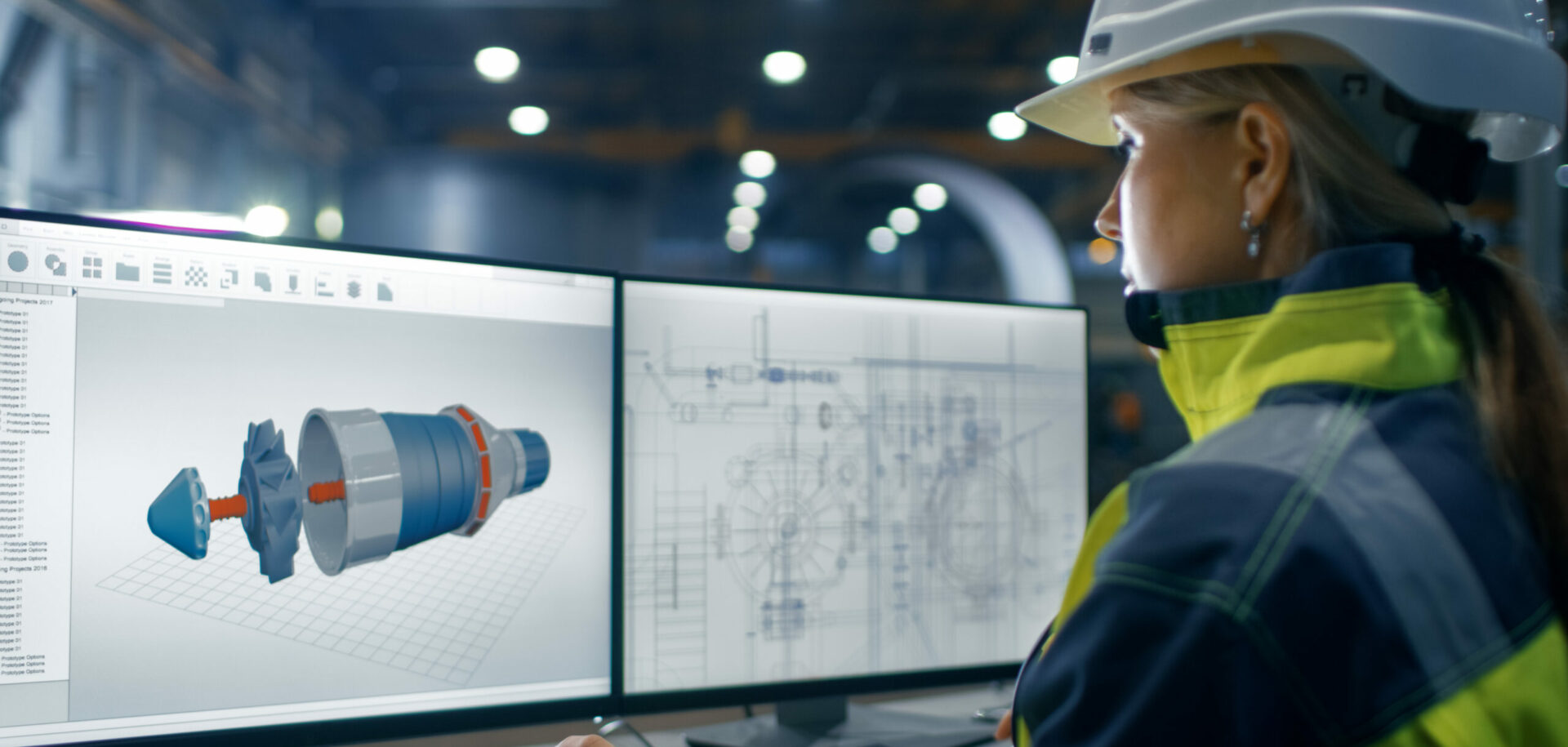
Yarn spinning innovation
Ring spinning is a basic process in the production of high quality fabrics out of wool, cotton, man-made fibres or blends of these fibres. The yarn quality produced by a ring spinning machine is mainly influenced by the drafting system (fig. 1). Here a weighting arm (1) presses three top rollers (2) on to three bottom cylinders (3) which rotate at different speeds. The first bottom cylinder and top roller rotate very slowly, the middle ones move 10 to 20% faster and the front bottom cylinder and top roller about 12 to 30 times faster, depending on the fibre material. Because of these different speeds and the loads on the top rollers, the raw material (4), which is fed into the drafting system, is drawn, and in the case of wool becomes about 12 to 30 times thinner.
The desire to give textile companies better production control, greater manufacturing flexibility and improved overall product quality has led
to the development of a novel solution for yarn-making equipment.Developments have been concentrated on ring spinning machines, in particular the weighting arm, which is a crucial component in determining yarn quality.
Ring spinning is a basic process in the production of high quality fabrics out of wool, cotton, man-made fibres or blends of these fibres. The yarn quality produced by a ring spinning machine is mainly influenced by the drafting system (fig. 1). Here a weighting arm (1) presses three top rollers (2) on to three bottom cylinders (3) which rotate at different speeds. The first bottom cylinder and top roller rotate very slowly, the middle ones move 10 to 20% faster and the front bottom cylinder and top roller about 12 to 30 times faster, depending on the fibre material. Because of these different speeds and the loads on the top rollers, the raw material (4), which is fed into the drafting system, is drawn, and in the case of wool becomes about 12 to 30 times thinner.
The top rollers are coated with rubber cots to improve the clamping effect. Between the middle and the front roller, the fibre mass is guided between two small rubber belts (5), the top and bottom aprons. The top apron is tensioned and guided by a top apron cradle (6). Smooth and constant running of the aprons is very important to yarn quality.
While leaving the last top roller and bottom cylinder of the drafting system, the fibre mass is given a twist by a metal ring (7) with a rotating traveller (8) and a rotating spindle (9), which are located underneath the drafting system. The metal ring is the origin for the name of the ring spinning machine. The twist creates friction between the fibres by which the strength of the fibre mass increases. In this state, the fibre mass is now called yarn. The yarn is wound on to a bobbin (10) attached to the spindle. The speed of the spindles amounts to 10,000 to 14,000 r/min for wool and about 18,000 to 25,000 r/min for cotton. Thus one metre of yarn contains between 300 and 2,000 twists.
The weighting arm is required to allow different loads to be set on the top rollers. Normally this is achieved by helical springs which can be adjusted mechanically in steps.
Also the distances between the rollers have to be adjustable. The distance has to be larger than the length of the longest fibres to avoid the situation where single fibres are torn between the clamping points of top rollers and bottom cylinders.
A modern ring spinning machine for wool has about 1,000 spindles and 500 drafting systems. Weighting arms, top rollers, cradles and bearing units for spindles and bottom cylinders are core products for the SKF Textile Division. These components influence the yarn quality and this defines the quality of the entire spinning machine.
Development targets
Feedback from end users and OEM customers showed potential for improvement in the design of SKF’s existing weighting arm, PK 1601, especially in mounting and handling the arm on the ring spinning machine. To meet customers’ needs,
a number of development targets were defined as outlined below.
- Innovative drafting system
The existing product, PK 1601, has been on the market for many years. European and Japanese customers are keen to get an innovative product as a core component for their machines. In particular, this will help them differentiate from low-cost machines from Far East competitors. - Improved product quality
Constant load on the top rollers is very important to yarn quality. Taking into account the fact that all spindles of one machine should produce yarn of identical quality, constant load and small load deviations are significant quality characteristics of any new weighting arm. - Easy handling
Opening and closing of the weighting arm PK 1601 requires handling forces that can be uncomfortable for operators. During longer periods of machine standstill such as during weekends, the loads of all weighting arms have to be reduced in order to avoid marks in the soft rubber cots of the top rollers, which would otherwise hurt the quality of the yarn. - High technological flexibility and quality
Spinning of wool requires high flexibility in the spinning machine. Expensive raw material is often processed in small lots, and the yarn end users have to react very quickly to market demands influenced by changing fashions.
Different raw materials, types of yarn and desired yarn quality require the ability to allow a number of options for load setting at the top rollers. The existing weighting arm, PK 1601, offers three load steps for every top roller. The setting has to be done manually on each arm. This needs a special tool and takes a lot of time. - Easy mounting
In many cases the weighting arms are mounted on site. The large number of arms used means that quick and easy mounting and setting are essential.New weighting armThe underlying concept for the new weighting arm PK 6000 (figs. 2 and 3) was to use pneumatic pressure instead of metal springs to generate the load on the top rollers, which can be adjusted infinitely.A pneumatic ring tube (1) in the machine supplies each weighting arm with compressed air (2). When the machine is in operation and the weighting arm is closed, a pneumatic valve (3) is opened so that the compressed air can enter a pneumatic rubber spring (4). The pneumatic energy is transformed into mechanical forces on the top rollers (5) by weighting elements with pressure plates (6).When the weighting arm has to be opened, e.g. if the yarn is broken, the operator has to push back the handle (7) which is connected to the push rod (8). The pneumatic valve (3) is pushed down, the air inlet is blocked and the compressed air can flow out of the rubber spring. The helical spring (9) moves the weighting arm upwards automatically. This locking device has the advantage that the arm can be opened and closed without load, which results in low handling and low friction forces in the swivel joints.The design of the new drafting system is completed by a new top apron cradle (10) made from composite material with individual tensioning of each apron (fig. 4).
Advantages of the PK 6000
The pneumatic concept has brought a number of advantages including improved product quality, quick load setting and partial load reduction, considerable technological flexibility, easy and ergonomic handling, easy mounting and modern styling.
The pneumatic principle guarantees constant load on all top rollers at every spindle position. The load remains constant even when the diameter of the top rollers decreases as a consequence of grinding the rubber cots of the top rollers. This grinding is carried out in order to maintain a smooth surface during the lifetime of the cots. Since modern ring spinning machines have up to nearly 1,000 spindles, this affects yarn quality.
The surface structure of the new top apron cradle reduces the friction during apron operation and helps to preserve the aprons. Individual apron tensioning makes the system less sensitive to tolerances in the apron length, improving the fibre guidance and, consequently, yarn quality.
The air pressure is set centrally for all arms at just one point on the ring frame. Thus load setting and the partial load reduction, necessary during longer standstills, can be done in a second instead of having
to operate hundreds of weighting arms.The infinite pressure setting allows the machine to be adapted precisely to the requirements of the yarn.
No great physical strength is required for opening and closing. The weighting arm opens automatically after unlocking and the height of the opened arm is reduced. The top rollers can be easily exchanged.
The new top apron cradle saves up to 40% of the time spent on changing aprons. There is no longer any need to remove and dismantle the top apron cradle for service work.Mounting and setting of weighting arms on the machine is much easier due to improved accessibility of the fastening and setting elements (fig. 5).
Finally, the compact design has a modern appearance and smooth surfaces mean less cleaning.
These advantages benefit both the end users’ customers and the machine manufacturers.Market introduction
A prototype weighting arm was presented to OEM customers at the end of 1994. In September 1995 this was followed by a joint field test with the market leader in worsted ring spinning machines.
The International Textile Machinery Exhibition ITMA at Milan in October 1995 was the opportunity to present formally the new weighting arm. Interest taken in PK 6000 at this venue confirmed to SKF that this weighting arm was a rare, really novel product. The easy handling and the central load setting were recognised as big improvements over current designs.
The continuing field test shows that the new weighting arm has been well accepted by operators and spinning mill management. Both appreciate the advantages of the PK 6000 which were amply demonstrated in the test, and they are keen to acquire the new system in the future. Serial production started in September 1996.
Conclusions
Many positive lessons were learned from this design project. The experience resulted in benefits both for the customer and SKF in improved product quality, gain in market share and reduced development time.
The total development process was characterised by strong market orientation and customer focus. The team members of Marketing & Sales and Textile Technology took care that all customer requirements were met. Besides this, the main OEM partner was involved in the project at an early stage. The combination of the empowered multidisciplinary team and early involvement of suppliers and customers was important for the success of the project overall. Early presentation to customers was an approach that has not been common previously. A 40-50% reduction was achieved in development time when compared with earlier product development projects.
Hansgeorg Binz,
SKF Textilmaschinen-Komponenten GmbH,
Research & Development (CTE),
Stuttgart, Germany