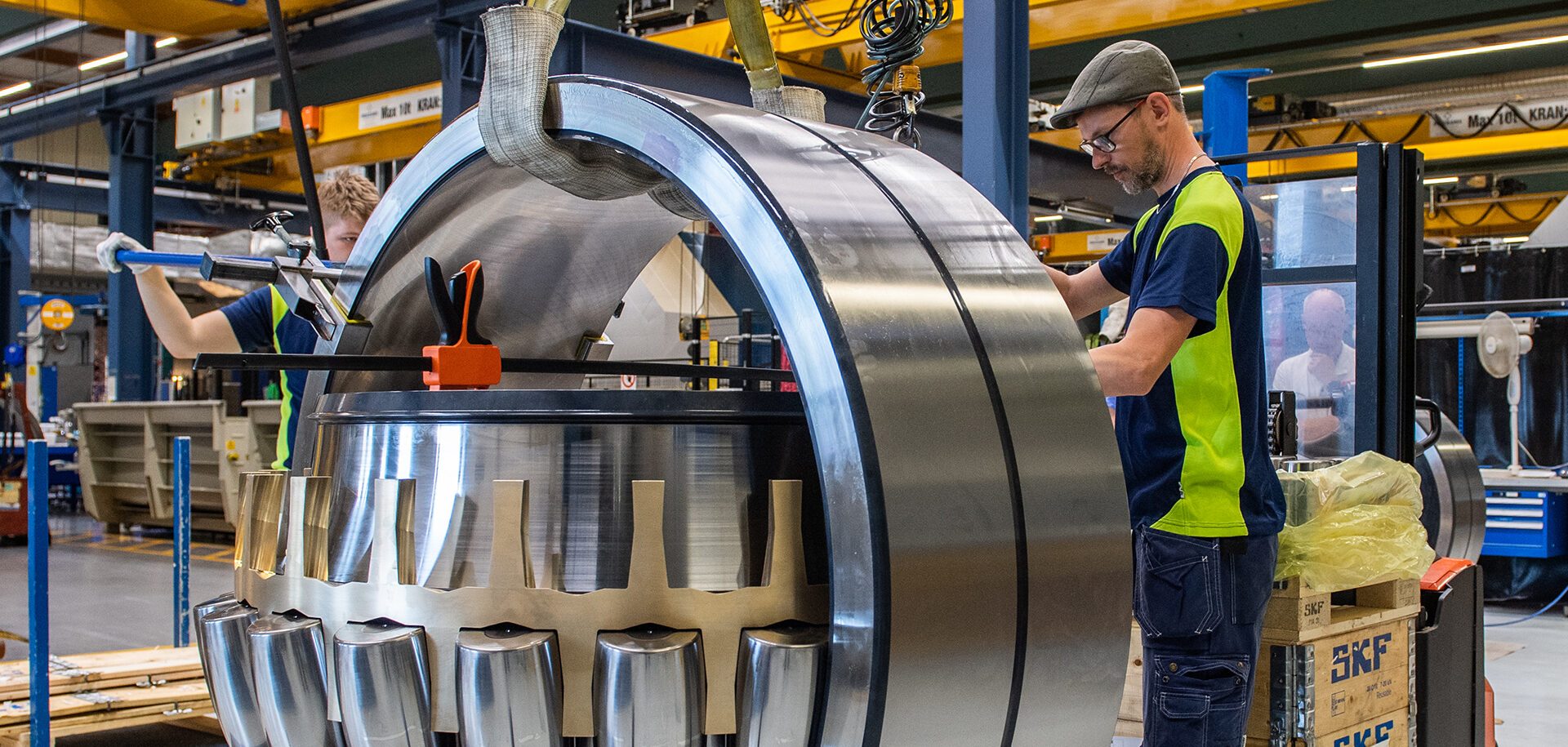
SKF delivers large order of sealed bearings to mineral mine in Latin America
SKF in Gothenburg has delivered a large order totalling twelve large sealed spherical roller bearings with an outer diameter of up to 2.5 metres, intended for a mineral mine in Latin America. The newly designed sealed spherical roller bearings are now in full series production at the factory in Gothenburg.
“This delivery is a confirmation that our customers see considerable value in the new bearing design, where the Gothenburg factory is alone on the market when it comes to mass-producing this size and design,” says Daniel Ortega, Product line manager for sealed spherical roller bearings at SKF.
There is a high level of demand for minerals around the world, which is putting pressure on efficient operations and a flexible supply chain for the mining industry. As a result, operators are not that keen to move away from tried and tested bearing arrangements in critical mechanical equipment. A traditional bearing solution in a rock crusher consists of an open bearing into which grease is pressed, which in turn creates a barrier that prevents dirt from entering the bearing.
The new bearing design from SKF, which encompasses large bearings with an outer diameter of up to 2.5 metres, comprises two seals that protect the bearing’s rollers, cages and raceways against dirt, which significantly increases the bearing’s service life. The bearing also has the same load capacity as an open bearing. The seal solution means that grease consumption can be substantially reduced. One customer using the new bearing design in a rock crusher managed to reduce their annual grease consumption from as much as 540 kg to just 7 kg. This saved the customer money and also has a positive impact on the working environment.
This delivery is a confirmation that our customers see considerable value in the new bearing design.
Daniel Ortega, Product line manager for sealed spherical roller bearings at SKF
In addition, the bearing can be reconditioned and used again, twice, an option that is leading to more and more customers in the mineral and mining sectors starting to take an interest in the new design. The reconditioning work is performed in one of SKF’s global services centres. These are situated close to the customer in geographical terms, reducing the risk of long delivery times and resulting in lower CO2 emissions.
“We have a head start in that we are the first to mass-produce this design, and so far we have more than 160 different sizes of this type of bearing in a sealed design. For us, it is a matter of constantly developing our products to achieve efficient performance from rotating equipment with as little impact on the environment as possible. These sealed bearings represent an important element in the creation of sustainable circular economy,” says Daniel Ortega.