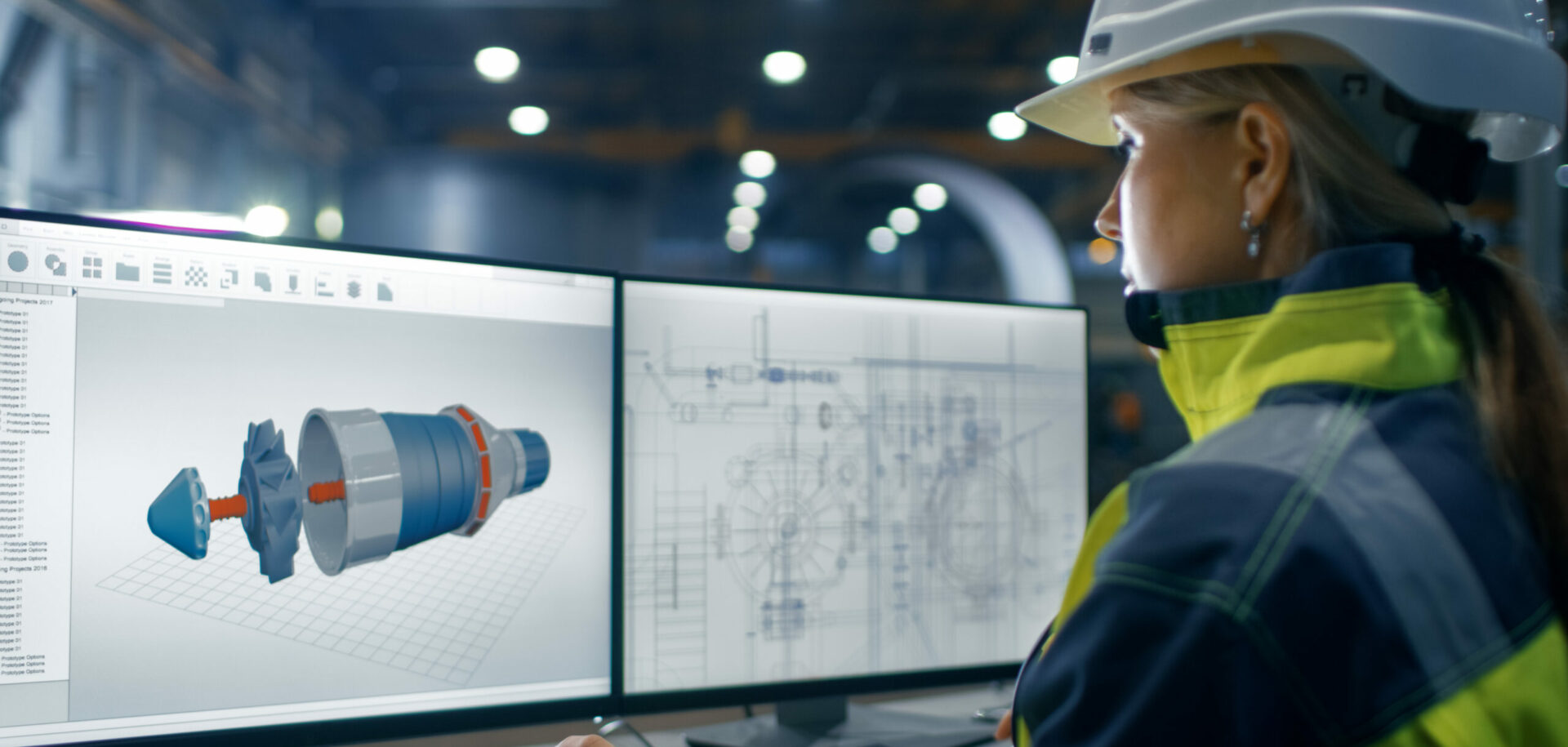
The clean skies of the future
The aviation industry accountsfor 2 percent of global carbon dioxide emissions, according to the International Air Transport Association (IATA). This makes it a small part of the major problem that is climate change.
Increasingly, the aviation industry is being pressured to reduce
its impact on the environment, and with the European Union contemplating a drastic cut in aircraft emissions, the time to make aircraft greener is now.
The aviation industry accountsfor 2 percent of global carbon dioxide emissions, according to the International Air Transport Association (IATA). This makes it a small part of the major problem that is climate change.
The long-term goal of a zero carbon dioxide-emissions aircraft is thought to be attainable within 50 years. But the industry faces more immediate challenges.
“All the projections say that the aviation industry will grow by 5 to 6 percent annually over the next few years, so the pressure is mainly coming from that front now,” says Jürgen Haacker, director of operations, Technical Activities, at IATA. “It’s good that the business is growing and that people have greater freedom to travel. But this brings a further challenge to the aviation industry to do even more than we have in the past.”
Improved airline operations and flight plans are one way to find greater efficiency, but aircraft technology is key. “We’re encouraging the manufacturers to do even more on the aircraft efficiency side,” says Haacker. “They are all working on increasing the share of fusel-age and wings made out of composites. Another elem-ent is the fuel efficiency of engines, which is certainly a very important factor. Our studies show that roughly two-thirds of the contribution to improved efficiency comes from the engine burning less fuel and one-third comes from making the plane itself as fuel-efficient as possible. Manufacturers tell us they think they can achieve between a 20 and 25 percent efficiency improvement for an aircraft in the timeframe of 2015 to 2020, with the expected replacement of the current short-haul range.”
In line with this effort, SKF has made development of energy-efficient aviation solutions a central plank of its strategy in the sector.
SKF Aerospace is actively developing greener solutions in several areas, notably engine bearings, composite rods and struts, bearings for the airframe, landing gear and ailerons, rudders, elevators, spoilers and mechatronics. If these SKF solutions were applied to all new long- and short-range commercial aeroplanes, the result would be estimated fuel savings of 200 million litres per year. This is equivalent to about 600,000 tonnes of CO2 emissions per year.
“Today all our major customers talk about the
environment and are trying to work on greener engines for the future,” says Frédéric Ponchon, director of the engine and gearbox sector at SKF Aerospace, a world leader in aero-engine bearings. “With each tender and in each specification there is a clause about making greener products. ‘Green’ is a commercial argument today, and we have a policy of sustainability and the objective of manufacturing more green solutions.”
“The environmental argument only appeared recently, but in fact it links up with a whole strategy that we’ve been developing at SKF Aerospace for several decades to reduce weight,” says Gilles Labouret, marketing manager, SKF Aerospace. “The lighter a plane is, the less fuel it uses, which means a reduction in pollution. So in fact it’s two birds with one stone.”
Engines are obviouslythe direct source of aircraft pollution, and making them burn leaner to reduce emissions is a primary goal. Bearing performance plays a key part in this. “We see today a willingness on the part of engine manufacturers to develop engines that are much more economic in terms of energy consumption,” says Ponchon. “We participate with all the engine makers on the definition of bearings for these new applications. I think that if each element can contribute a gain in power in an engine, by accumulating all these gains you can make a huge gain for the engine overall.”
New engine technologies are arriving to deliver this improved performance, such as the geared turbofan, a technology that is already on the test bench at Pratt & Whitney Canada. French engine maker Snecma is moving towards testing an engine using contrarotative turbofans. Instead of one fan at the engine intake, there are two fans linked mechanically and rotating in opposite directions to reduce turbulence and thus improve the engine’s performance. Open-rotor engines are also promising significant efficiency gains, if a solution can be found for their higher noise levels.
“We’re partnering with our customers on the defin-ition of bearings for these new engines, with specially adapted technology,” Ponchon says. “All the tests we will carry out in the coming five to seven years will define the optimal technology for an engine that will save around 30 percent in consumption.”
As part of this development, SKF Aerospace is study-ing the technology of hybrid bearings, which comprise steel rings and ceramic rolling elements. The advantage is that the bearing life is increased and power losses are reduced. “By using ceramic rolling elements, we can reduce the lubrication of the bearing and thus reduce the quantity of oil that needs to be fed to the engine, which means also a weight saving,” says Ponchon.
SKF is also developing bearings for main shafts, incorporating ceramics in tapered roller bearings that can withstand more radial stress than an equivalent all-steel bearing. These would be used in geared turbofan engines. Another engine-bearing technology SKF is developing involves cages made of composite materials. “Today bearing cages are made from steel or copper alloys that are silver-plated to optimize the coefficient of friction,” says Ponchon. ” It’s an electrolytic coating, and this manufacturing process is very polluting for the environment. We’re trying to find greener technologies in the manufacture of our parts.”
SKF is also playing a partin the maintenance process, where greener practices have been introduced. “When an engine is dismantled for an overhaul, the airline sends us back the bearings to be inspected and refurbished,” Ponchon explains. “Instead of throwing away the bearing – as was done in the past – we carry out a refurbishment, just as a mechanic might refurbish the brakes on your car. That too is part of protecting the environment.”
Apart from engine performance, SKF’s main focus in improving aeroplane efficiency is centred on weight reduction through its range of rods, bearings and mechatronics. “Where we can make a major difference is wherever there are large plain bearings – those found in the end of the flaps, for example, or in the undercarriage where there are parts weighing several kilograms that we have reduced by up to 60 percent in weight,” Labouret observes. “This is a massive gain for the plane as a whole.”
With Airbus, SKF has developed the concept of composite rods made of carbon fibre, using resin transfer moulding (RTM). “We obtain characteristics close to steel with a minimal weight,” says Labouret. “That is one of the major future paths of development, given that SKF is a leader in the market for composite rods.”
But composite rods are not cheap. SKF recently launched a new range of rods using a new production process called pultrusion. These rods have a very low cost – close to or even lower than metal rods – with the additional advantage of being light. “We now have a very complete range, which covers just about all needs, from very small rods that can withstand relatively heavy loads to large rods in composite RTM that can replace steel rods,” says Labouret.
Another major area for potential energy savings is electromechanical, or fly-by-wire, actuator systems. In terms of weight reduction, compared with hydraulic systems, these systems may add another 3 to 4 percent to fuel efficiency, says IATA’s Haacker.
“Fly-by-wire is a concept that was developed essentially by SKF, together with Airbus, but it’s becoming more widespread – in business jets from Dassault, and, also Boeing, which will install the systems in the future,” says Labouret. The main environmental argument is weight reduction, but there is also the significant fuel economy offered by the throttle-by-wire system.
Labouret says that the likelyintroduction of stricter European Union rules governing emissions has forced the issue of greener aircraft to the forefront. “When you look closely at CO2 production, aviation is responsible for about 2 percent of total emissions,” he says. “But what worries people is the rapid growth in air transport. It’s estimated that, six years from now, aviation will account for 6 percent of emissions. That poses a problem. The EU is talking about imposing a 50 percent reduction in emissions.” By current reckoning, roughly half of this reduction could come from the reorganization of airports, more direct air lanes and altered flight patterns; the other half would come from plane and engine design changes. “It’s the right time to position SKF in this field,” says Labouret.
Weight reduction on Airbus A380
SKF Aerospace has worked closely with its customers, for example with Airbus on its new 555-seater long-haul A380, the world’s largest passenger aircraft. The A380 design team worked on the principal that every 10 kilograms trimmed from the aircraft would save nearly half a litre of fuel per flight hour. SKF solutions from titanium bearings to composite rods and fly-by-wire actuator systems led to weight savings of nearly two tonnes, which translates to fuel savings of nearly 100 litres/hour for a long-range commercial aircraft.
SKF titanium bearings are used in the landing gear, engine support frame and ailerons. The landing gear alone led to a weight reduction of 110 kilograms per plane, plus another 90 kilograms from the frame and flaps. Taken together, this equates to nearly 10 litres per hour of flight in fuel savings. SKF composite rods meant a weight reduction of up to 40 percent, with a total saving of 111 kilograms throughout the plane, which equates to a saving of some five litres of fuel per hour.
The contribution from the fly-by-wire system is more significant. Compared with hydraulic systems, the SKF electromechanical actuators reduced weight by about 1,600 kilograms, resulting in a saving of more than 75 litres of fuel per hour of flight.
Throttle-by-wire
Manufacturers of business jets are continually looking for ways to enhance the value and performance of their aircraft for customers and to gain a competitive edge in the market. In this field, SKF has developed the “throttle-by-wire” system, an electromechanical throttle control lever governing engine power.
“The system is designed to optimize the control of engine power, and that generates a fuel economy,” says Gilles Labouret, marketing manager, SKF Aerospace. “The concept is that we optimize the aircraft’s power according to requirements, and this leads to a reduction of consumption in the region of 5 percent. If it was fitted to all business jets, it would add up to a relatively sizeable saving.”
The following is a projection of energy savings for business jets fitted with SKF throttle-by-wire (assuming global business jet population of 25,000 aircraft):
-
Fuel savings per flight hour per aircraft: 100 litres
-
Fuel savings per aircraft per year: 50,000 litres
-
Fuel savings per aircraft lifetime: 1 million litres
- Fuel savings per 25,000 aircraft per lifetime: 25,000 million litres.