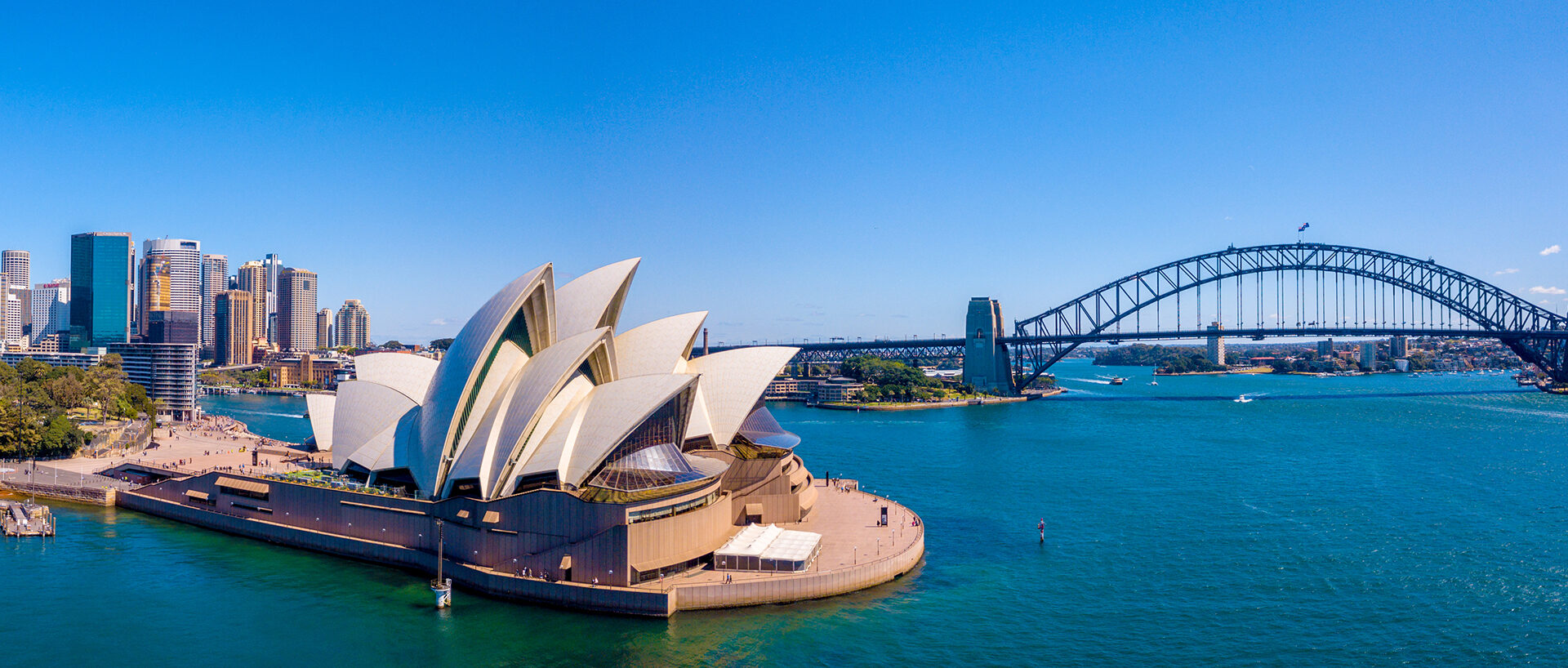
Testing towards more effective maintenance of Sydney’s railway
Responsible for maintaining the bulk of Sydney’s passenger rail fleet, engineering business Downer Rail & Transit Systems has recently been trialling two SKF condition-monitoring solutions with encouraging results.
The job of maintaining the bulk of the Sydney passenger rail rolling stock is undertaken by engineering business Downer Rail & Transit Systems, part of the 150-year-old Downer Group. Downer Rail & Transit Systems’ massive Auburn Maintenance Centre in the geographic heart of the city is used to service Waratah A-Set trains owned by Sydney Trains, as well as sets owned by other entities.
“We’re responsible for the maintenance of everything from the wheels, axleboxes, traction motors and bogies of the trains through to the carriage exterior and interior, the doors and the pantograph on the roof,” explains Frank Lukacevic, senior mechanical engineer, Downer.
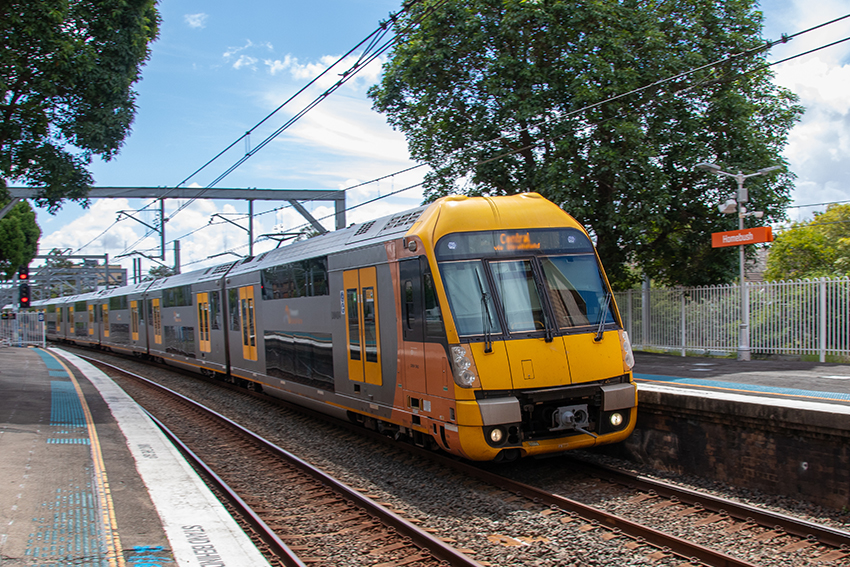
Time- and distance-based maintenance
Like most rail operations globally, Downer has traditionally structured its maintenance programmes around time- and distance-based models. Components in the trains are replaced once they approach the end of the lifespan recommended by the OEM. However, with passenger journeys trending upwards, both Downer and the owners of the rolling stock it services are looking for ways to boost uptime and availability.
With this in mind, Lukacevic and Christian Douglas, Downer’s asset strategy manager, have been tasked with finding new ways to reduce downtime and safely extend component use. The pair have been particularly interested in the potential benefits of condition-based monitoring. Could monitoring components in real time, they wondered, help reduce premature part replacement, safely lower costs and decrease maintenance needs?
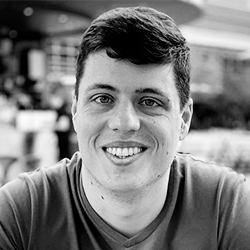
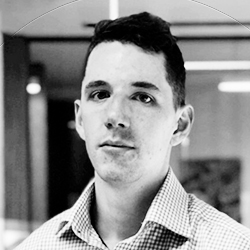
Downer.
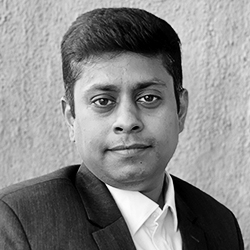
Trial of condition-monitoring systems
So, when SKF approached Downer in 2020 with two rail condition-monitoring systems that had been successfully deployed elsewhere in the world, they were naturally curious. They agreed to trial the technologies.
SKF Railway Business Development Manager Lokesh Jain explains that the first system, SKF Insight Rail, is a wireless, self-powered system for monitoring the condition of bearings in passenger rail bogies. Fitted to the axlebox, it gathers vibration and temperature data and uses a cellular data connection to send updates to a user interface.
SKF’s IMx Rail, meanwhile, is a more sophisticated, multi-channel system for the condition monitoring of a wide range of assets such as wheelset bearings, wheels, gearboxes and traction motors. Data is continuously uploaded to the SKF cloud and analysed in a remote diagnostics centre. Customers receive alerts from the diagnostics team and can view key data through an easy-to-use interface.
Under the Downer trial, IMx Rail was fitted to two bogies of a Sydney Waratah A-Series train. In addition to providing data on the eight bearings inside, it collected and relayed comprehensive information on the condition of the two traction motors and gearboxes.
SKF Insight Rail is a simpler system: 64 units were fitted across the axleboxes of an eight-car train to monitor each of the 64 wheel bearings. Another 32 units were fitted to monitor the wheel bearings in a separate four-car train.
Douglas explains that Downer hoped to achieve different goals with each system. While he and Lukacevic were interested in assessing Insight’s suitability as a potential fleet-wide condition-monitoring system, the pair hoped to use IMx Rail to gather baseline data about bogie components to be used in studies with research partners. In the longer term, such data may help make a case for introducing condition monitoring across the fleet.
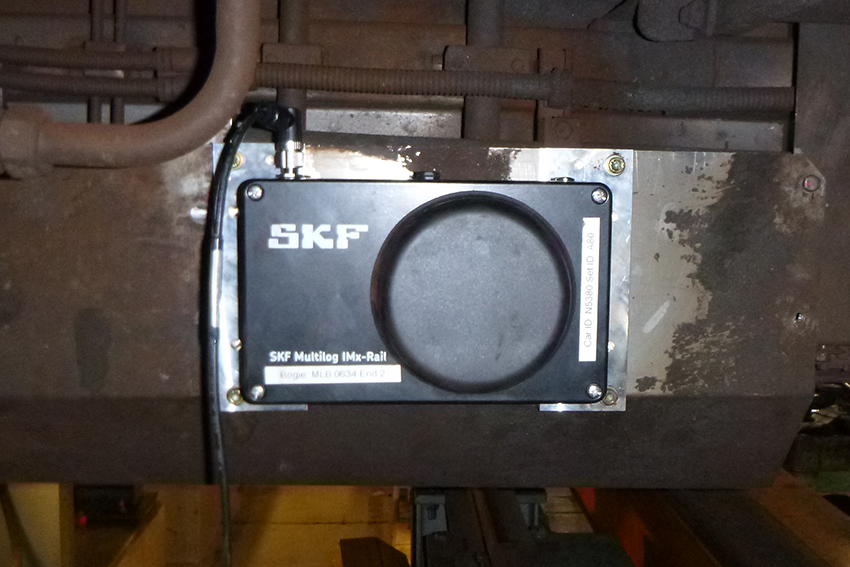
Wealth of data
After more than a year of trials, the two systems have delivered encouraging results. In particular, the Downer team has been extremely impressed with the quality of the data being delivered by the IMx system, which, they say, greatly broadened their knowledge of how components age and degrade.
“There are acoustic trackside systems in place to monitor wheel bearings, but we were previously blind to what was happening with the traction motors and gearbox,” says Lukacevic. “With IMx Rail, we have been able to change that and actually pick up on some gear mesh faults in our gearboxes. We have then been able to monitor how they have changed over time. If we learn that the fault is degrading very slowly over time, then we might gain the confidence to say in future that a gearbox can run for some time like this without action being taken.”
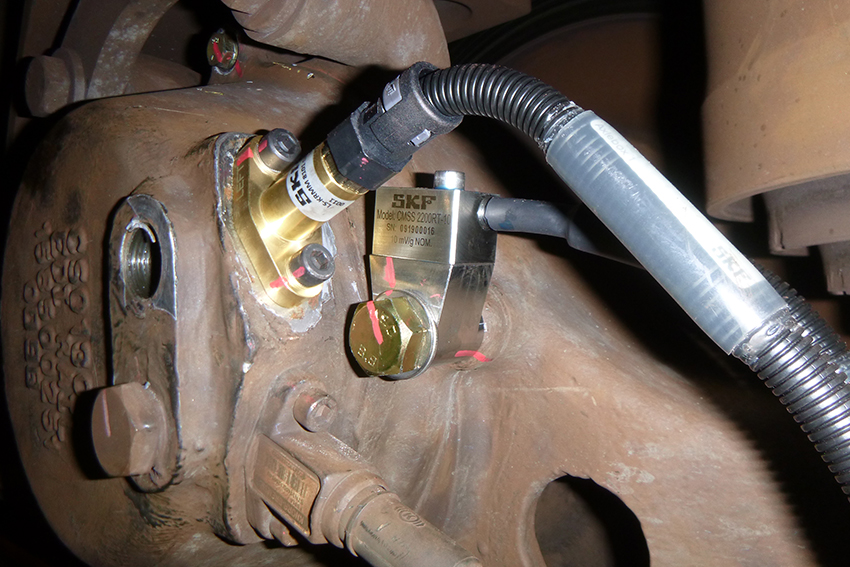
Track shock detection
As well as extremely high-quality data and analysis, another major benefit to Downer of IMx Rail has been the shock-detection capability. Because the system is continuously taking and transmitting data, it is able to identify locations where track damage may be present.
“Everywhere [the train] goes we can map the network and identify vibration hot spots, which is something we’ve never been able to do before,” says Douglas. “In turn, we are able to go to [the network operators] and tell them what we’d seen. It strengthens that relationship and is quite a value-add.”
We were previously blind to what was happening with the traction motors and gearbox.
Frank Lukacevic, senior mechanical engineer, Downer
Getting the most out of the Insight system on the Sydney network has initially been more challenging. The Downer team explains that the short distance between some network stations hasn’t always provided the system in its current configuration with sufficient opportunity to capture and send meaningful data. An enhanced configuration was applied to meet this particular challenge, but that solution reduced battery life.
SKF has listened to Downer’s challenges and continues to work closely with the company’s engineers to make modifications and tailor the system to local needs.
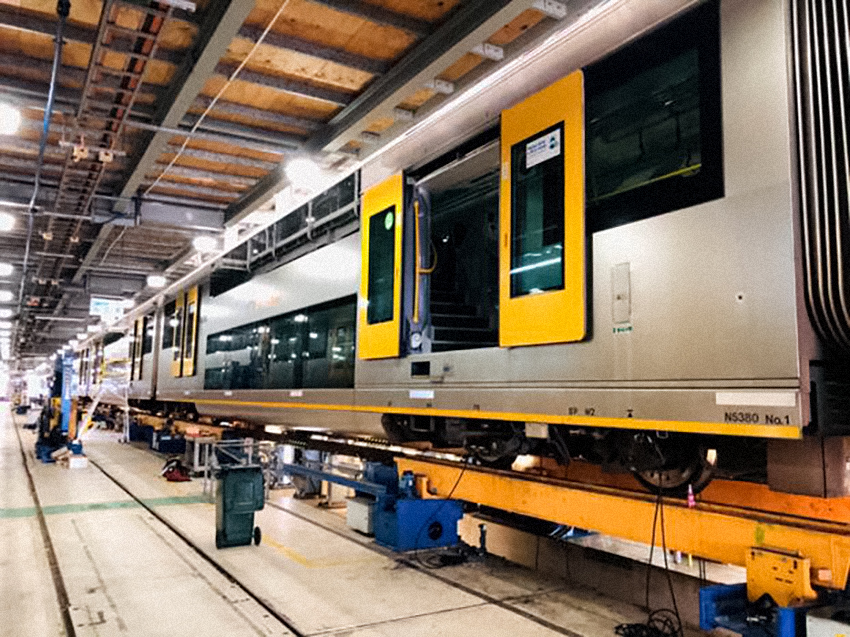
Early fault detection
Despite some initial teething challenges, there have also been encouraging success. For example, Insight successfully detected a wheel bearing fault nearly two weeks before it was detected by trackside sensors along the network.
Lukacevic says such early warning has the potential to be a powerful tool moving forward. “Being able to pick things up earlier gives us more time to plan in maintenance,” he says. “That in turn means we can do the work without impacting other activities or having sets parked up and not available for service.”
Downer is continuing to work closely with SKF in trialling the systems.
Bright future
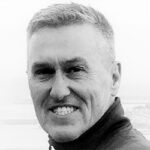
While it’s still early days on the journey, both Lukacevic and Douglas agree that condition monitoring is the future of passenger rail maintenance.
“Condition-based monitoring is the future because of the benefits in terms of efficiency and competitiveness,” says Douglas. “If you’re not needing to replace components as quickly, you’re using fewer resources and less electricity and saving money and time.”
Nigel Herbert, SKF business manager for rail for Queensland, New South Wales and New Zealand, says Downer deserves praise for investigating the potential of condition-based monitoring systems.
“The rail industry worldwide tends to be quite cautious, but systems such as SKF Insight and IMX Rail have been proven to greatly increase efficiency and lower costs for maintaining rail fleets,” he says. “Downer is helping to pioneer this technology in Australia, and we remain confident that they will enjoy the many benefits it has to offer.”
SKF Insight Rail
Read more about it here.
SKF IMx-Rail
SKF Multilog On-line System IMx-Rail is a multi-channel online condition-monitoring system designed to monitor railway assets such as wheelset bearings, wheels, gearboxes and traction motors. This solution enables instant status updates and 24/7 monitoring of rail fleets, with performance data relayed to the cloud via Wi-Fi, mobile or Ethernet connection. Data is made accessible via a user-friendly interface, and the system can also incorporate GPS data along with speed, vibration and temperature.
Read more about it here.