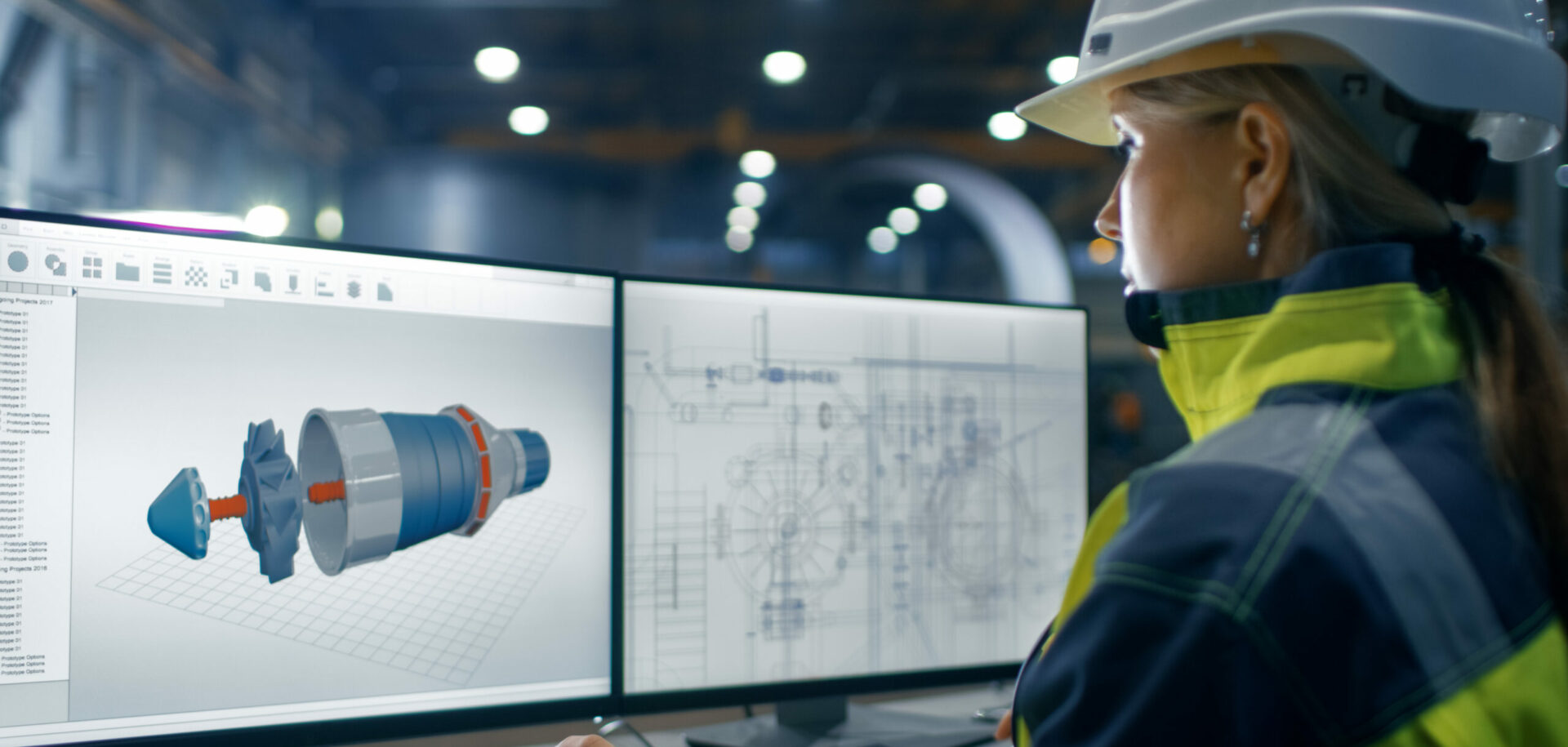
The ability to deliver greater power in a more compact form is what the auto industry is looking for in terms of current alternator design.The highly competitive nature of the auto industry means increasingly rapid changes in design and more sophisticated features, which affect the performance demands on car alternator bearings.
Increasingly cars are designed to include such power equipment as air conditioning, electric windows, automatic seat adjusters, power-assisted steering, fuel injection and engine-management systems. The trend is towards more compact cars designed for city environments, which means that average speeds are dropping while engine temperatures are rising. This puts pressure on alternator manufacturers to improve overall performance and reduce size.
For the bearings within such products, the impact is evidenced in increases in rotational speeds, temperature and loads from the poly V belt now commonly used to supply power to systems such as the AC compressor, the pump for power steering, the water pump and the alternator.
Current car alternator designs
Today, car alternators typically supply electrical current in the range of 50 A to 110 A, although 150 A is possible, depending on equipment requirements and battery needs.
Normally the alternator requires two deep groove ball bearings mounted on the rotor shaft. The bearings mounted on the drive end (pulley side) locate the rotor. Usually, these would be SKF sizes 6303, 6302 or 6203. The bearings mounted on the other side (slip ring side) are axially free, i.e. non-locating, sizes 6203, 6202, 6003 or 6002.
Modern alternators have internal ventilation and are equipped with two high-performance fans located inside the alternator body at each end of the rotor coil. Previous designs have a single external fan behind the pulley. In some cases, to provide better servicing and other functions, the slip ring and its two brushes are located at the end of the rotor instead of between the two bearings.
Bearing design criteria
Based on the changing trends in car alternator design, SKF engineers set about developing new criteria for bearings within this application. They defined design goals that included a service life in excess of 2,000 hours under high, variable loads up to 1,800 N from the poly V belt tension, speeds of up to 20,000 r/min and angular accelerations up to 2,000 rad/s2 as average value. Additional conditions included the ability to withstand certain measured vibration levels, an ambient temperature of 120 °C and under dry and wet contamination conditions, a starting temperature as low as -40 °C and quiet running.
Such performance criteria required optimisation of all the bearing components – seal, cage, lubrication and steel ring components. Optimisation was carried out using the Failure Mode Effect Analysis method and verified by tests in SKF laboratories.
Seal improvements
The key new requirement was the ability of the bearing seal to survive a linear speed of 25 m/s against its bearing inner ring counterface. Normally this speed is in the range of 15 m/s. An additional key requirement was sealing efficiency against contaminants such as dust and water while retaining lubricant inside the bearing.
A finite element-based computer program developed by the SKF Engineering & Research Centre (ERC) in the Netherlands was used to evaluate and optimise seal designs. This program analyses the sealing lip contact force, friction and stress. The target was to avoid significant changes in the lip contact force regardless of the lip interference with its counterface inside the tolerance range set, either by the bearing axial clearance or the manufacturing tolerances of the bearing components.
As a result of this work, the hammer seal lip, HSL, was created, its name reflecting its overall shape. This low contact, low heat-generating seal has a number of important features. The seal has a long, thin, radial, flexible lip that acts on the bearing inner ring counterface. Contaminant exclusion is achieved by a special seal groove. The internal seal shape acts as a labyrinth so the inner ring shoulder, followed by a tapered rubber shape, allows the correct grease flow and good grease retention. The seal has a metal insert that increases the bearing’s internal volume to provide good lubrication conditions. A tight fit and good seal position are achieved through the design of the seal anchorage area. Finally, the seal is made from a polyacrylic rubber that can withstand high temperatures and resist lip tearing.
A full testing regime was carried out on the HSL design. This was to provide a comparison between the traditional RS1 seal types used in car alternator applications. Such seals perform well in dirty and dry environments. The tests applied were:
- frictional torque measurements at low speed to define the starting and steady-state bearing friction
- frictional torque at the maximum alternator speed (18,000 r/min)
- speed test at maximum speed. This provides information on bearing temperatures and grease retention under severe conditions
- dust test with Arizona dust
- static and dynamic water tests.
A final experiment on complete alternators is the high-pressure water test that simulates hot water cleaning of the car engine by high-pressure cleaners.
The HSL successfully passed even the most severe of these tests and was released for car alternator applications.
Cage selection
Today’s 16-valve petrol engines have less inertia than eight-valve designs. This means that their speed can change quickly from 2,000 to 4,000 r/min with, consequently, a larger change for the alternator – from 6,000 to 12,000 r/min. Also, at idling speeds, some acyclism, or irregular rotational speed, can occur. The designers chose a polymer cage reinforced with glass fibre rather than pressed metal to give the desired characteristics for this application of good speed behaviour, low heat generation, good performance during misalignment with angular acceleration – deceleration and, after a period of operation, subsequent poor lubrication conditions.
Complete alternators incorporating this cage design were tested by means of a range of rapid speed changes. Both the material and cage design met qualification standards of 2,000 rad/s2 of angular acceleration – deceleration.
Choice of grease
Grease selection is an important consideration for car alternators. At ERC, bearing tests highlighted the particular performance criteria for this application. The characteristics were clearly defined as high-temperature performance, high-speed capability, good load-carrying capacity, rust inhibition, low temperature limit, quiet running and compatibility with the various bearing materials. As a result, a modern polyurea grease with synthetic oil was chosen.
Again, rigorous qualification of the grease was carried out. To consider all the possible effects of bearing components on grease life under high speed and high temperature, tests were carried out on one of the most critical bearings in the car alternator arrangement. This is the 6202 rear bearing, which is exposed to the highest temperatures. This bearing, along with a grease based on polyurea thickener and a synthetic hydrocarbon/alkyldiphenylether base oil, was tested in specially designed high-speed, high-temperature test rigs.
New steel generation
Since the dawn of car alternator design, some early failures of the drive end bearings have been experienced (less than 60,000 km). The returned bearings show spalling of the outer ring raceway and some on the inner ring. Mainly taxi fleet operators noted this problem, often in diesel vehicles.
Metallurgical inspection shows typical fatigue patterns with dark and white etching regions. The difference in the orientation of the white bands when compared with the classical fatigue picture suggests a higher level of stress induced by a stress field superimposed on one created by pure rolling contact. Vibrations from the engine, system resonance and the aluminium end-cover deformations (mainly on the drive side) were considered to be the causes.
Steel technology is continually under development within SKF, and it was realised that a new bearing steel for car alternators would improve bearing performance. The new steel composition is designated SKF 3M and has been tailored to obtain the optimum bearing properties. The main changes are the addition of molybdenum to increase structural strength, wear resistance and dimensional stability of the bearing rings. The carbon content was optimised to increase toughness.
A special test rig was built to simulate the true axial vibrations of the application. The test conditions applied to this rig were based on recordings made on cars and then tuned to obtain a good correlation between test results and failures observed in the field. The tests were carried out on complete alternators equipped with two batches of bearings – one made of standard steel, the other with the new SKF 3M steel. It was observed that the first batch had an actual life shorter than that expected from the basic life calculation, while for the SKF 3M bearings, expectations were exceeded. Early failures were eliminated through the use of the SKF 3M steel with fatigue life 10 times that expected with the traditional steel.
Final validation
The crucial step is to ensure that the new bearing matches its expected performance in real applications. Manufacturers typically requested that testing of alternators incorporating the new bearing be carried out at an ambient temperature of 100 °C, electrical output at 80% of full load and initial belt tension load on the alternator pulley of 1,800 N. The tests were run with a running-in period of 50 hours at 5,000 r/min, followed by 200 hours at 3,000 r/min and then a maximum speed of 18,000 r/min for at least 1,000 hours. The acceptance criterion for the bearing was that the grease was still in a good lubrication state after this time (confirmed with a Fourier Transform infrared spectrum analysis) with no material fatigue on ring raceways and balls. During testing, all the parameters, such as speed and current, were controlled and bearing temperatures provided an early alarm of failure. Additional tests were typically time-dependent tests involving variable speed and electrical loading.
In the final validation tests and in subsequent field and customer testing, bearing life exceeded that requested by customers in their applications. Mass-produced bearings continue to meet the standards set. Bearings will continue to be improved and developed in line with trends for even tougher alternator performance demands.
Michel Boutreux,
Electrical Division,
Saint-Cyr-sur-Loire,
SKF France S.A.