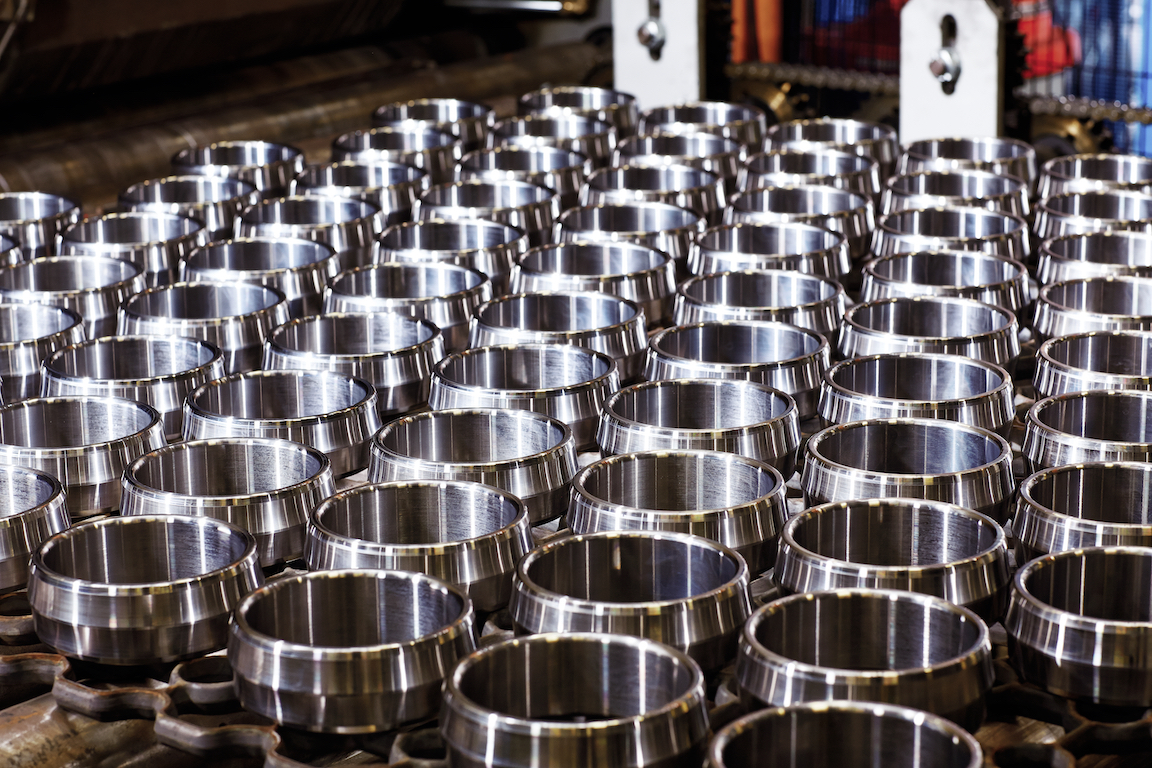
Shared ownership, shared rewards
Just as a company car assigned to an individual is more likely to be properly cared for and serviced than a pool car driven by many, the owner of the family automobile is naturally motivated to keep the vehicle running smoothly. What drives this behaviour is a feeling of ownership.
When machines are taken care of by operations and maintenance staff in cooperation with each other, reliability is improved.
Most people take considerable care to ensure that their automobiles don’t break down. Many drivers will regularly check the oil and perform other basic maintenance, only consulting a specialist when specific skills or tools are required.
Just as a company car assigned to an individual is more likely to be properly cared for and serviced than a pool car driven by many, the owner of the family automobile is naturally motivated to keep the vehicle running smoothly. What drives this behaviour is a feeling of ownership.
On the factory floor, maintenance and operations personnel who feel a sense of shared ownership about the reliability of day-to-day operations will more willingly work together as a team to achieve results. This is the philosophy behind operator-driven reliability (ODR): Shared ownership brings shared rewards.
Preventing problems before they happen
ODR places operations and maintenance personnel side by side, in order to capitalise on each other’s expertise, and lets operators perform certain maintenance activities as well as interact with other departments that impact on plant-wide reliability. The goal is to prevent problems before they happen and to optimise the life-cycle costs of the plant by spotting early on where reliability can be improved.
An increasing number of companies are taking ODR practices on board as part of their maintenance-reliability programmes. This means daily coordination between equipment operators and the maintenance department. This is a hands-on approach. Operators perform certain maintenance tasks to decrease equipment downtime.
A parallel trend in the maintenance world is the growth of reliability-improvement technologies such as process control, computerised maintenance management systems and new generations of handheld equipment. Taking these trends together, the term ODR has emerged.
While involving operators in the maintenance of equipment to improve reliability is not a new concept, attempts to implement an ODR programme are not always successful. The key is that sense of shared ownership.
In some arguably more enlightened companies, the concept of plant ownership is a tacit, inherent part of the workplace culture. In other companies, the culture is one of “mutual blame.” In some cases, this has resulted in rigid lines of demarcation between “operations” and “maintenance.”
A cross-functional effort
Operators at Mobil Corporation’s Beaumont Refinery found that ODR was a way to engage both the top and bottom of the organisation. At the Industrial Services International Conference in 1999, reliability engineer Walter Jones and his team presented their efforts to reduce the costs of unreliability at the refinery by 100 million US dollars over the next five years. Requiring a “fundamental change in the culture of our site,” Jones reported that the new approach was already beginning to deliver substantial bottom-line results.
“By getting your operators and craft people involved, you can quickly eliminate a lot of the nagging defects and begin to change the culture,” Jones and his team reported. “Previous efforts had failed because we had gotten into the ‘paralysis by analysis’ mode. The equipment does not run better until you take some action to improve it.”
Reliability is a cross-functional effort, the Mobil Beaumont Refinery experience showed. “The main costs of unreliability are in the process,” says Jones. “Many of the defects come from the way equipment is operated and can only be detected early by the operators.
If you cannot engage the operating group in reliability improvement there is not much point in continuing. There is limited value that can be added through only a maintenance functional approach.”
Keith Burres, director of international operations for HSB Reliability Technologies in Texas in the US, shared another example of bottom-line results from ODR in a recent issue of Maintenance Technology magazine.
He reported that at one plant, pump cavitation typically resulted in 88 hours of downtime per year. By optimising the frequency of lubrication, production increased by 16,000 tonnes in the first year. The operator focus on reliability also led to an improvement of 30,000 tonnes in the first-pass quality product, and overall equipment effectiveness rose from 85 percent to 89 percent.
What operators need to know
There are some fundamental aspects of an ODR programme, no matter what kind of company or technologies are in place. Operators who will be involved in maintenance activities need to know:
- What to do when a problem is observed
- what not to do when a problem is observed
- What tasks fall within the limits of their competence
- What tasks are outside the limits of their competence.
These concrete actions demonstrate clearly that ODR is a distinct group of activities that make things happen, rather than simply suggesting what should happen. Experience shows that if properly implemented, ODR is a versatile practice that can make a valuable contribution to the success of an overall maintenance-reliability programme.
Overcoming barriers
The lines of demarcation that frequently exist between maintenance and operations are one of the most obvious barriers to implementing a total productive-maintenance programme with ODR at its core. In many organisations, maintenance and operations function virtually independently of each other, each with separate objectives and structures.
Transforming a culture of blame into one of shared ownership may be a big hurdle, but it can be done. Successful implementation of an operator-based inspection programme requires an understanding that the activity ultimately benefits all parties. And it requires that management buy into the programme from the top down.
Individuals from all areas of the business need to fully recognise and respect the skills and experience of the other parties and the contributions that they make. Disputes should be discussed and resolved in an environment of courtesy and cooperation, with all parties contributing in a frank and honest manner.
When an ODR programme is implemented within a general atmosphere of enthusiasm for the benefits that the programme brings to the organisation, it can not only dramatically reduce downtime and improve profitability, but it can enhance workplace culture.