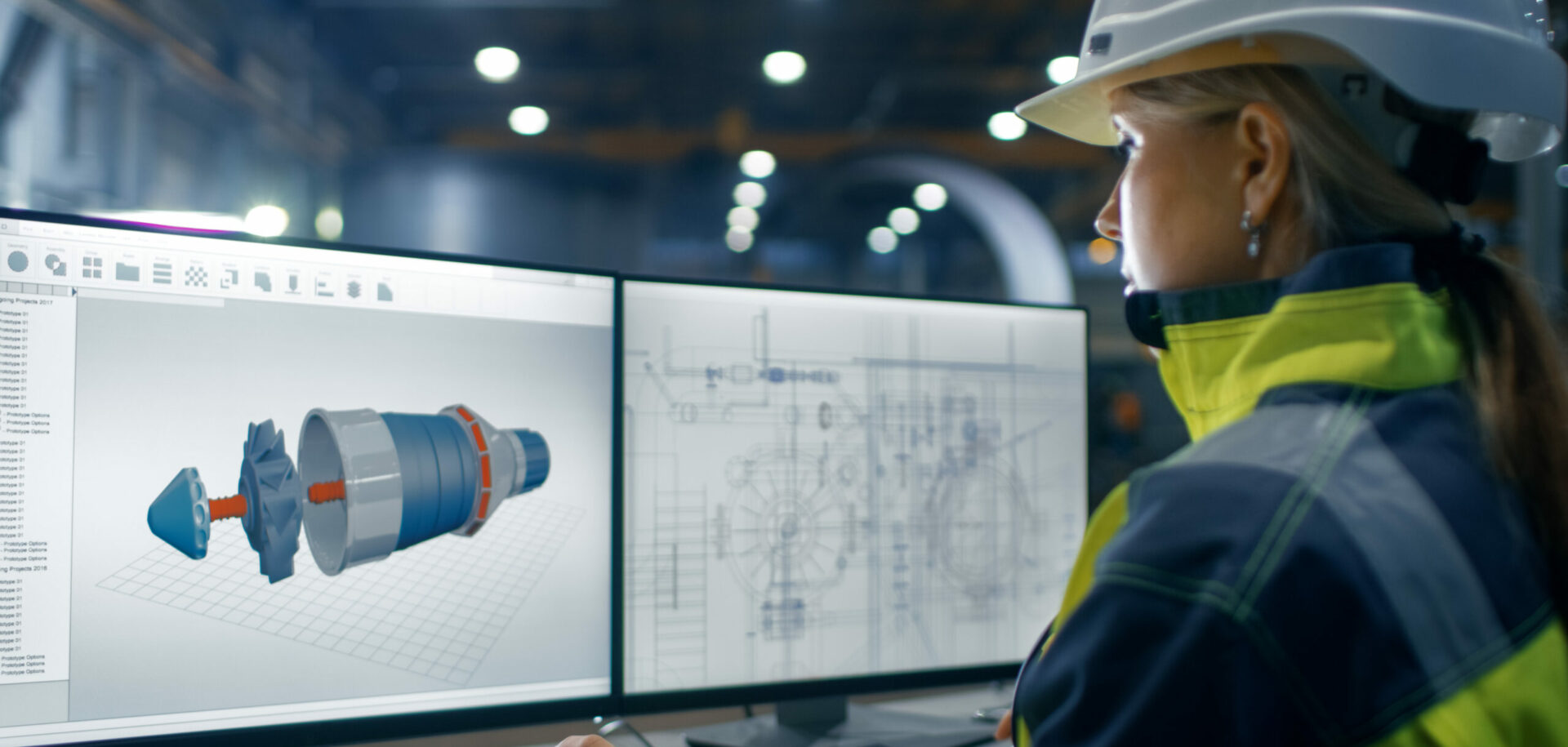
Testing standards set for railway bearings
Reliability is a key word in railways operation. One way of ensuring the long-term reliability of Europe”s network is through rigorous testing procedures. New standards are being negotiated to achieve this end.Rolling bearing designs, like railways themselves, have evolved gradually over the years. This has led to the situation where individual railway companies and rolling stock manufacturers have their own preferred specifications in addition to any national railway requirements. With the long-term aim of European unification in mind, new standards are being negotiated for railways operation. As a result, bearing testing has three new standards.
Reliability is a key word in railways operation. One way of ensuring the long-term reliability of Europe”s network is through rigorous testing procedures. New standards are being negotiated to achieve this end.Rolling bearing designs, like railways themselves, have evolved gradually over the years. This has led to the situation where individual railway companies and rolling stock manufacturers have their own preferred specifications in addition to any national railway requirements. With the long-term aim of European unification in mind, new standards are being negotiated for railways operation. As a result, bearing testing has three new standards.
The International Union of Railways, known as UIC (Union Internationale des Chemins de Fer), has played an important role in developing specifications for rolling stock operating along international networks in Europe, including axleboxes. There remains, however, much to be done to ensure full interoperability on European main-line networks.
In 1990, the Council of Ministers of the European Communities issued a directive that regulates public procurement contracts in the transport sector. Its aim is to remove any remaining barriers to open trade in the community. To achieve this, commonly established standards must exist so that they can be referred to by end users as part of tender documents. Such specifications should also be internationally recognised, if possible, by the European Committee for Standardisation, CEN.
The CEN is composed of national standards bodies from the member states. Its decisions are binding for them. As regards railway standardisation, CEN established Technical Committee, TC 256, in 1991. A sub-committee, SC2, deals with wheelsets and bogies while working group WG 12 specialises in the rolling bearings and lubricants. This working group involves specialists from railway companies and equipment suppliers, and here SKF has played a major role in the work.
New standards
The starting point for harmonising European railway standards has been the various existing standards used by individual countries, the specifications used by railway companies and the leaflets drawn up by the UIC for international use. From these, new sets of standards drafts were created and distributed via national standardisation bodies. Following a series of consultations, comments and remarks were received, and ultimately the working committee produced three standards. After public enquiry in 1996 and a number of amendments, final drafts have been submitted to CEN for formal voting, approval and publishing.
EN 12 080 Railway Applications – Axleboxes – Rolling Bearings defines the quality parameters of axlebox rolling bearings required for reliable operation of trains on European networks. It covers metallurgical and material properties as well as geometric and dimensional characteristics. It also defines methods for quality assurance and conditions for approval of products. This standard is aimed at establishing levels of product reliability; it is not aimed at standardising dimensions or basic load ratings.
The new standard relating to lubricating greases for railway axleboxes, EN 12 081, similarly defines quality parameters for greases. This standard covers approval procedures, quality control methods and quality monitoring of grease for two speed classes.
The third standard relates to performance testing of axleboxes. EN 12 082 describes the principles and methods for a rig performance test of assembled axleboxes with rolling bearings and lubricating greases. Test parameters and minimum performance requirements of axleboxes in operation on main lines are specified. Different test parameters and performance requirements may be selected for vehicles in operation on other networks. Basic principles for a field test are also proposed.
Performance test
This new standard EN 12 082 is a particularly important standard for bearing manufacturers, rolling stock manufacturers and railway operators alike. It provides details on principles, methods and equipment to test assembled axleboxes in test rigs along with criteria for acceptance. This standard describes two main types of testing, rig performance and field testing.
Rig testing
This test involves two axleboxes mounted on a test rig and subjected to repeated loading cycles that reflect accurately the service conditions of the intended application. For bearings, performance is gauged by monitoring the operating temperature throughout the test. The values of absolute and relative temperatures have to remain within certain limits. After the test, bearings and grease have to be examined and documented.
For railway vehicles with a speed limit up to 200 km/h, the test rig has to be run for an equivalent service distance of 600,000 km. Above this speed, the test distance is increased to 800,000 km. For less demanding conditions and for minor changes in proven designs, shorter distances are recommended. If particular conditions for similar rolling bearing, grease or axlebox housings are altered, a reduced test regime can be sufficient, as long as the overall performance is predictable and stable. Unless otherwise agreed, the cumulative distance covered in this case is 100,000 km.
Field testing
This type of test relates to railway vehicles covering a high annual mileage at maximum operating speeds and the highest possible axle loads. For main line vehicles with a speed limit up to 200 km/h, the rig and field tests should last the equivalent of two years, or 600,000 km. Above this speed, the distance is increased to 1 million km. The number of axleboxes tested must be agreed between customer and supplier.
The CEN standard EN 12 080 also provides guidelines to determine the extent of approval procedures of axlebox rolling bearings, if both rig and field testing have to be carried out.
EN 12 082 allows test parameters such as speed, radial and axial forces, air cooling and test cycles to be defined in such a way that test results achieved by different companies or institutes can be directly compared and mutually recognised. Approval certificates will be granted by government-appointed notified bodies to ensure consistency and credibility of this standard throughout Europe.
Testing capacity
The SKF R3 railway bearing test rig has evolved through considerable experience in evaluating railway bearing performance. The rig consists of a shaft with two support bearings which are mounted inboard. The axlebox bearings are mounted on both ends of the shaft. Actuators provide radial and axial forces. After a “running in” phase with speed increased in steps, the rig repeats identical cycles at maximum speed. Typically, such tests involve two hours of rotation in each direction, separated by a short stop. Fans directed at the axleboxes give a similar cooling effect as that experienced during actual operation.
Performance is monitored by measuring temperature in a minimum of three positions. Normally these measurements take place above the loaded zone of each bearing row in contact with the outer ring and the scanning zone of the infrared temperature scanners, known as hot box detectors, along the track.
Service simulation
Beyond the quasi static testing method already described, the behaviour of new bearing and axlebox designs has to be evaluated under realistic operating conditions. To this end, the SKF Engineering & Research Centre (ERC) at Nieuwegein in the Netherlands has developed a sophisticated test rig called THISBE (test rig for high speed bearings) which can simulate dynamic load conditions. Here the bearing and axlebox are fitted in part of an actual bogie frame, including the suspension system with springs and dampers. The rig is controlled by a computer using signals obtained by recording and analysing actual loads, acceleration and displacements on axleboxes in service. THISBE allows joint development of products that will help meet demands for ever-increasing speeds, carrying capacity and economy.
Today, ERC uses THISBE and an additional six R3 railway bearing test rigs that comply with the EN 12 082 standard. This is a significant resource when compared to railway testing facilities available elsewhere. This provides railway companies and OEM railway rolling stock suppliers with a full bearing package that is approved according to a universally accepted European standard.
Gottfried Kure,
SKF Österreich AG,
Steyr, Austria,
and John Skiller,
SKF Engineering & Research Centre (ERC),
Nieuwegein, The Netherlands