be drop-in replacements. The SKF range is not only unique in terms of its size, but also because of its wide stock availability.
APPLICATION AREAS
Until now, sealed spherical roller bearings have mainly been used for special applications such as continuous casters (se bild . 4), where high load capacity in the extremely harsh environments is required. However, the extended range of sealed spherical roller bearings makes them appropriate for industrial robots (se bild . 5), for many applications in the materials hand-ling industry for conveyors (se bild . 6), elevators and cranes, in the metal industry for cooling tables and overhead cranes, and in the mining, mineral and cement-processing industries for conveyors, pinion shafts, hoist ways and drilling machine winches.
They are also suitable for use in industries were they can be replacements in applications where self-aligning or high load carrying capacity bearings are required, such as in equipment for agricultural and construction machinery and in mixing applications for the food industry.
In applications where contamination or frequent maintenance is an issue, sealed spherical roller bearings may substitute other high load carrying capacity bearings such as cylindrical roller bearings or tapered roller bearings and open spherical roller bearings.
PROVEN PERFORMANCE
At RWE’s open-cast coal mine operation in Germany, replacement of open cylindrical roller bearings in conveyor impact idlers with sealed spherical roller bearings resulted in a 100 % increase of the service life. Mounting the sealed spherical roller bearing arrangement took half the time of conventional bearings and the greased-for-life solution eliminated relubrication costs and disposal of used grease. In addition, main-tenance staff was able to focus on more critical mining operations.
For another major operator, Askania, which has a major sand-processing facility in Sweden, sealed spherical roller bearings were tested in its extensive conveyor system. The plant handles more than 35,000 tonnes of sand a year and uses 11 vertical and 11 horizontal conveyors with 88 bearing positions. Over a two-year test period, the sealed bearings were compared with conventional open bearings and open bearings with taconite seals. While open bearings failed every nine months, the sealed spherical roller bearing solution kept going equally well as the more advanced taconite sealing system. The sealed spherical roller bearings proved superior, offering lower overall costs and trouble-free operation while eliminating the need for the environmentally unfriendly grease required by the taconite seals and the added costs of its disposal.
The extended range of sealed spherical roller bearings adds up to a design that can offer real benefits to OEM designers and operators. For the OEM, incorporating these bearings offer the opportunity to downsize the complete bearing arrangement without compromising operating life. For the user, the benefits are clear. Sealed spherical roller bearings offer reliability, long operational life, reduced need for maintenance and lower operating costs coupled with environmental savings.