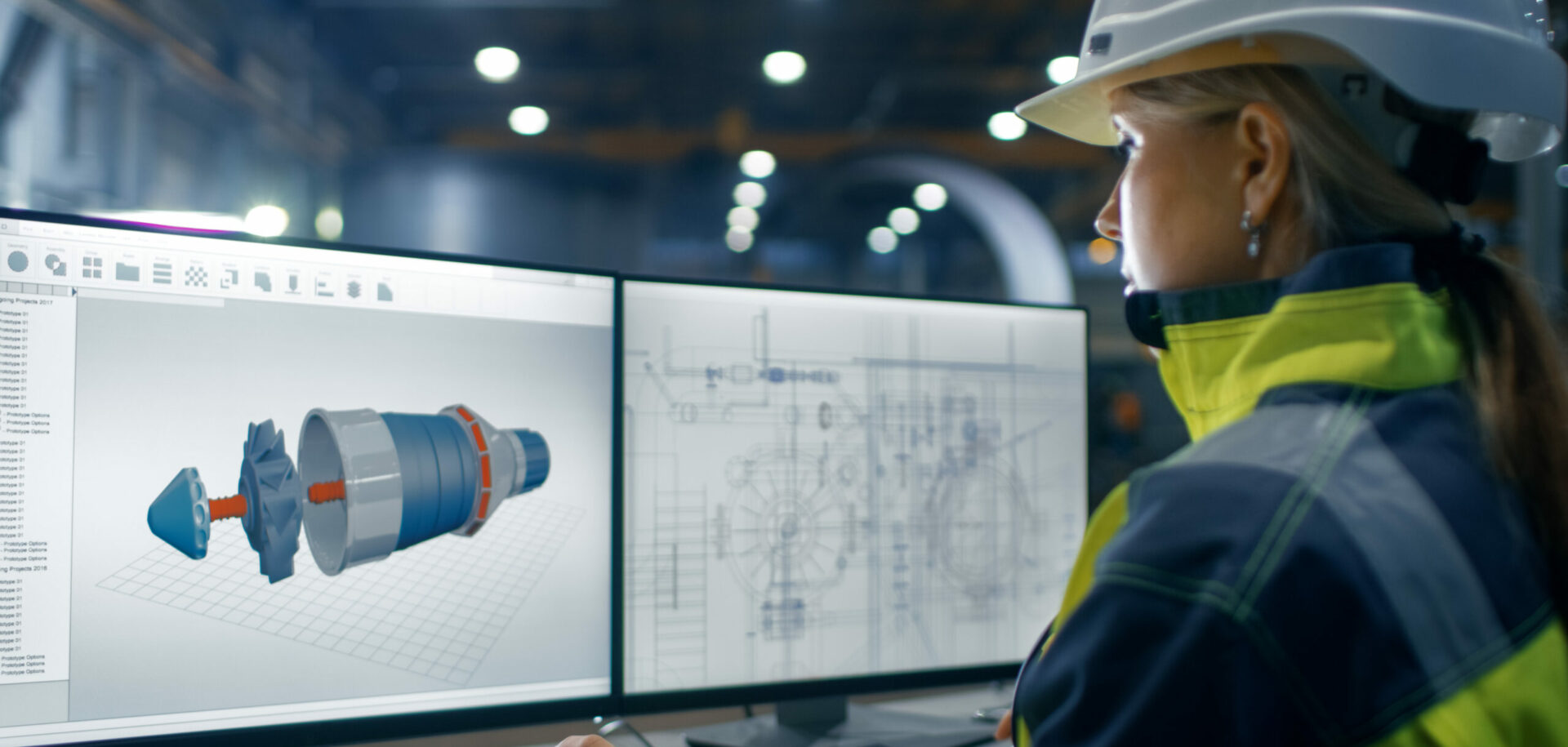
WIRELESS TECHNOLOGY – revolutionizes condition monitoring
A new wireless system from SKF overcomes implementation barriers and expands condition monitoring applications.
Summary
By turning to the wireless technology that enables laptop users to surf the Internet, SKF has created a powerful new tool for use in condition monitoring systems. With Wi-Fi-enabled monitoring systems, SKF has helped remove the barriers to the wider use of condition monitoring by creating a system that is practical, cost-effective and highly mobile.
A new wireless system from SKF overcomes implementation barriers and expands condition monitoring applications.
Condition monitoring technologyhas been used by industry for many years to optimize maintenance and production, by avoiding unplanned downtime to increase overall productivity. The principal parameter used is vibration, by virtue of its direct relevance to the condition of rotating machinery and its diagnostic value.
Instruments used for data collection are generally either portable data collectors for manual/”walk-around” programmes or permanently installed online systems that automatically collect and store data. Use of the latter is well established, especially in machines critical to production. However, there remain a number of barriers to wider adoption, including:
-
high cost of installation, especially in hazardous areas
-
insufficient justification for a permanent system on certain balance-of-plant machines
-
traversing/moving machines where fixed cabling is not possible.
ADVANTAGES OF WIRELESS TECHNOLOGY
SKF has utilized wireless technology to overcome these barriers and to facilitate applications that in the past were impractical, such as temporary installations for troubleshooting and remote monitoring.
Wireless technology eliminates the need for hardwiring for communications and also dramatically reduces sensor cable lengths. Benefits include reduced installation cost, mobility/portability, untethered operation, convenience and reliability.
CHALLENGES TO WIRELESS VIBRATION MONITORING
Vibration monitoring presents unique demands on wireless devices, networks and associated components. High bandwidth is needed, due to the relatively large amounts of data that need to be sent over the wireless link. In addition, good dynamic range, low noise levels and higher-level processing cap-abilities and the ability to capture data at the right time are also key requirements. Battery-powered devices that are required to provide onboard power must satisfy customer demands for long service life. The devices and sensors, as well as the wireless network components, must also cope with conditions commonly found in the industrial environment, such as exposure to water, elevated temperatures, electrical interference, hazardous-area classifications, obstructions, physical location and distance. Wireless security is a must.
CURRENT STATE OF WIRELESS TECHNOLOGY
There are a number of wireless technologies available. At present the one best-suited for condition monitoring applications is 802.11 b/g (often referred to as Wi-Fi). This is the same technology used for laptop computers and wireless office LANs. It has also found increased use in industrial applications for monitoring and certain specific automation functions. It is able to meet the technical needs of condition monitoring (e.g., high bandwidth) and, as an infrastructure choice, offers several advantages in network security, standard implementation well understood by IT departments, multi-use and cost-effectiveness. Power consumption is moderate, and in typical condition monitoring implementations batteries can last for one to two years.
SKF SOLUTION
The SKF Wireless Monitoring System (se bild . 1) is self-contained and battery-powered and utilizes Wi-Fi technology. It can monitor four channels of vibration and four process inputs (4-20 mA) plus one tachometer input. The wireless system is usually programmed to wake up and take measurements based on a fixed time interval, or it can be externally activated on demand by a programmable logic controller, or PLC. The system uses standard accelerometers, including those that also have a temperature output. It performs standard vibration measurements as well as SKF acceleration enveloping and stores dynamic data (FFT and/or time) for diagnostics. Data from the wireless system alone are stored and analyzed in SKF @ptitude software, along with data from other SKF portable or online surveillance devices.
CASE STUDY: AVOIDING CATASTROPHIC BEARING FAILURE
The SKF wireless system was an excellent fit for a paper mill customer who used it to successfully avoid a catastrophic bearing failure. From previous experience, the cost of similar failures was estimated at several hundred thousand dollars. During routine checks using hand-held analyzers, the customer found damage starting on the inner-inner ring raceway of a triple-ring bearing in the paper machine press section. A planned stop was to occur in a couple of weeks, but it was uncertain whether the bearing would be able to last until then. A wireless monitoring system was installed (se bild . 2) to provide 24-hour monitoring and display the data to machine operators. The main advantages of the wireless system were ease and speed of installation and automated data collection and display.
The data display enabled operators to monitor the bearing’s deterioration every hour. The resulting data (se bild . 3) showed that the bearing condition was severe, prompting a decision not to wait for the scheduled stop but instead to replace the roll as soon as possible. Subsequent examination confirmed that the bearing was so severely damaged that it would not have lasted until the scheduled stop (se bild . 4). Thus, in addition to avoiding extended downtime, severe damage to the roll shell and hydraulic beam was also prevented.
CASE STUDY: INNOVATIVE SOLUTION TO A UNIQUE PROBLEM
At a major retail distribution centre, one of the key pieces of equipment is a stacker crane. This machine, essentially a robotic crane running on tracks, automatically handles inventory in and out of high-capacity/high-efficiency storage locations. One of the problems encountered by the customer was the deterioration of the stacker crane tracks (se bild . 5), as evidenced by loud noises sometimes heard during operation. Since the entire assembly moved on the tracks, making fixed cabling impossible, the SKF wireless monitoring system was installed to identify specific locations on the track that had worn out. To do this, the system was set up to collect vibration data as the crane traversed the length of the track. The resulting “spikes” in the time signal (se bild . 6) were correlated with the position of the crane on the track to pinpoint areas of concern.
As a result of the testing, worn sections were repaired instead of the alternative – total replacement of the tracks. Follow-up testing confirmed that the repairs were successful.
CONCLUSION
WiFi/802.11 b/g is a practical solution from both technical and cost perspectives, and its use is expected to expand rapidly. Wireless technology is an important enabler in condition monitoring systems, overcoming barriers to implementation such as cost, practicality and mobility. SKF will continue to be on the forefront of wireless monitoring technologies that are innovative and reliable and that benefit customers in new and traditional applications.
Wireless capabilities expanded for use in hazardous areas
SKF Multilog WMx,a compact, eight-channel, field-mounted monitoring device, collects acceleration, velocity, temperature and bearing condition data in hazardous locations with ease, safety and accuracy.
This newest model is certified to ATEX 2/IEC Zone 2, allowing it to be used in most areas in the hydrocarbon processing industries where non-certified systems are not allowed. The device, which can be powered by batteries, is compatible with standard hazardous-area certified sensors. In add-
ition, the Multilog WMx supports WEP, WPA or WPA2 encryption for increased security.
Outstanding for semi-critical/balance-of-plant machines in hazardous areas, troubleshooting and remote monitoring, the WMx can be a cost-effective choice, by speeding time to implementation and reducing the need for expensive cabling.