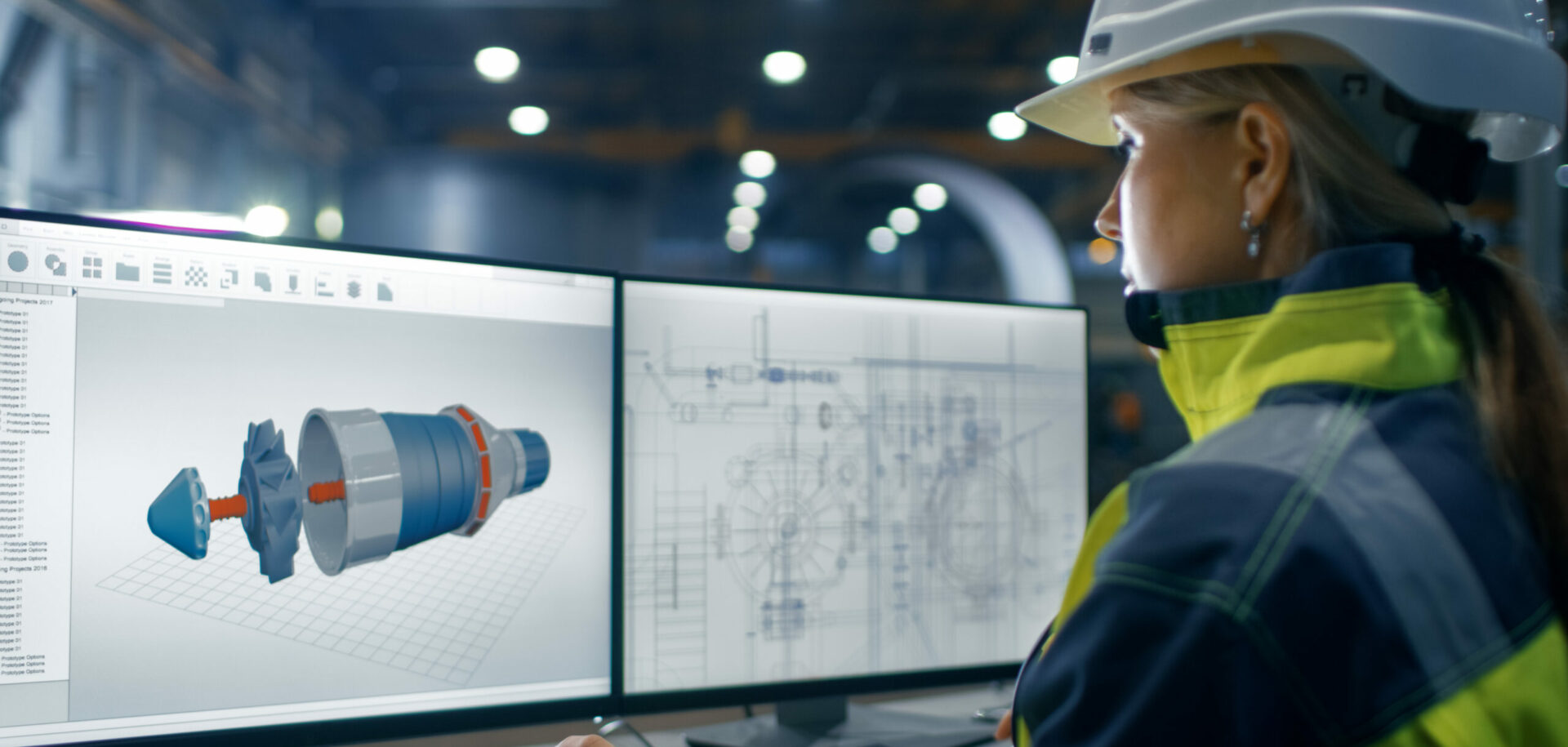
SKF solution for railway articulation joints
Low-floor mass transit vehicles offer easy entry for passengers. Modern articulated vehicle designs containing several body sections enable easy access inside the vehicle and contribute to passenger safety. The articulation joints of these sections contain special plain bearing solutions developed by SKF.
Low-floor mass transit vehicles offer easy entry for passengers. Modern articulated vehicle designs containing several body sections enable easy access inside the vehicle and contribute to passenger safety. The articulation joints of these sections contain special plain bearing solutions developed by SKF.
Today there isan increased public and political awareness of the need for collective mobility, especially in crowded urban and suburban areas. This opens new opportun-ities for further development of mass transit systems and, as a consequence, encourages the rolling stock industry to pursue novel solutions. Innovative vehicle generations provide superior quality, comfort and safety in transport.
Modern mass transit vehicles such as multiple units, suburban trains, metro cars, light rail vehicles and trams are based on articulated body designs. There are different configurations on the market with 2 to 7 connected vehicle body sections. Previously, several independent vehicles such as power cars and trailers were coupled to a train. The disadvantage of this is lower passenger capacity, no access inside the train and a diminished feeling of safety for the passengers. Today, articulated mass transit vehicles offer new advantages to increase efficiency and to provide higher passenger safety (figs. 1 and 3).
Articulated vehicle bodies can be joined by using bogies underneath, known as Jakob’s bogies. In this case a larger number of bogies have to be applied, which increase weight and cost. Another design principle, which is used more and more, is to connect vehicle bodies directly with articulated joints and reduce the number of bogies. Articulated joints have to enable three-dimensional movement of the two connected vehicle bodies.
The sliding angles and velocity are very low and depends on the track design, such as curve radii in horizontal and vertical directions and the speed. In addition, important emergency buffer strokes in horizontal direction need to be considered. In most applications the articulation joint is well protected and outside the body design. Maintenance is not easy and should be avoided wherever possible.
Typical requirements
- Accommodation of various loads and motion cycles according to VDV 152 , EN 12663 and customer specifications
-
Operational dynamic and static load cases, plus emergency buffer strokes (table 1)
-
No disconnection of the joint in an emergency case
-
Three-dimensional functionality for cornering, rolling and pitching (tilting) from operation and distortion of the bodies
-
Compact and space-saving design
-
Easy integration of the joint into existing supports from light alloy or cast iron
-
Operation without noise and stick-slip free
-
Insensitivity to cleaning media, salt-spray, corrosion attacks and contaminants
-
Low life-cycle costs.
Structural requirements for rail vehicles for the public mass transit in accordance with BOStrab.
Structural requirements of railway vehicle bodies.
Product features, design
The special thrust spherical plain bearing (fig. 2) consists of:
1. A case-hardened shaft washer having a hard-chromium plating on the ball-shaped raceway with precise interface diameter and threaded holes for connection purpose
2. A housing washer
3. The housing washer inserts of high-performing PTFE-composite polymer shells
4. A central bolt acting as an anti-lifting device, having a ball-shaped head and being adjusted with clearance relative to the shaft washer
5. A lock nut (if the central bolt is not directly connected to the housing washer)
6. A flexible two-lip seal connected to the housing washer
7. A polymer cover sealing the top of the bearing
Modern computer simulations are used when designing railway joints. This enables calculation of the reaction forces, in particular for the worst case, which is the maximal emergency horizontal force combined with a minimum vertical load. The vertical reaction force has to be taken by the anti-lifting device and all bearing parts, and determines the necessary bearing size. In addition, the design of the adjacent parts or special mounting needs has to be taken into consideration. Although the bearing is customized and adapted to the operating conditions, it follows the basic design, which contributes to keep costs down.
The sliding material combination is the core of this particular bearing design.
It ensures smooth, reliable operation to provide a long service life, even under dry or boundary lubrication conditions. The poly-mer material that is thoroughly anchored to its substrate is supplied with an effective wear thickness of approximately 2 mm (fig. 4).
Compared to other, thinner dry-sliding materials, it is less sensitive to the entrance of abrasive particles and thus a better choice, especially when considering the requested reliability. The sliding material also exhibits quite good damping properties, which is beneficial for railway applications. Also, the material has very good wear-resistant properties, with an almost linear wear rate, which facilitates service life prediction (fig. 6).
The sliding material friction values are excellent, exhibiting low noise levels and no negative stick slip. The tribological behaviour of the joint can be further improved when appropriate lubrication is applied. Even though the sliding material combin-ation might also be operated completely dry, SKF supplies the bearing with an initial grease fill and provide a possibility for relubrication (fig. 5).
Relubrication not only enhances the tribological mechanism but also gets contaminants out of the bearing and improves the protection against corrosion.
Field experience
For almost 30 years, SKF has gathered very positive field experience with the sliding material combination steel/PTFE-composite polymer in railway and mass transit vehicles. This experience is reinforced in applications with comparable dynamic operation, such as thrust spherical plain bearings in ladle turrets in steel works, bascule bridges, cranes and ship loaders.
Wear measurements of inspected tram bearings after eight years of service and mileage of about 500 000 km showed an amazing low amount of wear. The bearings were found in an excellent condition and could be further used for another period of time. With its specific design, SKF has set an industrial standard for articulation joints. This is well accepted by the majority of manufacturers of mass transit vehicles.
Customer benefits
-
Reliable operation
-
Low life-cycle costs (LCC)
-
Ready-to-built-in solution customized to the envelope space
When developing these special spherical plain bearing units, SKF has been closely working together with leading vehicle producers. The plain bearing engineering team has been carefully analyzing its requirements and incorporated them into bearing technology.
As the railway industry belongs to the most sensitive concerning safety and LCC, it is therefore crucial to provide reliable value-added integrated solutions to acceptable costs.
Applications
Meanwhile various executions for 400 kN and 800 kN buffer strokes and for different tram configurations have been developed and manufactured, all to the same design principles with the well-proven sliding material combination in its centre and the anti-lifting device as a ready-to-mount “black box.” From the first use of standard thrust spherical plain bearings the articulation has evolved to a value-added unit fulfilling the ever-increasing requirements of the railway industry. The spherical plain bearing joints supplied by SKF are contributing to the safe transport of passengers in cities all over the world.