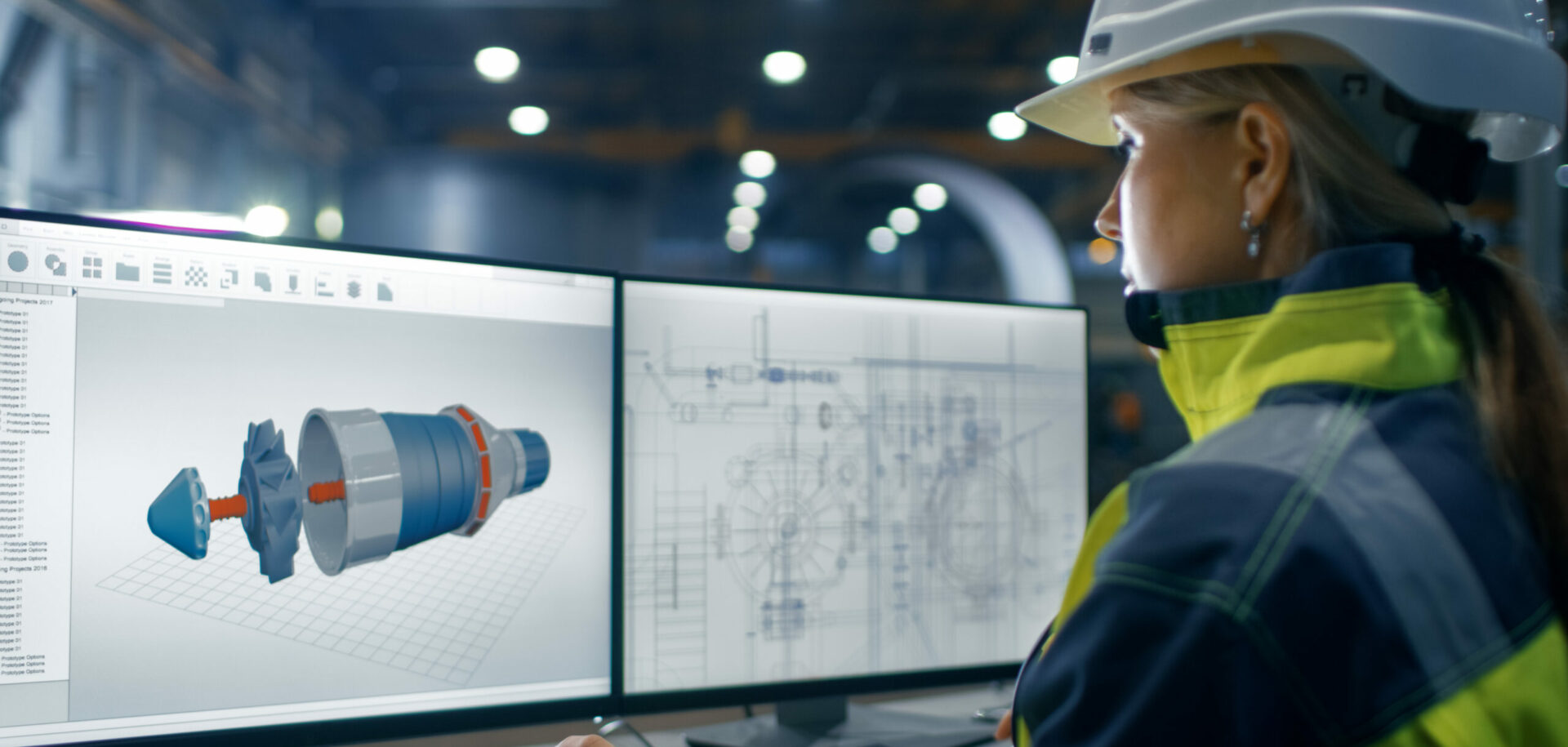
Sealed bearings clean and cost efficient
The sealing adds a number of attributes:
Sealed spherical roller bearings can save space, money and the environment. These are attractive attributes in an increasingly competitive market.Seals on spherical roller bearings open up new areas of application for this type of bearing. Over time, the sales of sealed bearings could represent a considerable part of the total market for spherical roller bearings.
Sealed spherical roller bearings are able to handle high loads and large misalignments, with effective protection against dirt, and at the same time maintain lubrication.
The sealing adds a number of attributes:
- The bearing is protected against external contamination.
- Lubricant is kept in place. This means that the bearings are lubricated for life, or the relubrication interval is extended.
- Easier handling. The bearing is protected against dirt during mounting.
- Space saving. External sealing can be avoided.
The seals are specially designed with two sealing lips – an outer lip that repels coarse particles and an inner one that forms the real seal. This allows for good sealing and a longer life span. In addition, for larger bearings, the seals are simple to dismount, allowing inspection of the bearing and, if necessary, change of seals.
This has been combined with SKF proprietary bearing design technology – self-guiding rollers, strong steel cages and floating guide ring – to create the market’s most effective spherical roller bearings when it comes to load capacity, friction and life. Sealed spherical roller bearings can also cope with misalignment, a condition that will allow good load distribution even if the machine shaft is slightly misaligned.
Where this new product has been applied, it has performed well. The bearing has been tested both in the laboratory and in practical situations, and SKF is continuing further extensive laboratory testing to meet expected future market demands. While the bearing meets its original performance specifications, the extreme limits of its abilities are higher.
All test results show that the bearing’s performance well exceeds expectations in the applications in which they have been used. With the information gained from these tests, it will be possible to recommend the bearing for tougher operating conditions, paving the way for new application areas.
Space saving
A bearing with integral seals requires less space than one with external sealing. This compact solution provides several clear advantages, such as weight and space savings, which the end user can always measure in financial savings. A good example is found in robotics. By replacing the previous bearing arrangement with a sealed spherical roller bearing, the robot bearing arrangement width can be reduced by half. This in turn reduces the overall width of the robotic arm, which means that the end user can put the robot in more confined spaces. This is also a cost-effective solution. A clean environment is not so important when the bearing is being mounted. As a bonus, the bearing does not require relubrication, which also offers savings during maintenance.
Simple mounting
With seals integrated into the bearing, it is less expensive to build-in and mount bearings. A manufacturer of Jacquard looms, a type of machine that produces high-quality woven cloth, has adopted this option. The SKF sealed spherical roller bearing is also ideally suited to the high-shock loads and relatively low speeds required in this textile application.
Machining operations in the housing to accommodate separate seals are no longer necessary, and the complicated mounting processes for seals can also be avoided. In addition, the bearing is fully protected from the introduction of dirt during mounting, and initial lubrication is already provided. In most cases, relubrication is not required in service for these looms. If necessary, relubrication can be provided using the SKF feature designated W33.
Environmentally friendly
In trams, sealed spherical roller bearings are used to provide an environmentally friendly solution. Such vehicles are subject to frequent stops and starts with a moderate running speed. In this application, the C/P ratio (the ratio of basic dynamic load rating to equivalent dynamic bearing load) is around 10. The need to change to sealed bearings was to reduce oil leakage through external seals. Previously oil-lubricated bearings were used where the same oil was used to lubricate both these bearings and the gearbox. With a sealed bearing, the bearing is lubricated with grease and the bearing seals give extra protection. All this means that considerably less oil is spilled.
Dirt protection
One of the areas in which the seal’s protection qualities are used is in steel manufacturing. Sealed spherical roller bearings have been successfully applied in continuous casting machines and roller tables. In casters, molten steel is transformed into sheet iron, slabs or billets. Bearings are used in the support rollers of the conveyor system and are exposed to constant streams of water mixed with salt and contaminants. In this application, the temperature acting on the bearings can vary between 20 °C and 180 °C and the support roll speeds are normally between 2 and 10 r/min with a C/P ratio usually of less than one.
Traditional external seals are insufficient to prevent the entry of steam and scale. The old solution was to continually lubricate the bearings to protect them from dirt. This requires enormous consumption of lubricant. A single slab caster can consume up to 50 tonnes of grease annually. With sealed spherical roller bearings, consumption is reduced dramatically. The sealed bearing does not require relubrication, while the external seal is only occasionally relubricated.
In practice, this means that use of grease is reduced to a few tonnes per year. As well as the reduced use of lubricant, which produces savings, even larger savings are to be gained through eliminating the need to deal with the lubricant-contaminated wastewater. Another bonus is that it is easier to keep the cooling system clean. This means that all parts that need to be cooled can be kept cool. In turn, the number of breakouts, where the cast of steel breaks open and liquid steel spills out, are reduced drastically.
Sealed spherical roller bearings are available in two variants, one for normal temperatures up to 110 °C and one for high temperature applications up to 180 °C. The bearing is available with different lubricant and seal material alternatives. The range contains bearings for shaft diameters of 40 mm to 220 mm.
Further development
Experience of current sealed designs is very encouraging. As there is significant potential for sealed spherical roller bearings, SKF is committed to further long-term investment in this product. This allows SKF to offer customers a wide range of bearing sizes.
Håkan Lindgren,
SKF AB, Göteborg, Sweden