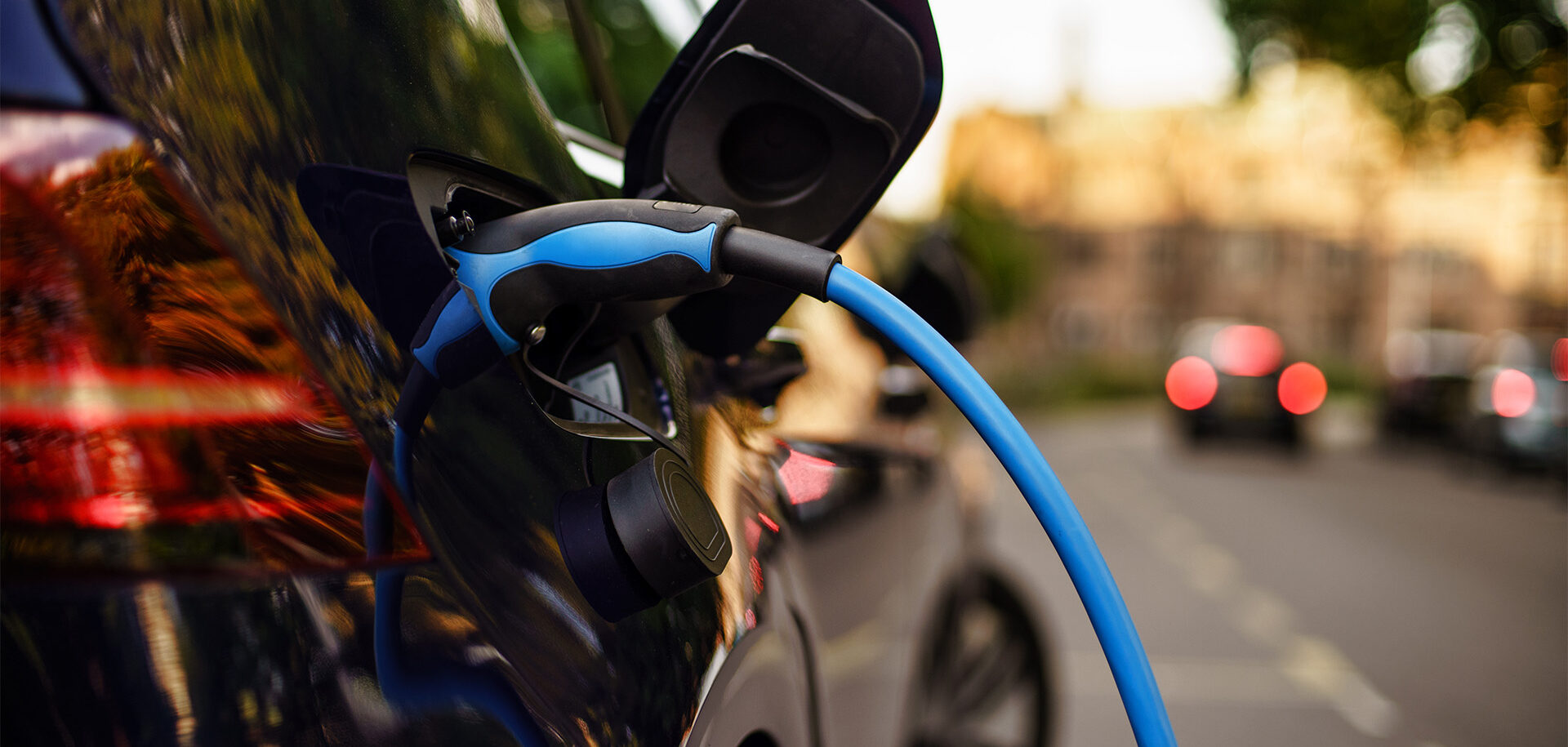
Understanding and Mitigating Electric Discharge Damage in Electric Vehicle Motor Bearings
Fundamental study reveals strategies for diminishing electric erosion damage in EV motor bearings.
Single ball-on-disc contact study sheds new light on electric discharge behaviour
The primary objective of this research is to investigate and comprehend the electric discharge behaviour in electric vehicle (EV) motor bearings by focusing on the study of a single ball-on-disc contact under elastohydrodynamic lubrication (EHL) conditions. By narrowing the scope to a single contact point, the research seeks to isolate and analyze the fundamental factors influencing electric discharge behaviour, providing valuable insights into the intricate dynamics that contribute to electric erosion in EV motor bearings.
Compared to a full bearing test, a single ball-on-disc rig provides enhanced control over electric and lubrication conditions. Adopting a commercial mini-traction machine (MTM) from PCS instruments (fig. 1), initially designed for measuring lubricated and unlubricated contact friction, allows for precise experimentation. To simulate electric discharge in EV motor bearings, the MTM rig is modified with a self-designed pulse drive unit (PDU) (Figure 1). The PDU introduces variable-frequency, amplitude-adjustable electric pulses, closely resembling real EV application conditions. Real-world EV motor conditions, featuring high-frequency alternating current/voltage (AC) exceeding 10 kHz, are replicated with a PDU-generated voltage at 12.5 kHz.
Key Findings
1) Typical discharge signal
Fig. 2 depicts an electric signal obtained from an MTM test. The red line represents input voltage from the PDU, while the black line shows the response voltage of the ball-on-disc contact. Despite using smooth surfaces in the test, the electric performance of the ball-on-disc contact is variable. At moments a and c, the ball-on-disc voltage mimics the input, meaning the contact acting as a capacitor. However, at times b, the output follows the input initially but drops to zero before the input pulse concludes, indicating typical electric discharge behaviour in EV motor bearings.
Fig. 3 displays electric discharge damage on the ball surface observed in an MTM test using optical and scanning electron microscopy (SEM). Two symmetrical damage bands in the contact area (figs. 3(a) and 3(b)) suggest that discharges primarily occur there. The contact area is divided into three areas (fig. 3(b)), with significant surface damage (numerous overlapping electric discharge craters) in Areas 1 and 3, resembling the surface damage on returned bearings from application fields. In contrast, Area 2 exhibits minimal damage with only a few isolated craters. The disc surfaces exhibit a similar distribution of craters as the balls.
Upon comparing the damaged surfaces with the calculated distribution of film thickness, it is evident that the two damage bands align precisely with the area of minimum film thickness, as depicted in figs. 3(b) and 3(c). The reason is that the crucial determinant in the initiation of electric discharge was identified as the electric field strength. The minimum film thickness area has the maximum electric field, strength and consequently, discharge consistently manifested in regions characterized by minimum film thickness, hmin.
Inspired by the craters distribution, an electric discharge energy model (equation (1)) was developed,
where a1, a2 and a3 are constants, and they depend on the capacitance of the test rig, the electric parameters of the lubricant and working conditions (load, speed, etc.). More details about this model can be referred to in [9]. Clearly, this model establishes a direct correlation between discharge energy and film thickness. As per equation (1), decreasing hmin can mitigate discharge damage on the disc and ball surfaces.
4) Modulating electric discharge damage through film thickness
Based on the electric discharge energy model, the extent of electric discharge (ED) damage in EHL single contacts can be modulated by controlling the film thickness. Therefore, a series of experiments were conducted, and it was found that decreasing the value of the minimum film thickness proves to be an effective strategy in reducing electric discharge damage.
Fig. 4 reveals the outcomes of surface analysis, illustrating a gradual reduction in electric discharge damage as the decrease of minimum film thickness hmin. These observations are in line with the model predicted trend. In tests where all conditions are identical except for lubricant viscosity, the single discharge energies are solely influenced by the respective hmin values. Test 23, with the highest hmin values, exhibits the greatest discharge energy, resulting in severe damage on the disc surface (as observed in fig. 4(a)). In contrast, tests 24 and 25, with much smaller hmin values, show no clearly visible craters on the sample surfaces (as depicted in fig. 4(e–f)). Test 27, with higher hmin values than test 24, displays visible craters due to a relatively higher discharge energy (fig. 4(d)). However, test 27 exhibits lower hmin values than tests 26 and 32, resulting in larger, more overlapping craters on the contact surfaces in these two tests, as depicted in figs. 4(b) and 4(c).
Optimum film thickness crucial for minimizing both electric and mechanical bearing damage
The experimental findings reveal that discharge behaviour in EHL contacts varies with film thickness, aligning with earlier work [8] indicating that a thicker lubricant film leads to a higher breakdown voltage. Traditionally, breakdown voltage was used to compare electric breakdown resistance of bearings, but this study shows electric breakdown is influenced by film thickness and lubricant dielectric strength. Considering film thickness, dielectric strength and breakdown voltage together is crucial when predicting electric discharge behaviour in EV motor bearings. The current model and test results show that by reducing the minimum film thickness the electric damage in bearings can be reduced due to a decrease of individual discharge energy.
However, it should be noted that excessive reduction in film thickness can result in mechanical damage, for example wear, posing a significant challenge to optimal bearing performance. This underscores the critical need for further research to precisely determine the ideal film thickness range, striking a delicate balance between mitigating electric damage and preventing harmful mechanical damage. Moreover, the choice of a suitable lubricant is pivotal in navigating this delicate equilibrium. A thorough examination of lubricant properties and compatibility with operational conditions is essential. Such research can lead to strategies that not only minimize electric damage but also effectively protect against mechanical damage on bearing surfaces. Hence, comprehensive research in this direction is vital for a nuanced understanding of the interplay between film thickness, lubricant selection and overall bearing performance.
Conclusion
This study investigates the intricate dynamics of electric discharge behaviour within electric vehicle (EV) motor bearings, utilizing a self-improved mini-traction machine (MTM) test rig. The examination of damages resulting from electric discharges led to the formulation and validation of an electric discharge energy model. The key conclusions of this research are summarized as follows:
- The modified MTM test rig effectively replicates the electric discharge phenomenon observed in single ball-on-disc contacts under elastohydrodynamic lubrication (EHL) conditions.
- The initiation of electric discharge predominantly hinges on the electric field strength, consistently manifesting in the region of minimum film thickness.
- A model for electric discharge energy, as delineated by equation (1), has been developed to elucidate the influence of lubrication conditions on discharge behaviour.
- The magnitude of electric discharge (ED) damage in EHL single contacts can be regulated by manipulating the film thickness. A reduction in the minimum film thickness diminishes the damage arising from electric discharge.
These findings contribute significantly to the comprehension of electric discharge behaviour in EV motor bearings and provide valuable insights into strategies for mitigating ED damage through the manipulation of film thickness. The implications extend beyond academic realms, offering practical guidelines for engineers and researchers engaged in advancing the reliability and durability of electric vehicle technologies.