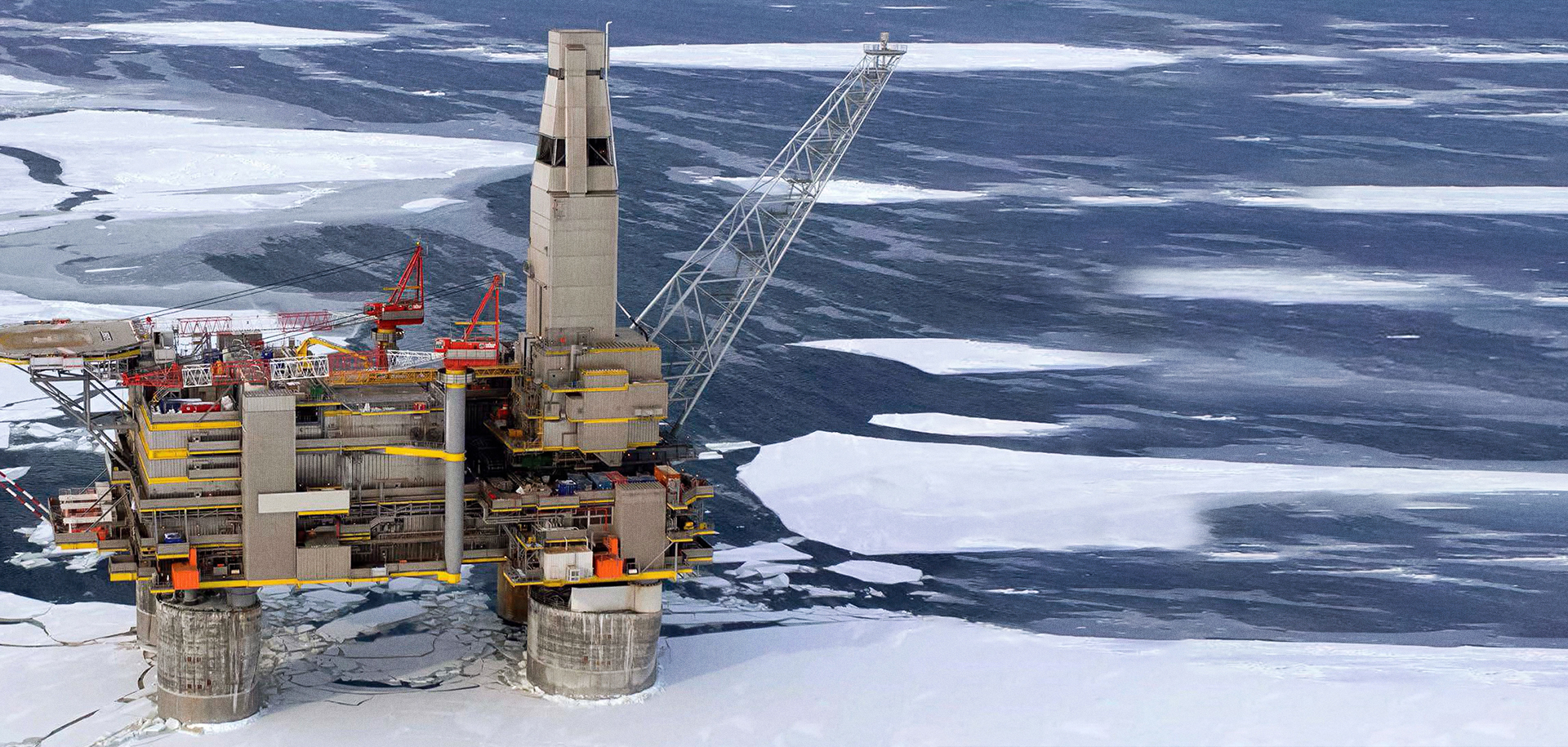
Modèle généralisé de durée de vie SKF pour roulements hybrides
SKF a récemment introduit son concept de Modèle généralisé de durée de vie des roulements (GBLM) [1]. Depuis, ses travaux se sont focalisés sur des roulements pour applications spécifiques et sur la validation expérimentale du modèle. Le calcul de la durée nominale des roulements hybrides est l’une des applications de ce modèle. Il s’agit de roulements dotés de bagues en acier et d’éléments roulants en nitrure de silicium (Si3N4).
Les roulements hybrides sont destinés aux applications où les conditions de service sont difficiles, avec, par exemple, une lubrification médiocre et/ou un niveau de contamination élevé [2], [3]. Du fait de la rigidité supérieure du matériau céramique, la zone de contact hertzien est légèrement moins étendue dans un roulement hybride, ce qui se traduit par une pression de contact et une contrainte en sous-couche supérieures par rapport à un roulement tout-acier de géométrie identique. En théorie, la durée en fatigue du roulement s’en trouve réduite. Toutefois, dans certaines applications typiques, il a été observé que les roulements hybrides duraient plus longtemps. Comment expliquer ce phénomène surprenant ? Comment le modéliser ? Cet article est consacré à ces questions et montre que le modèle GBLM est tout à fait adapté pour expliquer ces observations sur le terrain. Le modèle GBLM de SKF pour roulements hybrides est désormais disponible.
Les roulements hybrides sont dotés de bagues en acier pour roulements et d’éléments roulants en nitrure de silicium de qualité roulements (Si3N4) (Fig. 1). Le nitrure de silicium est un matériau céramique (autrement dit non-métallique) très dur et peu ductile, qui présente un module d’élasticité élevé, une excellente résistance thermique et chimique, une faible densité et qui est peu conducteur. Compte tenu des propriétés d’isolant électrique de ce matériau, les roulements hybrides peuvent être utilisés pour fournir une isolation électrique efficace entre le palier et l’arbre dans les moteurs CA et CC, ainsi que dans les générateurs. Les roulements hybrides offrent d’excellentes performances dans des conditions de lubrification médiocre et de contamination solide, malgré des contraintes de contact plus élevées par rapport à des roulements tout-acier soumis à une charge identique (du fait de la rigidité supérieure des éléments roulants en céramique).
En outre, les roulements hybrides se caractérisent par une vitesse admissible supérieure et, dans la plupart des cas, une durée de vie nettement accrue par rapport à des roulements tout-acier de même taille soumis aux mêmes conditions de fonctionnement. Les roulements hybrides réalisent également d’excellentes performances dans des conditions de fortes accélérations, vibrations et oscillations. Dans des applications caractérisées par des vitesses élevées, comme les broches de machines-outils et turbocompresseurs, une géométrie interne, des matériaux et des systèmes de lubrification spécifiques peuvent cependant être requis. Cette tendance devrait perdurer et de nombreuses autres applications industrielles modernes devraient apparaître et tirer profit des propriétés uniques offertes par les roulements hybrides.
Les matériaux céramiques sont utilisés dans les roulements depuis les années 60. À l’origine, ils étaient destinés aux roulements pour températures extrêmes dans les applications aéronautiques. Des essais ont montré que le nitrure de silicium dense pressé à chaud offrait une meilleure résistance à la fatigue de contact de roulement (FCR) par rapport à d’autres matériaux céramiques. Des variations significatives des performances en fatigue ont, par ailleurs, été observées entre des lots de production de billes en nitrure de silicium en apparence identiques. Dans les années 80, Lorösch et al. (1980) [4] ont soumis des roulements à billes à contact oblique hybrides à des essais de durée en fatigue. Leur essai réalisé avec des billes en nitrure de silicium de la meilleure qualité disponible a révélé que la résistance à la FCR des roulements hybrides était comparable à celle de roulements tout-acier soumis à une charge identique – et ce, malgré une pression de contact supérieure de 12 % dans les roulements hybrides. Cependant, lors d’un essai supplémentaire réalisé avec un deuxième lot de billes en nitrure de silicium, les résultats de durée en fatigue ont été cette fois-ci médiocres, ce qui démontre l’importance de la qualité des billes en céramique en ce qui concerne ces performances.
Au fil des ans, la qualité et la fiabilité des éléments roulants en céramique se sont considérablement améliorées. L’introduction de méthodes d’essais non destructifs (END) et les progrès continus réalisés au niveau de la pureté du nitrure de silicium et de la technologie de frittage ont permis aux ingénieurs de mettre au point des billes en nitrure de silicium offrant des performances stables en FCR, cf. Galbato et al. (1992) [5]. Les roulements hybrides ont ainsi été de plus en plus utilisés, à partir des années 90, dans les broches de machines-outils à grande vitesse où ils ont permis d’atteindre une vitesse supérieure et une meilleure précision, Cundill (1993) [6]. La Fig. 2, tirée de Cundill (1990) [7], illustre l’amélioration de la résistance en fatigue de la céramique grâce aux progrès réalisés en matière de pressage à chaud, de diminution de la porosité et des défauts de surface, d’un bout à l’autre du processus de fabrication (qui peut désormais être contrôlé au moyen d’END).
Objectif des travaux actuels
Il ressort de la rétrospective de l’évolution des roulements hybrides que la résistance en fatigue du nitrure de silicium de qualité roulements a fait des bonds de géant au cours des 20 dernières années. Les performances en FCR des billes en nitrure de silicium ont augmenté de deux ordres de grandeur depuis le début des années 80. Des essais de durée en fatigue réalisés sur des roulements hybrides montrent par ailleurs clairement que l’élément roulant en céramique est le composant le plus fiable dans un roulement. Néanmoins, l’impact de la hausse de 12 % de la pression de contact observée dans les roulements hybrides est visible dans des conditions de fonctionnement où la fatigue de contact en sous-couche constitue le mécanisme de dommage prédominant. La Fig. 3a représente la courbe de probabilité de Weibull des essais d’endurance réalisés par Forster et al. [8] sur des roulements hybride et tout-acier dans des conditions identiques. La courbe montre que dans des conditions de charge élevée et de lubrification adéquate, les performances en fatigue des roulements sont dominées par la fatigue en sous-couche. Par conséquent, la probabilité de défaillance pour une durée de service donnée est supérieure pour les roulements hybrides, qui sont soumis à une pression de contact élevée (3,5 Gpa), par rapport à la variante tout-acier soumise à une pression de 3,1 Gpa. (Remarque : la pertinence statistique est faible compte tenu de l’importance du chevauchement de la barre de confiance de 90 % visible sur la courbe de Weibull de la Fig. 3a).
La Fig. 3b représente la courbe de probabilité de Weibull des essais d’endurance réalisés par Chiu et al. [9] sur des roulements hybride et tout-acier dans des conditions identiques. L’essai a été réalisé sous une charge moins élevée se traduisant par une pression de contact hertzien maximale de 2,6 GPa pour le roulement hybride et de 2,3 GPa pour la variante tout-acier. Cet essai a été effectué dans des conditions sévères : température élevée, film lubrifiant mince et rodage des pistes avec une huile contaminée par des impuretés de l’environnement, pour simuler les conditions réelles de lubrification de l’application.
Démarche de modélisation généralisée
Une équation généralisée de durée a été définie dans la référence [1] avec des termes distincts pour la surface et la sous-couche (Fig. 4). La relation entre la durée L du roulement en nombre de tours et le nombre de cycles de charge N peut être exprimée par la formule L=N/u , où u correspond au nombre de cycles de charge par tour.
Dans les calculs de durée nominale des roulements, une pente standardisée de la loi de Weibull est appliquée, e. L10 correspond à 10 % de durée de vie des roulements, ce qui correspond à une survie des roulements de 90 %, S=0,9. Le calcul de durée peut alors s’écrire sous la forme de l’équation (1) :
L’équation (1) représente la base d’un modèle généralisé de durée de vie des roulements qui fait clairement la distinction entre l’accumulation des dommages en surface et la fatigue en sous-couche. La partie de l’équation (1) correspondant à la sous-couche, représentée par l’intégrale du volume, peut être résolue de la même manière que dans la référence [1], en utilisant les techniques classiques relatives à la fatigue des contacts de roulement.
En revanche, la partie correspondant à la surface, représentée par l’intégrale de l’aire dans l’équation (1), doit être quantifiée d’une manière radicalement différente. Une estimation des dommages dus aux conditions réelles de contrainte à la surface des pistes dans les différentes conditions de fonctionnement potentielles du roulement est nécessaire.
Cette tâche est complexe mais offre la possibilité, dans l’estimation de la durée nominale des roulements hybrides, de tenir compte de façon cohérente des phénomènes tribologiques qui régissent les performances et propriétés d’endurance du contact céramique-acier décrit dans la référence [2].
Survie de la surface au niveau de l’interface céramique-acier
L’équation (1) peut être reformulée d’une manière qui indique clairement la distinction entre la contribution de la surface des pistes et celle de la sous-couche à la durée de vie du roulement : équation (2).
Pour une taille de roulement donnée, et en excluant les constantes, le dommage par fatigue en surface dans l’équation (2) est une fonction directe des effets combinés des conditions de contrainte auxquelles la surface des pistes est soumise à chaque passage dans le contact de roulement : équation (3).
L’évaluation de l’intégrale des dommages en surface (3) peut s’effectuer en intégrant les contraintes induites en surface des pistes par diverses conditions de fonctionnement du roulement.
Dans la formulation actuelle, les contraintes en surface et l’accumulation de dommages peuvent être traitées en recourant à une modélisation avancée de l’altération de la surface pour les contacts rugueux de roulement-glissement à lubrification élasto-hydrodynamique, comme les modèles micro-EHL par exemple, voir Morales-Espejel et al. [10]. Cette approche, également applicable à des conditions de lubrification marginale et en présence d’indentations, nécessite d’utiliser des échantillons 3D de l’état de surface des pistes (incluant la microgéométrie des indentations) (Fig. 5).
Le recours à des analyses pointues des contraintes en surface basées sur le régime micro-EHL peut parfois s’avérer chronophage et fastidieux pour des calculs généraux de durée nominale des roulements. C’est la raison pour laquelle une étude paramétrique a été réalisée pour définir une équation analytique simplifiée qui permettra une estimation rapide des dommages par fatigue en surface dans les roulements hybrides, pour des conditions de fonctionnement données. Pour cette étude paramétrique, plusieurs topographies de surface ont été collectées par le biais de mesures 3D par interférométrie optique de la piste de roulement (Fig. 5).
Dans le cadre de ce projet, une centaine d’échantillons de pistes de roulements hybrides de type rigides à billes, à contact oblique et radiaux à rouleaux ont été collectés. Les échantillons couvraient une multitude de conditions de rodage des pistes de roulements, avec différents niveaux de propreté et contamination.
Les micro-géométries de surface collectées ont permis de réaliser plusieurs simulations numériques de l’intégrale des contraintes de fatigue en surface dans les contacts hybrides. L’effet de la contamination du lubrifiant a été intégré aux simulations à travers la prise en compte de la présence d’indentations sur les topographies et de contraintes locales de tractions en surface. Dans les simulations numériques, les conditions de lubrification du roulement ont été modélisées par le biais de simulations du régime micro-EHL transitoire du contact de roulement pour différentes épaisseurs de film lubrifiant.
Les résultats numériques de l’étude paramétrique de l’intégrale des contraintes en surface des roulements hybrides ont mis en lumière la possibilité de représenter cette quantité au moyen d’une formule analytique. Il est apparu que tous les résultats numériques pouvaient être estimés de manière satisfaisante au moyen d’une fonction exponentielle. Cette fonction repose essentiellement sur deux paramètres principaux : la charge relative Pr = P/Pu du contact de roulement et le facteur environnemental de la lubrification, ηenv = ηlub ∙ ηcont , équation (4) :
Les termes c1⋯cn de l’équation (4) dépendent de la condition environnementale de l’application (ηenv), directement déductible des facteurs de lubrification (ηlub) et de contamination (ηcont), utilisée dans l’application de roulement.
Application du modèle
Le modèle généralisé de durée de vie des roulements de l’équation (4) peut être appliqué pour représenter les données des essais d’endurance de Forster [8] et Chiu [9] mentionnés ci-dessus.
Les essais ont été réalisés avec des roulements à billes à contact oblique taille 7208. Au total, 40 roulements hybrides ont été testés et 12 défaillances ont été enregistrées. En ce qui concerne la variante tout-acier, 32 roulements ont été soumis à un test d’endurance qui a occasionné 21 défaillances. Les détails géométriques des échantillons et les conditions de charge et de contrainte relatifs à ces essais d’endurance sont indiqués dans le Tableau 1.
La principale différence entre les deux types d’essais porte sur les conditions de charge et de lubrification. Lors des essais d’endurance de Forster, la charge était supérieure, entraînant une pression de contact hertzien de 3,5 Gpa pour la variante hybride. Le système de circulation d’huile était doté d’une excellente filtration. Les conditions de lubrification étaient bonnes par ailleurs, avec une valeur kappa d’environ 2,5. Le facteur environnemental GBLM découlant de ces conditions de lubrification est alors ηenv=0,85.
On obtient ainsi un faible indice de contrainte superficielle. En effet, dans les conditions de fonctionnement indiquées, la fatigue en sous-couche détermine les performances du contact de roulement. Par conséquent, les conditions d’essai de Forster sont avantageuses pour la variante tout-acier du roulement 7208 qui fonctionne avec une contrainte hertzienne inférieure, de 3,1 Gpa, d’où un dommage par fatigue par cycle de passage des éléments roulants également inférieur.
Lors des essais d’endurance de Chiu, la charge appliquée était nettement inférieure, entraînant une contrainte hertzienne maximale de 2,6 Gpa pour la variante hybride. La température de fonctionnement lors de ces essais était supérieure (150 °C), d’où des conditions de lubrification du roulement moins favorables. Par ailleurs, ces essais ont été réalisés avec des défauts artificiels sur les pistes afin de reproduire les conditions de contamination typiques de nombreuses applications de roulements. Les roulements ont, pour ce faire, été rodés pendant 15 minutes dans une huile contenant 2,5 ppm de particules d’oxyde d’aluminium de 20 mm. Le facteur environnemental GBLM relatif aux conditions de service est faible dans ce cas : ηenv=0,035.
Dans le cas des essais d’endurance de Chiu, compte tenu des conditions environnementales et de charge indiquées, la résistance à la fatigue en surface joue un rôle prépondérant dans la survie du roulement. En d’autres termes, l’indice de contrainte en surface est élevé ; c’est la fatigue en surface qui détermine les performances en fatigue du roulement. L’indice de contrainte en surface spécialement développé pour les roulements hybrides joue ici en faveur des performances en fatigue des roulements hybrides, ce qui compense la contrainte hertzienne supérieure (2,6 GPa) présente dans le contact céramique-acier.
Les conditions de fonctionnement indiquées ci-dessus concernant les essais d’endurance du roulement hybride ont été introduites dans un code ad hoc de calcul de la durée de vie des roulements avec la mise en œuvre du modèle généralisé de durée de vie des roulements d’après l’équation (4). Les performances de durée de vie du roulement 7208 dans sa variante tout-acier ont également été calculées en utilisant une version équivalente du GBLM comme indiquée dans la référence [1] de Morales-Espejel. Les résultats des 10 % de durée en fatigue calculés correspondant aux différents essais et variantes de roulements sont présentés sous forme des courbes de Weibull des Fig. 7a et 7b. Les durées théoriques, en millions de tours, sont indiquées sur les courbes par les lignes verticales fines correspondant chacune à la variante du roulement indiquée.
L’analyse des résultats fournis par le modèle GBLM, concernant les essais de Forster, est présentée sur la Fig. 7a. La courbe montre que les durées en fatigue théoriques de la variante hybride et de la variante tout-acier correspondent environ à la borne inférieure de l’intervalle de confiance à 90 % de la probabilité de défaillance de 10 % des résultats d’essais d’endurance. Autrement dit, les essais d’endurance de Forester valident les résultats du modèle GBLM avec un niveau élevé de pertinence statistique.
Les résultats fournis par le modèle GBLM, concernant les essais d’endurance de Chiu, sont présentés sur la Fig. 7b. Dans ce cas, la prédiction présente un niveau de pertinence statistique inférieur. Cela peut s’expliquer par le faible nombre de défaillances relevées pour la variante hybride et par une défaillance précoce ayant affecté les résultats des essais sur la variante tout-acier. Cependant, les résultats d’endurance du modèle GBLM sont tous nettement en dessous des durées expérimentales L10,50 et parfaitement cohérents avec les observations expérimentales. En effet, le modèle a montré sa capacité à représenter parfaitement la durée en fatigue de contact de roulement nettement plus longue de la variante hybride, et ce, malgré la pression de contact supérieure à l’intérieur de ce roulement lors de l’essai.
Synthèse et conclusions
Les progrès importants réalisés pour améliorer la qualité de la céramique pour roulements ont permis d’obtenir des roulements hybrides fiables et performants, notamment dans des conditions tribologiques difficiles (lubrification médiocre et/ou forte contamination). Il est ainsi désormais possible de prédire avec une fiabilité élevée la durée nominale des roulements de ce type. Le modèle généralisé de durée de vie des roulements (GBLM) SKF qui permet de distinguer entre surface et sous-couche a été appliqué pour calculer la durée nominale des roulements hybrides. SKF a développé un modèle et un outil informatique pour ce calcul. Ce modèle a été appliqué à des fins de démonstration dans deux séries d’essais d’endurance qui ont fait l’objet de publications. Les résultats ont été inattendus. Dans un cas (lubrification correcte, propreté et charge élevée), les performances du roulement hybride étaient inférieures à celles du roulement équivalent tout-acier, tandis que dans l’autre cas (charge inférieure mais contamination supérieure et lubrification médiocre), le roulement hybride a affiché des performances supérieures. Seul le modèle GBLM, capable de distinguer entre survie de la surface et de la sous-couche, peut fournir ces résultats.
Les conclusions peuvent être résumées comme suit :
- L’estimation de la fatigue de contact de roulement dans les roulements hybrides nécessite de prendre en compte, d’une part, la fatigue en sous-couche, qui est moins favorable aux roulements hybrides, et, d’autre part, la fatigue en surface, qui est nettement plus favorable aux roulements hybrides ;
- En distinguant entre survie de la surface et survie de la sous-couche, le modèle GBLM de SKF permet d’équilibrer les deux mécanismes de dommage par fatigue et de fournir une description fiable du comportement de FCR des roulements hybrides ;
- SKF a développé et intégré à des outils informatiques le modèle GBLM pour le calcul de la durée nominale des roulements hybrides. Les clients peuvent ainsi désormais tirer pleinement profit des roulements hybrides.
Références
[1] Morales-Espejel G.E., Gabelli A. : « Un nouveau modèle – Une avancée majeure », SKF Evolution N° 4, 2015, p. 21-27.
[2] Vieillard C., Brizmer V., Kadin Y., Morales-Espejel G.E., Gabelli A. : « Les avantages offerts par les roulements hybrides dans les conditions difficiles », SKF Evolution n° 3, 2017, p. 21-26.
[3] Morales-Espejel G.E., Hauleitner R., Wallin H. H. : « Garder la tête froide », SKF Evolution n° 1, 2017, p. 26-30.
[4] Lorösch H.K., Vay J., Weigand R., Gugel E., Kessel H. (1980) : « Fatigue Strength of silicon nitride for high-speed rolling bearings », Transactions of ASME, J. of Engineering for Power, vol. 102, 128-131.
[5] Galbato A.T., Cundill R.T., Harris T.A. (1992) : « Fatigue Life of Silicon Nitride Balls », Lubrication Eng. 48 (11), 886–894.
[6] Cundill R.T. (1993) : « High precision silicon nitride balls for bearings », Ball Bearing Journal, 241, p. 26-32.
[7] Cundill R.T. (1990) : « Material selection and quality for ceramic rolling elements », Proc. of Mech. Eng. Seminar, Rolling Element Bearings – Towards the 21st Century, p. 31-40.
[8] Forster N. H., Peters S. M., Chin H. A., Poplawski J. V. et Homan R. J. (2017) : « Applying Finite Element Analysis to Determine the Subsurface Stress and Temperature Gradient in Highly Loaded Bearing Contacts », Bearing Steel Technologies : 11e volume, ASTM STP1600, J. M. Beswick, Ed. ASTM, West Conshohocken, PA, p. 151–166.
[9] Chiu Y. P., Pearson P. K., Dezzani M. et Daverio H. (1996) : « Fatigue Life and Performance Testing of Hybrid Ceramic Ball Bearings », Lubrication Eng. 52, 3, 198-204.
[10] Morales-Espejel G. E., Brizmer V. (2011) : « Micropitting modelling in rolling-sliding contacts: application to rolling bearings », Tribol. Trans. 54 625–643.