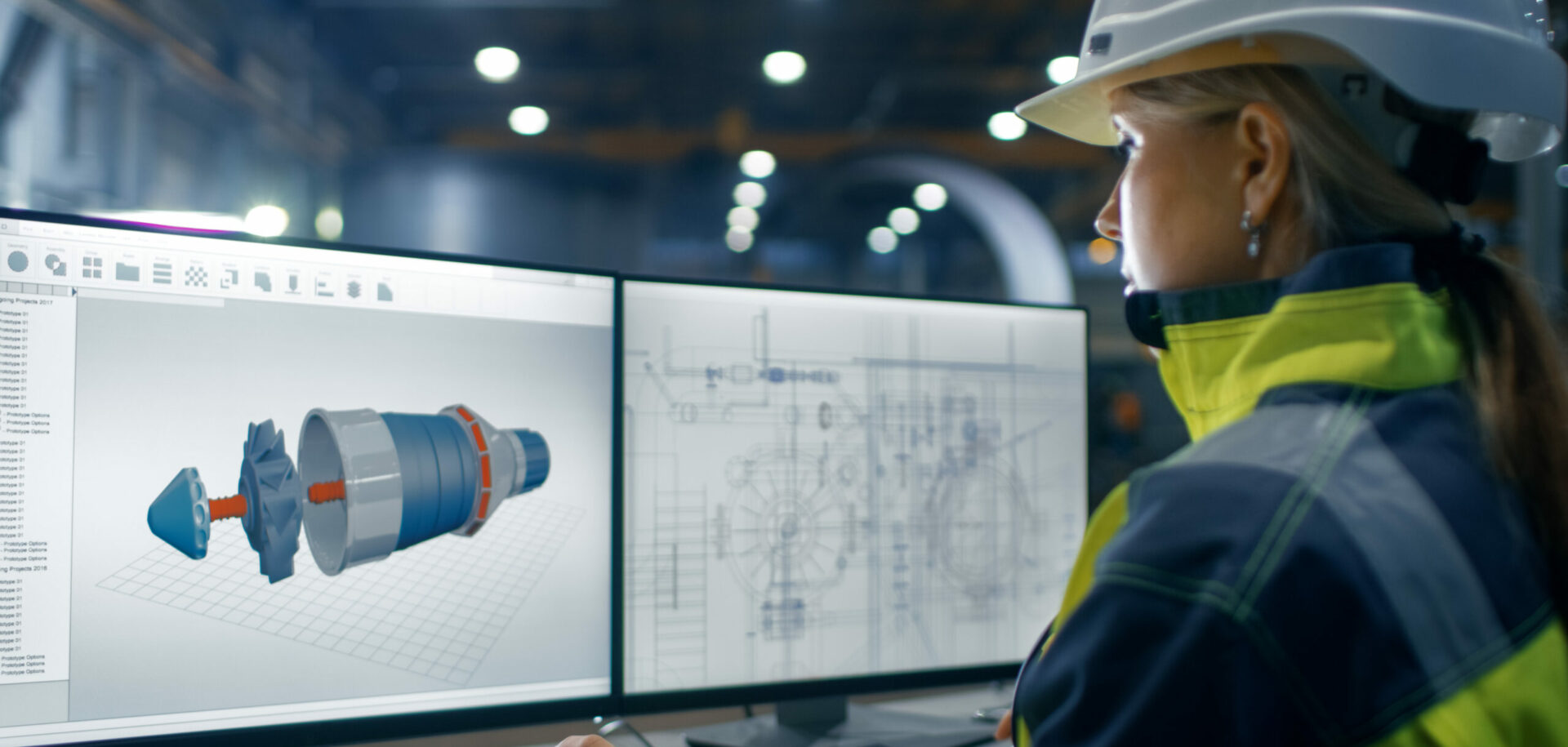
Comprendre et prévenir la fatigue de surface
Technologie
Dans de nombreuses applications industrielles présentant des contacts roulants/surfaces de glissement comme les roulements lubrifiés, la densité de puissance n’a cessé d’augmenter au fil du temps pour satisfaire des besoins de rendement accru, de réduction du poids et de diminution des coûts (à travers une conception plus compacte). En parallèle, les conditions de service sont devenues de plus en plus difficiles – charges élevées combinées à des températures supérieures, film d’huile plus mince et/ou conditions de lubrification extrêmes – ce qui
peut entraîner une altération de la surface
des pièces [1].
Technologie
La fatigue de surface se manifeste dans un premier temps par une modification de la couleur/perte d’éclat de la surface qui s’amplifie à mesure que le phénomène se développe. L’observation au microscope des zones endommagées de la surface révèle la présence d’un micro-écaillage, de micro-fissures ou de micro-piqûres (Fig. 1).
S. Way [2] a été l’un des premiers à se pencher sur la fatigue de surface dans les contacts lubrifiés. Il a ainsi observé que le rodage de disques en contact améliorait nettement leur résistance à la fatigue de surface. Plus tard, P. H. Dawson [3] a découvert l’importance d’une bonne lubrification et d’une faible rugosité pour empêcher ou retarder l’apparition de ce phénomène.
Il est maintenant admis que la fatigue de surface est un phénomène imputable à des conditions de lubrification médiocres [4] générant un frottement localement élevé et des pressions importantes au niveau des aspérités. Ce phénomène a fait l’objet de nombreuses expériences et études théoriques [5-7]. D’autres phénomènes superficiels, comme l’usure douce (enlèvement modéré de particules) [8, 9], viennent contrer la fatigue de surface pendant une phase initiale de rodage et à d’autres stades ultérieurs. En éliminant des couches de matière endommagée, ils rendent la surface moins propice au développement de micro-fissures. SKF a récemment développé des modèles détaillés de fatigue de surface [10], basés sur l’interaction entre la génération de micro-fissures de surface et la perte douce de matière dans le but d’identifier des paramètres clés et de prédire les risques d’endommagement des surfaces.
Les sections qui suivent offrent une description succincte des aspects mécaniques (lubrification, rugosité, frottement et perte douce de matière) dont on considère qu’ils jouent un rôle important dans le processus. Cette description s’accompagne de recommandations pour améliorer les conditions au niveau du contact et réduire ainsi le risque de fatigue de surface. La chimie (tribochimie) joue sans nul doute un rôle clé [8, 9] en influant sur l’enlèvement de matière et/ou le coefficient de frottement limite au cours de la phase de rodage et des différents stades suivants.
Frottement de surface
Compte tenu de l’impact du régime de lubrification sur la fatigue de surface, qui est en effet nettement amplifiée par des conditions de lubrification limite et/ou mixte, le frottement « à sec ou en conditions limites » joue un rôle déterminant. Dans un régime avec une épaisseur du film lubrifiant adéquate, la force de frottement est introduite par cisaillement du film lubrifiant lors du glissement. La contrainte de cisaillement (et, par conséquent, la force de frottement) dépend de la rhéologie du lubrifiant, selon le schéma de la Fig. 2a. Cependant, chaque fois que des sommets d’aspérités sont en contact, il se produit un frottement « sec » (ou frottement en lubrification limite) qui s’apparente à un frottement de Coulomb, comme sur la Fig. 2b, caractérisé par une valeur nulle lors du « roulement pur » et une valeur quasi-constante dès que le glissement commence. Il convient de noter que, dans les deux cas, une vitesse de glissement supérieure n’induit pas nécessairement un frottement supérieur. Au sein d’un contact rugueux (conditions limites) ou en régime de lubrification mixte, les points « secs » ne génèrent aucune force de traction à la surface sauf en cas de glissement, aussi faible soit-il, comme indiqué sur la Fig. 2b. Cependant, des conditions de « roulement pur » n’existent pas. Des contacts réels, y compris dans des conditions de « roulement nominal pur », présentent toujours une petite part de glissement qui se traduit par un certain frottement de glissement et, par conséquent, par un risque possible de fatigue de surface. Des essais réalisés au sein du Centre d’ingénierie et de recherche SKF, à Nieuwegein, aux Pays-Bas, ont montré que des conditions de roulement nominal pur peuvent également déboucher sur une fatigue de surface. Il a également été démontré que, dans des conditions identiques et pour un même nombre de cycles, lorsque le coefficient de frottement en conditions limites augmente, la fatigue de surface est plus sévère. En conclusion, le coefficient du frottement limite est un facteur extrêmement important dans l’apparition de micro-fissures superficielles lorsque le contact s’opère dans des conditions de lubrification limite ou en régime mixte.
Le frottement limite dépend largement du type de lubrifiant utilisé et du cocktail d’additifs qu’il contient. La valeur du coefficient de frottement limite peut être extraite des courbes de Stribeck obtenues à l’aide de tribomètres bille-sur-disque. Cela s’effectue d’ordinaire à partir d’une valeur déterminée de glissement nominal dans le contact (2 – 5 %) et en augmentant progressivement la vitesse d’entraînement du lubrifiant. Le coefficient de frottement limite dans un tribomètre bille-sur-disque correspond au premier point de la courbe de Stribeck (Fig. 3). Il est à noter que les coefficients de frottement mesurés ici représentent des valeurs moyennes dans le contact.
Importance de la lubrification et de la rugosité
La lubrification joue un rôle décisif dans la durée des roulements. C’est la raison pour laquelle les modèles SKF utilisés pour le calcul de la durée tiennent compte de l’impact du paramètre de lubrification к. L’importance de la lubrification et de la rugosité dans la fatigue de surface est intimement liée à l’effet des forces de frottement et des concentrations de contraintes locales (au niveau des aspérités). Dans le cas d’une lubrification limite ou mixte, la présence d’irrégularités (rugosité ou empreintes, Fig. 4) sur la surface influe sur la répartition des points secs et lubrifiés dans le contact. En outre, la variation de la contrainte de traction en surface et les concentrations de contraintes possibles (Fig. 5) doivent également être prises en compte. Une rugosité élevée (ou des variations de rugosité importantes) favorise la détérioration du film, ainsi que des pressions de contact et des contraintes de traction élevées. Les concentrations de contraintes dans les zones critiques de discontinuité de la contrainte de traction sont alors amplifiées.
D’après des résultats d’essais et une modélisation théorique réalisée par SKF, l’altération de surface apparaît en premier lieu dans des zones de pression discontinue (gradients de pression élevés) associée à une rugosité accrue. Elle est nettement visible sur les bords de stries, au sommet des aspérités ou au niveau des bourrelets autour des empreintes (Fig. 4). De façon assez inattendue, c’est généralement la plus lisse des deux surfaces en contact qui montre des signes d’altération en premier.
Interaction entre orientation de la rugosité et direction du frottement
Des expériences montrent que dans des conditions de lubrification limite ou mixte, une orientation transversale de la rugosité (par rapport au sens de roulement/glissement) est plus propice à une fatigue de la surface qu’une orientation longitudinale (Fig. 6) ; ces mêmes conclusions sont décrites dans le document [5]. Cette observation est intéressante car il s’ensuit que dans des conditions de film lubrifiant élastohydrodynamique (EHL), la rugosité transversale peut entraîner la formation d’un film mieux établi mais également des ondulations de pression plus importantes. Toutefois, dans des conditions de lubrification limite ou mixte, les mécanismes en œuvre sont différents.
Les chercheurs SKF ont déterminé que la composante de la force de frottement normale à la direction de la rugosité peut accroître considérablement la concentration de contrainte à la base des pics de rugosité pour la surface la plus rugueuse et aux sommets des micro-contacts pour la surface la plus lisse (Fig. 5). Ce phénomène peut accroître les dommages et l’altération de la surface, mais sa sévérité est fonction de la micro-géométrie réelle de la rugosité. Il existe toutefois un autre aspect lié à l’historique des contraintes. Par rapport à la rugosité longitudinale, la rugosité transversale induit un nombre supérieur de cycles de micro-contraintes dans le contact (avec ou sans lubrification). La fatigue étant sensible au nombre de cycles de contraintes, une altération plus soutenue est par conséquent attendue sur la surface de contact opposée. Des expériences ont été menées, parallèlement à des simulations numériques, pour démontrer cet effet (Fig. 6) en soumettant des surfaces très similaires aux mêmes conditions, exceptée l’orientation de la rugosité. Pour le modèle, le même échantillon de rugosité a été utilisé à 0° et 90°. Les modèles SKF et les résultats des expériences concordent.
Le contact de deux surfaces rugueuses
Dans les applications industrielles, le contact s’opère entre deux surfaces réelles présentant une certaine rugosité. C’est également le cas lors des essais réalisés au sein de SKF grâce à l’utilisation d’un banc d’essai sur la fatigue de surface (SDTR) qui repose sur une barre tournante en contact avec trois disques (tous en acier à roulements trempé). Il a été observé que, lorsque la barre présentait une rugosité supérieure à celle des disques de charge, aucune altération de surface n’apparaissait au bout d’une durée raisonnable, y compris dans les conditions les plus sévères (Fig. 7a). À l’inverse, lorsque les disques présentaient une rugosité plus élevée que celle de la barre (Fig. 7b), la surface de la barre était facilement altérée. D’autres sources font également état de cette observation ([9]). L’explication probable réside dans l’historique des charges induit par les micro-cycles de fatigue générés par la rugosité.
Les conditions dans la zone de contact étant, en général, proches de la lubrification limite ou mixte, l’historique des charges est imposé par la surface la plus rugueuse à la surface la plus lisse, dès qu’un roulement s’opère. Cette situation (une surface lisse et une surface rugueuse en contact de glissement l’une sur l’autre) est représentée schématiquement sur la Fig. 8. On observe que la surface lisse « voit » une fluctuation de la pression (micro-cycles de charge), tandis que tous les points de la surface rugueuse sont toujours soumis aux mêmes contraintes (supérieures dans les zones de contact et réduites dans les zones de non-contact). Cet exemple montre que la surface rugueuse domine en imposant la variation de charge à la surface lisse. Dans des contacts réels, les surfaces sont toutes les deux rugueuses et en mouvement (avec un certain degré de glissement), mais en cas d’écart de rugosité, la surface la plus rugueuse impose les micro-cycles de charge à la surface la plus lisse. Si les propriétés mécaniques des deux surfaces sont identiques, la surface la plus lisse sera ainsi plus sensible à la fatigue de surface en présence d’un glissement. Cependant, dans des conditions de lubrification optimale avec des pressions hydrodynamiques, cet effet dans l’historique des charges peut être très différent. En cas de roulement, les ondes de pression hydrodynamique se propagent à des vitesses différentes.
La Fig. 9 fournit des résultats de simulation pour un contact surface rugueuse sur surface lisse. Elle présente la zone altérée en fonction de la pression de contact hertzien maximale. On remarque que la fatigue de surface progresse beaucoup plus vite sur la surface la plus lisse et que, pour les deux surfaces, le risque augmente avec la charge.
Usure douce
Des tests effectués sur le banc SDTR ont montré que si la viscosité du lubrifiant est trop faible (1 cSt par ex.), l’apparition d’une fatigue de surface n’est pas systématique, c’est plutôt une usure douce (léger enlèvement de matière) qui s’opère. Il est ainsi admis qu’en cas de diminution de la qualité de lubrification, représentée par le paramètre к, pour les roulements, ou le ratio lambda Λ (Λ = h/Rq) pour les contacts lubrifiés d’une façon plus générale, l’enlèvement de matière devient important. La fatigue de surface et l’usure douce se font concurrence [8, 9] en s’opérant toutes deux lors du rodage et en phase de régime constant. La modélisation de la fatigue de surface est une tâche complexe compte tenu de cette interaction de plusieurs phénomènes.
On estime que, dans certains cas, l’usure douce en surface peut réduire ou empêcher la fatigue de surface en modifiant la topographie de la surface ou en enlevant des couches de matière altérée, ce qui rend la surface moins sensible à la fatigue de surface [8, 9]. L’usure douce peut également interagir avec les conditions de lubrification du contact. La Fig. 10 montre un exemple de l’impact de la lubrification, selon des prévisions SKF établies par modélisation concernant le pourcentage de surface altérée en fonction du paramètre de qualité de la lubrification (Λ) pour deux cas : avec et sans usure douce. Comme on peut le voir, en l’absence d’usure douce, la fatigue de surface augmente progressivement avec la diminution de la valeur de Λ, car plus le film lubrifiant est épais, plus la surface est protégée. Lorsque la fatigue est combinée à une usure douce, le comportement se révèle plus complexe. À de très faibles valeurs de Λ, la fatigue de surface est entièrement supprimée par l’usure douce en surface. Toutefois, l’effet de contre-balancement exercé par l’usure douce disparaît rapidement avec l’augmentation de Λ, entraînant une progression temporaire de la fatigue de surface avec un pic à Λ≈ 1,1. Dans l’exemple ci-dessous, au-delà de ce point, l’influence de l’usure douce devient négligeable et les deux courbes se rejoignent.
Impact du glissement
L’impact du glissement sur la fatigue de surface dans les roulements bénéficie depuis quelque temps d’un regain d’intérêt en tant que sujet d’étude. De nombreuses études affirment qu’une augmentation du glissement aurait pour effet de majorer la fatigue de surface en s’appuyant sur des concepts de propagation des fissures. Toutefois, avant de se propager, une fissure doit d’abord apparaître. Grâce aux outils de modélisation SKF et à des expériences réalisées en laboratoire, il apparaît qu’une augmentation du glissement n’entraîne pas nécessairement un accroissement de la fatigue de surface. En réalité, c’est même l’inverse qui se produit. La Fig. 11 montre l’impact du glissement avec le modèle SKF (courbe) lorsque l’usure douce est prise en compte. Sur la même figure, des photographies de la surface des rouleaux dans le cadre d’une expérience d’augmentation du glissement avec respectivement S=0,01, S=0,02 et S=0,1 (S= vitesse de glissement/vitesse d’entraînement) indiquent clairement une coïncidence entre la fatigue de surface maximale et des valeurs de glissement faibles (S≈0,01). La valeur de glissement généralement présente dans n’importe quel type de roulement. Ainsi, en matière de résistance à la fatigue de surface en fonction du glissement, il n’existe aucune différence de performance entre, par exemple, des roulements à rouleaux à profil rectiligne ou à profile courbe, voire même des roulements à billes.
Il existe donc deux explications à ce mécanisme, sur la base de concepts de génération des fissures.
Frottement : il n’augmente pas nécessairement avec le glissement dans les deux cas lubrification ou fonctionnement à sec (=> Frottement de surface). Dans un contact sec (lubrification limite), le frottement suit la loi de Coulomb. Un glissement même minime suffit à activer ce mécanisme qui atteint pratiquement sa valeur maximale. Si le glissement continue d’augmenter, la force de frottement exercée sur la surface n’augmente pas (une fois une certaine stabilité de la surface atteinte). Dans des contacts lubrifiés, le frottement suit la loi rhéologique du lubrifiant. Dans des conditions de lubrification élasto-hydrodynamique, le comportement du lubrifiant est non-newtonien et proche des conditions limites de contraintes de cisaillement. Par conséquent, un glissement accru n’a pas pour effet d’augmenter considérablement le frottement sur la surface.
Usure douce : elle augmente avec le glissement, enlevant les couches endommagées de matière à la surface, ce qui retarde l’apparition des dommages par fatigue.
Conclusions
On peut tirer un certain nombre de conclusions relatives à la fatigue de surface. En premier lieu, la qualité de la lubrification (et l’état de surface) est extrêmement importante en ce qui concerne l’apparition (et le contrôle) de la fatigue de surface. Une lubrification mixte ou limite génère des points de contact essentiellement « sec ». Il en résulte une augmentation locale des contraintes de traction en surface, des concentrations de contraintes (les zones humides présentent un frottement inférieur par rapport aux zones sèches) et des cycles de micro-contraintes, ce qui favorise la fatigue. Le frottement en surface joue un rôle majeur dans l’apparition de la fatigue de surface. Même dans des conditions de roulement pur « idéales en apparence », une fatigue de surface peut se produire puisqu’un glissement est toujours présent dans les applications réelles. Compte tenu de l’importance du frottement en surface dans la génération de la fatigue de surface, l’apparition de contraintes de traction et de dommages en surface nécessite un certain glissement. Cependant, l’augmentation du glissement au-delà de 1 ou 2 % (valeur type pour n’importe quel type de roulement) n’augmente pas le risque de fatigue de surface car le frottement n’est pas augmenté et l’usure douce associée contribue à contrer la fatigue en surface.
Les concentrateurs de contraintes en surface et l’historique des contraintes (micro-cycles) dans des conditions de lubrification limite ou mixte constituent probablement les facteurs les plus importants responsables des différences de performance de la rugosité contre la fatigue de surface. Toutefois, en présence d’un film lubrifiant optimal, l’effet de la rugosité s’avère négligeable. Les essais ont démontré que dans le cas d’un « contact » entre une surface rugueuse et une surface plus lisse, cette dernière est plus sensible à une fatigue de surface. Enfin, l’usure douce a généralement pour effet d’empêcher ou de retarder l’apparition de micro-fissures en gommant les aspérités importantes pendant la phase de rodage et en enlevant les couches de matière abîmée proches de la surface. Toutefois, une usure importante ou localisée peut causer des modifications de la macro-géométrie des pièces avec des répercussions néfastes en termes de durée de vie.
Méthodes de prévention
Il ressort de ces études un certain nombre de mesures pratiques à mettre en œuvre pour réduire la fatigue de surface. Par exemple :
-
assurer une lubrification satisfaisante (film établi) en fonction de l’application, à savoir viscosité supérieure du lubrifiant, vitesse de rotation supérieure, température inférieure etc. ;
-
réduire le frottement en conditions limites (lubrifiant, épaississant, revêtements à faible frottement, etc.) ;
-
réduire les éléments favorisant les micro-concentrations de contraintes (contamination, impuretés, marques dues au montage, etc.). Recourir à une topographique optimisée ;
-
réduire les mouvements dynamiques perturbateurs sous charge (application de précharges ou réduction des jeux par ex.) ;
-
dans le cas de matériaux similaires, veiller à l’homogénéité de la rugosité des différents éléments en contact (par le biais du rodage par ex.) ;
-
dans certains cas, un enlèvement léger et parfaitement maîtrisé de matière en surface (interaction additif-lubrifiant) peut être justifié pour réduire le degré de fatigue de surface ;
-
utiliser des roulements SKF Explorer, dont la topographie de surface a été optimisée, pour éviter le risque de fatigue de surface.
Références
[1] Norme ISO 15243 : Roulements – Détérioration et défaillances – Termes, caractéristiques et causes (2004).
[2] Way S. : Pitting due to Rolling Contact, J. of Appl. Mech., vol. 57, pp. A49-A58 (1935).
[3] Dawson P.H. : Effect of Metallic Contact on the Pitting of Lubricated Rolling Surfaces, J. Mech. Eng. Sc., vol. 4(1), pp. 16-21 (1962).
[4] Olver A.V. : The Mechanism of Rolling Contact Fatigue – an Update, Proc. Instn. Mech. Engrs., Part J, J. of Eng. Trib., Vol. 219, pp. 313-330 (2005).
[5] Oila A. et Bull S.J. : Assessment of the Factors Influencing Micropitting in Rolling/Sliding Contacts, Wear, Vol. 258, pp. 1510-1524 (2005).
[6] Brandão J.A., Seabra J.H.O. et Castro, J. : Surface Initiated Tooth Flank Damage Part I: Numerical Model, Wear, Vol. 268, pp. 1-12, 2010.
[7] Brandão J.A., Seabra J.H.O. et Castro J. : Surface Initiated Tooth Flank Damage Part II: Prediction of Micropitting Initiation and Mass Loss, Wear, Vol. 268, pp. 13-22 (2010).
[8] Lainé, E. et Olver, A.V. : The effect of Anti-wear additives on fatigue damage, Extended abstract, 62e conférence annuelle STLE (2007).
[9] Lainé E., Olver A.V. et Beveridge T.A. : Effect of lubricants on micropitting and wear, Tribology International, 41, pp. 1049-1055 (2008).
[10] Morales-Espejel G.E. et Brizmer V. : Micropitting Modelling in Rolling-Sliding Contacts: Application to Rolling Bearings, Tribology Transactions, sous presse.