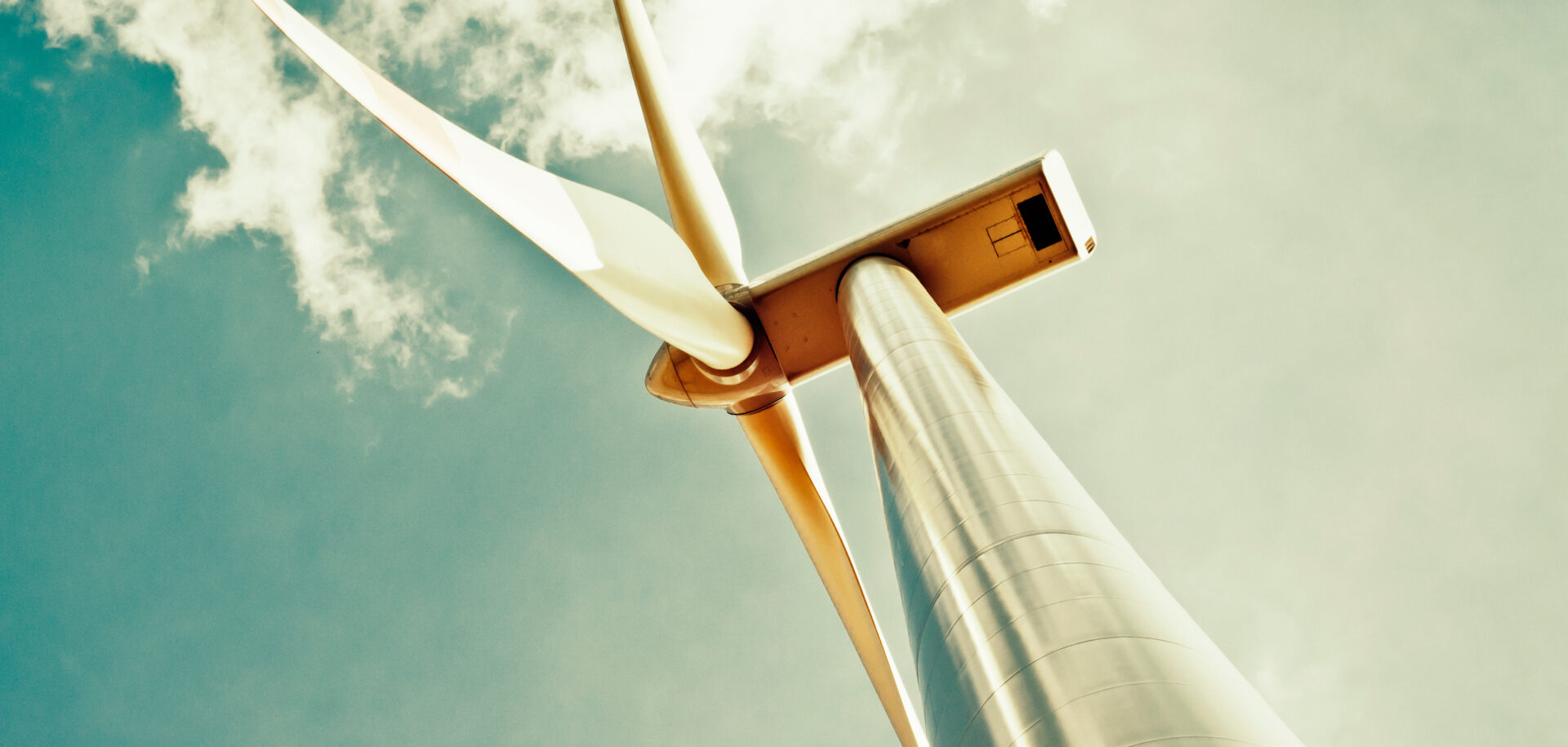
Up in the air or deep in the sea, lubrication is key
Optimum lubrication is a key factor when it comes to reliable operation of power turbines. Applications in harsh environments such as wind turbines and tidal devices require intelligent lubrication-management solutions to optimize the outcome.
Summary
Lubrication systems for wind turbines
Wind energy has long since cast off its status as a niche risk sector that gathers visionaries. Today, wind energy provides 14 % of the European energy mix [1], which means that it ranks directly after gas, coal and water. The wind energy sector has some 600,000 employees worldwide [2] and can now be characterized by highly developed technologies and continually improved processes, standards and norms. It is impossible to imagine today’s industrial landscape without wind energy.
Wind turbines have undergone continual development over the years, including a spectacular increase in size. In 1990, rotor diameter was only 23 m; in 2014 it had already reached 99 m. This size increase and the associated regulations and new demands pose challenges to component manufacturers.
SKF automatic lubrication systems have been accompanying the wind energy industry since its beginnings. For more than 20 years, single-line and progressive lubrication systems have been used all over the world by renowned OEMs (fig. 1).
With the increasing size of wind turbines and the advances in technology, lubrication systems are state-of-the-art parts of the yaw bearing and open gear, rotor blade bearings and their open gear, main shaft and generator bearings (fig. 2).
With a precisely applied quantity of lubricant in the right place and at the right time, one can achieve operative advantages, but that’s not all: Service intervals can also be extended and wind turbine availability is increased. The risk of accidents is minimized, over-lubrication is prevented, and unplanned downtime is reduced. All these factors make the SKF Lubrication Portfolio an established technology and an attractive upgrade. But it is not exclusively for the OEM sector. Retrofitting with automatic lubrication systems has long been practised in the aftermarket. SKF Lubrication Upgrade Kits are available for this purpose (fig. 3). The kits extend the customer-specific solutions in the OEM sector, providing easily installed plug-and-play solutions. Along with the pump, the kits include all the connection elements and accessories. A wide range of kits provides the utmost flexibility for the relevant applications and number of lubrication points.
Given the easier handling of such systems, the aftermarket mainly uses SKF ProFlex (fig. 4a), which is a progressive lubrication system.
This differs from the SKF MonoFlex system (fig. 4b) in construction and in the way it operates.
With a progressive system, the lubricant is continually dispensed from the pump to the lubrication point through a main line and sometimes through a secondary one. The cycle of a progressive system lasts until all pistons in the metering device have caused lubricant to be dispensed.
If grease is contaminated or incorrectly filled, this could result in a problem; the grease cannot be sucked in or it blocks the sensitive pistons in the progressive metering devices. In a monitored system, this triggers a fault notification.
The feedback signals of a monitored system are extremely important in today’s industry. The market demands intelligent upgrade options that minimize operating costs and increase wind turbine life. For SKF Lubrication, a focus of new developments is on independent monitoring and control systems. With the SKF Lubrication Remote Monitor (fig. 5), it is possible to monitor retrofitted lubrication systems for low lubricant and system fault notifications. If the grease reservoir is empty or there is a fault in the lubrication system (e.g., a blockage in the metering devices), status notifications are sent by SMS to one or more mobile phones. The maintenance team is immediately notified and countermeasures can then be taken. The SKF Lubrication Remote Monitor is easy to use due to its pre-installed software and pre-configured components. It is easy to add or delete service numbers and set up additional lubrication cycles using an SMS instruction. With the combination of this device and the pump, SKF Lubrication offers a cost-effective solution for monitoring lubrication systems in the onshore retrofitting market.
With its installed total capacity having reached 11 GW in Europe in 2015 (fig. 6) [3], the offshore wind sector continues to have huge growth potential. The United Kingdom (GB) offers the best preconditions, as demonstrated by the installed total capacity of more than 5 GW [4].
The locations of wind turbines and the harsh conditions at sea mean that the cost of offshore energy comes under continual close scrutiny. This is due in part to the required C5M standard (or sometimes “C5M – high”; see ISO 12944), which component manufacturers must comply with. This corrosion protection category requires a resistance period of more than 15 years in coastal and offshore areas exposed to high salinity levels. SKF Lubrication uses a process of electroless nickel plating, allowing the company to offer a cost-effective alternative to more expensive stainless steel components.
In the electroless nickel plating process, components are dipped into special solutions that create a layer of uniform thickness on, for example, the progressive metering devices. The nickel coating makes the component resistant to air, water, acids and alkalines. At SKF Lubrication, metering devices, connection elements, fittings, pumping elements and pump housings all undergo this process. To confirm the C5M corrosion protection class, they are subjected to a 1,440-hour salt spray mist test that is then reviewed and documented.
The lubrication systems are mostly SKF MonoFlex (single-line) systems. The components of a single-line system are shown in fig. 7.
A single-line system is a cyclically operating system (compare with figs. 4a and 4b). This means that the lubricant is dispensed from the pump to the single-line injectors using only one main line. Every lubrication point is equipped with an injector, which, under pump pressure, dispenses lubricant to the lubrication point. Unlike in the lubricant dispensing sequence in progressive systems, in a single-line system the injectors are arranged in parallel. An advantage of this is that if one of the lubrication points is blocked, the remaining injectors can continue to dispense grease. In offshore turbines, this technology has proven itself: It has enabled higher levels of turbine availability. The pump continues to dispense the lubricant into the main line until a pre-configured pressure is reached in the pressure switch. The pressure switch built into the pump is activated and turns off the pump. In larger systems, the pressure can be monitored by an additional pressure switch at the end of the longest line. At the end of the lubrication cycle, the pump is switched off and the main line is relieved by means of a valve built into the pump. Blockages of individual lubrication points or one or multiple injector failures do not impact the function of the rest of the system. This means that all other injectors will continue dispensing grease to the lubrication points. Given the pressure release between lubrication cycles, a single-line system can also be used to dispense rapidly separating lubricants.
Lubrication systems for tidal turbines
With its many years of experience in offshore wind and the marine industry, SKF Lubrication has emerged as a competent focal point in the new industry of tidal power plants (fig. 8).
The elements in a tidal turbine that need to be lubricated behave similarly to those in a wind turbine. The lubrication needs, however, are far more challenging and must be suitably adapted to the environment:
- Long maintenance intervals of up to six years require large grease reservoirs. It is not unusual for reservoirs to contain 20 kg or more of grease, because the turbines are extremely difficult to access and maintenance work is very costly.
- Automatic refill concepts need to make sure that the pumps do not run empty. In the design process, additional filling pumps are therefore planned.
- The use of redundant systems doubles the security of the grease supply. If a central lubrication device fails, the redundant second pump takes over to provide the fresh grease supply.
- The waste grease comes out over the outlet holes in the bearing and must somehow be collected. SKF Lubrication offers suction elements that can proactively suck out the grease in front of the outlets. The grease goes to one centrally installed waste grease container. This simplifies the maintenance work because it avoids the need for separately installed grease bottles on every outlet.
- All the components must comply with corrosion protection category C5M (see above).
SKF Lubrication has already equipped the first tidal turbines to produce MW capacity power in the UK. It is only a matter of time before these can start making a commercial contribution to the energy mix.