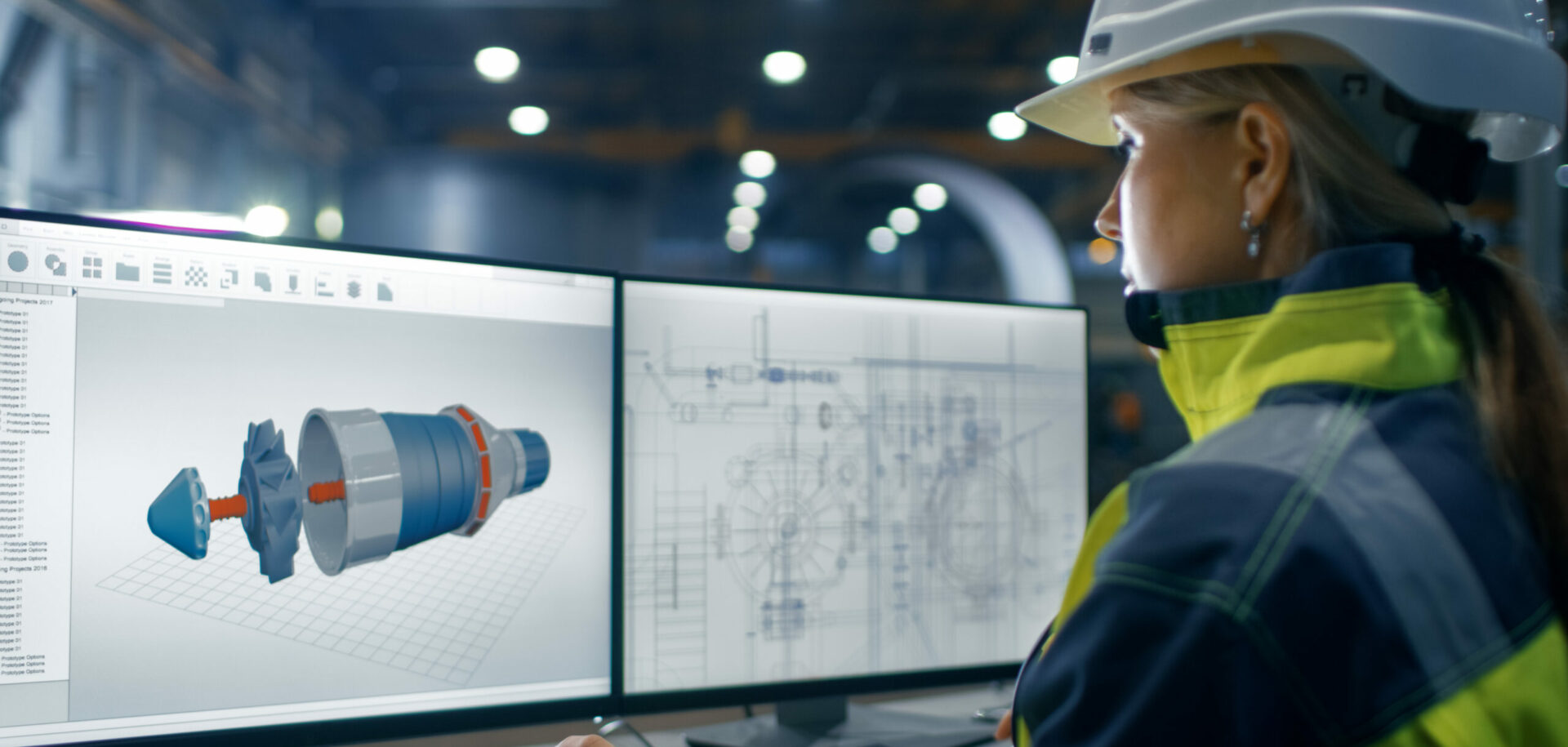
The great power
The only three companies in the world making wind turbines with a power output of around five megawatts are German, and REpower builds the biggest.
When the world’s biggest wind turbinewent on stream in the German coastal city of Brunsbüttel in early February 2005, the German minister for the environment just had to turn up. Jürgen Trittin described the REpower 5M as an important milestone. It showed, he said, that “the German wind power industry leads the world technologically.” And he added, “The future of wind power is out there at sea.”
Indeed it is, and the Brunsbüttel turbine is really only the first of a series of dry runs for the “wet” version of the 5M, that will be “out there at sea.” The first will probably be in 2006, 25 kilometres from the Scottish coast in 44 metres of water as part of the Talisman DOWNVInD project, supported by the European Union.
“In Germany,” says Bettina Linden, spokesperson for REpower, “we are forced to put wind power far out at sea.” Some people are sensitive to what they call the “asparagus-ation” of the landscape. So wind power needs to go where no one can see it. Linden puts it more generously: “There are several reasons for going out to sea,” she says, “some of them are good.”
Among the good reasons is that wind at sea is a much better power source than wind on land. Martin Skiba, until recently 5M project leader, says, “You get double the electricity from the same wind – the surface of the land puts a brake on the power source.”
One of the main problemswith the deep sea is that it’s so far away. REpower needs Brunsbüttel and a few more land-based sites where it can get at them easily, and run the turbines while optimizing them. But it’s not easy to get approval for wind turbines on land, especially not for five megawatt giants – each powerful enough to supply 4,500 households with electricity. REpower hopes that the jobs it provides throughout northern Germany will help convince local and state governments to look favourably on test sites.
Ursula Belker, mayor of the town of Husum, where REpower has one of its two main production facilities, was overjoyed in late February 2005 when the state interior ministry reversed its January objection to the installation of three 5Ms in a wind park next to REpower’s factory. The decision, she said, had saved 300 jobs: “That’s a reason to celebrate,” she said. “We need every one of those jobs, and that’s worth fighting for.”
The industry has learntfrom the errors of the first companies to go offshore, which tried to put up sea-proofed versions of their land-based turbines. Those first offshore turbines were also smaller than the current generation. However, the high costs of building foundations in 40 metres of water and connecting to the power grid means that the new generation of giant turbines is the only way of amortizing that high capital outlay.
New dimensions mean new materials. The first rotor blades were made of steel, and the current industry standard is glass-fibre-reinforced plastic, but REpower has had to reinforce the glass fibre with carbon fibre to give the 5M’s 126-metre-diameter three-blade rotors the extra length without the corresponding weight.
Designing windmills specifically for offshore-use demands new parameters, and maintenance and repair of these remote facilities will be difficult. The success of a company may be measured by how well it masters these problems.
“The main issue is to provide a high level of oper-ational availability,” says Skiba. “You can’t pop by on your way to the shops to change a fuse, so these turbines have to work reliably for months on end.”
The 5M has been conceived from the start for its inhospitable environment. Protection against corrosion caused by almost permanent salty wind is a main issue, but other less obvious aspects have also been taken into account. There’s partial redundancy in the design of many components. For example, as Skiba points out, “Whereas the rotor shaft on most wind turbines is supported by only one bearing – the other being in the gearbox – the shaft in the 5M has two: one locating and one non-locating.” This means that the gearbox bearings only have to carry torque loads.
The condition of critical componentsis continually monitored electronically, so that action can be taken on regular maintenance trips to put right faults that may be about to emerge. When the maintenance engineers do have to call, there’s a helicopter landing pad on the nacelle, and inside the nacelle, there’s a six-tonne crane that will enable the removal and replacement of 95 percent of the parts. Only the largest will require a jack-up platform with its own crane.
On land, the rotor often has to be removed and laid on the ground, so that the nacelle can be lowered. That’s not an optimal procedure on the high seas, and the 5M is designed in such a way that almost all repairs can be done inside the nacelle and replacements can be hoisted in and out through flaps.
REpower has pumped 12.5 million euros– about 15 percent of it from public funds – into the 5M, and it has set itself the challenge of making sure that its first turbines to be installed out at sea will provide the kind of reliability and return on investment the industry requires. The company has done its homework, but spokeswoman Bettina Linden says it can’t do it on its own. “We all have to pull together,” she says. “There are political decisions to be made about the infrastructure, about the cables under the sea, about how wind power can be integrated into the grid, and there are problems to be solved related to operation and service. But it’s clear that increasing wind power is the only way to meet global-warming targets.”
“We’re just at the start,” says Skiba. He compares wind power to the automobile industry. “We’re still very much at the stage where everything is done by hand,” he says. “Manufacturing could become more automated, and in 10 to 15 years, we could be the cheap element in the energy mix.”
REpower may still be making the 5M largely by hand, but the unit’s high power output and its reliability targets have made it a major step towards increased efficiency in wind power generation
A record-sized bearing
SKF supplies the bearings for the 5M’s huge rotor, which, with a weight of more than 100 tonnes, puts enormous loads on the rotor shaft. A CARB® toroidal roller bearing is fitted in the non-locating position – the largest ever produced, with an inside diameter of 1,500 mm and weighing 2,700 kg – while a spherical roller bearing is fitted in the locating position. The extraordinary size of the rotor unit meant that SKF had to design a new induction heater to heat the bearings and the 8,000 kg housings prior to assembly. SKF also designed and supplied special split nuts (also the largest ones ever) that facilitate assembly and disassembly. And SKF provides the WindCon online remote monitoring system for the coming units to keep an eye on a number of important parameters. (See article in Evolution 1.2005)