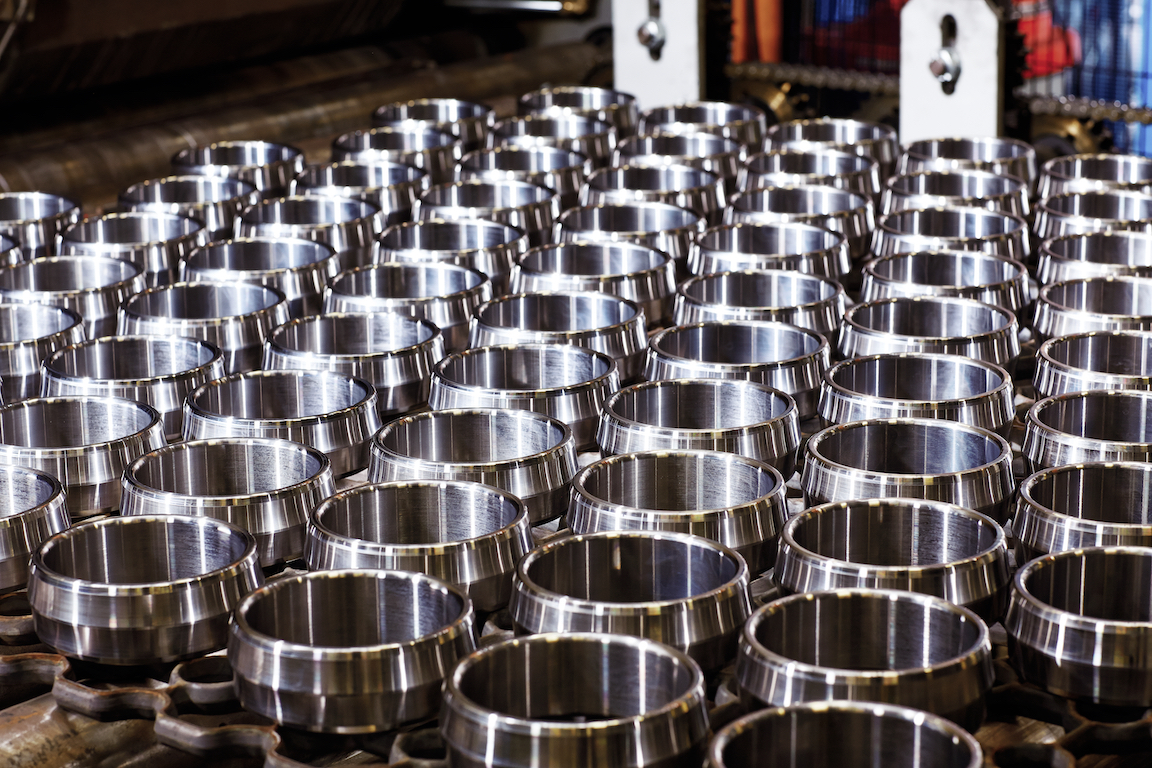
The fine print
In Gujarat, India, textile producers reduce both costs and environmental impact through energy-saving technologies.
At the Badra textile market in Ahmedabad, narrow, winding streets are lined with small shops and stands offering every imaginable fabric. Salespeople compete for the attention of women and girls in colourful, beautifully patterned saris; the shoppers point, select and bargain for new outfits. There is no better place to experience, with all your senses, the heart of Indian textile production. Gujarat produces the most cotton of any state in India, accounting for 30 percent of the country’s woven fabric. With 6 million inhabitants, Ahmedabad is its largest city, and as the centre of India’s industrial textile industry since the 1800s, it has been dubbed the “Manchester of the East”. With today’s growing concern about global warming – as well as India’s high energy costs – saving energy is a priority for textile mills. One pioneer in the development of energy-efficient technologies is Ahmedabad-based Indian Textile Engineers, a company that produces textile printing machines used by mills to print patterns on such products as saris and bed linens. “Our end users always ask us to reduce the energy needed, because it adds too much to the cost,” says Managing Director Niki Thakore. In typical textile printing machines, hydraulic cylinders are used to lift and lower the printing platforms that create a textile pattern. High energy consumption is not the only environmental downside to these systems: 400 litres of hydraulic oil per year per machine are used to run the two hydraulic actuators installed in each Indian Textile Engineers machine. A few years ago the company started to explore alternative solutions. Hydraulic systems require a constant power supply, even when the actuators are not performing their task, whereas electromechanical solutions only consume energy during movement. Electromechanical power transmissions do not require oil, eliminating its consumption and leakage on machines and mill floors. It also improves the working environment for machine operators through reduced noise and vibration levels. Together, SKF and Indian Textile Engineers explored a number of different actuator models. After extensive trials, they settled on the SKF CASM electromechanical cylinder, which can handle the heavy loads and high speeds required by a textile printing machine whilst also increasing production. Two electromechanical actuators were installed in a machine as a trial, and the observed reduction in energy use was significant, estimated to be 7 MWh per year (equalling 5.3 tonnes of CO2 emissions per year, according to world power grid mix CO2 factor of 0.749 kg CO2e/kWh). The next step was to test the solution at some customers’ operations. The energy savings amounted to approximately 120 euros per month per machine, and with about 5,000 machines running in the country, Indian Textile Engineers sees huge potential for energy and money savings. Moreover, one Ahmedabad mill increased its productivity from 600 to 850 metres per hour by changing to SKF CASM electromechanical cylinders. The successful installation of 17 actuators for Indian Textile Engineers has led to the ordering of another 300 SKF CASM electromechanical cylinders in 2012, to be installed in brand new printing machines as well as in machines already operating at various textile mills. The SKF CASM electromechanical cylinder is one of the first products to qualify for the SKF BeyondZero portfolio. Customer solutions included in the portfolio have significant environmental benefits that help customers improve their own environmental performance. The qualification requirements are extremely tough, involving customized investigations and board approval. “Foremost it has to have a really significant effect on the environment, and it cannot have any trade-offs,” says Mats Berglund, project leader for environmental research and development at SKF Group Manufacturing Development Centre. “That means that while we improve something in the life cycle of a product from cradle to grave, we may not make something else worse. For example, it cannot have a bigger impact on manufacturing.”
“The thought came into my mind to replace the hydraulic system with electromechanical actuators,” says Thakore. “And the company that came into my mind was SKF.”An SKF BeyondZero product