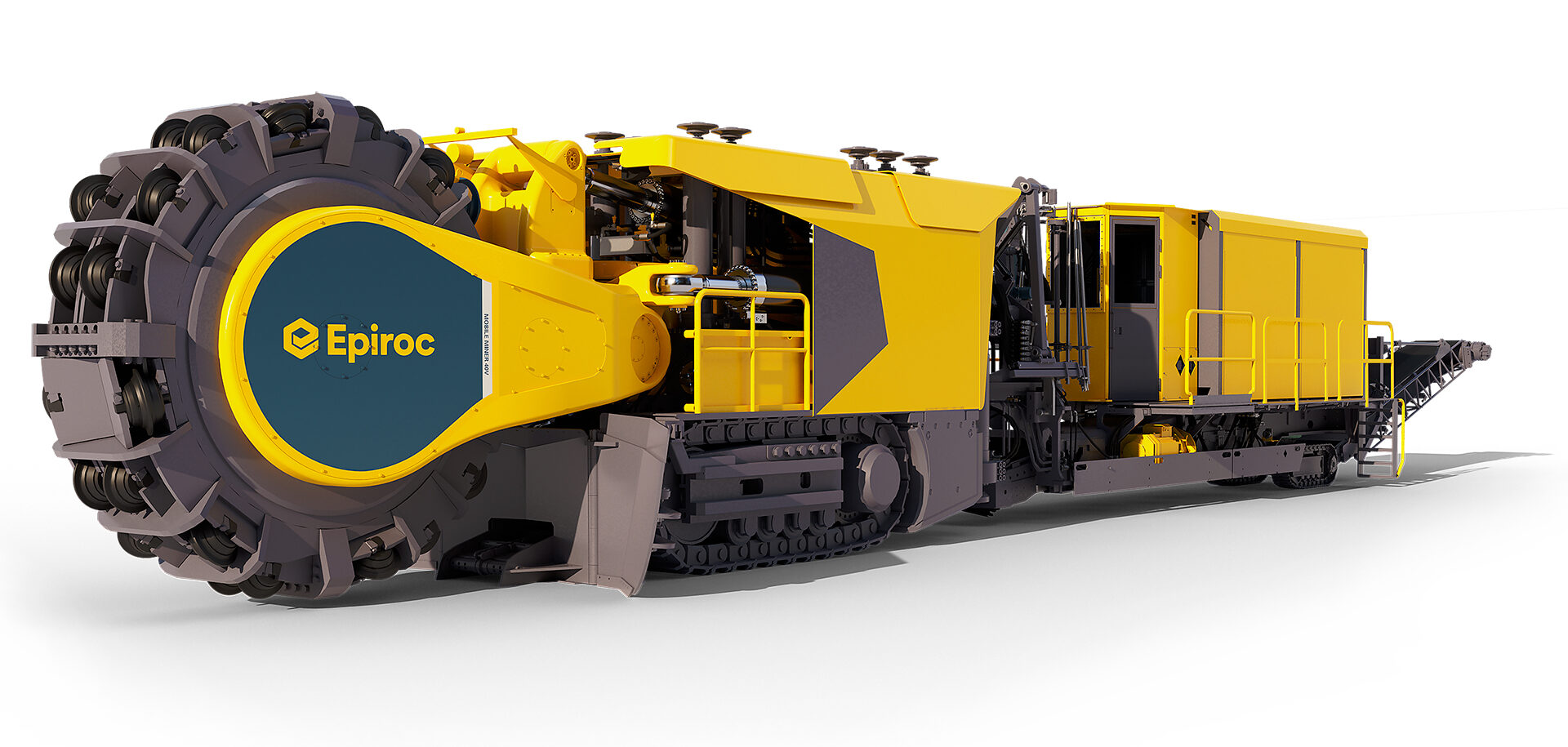
Solid as a rock
In the mining industry, increased demand for higher productivity and safer working conditions is creating opportunities for Sweden’s Epiroc and the company’s Mobile Miner machines.
One company to see the opportunities in this trend is Epiroc, a leading productivity partner for the mining, infrastructure and natural resources industries based in Sweden. Epiroc has a history of supplying drilling and mining equipment that stretches back to 1873, with the founding of Atlas Copco. Epiroc and Atlas Copco had a common history until June 2018, when Epiroc was distributed to Atlas Copco’s shareholders and became a stand-alone stock-exchange-listed company.
Since the early 1970s, Epiroc has been producing different types of tunnel drilling machines, and over the years a number of Mobile Miner rigs have been developed. Today, Epiroc is running a Mobile Miner project together with customers in different parts of the world. So far, three models have been developed – Mobile Miner 22H, 40V and 55V. The number indicates the size capacity of the machine (“55” refers to 5.5 metres), and the H and V indicate whether the cutter head is horizontal or vertical.
Custom-made bearing
“In the case of Epiroc’s Mobile Miner 40V, we have developed a special bearing that is a combined radial and axial roller bearing with an outside diameter of 2.18 metres,” says Ola Björkdahl, application engineer at SKF.
“We have also supplied specially designed sealings in G-ECOPUR that are suitable for these very demanding applications.”
Equipment used in mines is exposed to dust, water and gases, as well as vibrations caused by the excavation operation. SKF service engineers have assisted Epiroc in the assembly of the Mobile Miner 40V. “As always, it is paramount that the bearings are mounted properly,” says Björkdahl.
The front end of the Mobile Miner is equipped with a rotating cutter head, which is pressed into the rock. The excavated material is transported backwards using conveyor belts, and the shaft is then bolted by the machine, which means that the operator, who is running the machine from the back end, has a safe working environment.
Safety is of course one of the most important reasons for using the Mobile Miner.
Johnny Lyly
Global product manager for mechanical rock excavation
“Safety is of course one of the most important reasons for using the Mobile Miner,” says Lyly. “Compared with using drill and blast, this method also has less impact on the surrounding rock, which reduces the risk of accidents.”
Another important advantage with the Mobile Miner is the fact that it can produce tunnels at the same cost as the drill and blast method, but the efficiency is higher due to the continuous excavation. “If a mine is having an efficient drilling and blasting operation, they can advance some four to eight metres per day,” says Lyly. “With the Mobile Miner, you can easily double that.”
The Mobile Miner machines are developed in close cooperation with Epiroc’s customers for specific applications.
The Mobile Miner 22H is a powerful mechan-ical rock excavation machine. It is typically used in low seam or low profile mining for tunnels as low as 2.2 metres. The capacity of Mobile Miner 22H is 10 to 12 metres per day advance depending on rock type. It is currently being tested in South Africa, where the rock has a high tensile strength and is very ductile.
Mobile Miner 55V is typically used in large-size access tunnels (up to 5.5 x 5.5 metres) for mine development and material haulage. Thanks to the continuous mining technique, mine projects become easier to plan and more time-efficient compared to the drill and blast method. Some of the available automation features are laser navigation, remote monitoring/control and automatic rock cutting of the face.
The latest model, Mobile Miner 40V, is typic-ally used in small to medium-sized tunnels and cut-and-fill mining when a tunnel of about 4.0 x 4.0 metres is needed. The capacity of Mobile Miner 40V is 10 to 15 metres per day advance, depending on rock type. In August 2018, Epiroc received its first order for a Mobile Miner 40V from a mining company in the United States.
In future, Epiroc expects the Mobile Miner to take a central role in mining challenges around the world. “The Mobile Miner is a small, flexible and customizable machine that makes mining projects more productive, predictable and easier to schedule,” says Lyly.