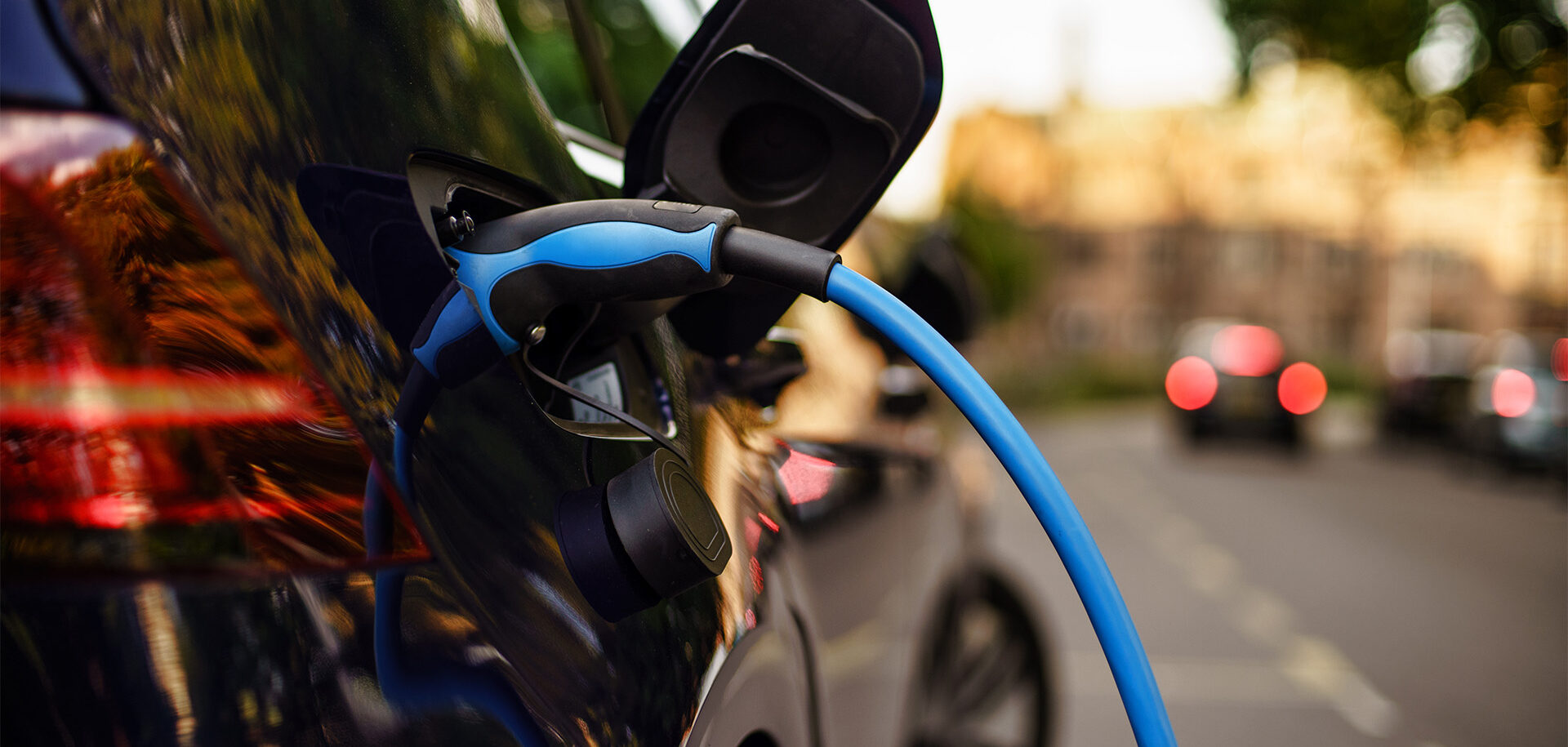
电动汽车电机轴承的放电损伤机理及对策
基础研究揭示减轻电动汽车轴承电蚀损伤的策略。
在全球能源危机以及人们对因全球变暖日益加剧而忧心忡忡的背景下,电动汽车凭借其优于传统燃油汽车的高能源效率、高功率密度以及卓越的加速性能,赢得了广泛关注[文献1]。然而,当寄生电流流经电动汽车电机轴承时,就会出现普遍存在的放电损伤问题——通常被称为电腐蚀[文献2-4]。这种轴承电流,分为非循环电流和循环电流,会引发电腐蚀,导致轴承表面局部熔化、以及噪声、振动与舒适度性能下降、润滑剂劣化和轴承过早失效等一系列严重后果[文献4]。
轴承表面的形貌损伤,如磨砂、点蚀和凹槽,会对电动汽车电机的性能产生重大影响[文献4-6]。当前的研究主要聚焦于轴承整体分析,但由于影响放电现象的参数众多,并相互关联,我们对其基本特性的理解仍显肤浅[文献7,8]。为了加深对这一领域的了解,SKF对弹性流体动力润滑下的球-盘单触点进行了放电试验。该研究揭示了电腐蚀现象与油膜厚度密切相关,并通过一个新型单次放电能量模型得到了验证。这一模型可作为拟定的缓解损伤策略的指南,有助于预防和减少电动汽车轴承中的电腐蚀现象。
球-盘单触点研究为放电现象提供了新的视角
本研究旨在通过深入研究弹性流体动力润滑条件下的球-盘单触点,来揭示和理解电动汽车电机轴承的放电现象。通过将研究范围限定在单一触点,我们希望能够甄别和分析影响放电现象的关键因素,从而深入了解导致电动汽车电机轴承电腐蚀的复杂动态过程,并为此提供有价值的见解。
与轴承整体试验相比,球-盘单触点试验台可增强对电气和润滑条件的控制。我们采用了英国PCS仪器公司生产的商用小型牵引力试验台(图1)。这种设备最初设计用于测量润滑接触和未润滑接触的摩擦性能,从而确保实验的精确性。为了模拟电动汽车轴承中的放电现象,我们对小型牵引力试验台进行了改造,加入了一个自主设计的脉冲驱动单元,如图1所示。该单元可以产生变频,振幅可调的电脉冲,从而高度还原电动汽车在实际应用中的工作环境。为了模拟现实中电动汽车电机的工作状况,尤其是其超过10kHz的高频交流电压特性,我们利用脉冲驱动单元生成的12.5kHz电压进行模拟。
主要发现
1)典型放电信号
图2显示了从牵引力试验台测试中获取的电信号。图中红线表示脉冲驱动单元的输入电压,黑线表示球-盘触点的响应电压。尽管在测试过程中使用了光滑的表面,但球-盘触点的电气性能仍呈现出变化特性。在时间点a和c,球-盘触点的电压与输入电压相近,这意味着触点此时起到了电容的作用。然而,在时间点b,虽然输出电压最初随输入电压而变化,但在输入脉冲结束之前,输出电压降至零。这种现象与电动汽车电机轴承典型的放电现象类似。
图3显示了通过光学显微镜和扫描电子显微镜在牵引力试验台测试中观察到的球体表面上的放电损伤情况。接触区域存在两个对称的损伤带(图3(a)和图3(b)),这表明放电主要发生在这两个区域。接触面分为三个区域(如图3(b)所示),其中区域1和3中呈现出明显的表面损伤,即存在大量重叠的放电凹坑。这些凹坑与从实际应用中退回的轴承表面损伤相似。相比之下,区域2的损伤较为轻微,只有少量孤立的凹坑。圆盘表面的凹坑分布与球体上的分布情况相似。
将损伤表面与计算得到的油膜厚度分布进行比较后,可以清晰地看到,两个损伤带与油膜厚度最小的区域完全吻合,如图3(b)和图3(c)所示。其原因在于电场强度是引发放电的关键性决定因素。油膜厚度最小的区域具有最大的电场强度,因此,放电现象始终出现在油膜厚度最小(hmin)的区域。
受放电凹坑分布的启发,我们开发了一个放电能量模型(公式(1)):
式中,a1, a2和a3是常数,取决于试验台的电容、润滑剂的电气参数和工作条件(如载荷、速度等)。有关该模型的更多细节,请参阅[文献9]。显然,该模型建立了放电能量与油膜厚度之间的直接联系。根据公式(1),减小hmin可以有效减轻盘和球体表面的放电损伤。
4)通过油膜厚度控制放电损伤
基于放电能量模型,我们可以通过控制油膜厚度来调节弹性流体动力润滑单触点的放电损伤程度。为此,我们进行了一系列试验,并发现减小最小油膜厚度的值是一个行之有效的措施,能够减轻放电损伤。
图4显示了表面分析的结果,表明随着最小油膜厚度(hmin)的减小,放电损伤程度也逐渐降低。这一观察结果与模型预测的趋势相符。在除润滑剂粘度外所有条件都相同的试验中,单次放电能量仅受各自hmin值的影响。在23号试验中,由于hmin值最高,其放电能量也最大,导致圆盘表面遭受严重损伤(如图4(a)所示)。相比之下,第24号和25号试验的hmin值要小得多,因此试件表面上几乎没有明显的放电凹坑(如图4(e–f)所示)。第27号试验的hmin值高于第24号试验,由于其放电能量相对较高,显示出可见的放电凹坑(图4(d))。然而,第27号试验的hmin值却低于第26号试验和第32号试验,所以在后两个试验中的接触表面上产生了更大、更密集的放电凹坑,如图4(b)和4(c)所示。
最佳油膜厚度对于最大限度地减轻轴承的电气损伤和机械损伤至关重要
试验结果表明,弹性流体动力润滑接触中的放电现象会随油膜厚度而变化,这与早期的研究[文献8]结论一致,即油膜越厚,所需的击穿电压越高。传统上,我们用击穿电压来比拟轴承的击穿电阻。但本研究表明,电气击穿不仅受油膜厚度的影响,还受到润滑剂介电强度的影响。因此,在预测电动汽车轴承的放电现象时,将油膜厚度、介电强度和击穿电压进行综合考虑至关重要。当前的模型和试验结果表明,通过减小最小油膜厚度,可以有效减轻轴承的电气损伤,这主要得益于单次放电能量的降低。
然而,应该注意的是,过度减小油膜厚度可能会导致磨损等机械损伤,这对轴承发挥最佳性能构成重大挑战。因此,我们迫切需要进一步深入研究,精确界定理想的油膜厚度范围,以便在减轻电气损伤和防止有害机械损伤之间取得微妙的平衡。此外,选择合适的润滑剂是实现这一平衡的关键。我们必须全面考察润滑剂的性能及其与运行条件的适用性。此类研究不仅有助于最大限度地减轻电气损伤,还能够有效地保护轴承表面免受机械损伤。因此,针对这一方向进行全面研究,对于深入了解油膜厚度、润滑剂选择以及轴承整体性能之间的相互作用至关重要。
结论
本研究利用自行改进的小型牵引力试验台,深入探讨了电动汽车电机轴承内部放电现象的复杂动力学。通过对放电损伤的详细研究,我们成功开发并验证了一种放电能量模型。本研究的主要结论总结如下:
- 改进的牵引力试验台成功地模拟了在弹性流体动力润滑条件下可在球-盘单触点中观察到的放电现象。
- 放电主要取决于电场强度,且这一特性在油膜厚度最小的区域始终显现。
- 为了阐明润滑状况对放电现象的影响,我们开发了一个放电能量模型,如公式(1)所示。
- 在弹性流体动力润滑单触点中,通过调节油膜厚度,可以有效控制放电损伤的程度。减小最小油膜厚度有助于减轻由放电造成的损伤。
这些发现对于理解电动汽车轴承的放电现象具有重要意义,并为通过控制油膜厚度来减轻放电损伤的措施提供了有价值的见解。这一研究成果的影响不仅局限于学术领域,而且为致力于提高电动汽车技术的可靠性和耐用性的工程师和研究人员提供了切实可行的指导方针。