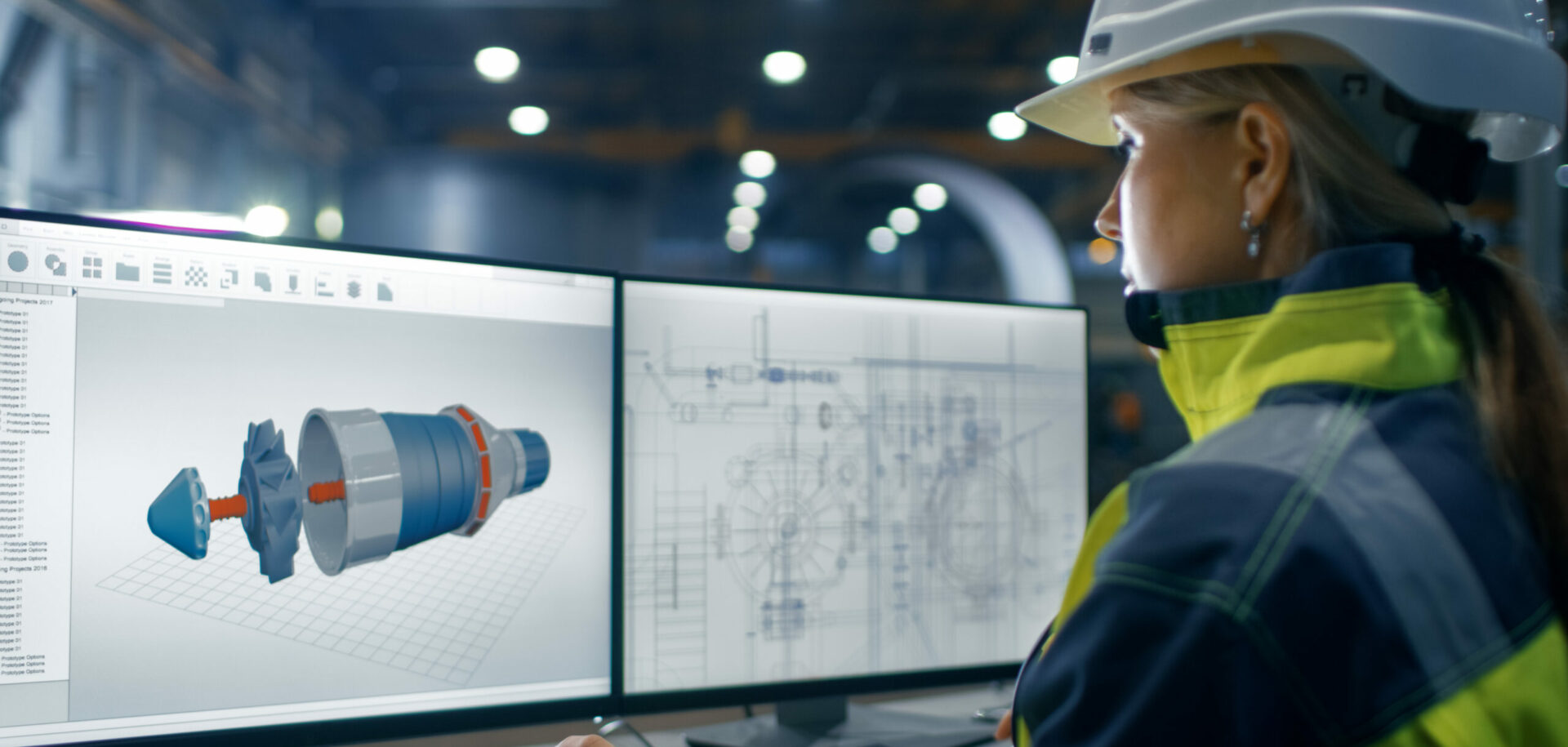
Where measurement and quality find a home
As a major engineering company, SKF relies on making sure that the products and services it provides live up to its own high expectations. Measurement and quality-assurance systems provide the SKF Group with the means to do just that. The SKF Group has its own dedicated Quality Technology Centre (QTC) that is now offering its expertise to other companies worldwide.
As a major engineering company, SKF relies on making sure that the products and services it provides live up to its own high expectations. Measurement and quality-assurance systems provide the SKF Group with the means to do just that. The SKF Group has its own dedicated Quality Technology Centre (QTC) that is now offering its expertise to other companies worldwide.
Based in Steyr, Austria,the Quality Technology Centre (QTC) is a fully integrated member of SKF. It was founded in 1983 to develop and supply instrumentation to gauge compliance with defined goals, and it offers the services of trained specialists worldwide.
The centre develops and supplies the latest technology as well as highly innovative equipment to customers. It also serves as the competence centre for measuring and quality-related equipment for the SKF Group on a global scale. With more than 20 years of measuring experience, the centre is at the forefront of development in measuring technology. QTC is approved by Lloyd’s Register Quality Assurance Limited to the Quality Management System Standards EN ISO 9001 and EN ISO 14001.
The core of QTC business is fulfilling the quality assurance needs of manufacturers of high-precision round parts and related products and grease testing for the grease industry.
Bearing-related work remains an important part of what QTC does. The company has a quality management system that supports development, design, production, sales and setup of equipment for bearing assembly and quality control of bearings and bearing components. Its engineers help to develop quality evaluation software for this equipment, and it has facilities that systemize the traceability of the calibration of sensors, waviness and vibration equipment.
A full range of technologiesand measurement approaches are available. QTC works closely with other specialists, if required. Installation, setup, training at QTC or within customer premises and extensive follow-up activities are part of the service supplied by the company.
At QTC, a range of in-line and off-line machines are developed and manufactured for:
-
Roundness, waviness and form analysis
-
Noise and vibration testing of bearings
-
Optical inspection
-
Non-destructive material testing
-
Dimension measuring
-
Laser marking
-
Grease testing.
In addition, SKF has developed a range of gauges to check tapered shaft journals or the radial internal clearance of cylindrical roller bearings. They are designed to meet the requirements of high-precision technology, especially in machine tool and spindle manufacturing and spindle repair services.
Low noise and vibrationlevels of bearings are becoming increasingly important in many applications. One of the main reasons for high vibration levels is waviness on the bearing components. The QTC waviness testers enable analysis of the waviness on the compon-ents and provide the production engineer with a powerful tool to improve the production process. As the amplitude of these waves can be within the nanometer range, this puts extremely high demands on the measuring accuracy and resolution. The expertise at QTC in relation to noise and vibration is an important resource for the SKF Group as a whole. The information gained is fed back to SKF’s own manufacturing processes, so that there is a continual improvement in quality of the company’s products
As reduction of vibration levels and low noise levels are becoming key issues in bearing-related applications, dedicated vibration assessment plus other measurements is increasingly important. This is in addition to the basic requirements of meeting the correct stiffness, load capacity, speed limit and life. Apart from other factors, a noisy application might be caused by wavy bearing components, by local defects at rings and rolling elements or by dirt particles in the bearing. All of these bearing quality-related issues can be tested with QTC’s bearing vibration equipment. QTC can also offer this high level of expertise to customers on a consultancy basis to support the optimization of particular applications when it comes to reducing noise and vibration.
Frequency analysis (FFT) as well as other advanced analysis tools can pinpoint faults. The use of spectral masks helps to optimize the bearing performance in customer applications. QTC has also introduced a worldwide calibration system to make sure that vibration equipment operates according to international standards.
For optical measurements, three factors come into play. These are the condition of the object (colour, roughness, etc), the nature of the illumination (white light, coloured light, laser light, etc) and the specific properties of the sensors (matrix camera, line camera, single photo-detector). Increasingly companies are looking for productivity improvements when it comes to optical inspection, through the introduction of machine vision systems that can automate inspection activities. QTC has a particular expertise in the optical inspection of surfaces and missing compon-ents. The machines the company has developed are designed for fully in-line inspection and are fully automated, thus addressing productivity issues. The range of applications cover surface inspection of bearing rings, rolling elements, components of linear systems, seals and cages, as well as identifying missing parts such as rivets or rolling elements, correct riveting of cages, etc. An example where this system has been successfully applied is the inspection of connecting rods within an automotive application.
Non-destructive testingis a widely used testing regime. QTC offers four distinct techniques: ultrasonic testing, eddy current testing, magnetic particle inspection and resonant inspection. As its name implies, non-destructive testing preserves the performance of the component while making sure to comply with specifications. This means that, where necessary, 100 % of production can be inspected in real time, enabling failed components to be eliminated from production, without adding to the production cycle time, to make sure that productivity is maintained throughout manufacture. Again the machines are designed for fully in-line inspection and are completely automated. The MPL250 machine made by QTC can check sintered plain bearing rings with a cycle time of less than three seconds. One area of importance is in the railway industry – for example, where the safety issue is an over-riding factor that puts particular demands on inspection systems.
Because of the importanceof grease performance within its own components and products, SKF has developed a number of grease testing machines. This has led to a deep understanding of lubrication theory. Within QTC’s product range are five dedicated machines, which are the SKF TMG/EMCOR grease-testing machine assesses the corrosion-inhibiting properties of greases. This machine is standardized in DIN 51802, ISO 11007 and IP 220 for the standard method using distilled water. The SKF TMG/ROF+ grease testing machine is used to assess grease performance at high temperatures and high speed, while the SKF TMG/V2F grease testing machine can assess the resistance to leakage under vibration conditions. The SKF V2F also meets the SS 3653 standard for railways – rolling bearings for axleboxes – which tests the mechanical stability of lubricating greases. The remaining machines are the SKF TMG/R2F for assessing the mechanical-dynamic behaviour of greases, and the SKF BEQUIET+ grease testing machine to assess the grease noise in rolling bearings.
Increasingly QTC isapplying its technology to applications outside the SKF Group because the broad range of techniques and equipment it has available is required by industry as a result of demands for efficient manufacturing processes and higher performance products produced with fewer manufacturing defects at competitive costs. Some examples of the range of the work include optical inspection of connecting rods for motor engines, non-destructive testing of sintered parts and the provision of grease testing machines for all leading grease companies worldwide.
With an increasing trend towards the combining of mechanical systems with electronic elements in the form of mechatronics, expertise in both technologies for testing and inspection is increasingly demanded throughout industry. QTC already has more than 20 years experience in measuring techniques that demand know-ledge of sensor technology and electronics. Within the SKF Group’s five platforms, one is mechatronics. QTC also makes a strong contribution to this strategic business area, and alongside the growth in integrated electronics solutions in mechanical systems, data acquisition and evaluation will play an increasing role.