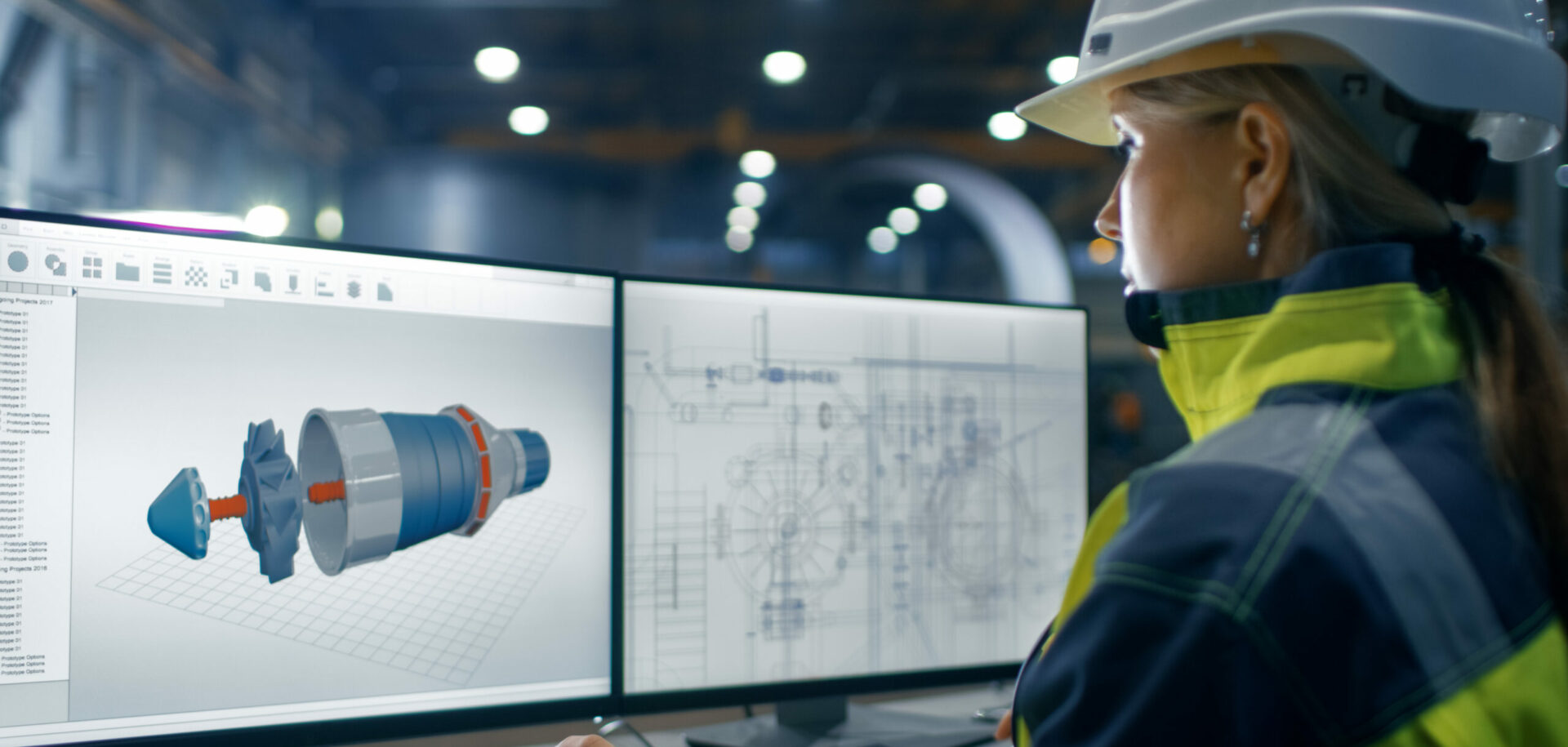
Vertical power
Tianjin Shiming Powder Technique Equipment Co. Ltd. is on the cutting edge of the cement industry in China in terms of the promotion of vertical roller mills in cement production.
Summary
The Tianjin Shiming Powder Technique Equipment Co. Ltd., established in 2003, is a leading company in the design of vertical roller mills in China, and its products are used widely in cement, steel, power generation and metallurgical plants. It has 50 employees and achieved a production value of 800 million renminbi (78 million euros) in the first 10 months of 2009. The company is a
subsidiary of Tianjin Cement Industry Design & Research Institute Co. Ltd. (TCDRI), a pion-eer that has been leading the evolution of cement production technology in China since it was established in 1953. TCDRI is now a subsidiary of the China National Materials Group Corporation Ltd., a state-owned company, directly under the administration of China’s central government.
Tianjin Shiming Powder Technique Equipment Co. Ltd. is on the cutting edge of the cement industry in China in terms of the promotion of vertical roller mills in cement production.
Liu Zhen, general manager of Tianjin Shiming Powder Technique Equipment Co. Ltd., is just back from a trip to China’s Shaanxi Province, northwest of Shanghai, and he is pleased. He has just negotiated an agreement with a cement company there, to provide four vertical roller mills for clinker grinding. The customer plans to build two cement production lines, each with a capacity to produce 5,000 tonnes of cement a day.
“The vertical roller mill for clinker grinding is a key product for us,” says Liu. “And the agreement in Shaanxi is our second for this product. We’ve already signed a contract with a Taiwan company to provide three vertical roller mills for clinker grinding.”
Established in 2003,the Tianjin-based company is a subsidiary of Tianjin Cement Industry Design & Research Institute Co. Ltd. (TCDRI) and is mainly responsible for research and development, marketing and after-sales services for vertical roller mills.
“Our products are manufactured in the TCDRI production facilities in east China’s Jiangsu and Shandong Provinces,” Liu explains.
The adoption of vertical roller mills has won great acclaim in China over the past three decades for its contribution to saving energy. Statistics show that the use of vertical roller mills can cut electricity consumption by more than 30 percent over traditional ball mills. In addition, vertical roller mills occupy less floor space than ball mills.
The quality of the cement produced by both machines is almost the same, although vertical roller mills have a less complicated structure and higher efficiency, and require less maintenance.
“China’s cement industry has a common goal, namely to eliminate ball mills in the entire production process,” Liu says.
So far, vertical roller millshave been used widely in raw material grinding. The final step in achieving this goal is to use them to grind the clinker into the end product. “This is why we are sparing no effort to introduce the clinker vertical roller mill,” Liu adds.
As a veteran in the research and development of vertical roller mills, Liu started working for the TCDRI in 1982 and has witnessed the development of domestically made vertical roller mills. The company produced its first domestic product in the early 1990s.
“Our first vertical roller mill for raw material grinding was put into service in 1993, and it is still running soundly,” he says.
The TCDRI establishedthe Tianjin Shiming Powder Technique Equipment Co. Ltd. to further strengthen the development of domestically produced vertical roller mills. In the past six years the company has sold some 160 machines.
In 2007, the company’s vertical roller mill for grinding raw materials for 5,000-tonnes-per-day lines, the largest domestically produced machine of its kind in the country, was put into operation at a cement company in north China’s Liaoning Province. The product marked an end to China’s dependence on importing large-capacity vertical roller mills. “Before that, China’s homemade machines could only cope with a capacity of around 3,500 tonnes per day,” Liu says.
For Liu and his colleagues, the economic recession that hit in late 2008 has had almost no impact on business, in part because China has invested 4,000 billion renminbi (389 billion euros) in large-scale infrastructure.
“In 2008, we sold 30 vertical roller mills with a production value surpassing 500 million renminbi [49 million euros],” Liu says. “By mid-October 2009, more than 50 had been sold and our production value had reached 800 million renminbi [78 million euros].”
But Liu says he feels a certain pressure when it comes to future development. China’s central government recently issued a notice to tighten the capacity of certain sectors, including cement production. “This will have an impact on the whole market,” Liu says, “but it’s also an impetus to develop innovative energy-saving technology.”
And Liu has confidencein his machines. “Only two companies in China can carry out strict grinding ability tests on raw materials for the customer,” Liu says, “and we are one of them.
“Raw materials for cement can differ according to the location, so this testing is crucial,” he explains. “Based on the data we collect from the test, we can conse bild ure the equipment properly to help the customer maximize efficiency.”
In the future, Liu will press ahead with the promotion of vertical clinker grinding machines. “In the long term,” he says, “we will develop more vertical roller mills according to market needs.”
Improved sealing solution tightens partnership
SKF provides bearings and seals to Tianjin Shiming Powder Technique Equipment Co. Ltd. “The grinding rollers need high-quality bearings and a good sealing solution,” explains David Jiang, manager of the seals platform at SKF China.
Since the operating conditions during the grinding process are extremely dusty and abrasive, the sealing system to protect the bearings is crucial.
“It has been a headache for the cement industry for a long time, as vertical roller mill users have to change the bearings on an average of every eight months, although the calculated bearing life is much longer,” Jiang says. “This is proof that contamination by dust has a great impact on the bearing service life.”
Changing the bearings in a roller that weighs many tonnes is time- and energy-consuming, and the frequent downtime causes an important loss of production and affects the efficiency of cement companies.
SKF’s latest achievement in sealing systems provides the key to the problem. To prevent premature bearing failure as a result of dust
contamination, SKF has developed a new sealing solution featuring an auxiliary PTFE excluder lip, which has been proved to provide extra protection against dust and other contaminants, extending bearing service life in the grinding wheels of vertical roller mills up to 24 months.
“The Tianjin Shiming Powder Technique Equipment Co. Ltd. has adopted this solution in one of its clinker grinding machines that was put into pilot use by the company in late January 2009,” Jiang says. “We have received no calls thus far. Sometimes, no news is good news.”