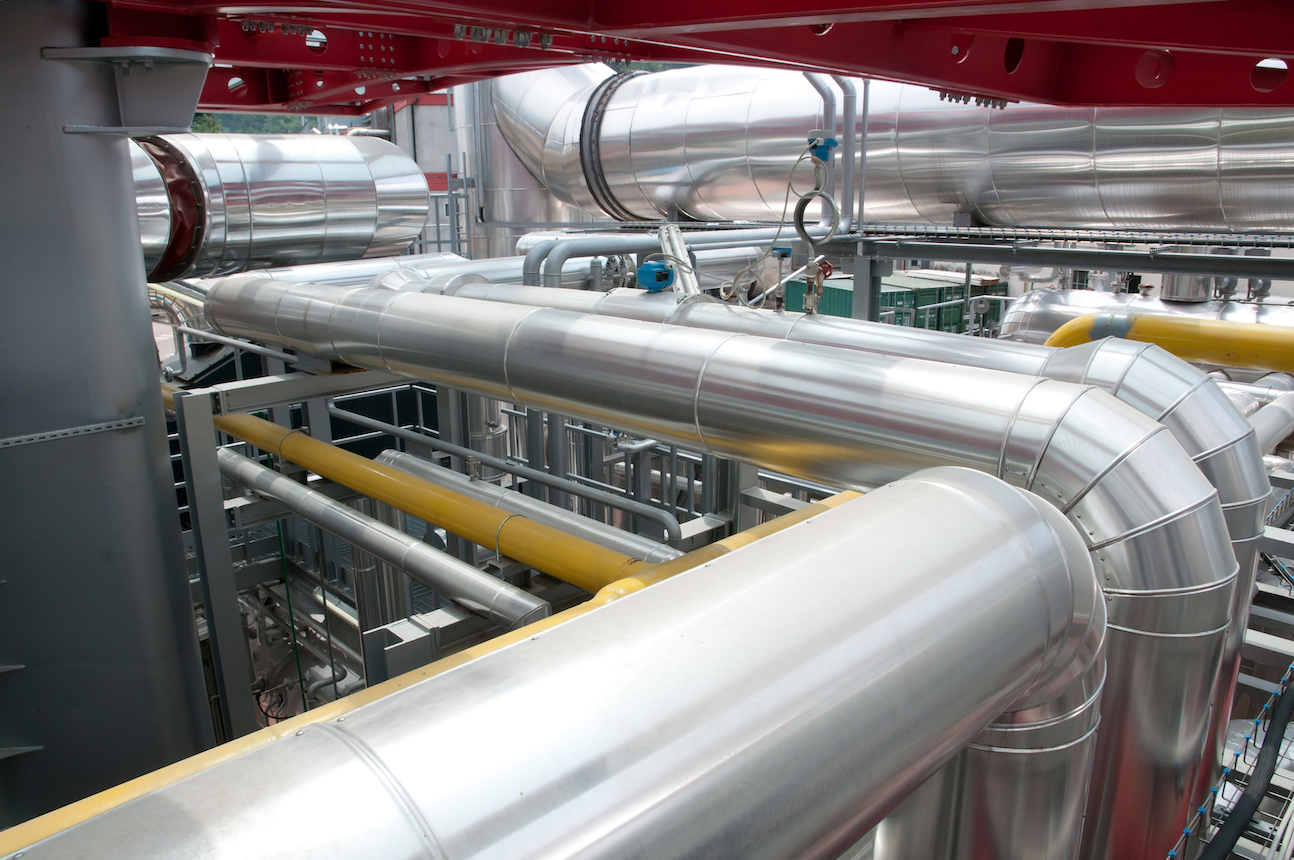
A world built of steel
Steel is the material of choice for a countless number of products. Here is the story of how steel became a key force in world devlopment.
Summary
Hot process
Steel making is a melting, purifying (refining), and alloying process carried out at around 1,600 degrees Celsius under molten conditions. It was almost an art form for centuries. In 1751, Englishman Benjamin Huntsman established a steel works in Sheffield that made steel according to the crucible process using coke as a fuel. With a weight of 30 kilograms, the melt was poured into ingots. It was not until almost a century later that this laborious process was superseded by the introduction of the Bessemer process in 1855, which permitted the production of large volumes of steel for the first time.
Today steel can be produced in basic-oxygen, open-hearth, or electric-arc furnaces. Basic-oxygen and open-hearth furnaces make steel from molten iron, while electric-arc furnaces re-melt scrap steel. The refining of steel usually involves burning off excess carbon and other impurities which separate from the molten steel as gases or slag. This is also the stage at which alloying elements are added.
In general, two processes exist to form raw steel into finished shapes. Hot-working includes hammering, pressing, rolling and extruding the steel under high temperatures. This was first done by hand, later by water power and then by steam.
Cold-working usually follows and includes rolling, extrusion, and drawing (i.e., pulling the steel through a die), and is used to make bars, wire, tubes, sheets and strips where machinability and a bright surface are desired.
Pure metallurgy
About 60 percent of the global steel needs of SKF are provided by wholly owned subsidiary Ovako Steel. All of Ovako’s 500,000-tonne yearly production is based on recycled steel. Around 60 percent of this goes into making the rings and other components for rolling bearings, while the rest is sold outside SKF.
Ovako’s output is based on ladle furnace technology together with advanced heat treatment processes. For bearing applications, Ovako Steel mostly produces Grade 3 Steel, an alloy containing 1 percent carbon and 1.5 percent chromium. This alloy has the advantage of retaining its properties even under huge pressures.
Extensive research and development efforts are currently ongoing to meet customers’ increasingly demanding requirements. “We are constantly pushing for better performance out of our components,” says Thore Lund, manager of material technology at Ovako Steel. “The trend is towards lighter steel designs that can function at higher stresses and higher speeds at a reduced cost.”
It can be said that the modern world is built on a skeleton of steel. The production of it fuelled the industrial revolution, including the railroad, shipping and other industries. Today steel is everywhere – in cutlery, aircraft landing gear, surgical instruments, bridges, skyscrapers and cars.
The first use of steel dates back to the Iron Age, or around 1000 B.C. It is only in recent times, however, that mass-production techniques have made steel the most versatile and utilised structural material in the world. Cheap, strong, eminently recyclable and dependable, modern steel still beats its archrivals – aluminium, plastics and composites – in its widespread use.
According to the Brussels-based International Iron and Steel Institute, world production of steel reached an all-time high of 795 million tonnes in 1997, a 6 percent rise compared with 1996. China, Japan and the United States top the list of producers.
“But steel isn’t just one material,” says John Olof Edström, professor emeritus in metallurgy at Sweden’s Royal Institute of Technology. “There are thousands of different steels, and new ones are constantly being developed for specific applications.”
Lustrous and strong
Steel is iron, a relatively soft metal on its own, hardened by the addition of no more than 2 percent carbon. It is through various melting, purifying, refining and cooling processes, as well as the addition of alloying elements such as nickel, chromium, tungsten, molybdenum, titanium and vanadium, that steel is given its many different qualities. Steel can be lustrous and super-strong as in a drill bit, rough to the touch as in an I-beam, or made to resist corrosion and oxidation for a river-spanning bridge cable.
Making structurally sound steel was discovered in ancient times when carbon from charcoal fires penetrated the melting iron, yielding unusually strong qualities. Refinements are still being made today.
“The history of steel is a blend of alchemy, chemistry, geography and physics,” says Dr. Henning Leidecker, a materials physicist at National Aeronautics and Space Administration (NASA), and an authority on the history of metallurgy. “There is the interplay between inventors with bright ideas and investors with money.”
And it goes a lot further back than one might think. It is a well-documented historical fact that iron- and nickel-rich meteorites collided with the earth containing ready-made alloys such as steel, albeit in a very raw, unrefined form. Some mines in Canada, for instance, still mine meteoric iron.
The art of steel making and iron forging was passed down from master to apprentice for ages. It was an art with many varying local techniques easily spreading from the Middle East to Europe and China. But according to scholars, it wasn’t until the time of Alexander the Great (323 B.C.) that steel came into its own.
At the time, Damascus steel in the form of swords and armour was legendary for its strength and toughness, despite high levels of carbon. Carbon strengthens steel, but too much makes it brittle. Damascus steel was discovered by European smiths centuries later during the 11th century crusades. For a long time, its superior quality could not be reproduced.
The secret, according to an article in Scientific American, was skilful forging, quenching and tempering. Oleg D. Sherby and Jeffrey Wadsworth, from Stanford University, write: “Some medieval smiths insisted that swords be quenched in the urine of a redheaded boy, or in that of a 3-year-old goat fed only ferns for three days.” While the authors cite other ancient instructions, they reinterpret these in the context of modern-day steel making to solve the riddle of Damascus steel.
Uncrackable misconception
Large-scale steel-forming operations can be traced back to wealthy English inventor Sir Henry Bessemer. In 1855, he developed and patented the Bessemer process by which large volumes of liquid steel could be produced for the first time.
By 1900, world production reached 50 million tonnes, according to the Encyclopaedia Britannica, a veritable bonanza compared with that produced under the old methods. While Bessemer got the credit for the process, it was Swedish iron master Göran Göransson who redesigned the Bessemer furnace, or converter, to make it reliable. Poured into seven-tonne moulds, steel was then re-heated and reduced into billets, smaller pieces of steel, which could be forged into bars, beams and rods.
Metallurgy did not become a full-fledged science until the advent of quantum mechanics in the early 1930s, says NASA’s Leidecker. Until then, knowledge of metals, their behaviours and properties, and more importantly what made a metal a metal, remained in the realm of folklore.
“All metals are crystalline and behave like glass,” says Leidecker. “In the late 1800s when railroads were being laid across the United States, there were often cases where a steel train axle would crack after an inspector hammered in an inspection die. Steel, like all metals, is susceptible to cracks. That was an illusion that had to be overcome.”
The lesson wasn’t learned until after World War II. The famous American Liberty Ships, built by the thousands as cargo ships, were also a structural catastrophe. To save time, and perhaps money, large steel plates were welded instead of riveted together into hull sections. On cold passages through the North Atlantic, fatigue cracks developed at the corners of square hatches and propagated rapidly, often with dire consequences.
Weight drawback
Steel has since come a long way. Today’s steel mills, with their computerised sensors controlling glowing slabs of steel gliding down aisles of rollers, are a world apart from the sooty ones of the past. And new technologies governing all aspects of its production – the refining stages, the furnaces, quenching liquids, new alloys – have pushed the capabilities of steel to heights unimaginable only a couple of decades ago.
Steel can be made stronger than anyone wants it to be, and it can withstand higher temperatures than most materials. But in many of its high-tech uses, a space shuttle’s solid fuel rocket motor case, for example, its relatively high weight compared with other materials has always been a drawback.
But that is likely to change. At the 1998 International Geneva Automobile Show, a consortium of 35 steel companies showed a new type of steel that they say can reduce auto body weight by 25 percent. The Ulsab auto body, for Ultra Light Steel Auto Body, is polypropylene sandwiched between super hard and thin steel plates. Because of its superior qualities, Ulsab steel will most certainly give aluminium, plastics and composites – materials traditionally used in the automotive sector – a run for their money.
Alexander Farnsworth
a feature writer based in Stockholm