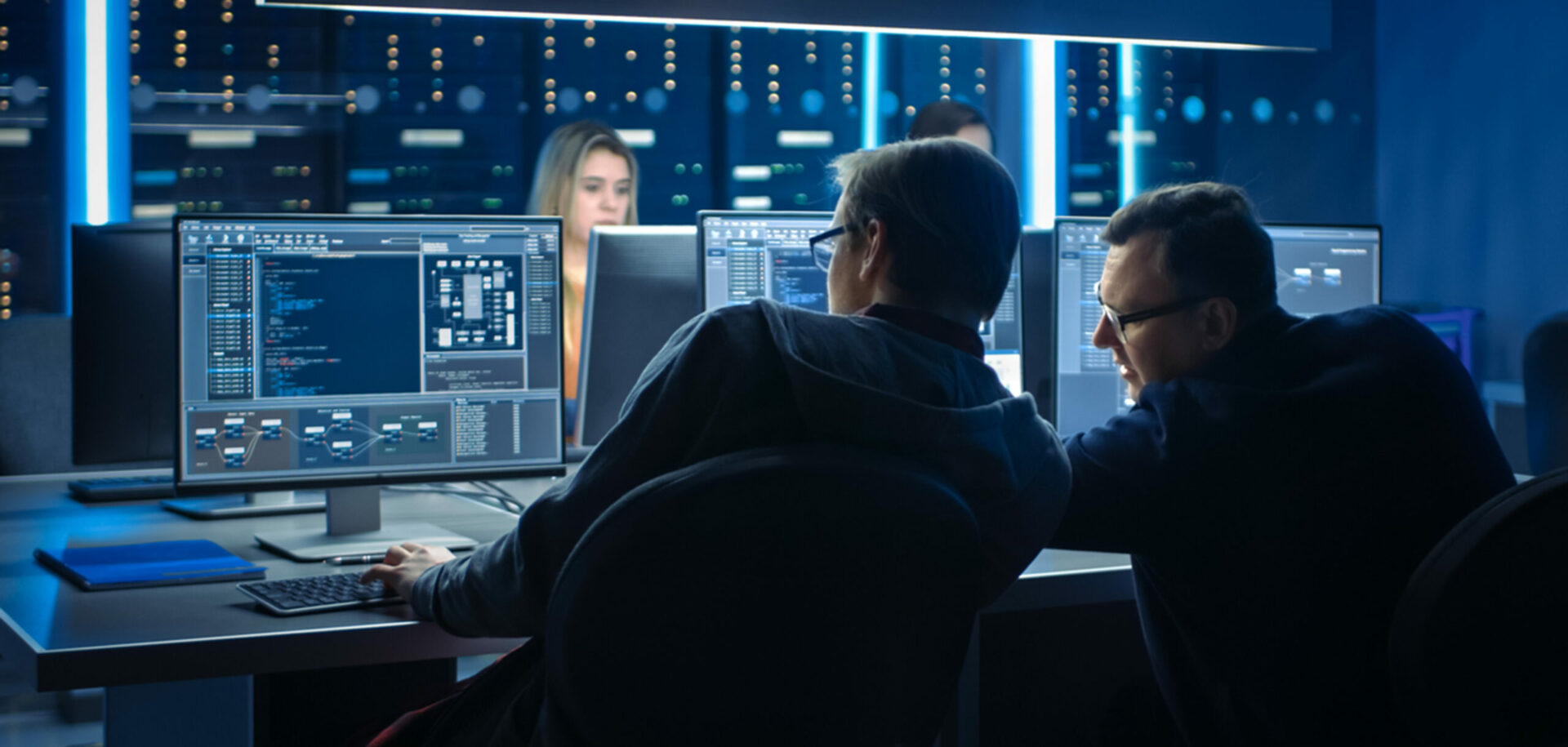
Taking a step-by-step approach to remote industrial maintenance planning
In the aftermath of the global pandemic, many industrial plants were forced to rethink and reengineer their supply chain, operations, and manufacturing processes. The need to limit the number of workers at a plant due to health-related concerns was a catalyst for change. Many executives who previously considered Remote Industrial Maintenance within the context of operational planning now recognize its strategic significance.
The handbooks were based on insights from working with many of the world’s largest manufacturers and our expertise in Rotating as a Service. We also include benchmark data from SKF research conducted as part of Client Needs Assessments performed at over 1,400 organizations globally.
This article covers a high-level summary of the Cross-Industry Handbook highlighting the topics covered in each chapter.
In addition to the Cross-Industry Handbook, there are industry specific versions for the Pulp & Paper, Steel and Chemical sectors available. Go directly to the SKF Remote Industrial Handbooks.
Chapter 1: Strategic application of remote industrial maintenance
What is remote industrial maintenance?
It starts with data. Industrial plants generate terabytes of data from sensors embedded in machinery. With the precipitous fall in costs such as data storage and computational power, machine learning can now be applied to the analysis of this data and provide real time operational industrial analytics. This type of industrial analytics (also referred to as remote monitoring) can be used to detect evolving asset degradation prior to shutdown or (depending on the maturity of the solution) even identify the failure mode and effects analysis (FMEA). Other elements of remote industrial maintenance include automated or machine- assisted processes for scheduling, spare parts management, repair, and inspection activities.
This chapter explains the elements of remote industrial maintenance and explores some of the emerging economic and regulatory trends and how they impact the shift to Remote Industrial Maintenance.
Chapter 2: Planning for the remote industrial maintenance roadmap
We identify some of the common strategic objectives which should be considered as a starting point for a prioritizing remote industrial maintenance. The next step is to gain an understanding of the current state of each of the remote industrial maintenance components.
An assessment requires input from plant level employees on maintenance practices and an understanding of the maturity of plant (and organizational) data maturity. In addition, stakeholders responsible for both operational technology and information technology should be included in auditing processes.
The Big Data audit:
An industrial plant’s data infrastructure is critical to the success of remote industrial maintenance and is a prerequisite to asset digital digitalization. To minimize implementation risk, a thorough audit of current data collection, management and governance is necessary.
Asset criticality assessment:
Asset criticality is defined as the ranking of an asset in order of its importance to the business. It is often calculated in terms of the consequence of an asset failing to perform its intended function and the likelihood of the failure occurring. Criticality is based on functional failure within a specific operating context. To determine functional failure requires an understanding of the specific function.
Remote industrial maintenance road-mapping:
Define deployment goals for each element of remote industrial maintenance based on the asset criticality assessment. The timing definitions (short-term, medium- term and long-term) are based on the priority of each element and the extent to which there are dependencies.
Chapter 3: Risk identification and assessment
Many plants consider remote industrial maintenance to be strategically compelling but the immense challenges facing the industry are not a pretext to bypass risk assessment. The core elements of change – organizational, process and technology need to be carefully evaluated from both a financial and operational perspective.
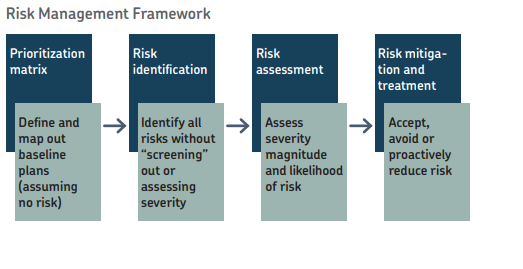
1 – What is the consequence to the successful deployment of remote industrial analytics if the risk occurs?
2 – What is the probability of this occurrence?
Only once risk is fully understood can we devise a plan to mitigate against it. After a risk is identified, there are three potential options:
1 – Proceed with the plan without considering the risk
2 – Eliminate the project or the element of the project from the plan
3 – Develop a mitigation strategy to address the underlying risk
Chapter 4: Estimating the financial benefits
The decision to move forward with one or multiple components of remote industrial maintenance is based on a specific business consideration. In this section we provide guidance on how to estimate the benefit of reduced unplanned downtime.
Industry benchmark data (SKF Client needs analysis – asset management):
This is a comprehensive, independent assessment of a plant’s reliability and asset management program. The goal of this analysis is to help plants compare current asset management practices with global best practices as well as average practices in their industry. This comparison is used to identify specific areas to improve the reliability and availability of plant assets in order to reduce operating costs.
The first step in this process is understanding where the plant is today and how it can manage assets more effectively to improve plant productivity and profitability. Since 2003, SKF has conducted more than 1,400 client analyses with customers across a wide range of industries, among them metals, cement, pulp and paper and mining, as well as food and beverage, material handling and wind energy. As a result, SKF has access to a rich database for use in assessing a plant’s performance compared to others in its industry.