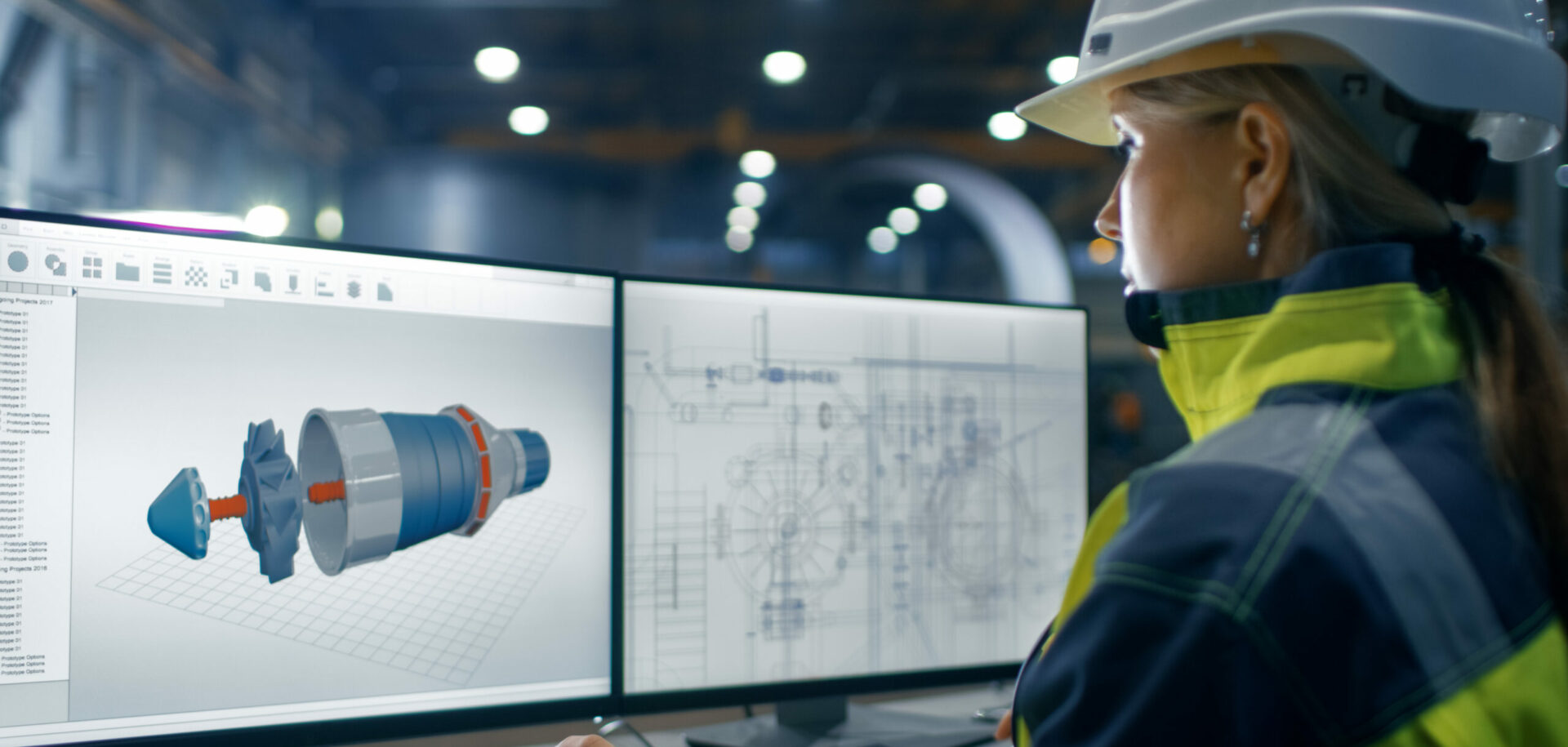
Solutions for railway bogie condition monitoring
Bogie condition monitoring offers new opportun-ities to increase reliability and safety and achieve lower maintenance costs. Incipient damage can be detected and mechanical failures prevented.
Facts
Applying the knowledge and experience of the wind mill industry has added a number of possibilities to the railway industry. It employs the use of intelligent sensing technology for critical components coupled with communications tracking through a global positioning system. The result is a bogie condition monitoring system that supports extended maintenance intervals with safe and reliable train operation.
The railway industry is constantly looking for methods and technology to significantly reduce life-cycle cost (LCC) and total cost of ownership (TCO). For more than 150 years, even before the economic terms LCC and TCO where invented, fragmented reporting systems were used to help establish railway vehicles costs. Purchasing cost, coal consumption for steam locomotives, workshop man-hours per operating mileage and spare-part costs were some of the main indicators of efficient railway operation, although reporting was rarely consolidated.
From the beginnings of railway technology, there was always a strong focus on reliability and safety. Traditional on-the-spot repair was quickly replaced by maintenance schedules based on mileage and/or time. Sometimes this led to maintenance intervals being too short, resulting in lost revenue opportunities from unused operational time and mileage still available on rolling stock.
However, under certain situations reduced maintenance intervals were required – for example, where railway vehicles operated on specific challenging lines, such as in alpine regions or on very poorly maintained tracks, under extreme weather conditions or when derailments went unreported during shunting operations.
LESSONS FROM WIND POWER
There is a continuously increasing demand for reliability and safety as well as for mainten-ance cost reduction. Condition monitoring is a mature technology, and the railway industry has benefited from such advances. In other industries, such as wind power, for years maintenance schedules have been based on condition monitoring results. Wind farm operators take a proactive approach to maintenance, thereby reducing operating costs.
An online condition monitoring system enables the operator to monitor individual turbines and gearboxes or an entire wind farm in order to predict when maintenance will be necessary. SKF’s WindCon online condition monitoring system collects and analyzes the mechanical data, compiles it and provides a reliable performance overview in order to identify incipient damage and predict possible failures before they occur. With this information it is possible to plan maintenance activities more effectively and to extend the time between costly offshore site visits.
Data are presented using an Internet browser, and the information is up-to-the-minute. The web-based version takes advantage of WebCon – SKF’s data warehousing and web-hosting services. This tool helps to shorten the lead time from alarm to solution, since authorized personnel can do the monitoring from any location with a computer or handheld device with Internet access. The simplified maintenance and increased reliability that SKF WindCon provides can be enhanced with the WindLub centralized automatic lubrication system for wind turbines.
This system easily integrates with SKF WindCon, so along with fully automated lubrication, the combination provides operators with a complete overview of the lubrication system, including pump status and lubricant levels. A team of SKF engineers is dedicated exclusively to wind turbine condition monitoring issues and the management of installed systems. SKF WindCon is approved by Allianz and certified by Germanischer Lloyd. A main driver for implementing condition monitoring into the wind power industry has been the requirements set by leading insurance companies.
RAILWAY CONDITION MONITORING
There are quite a few similarities between the basic reliability and maintenance requirements of wind turbines and railway vehicles, but there are significant differences as well. Wind turbines are stationary while railway vehicles are mobile, operating over vast areas and sometimes covering several countries.
This means not only different geographical locations, but also different technical requirements, and even the basic technical regulatory standards can be very different. The average life expectancy of railway rolling stock is also much longer than the life expectancy of a wind turbine, which makes the threshold for entry of new technology into the railway industry higher and more difficult and takes a longer time, particularly if one wants significant improvements in reliability, safety and cost of operation.
Bogie condition monitoring includes sensors for the detection of running instability according to the requirements of the European Technical Specification for Interoperability (TSI) Directive 96/48 EC. The TSI stipulates that the monitoring of the running stability must be continuous or at a frequency to provide reliable and early detection of damage. For Class 1 trains the system must also be linked to the onboard diagnosis data recorder in order to enable traceability.
Wheel set condition monitoring is implemented by a vibration sensor mounted on the axlebox housing, or integrated into the axlebox bearing, to provide information that can be used to determine the condition of the wheel set, such as wheel flats and wheel shape. The real-time calculation also uses information about the shaft speed. Wheel maintenance is very costly and time-consuming. With bogie condition-based maintenance, the timing of these operations can be scheduled by optimizing the operating mileage of wheel sets without any compromise to reliability and safety.
For decades axlebox bearings have been monitored in the railway industry by means of stationary trackside-mounted temperature- and noise-detection systems. This equipment is typically installed at certain intervals along the track or at strategic locations, such as ramps in the case of alpine railway lines. Such a system typically provides an indication of heavily worn or damaged components. As a result, the train must be stopped and the faulty wagon replaced and sent to the next suitable workshop. This causes operational delays and additional costs.
DYNAMIC FREQUENCIES
The onboard axlebox condition monitoring system IMx-R from SKF may be part of the train’s bogie condition monitoring system or may work as a stand-alone system. This system also fulfils the requirements of the TSI, which stipulates that the equipment must be able to detect a deterioration of the condition of the axlebox bearing by monitoring the temperature and/or its dynamic frequencies. The maintenance requirement is generated by the system, and the system indicates the need for operational restrictions when necessary, depending on the extent of the bearing damage. The detection system operates fully independently onboard the train, and the diagnosis messages are communicated to the driver.
Rollers and inner ring raceways of axlebox bearings, as well as toothed wheels all generate specific dynamic frequencies, which can be detected and analyzed with additional knowledge of certain geometry data and shaft speed. Minor geometry bearing differences such as spalls can also be identified very early through the analysis of the generated frequency spectra.
Traction motors and gearbox components such as bearings and toothed wheels may also be monitored, as well as shafts and couplings, using vibration sensors as part of the bogie condition monitoring system. Gearbox oil level and temperature, and more recently, oil condition may also be included in the bogie condition moni-toring system or may be monitored in a stand-alone mode. Vibration signatures from propulsion components vary, depending on the actual traction effort applied. Consequently, information about the train speed and load has to be considered in the data processing, together with certain geometric parameters and the gearbox ratio.
GPS TRACK PROFILING
Information from the axlebox vibrations through the bogie condition monitoring system linked with a global positioning system, GPS, facilitate profiling of the track sufficiently accurately to determine deterior-ation of the track as seen by the wheel sets over time. The system may accommodate any type of sensor, but principally vibration sensors are used.
Furthermore, the system collects, analyzes and compiles a range of operating data. The system provides a reliable performance overview that identifies incipient damage and predicts possible failures before they occur, enabling operators to consolidate maintenance activities and perform necessary inspection and repair work during planned stops. This also creates the possibility of extended maintenance intervals and less unexpected downtime and costs, which results in a longer bogie uptime. The collected data also enables root cause failure analysis, which facilitates the elimination of recurring problems and failures through equipment improvements and redesigns.
Using existing onboard vehicle information sources along with additional sensors to monitor operating parameters, maintenance cost, reliability and safety can be improved significantly, and the system may be installed on new vehicles or retrofitted. SKF has conducted a number of tests on different type of trains, including very-high-speed trains in Europe and Asia. The experience so far confirms the expectations of the OEM as well as operators.
SKF Axletronic is a trademark of the SKF Group.