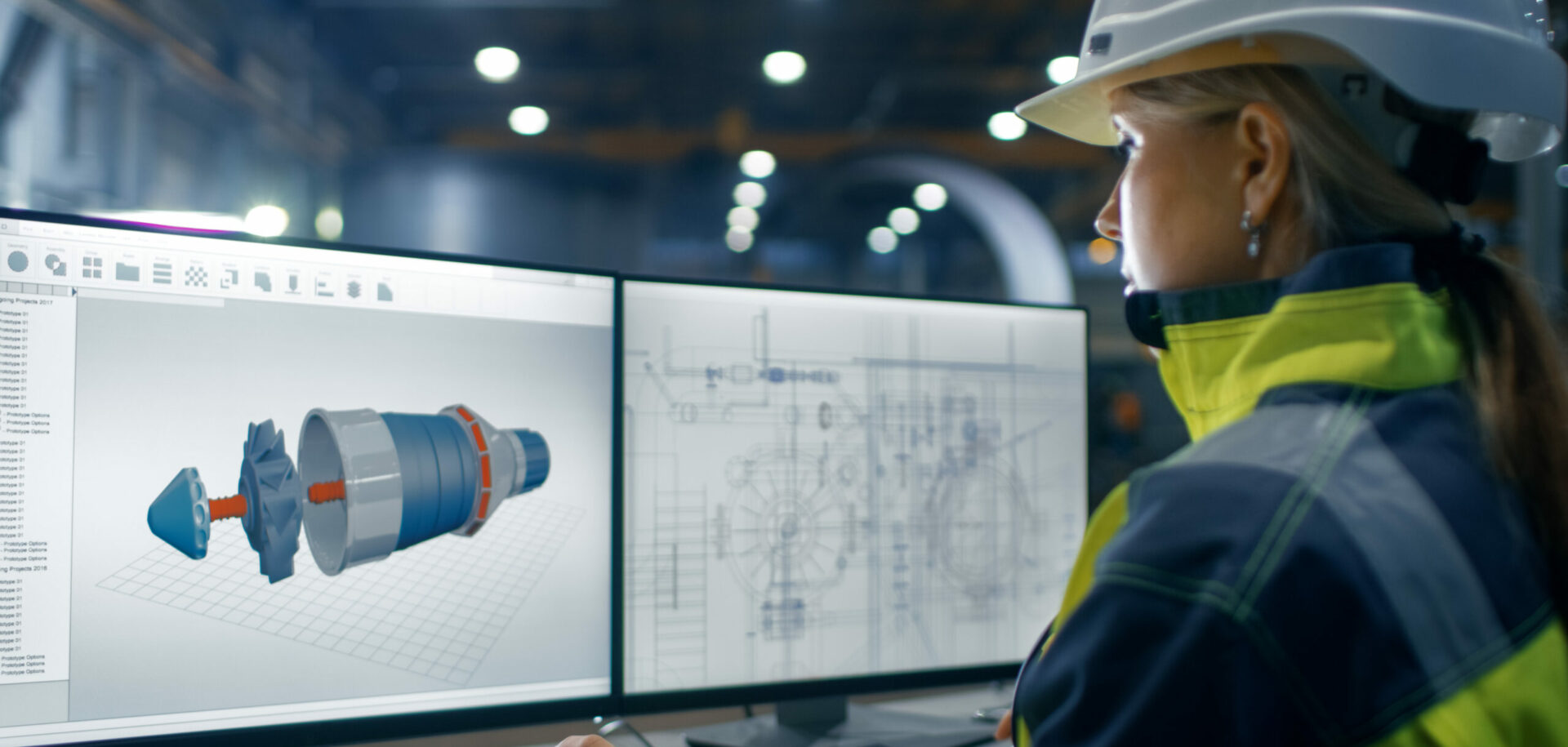
A mine with a mission
Summary
Feeling the vibrations
To minimise unscheduled downtime at its Mission Complex mining operations, Asarco Inc. employs a proactive maintenance strategy. Since early this year, Asarco has been testing SKF’s Copperhead system. This is a bearing system with optional services, specifically designed to monitor machine conditions in vibrating equipment.
Vibrating screens are key components in mine and quarry operations, where they are used to sift rock, aggregate and minerals during the milling process. The screens allow smaller material to pass through, while oversized rock is sent back for further size reduction.
Asarco is using an SKF Copperhead CPHD-4 fault detection kit, which is a package of sensors and an integrated MCM Unit – or Mechanical Condition Monitor – module. “The Copperhead sensors are mounted on the screen bearings. As the screen is operating, we take acceleration information and have software that will plot those frequencies,” says Asarco’s Charlie Carroll. With this information, it is easier to predict machinery faults before they can cause catastrophic damage.
“Bottoming out – a condition where material build-up under the screen causes damaging vibrations – is one of the problems SKF Copperhead can detect”, says Keith Meyers, SKF’s global engineering manager for mining and construction. “The system can also determine if a screen is overloaded and if a beam or the mesh of the screen is loose”, he says. “Lubrication distress in the bearings, gear damage and bearing damage are also detectable faults.”
SKF Copperhead uses a two-bearing system for longer service life and greater reliability. The first is the SKF Explorer spherical roller bearing for vibrating applications (VA405); the second bearing is either an SKF Explorer (VA406) or a CARB®.
Asarco – facts & figures
Asarco Inc has a history dating back to 1899, when several lead and silver smelting companies were consolidated under the name American Smelting and Refining Co. The name was changed to Asarco in 1975. In late 1999, the company, which includes mines, smelters and a refinery, became a wholly owned subsidiary of Grupo Mexico SA de CV.
Today, Asarco is one of the world’s leading integrated producers of non-ferrous metals, including copper, silver, lead, zinc, gold and by-product metals. Employing more than 400 people, the Mission Complex in Arizona operates around the clock, every day of the year. In 1999, the mine produced 90,000 tonnes of copper and 51 tonnes of silver from 74 million tonnes of extracted ore.
When Asarco Inc. mines copper ore at its Mission Complex in the midst of the southwest US desert, it’s a battle against both temperature and costs.In southern Arizona, the beauty of the deep blue skies and the seemingly endless landscape of subdued, yet rich, earthen hues belie what can be an unforgiving environment. The region, renowned for its Old West heritage and an intriguing mix of Native American, Mexican and Spanish influences, is a place where cactus is plentiful, the terrain is dusty and the air is very dry. In the summer months, when temperatures can reach the mid-40s °C, it is also unbearably hot.
This is the backdrop for the Asarco Inc. mining operations at the open-pit Mission Complex, 24 kilometres south of Tucson and about an hour north of the Mexican border. The mine is named for the nearby Mission San Xavier del Bac, an impressive and historic Franciscan mission dating back to the late 17th century. Asarco geologists discovered the Mission ore body in 1955 and began mill operations at the site six years later.
Today, the Mission Complex is a consolidation of five previously separate mining properties on more than 8,000 hectares of private, state-leased and Indian land. The most dominant feature is an immense crater-like open pit, large enough to hold a small town. Measuring 300 metres deep, it stretches 4 kilometres long and 2.4 kilometres wide.
Also at the site are an underground mine and two mills, each with separate crushing, grinding and flotation facilities that process a combined 55,000 tonnes of ore each day.
Mission’s end product – a copper concentrate that is sent to smelters for refining – represents 1 percent or less of the material removed from the mine.
A unique challenge
Unlike most other successful copper operations, the Mission mine has no ore from which copper can be extracted by solvent, or leached. “It is truly a disadvantage that we have here,” says technical services manager Charlie Carroll. “We are strictly a sulphide mineralised ore body.”
What this means is that, instead of going directly from ore to refined copper as is possible in a leach mine, Mission’s ore must go through added steps of grinding, flotation and smelting to achieve the same results. The extra steps add significantly to production costs.
Another complication is that the deeper Asarco digs, the harder Mission’s ore gets. “Staying competitive is even more important to us, because it’s more of a challenge,” says Carroll, a Texas native who’s been with Asarco since 1985.
Much of the large-scale earth-moving work in the pit is performed by electric shovels equipped with massive 47-cubic-metre buckets that can load a 270-tonne truck in just three passes. The trucks haul the ore to one of Mission’s two mills, where it is dumped into a primary crusher.
Like a giant mortar and pestle, the primary crusher noisily reduces the chunks of ore – up to 2.5 metres in diameter – to a top size of about 25 centimetres in a matter of minutes. Conveyer belts then transport the crushed ore either to a stockpile or directly to the secondary and tertiary crushers, which further reduce the ore to 1.25 centimetres or less in diameter.
“Then it goes into our grinding circuits, where we reduce that down to roughly the size of sea sand,” says Carroll. The point of all of this, he explains, is to liberate the copper minerals from the rest of the rock.
The next phase is flotation, which is repeated two or three times. Small quantities of organic chemicals are added to a watery mixture of the finely ground ore. These chemicals adhere to the surface of the copper minerals, so that when the mixture is agitated, bubbles carry the minerals to the top of the tank and over the edge.
After the last flotation, the product contains about 28 percent copper. “That’s our concentrate,” Carroll says. Although the percentage sounds low, Carroll says it is actually quite high. “The mineral we are floating is chalcopyrite. It’s a copper-iron sulphide mineral, and, chemically, that mineral is only 34 percent copper,” he says. “So, our concentrates are over 90 percent chalcopyrite.”
Preventive maintenance
Wherever possible, Asarco incorporates cost-saving technologies and maintenance techniques into the production process. “Certain bearing failures can cost us up to 25 percent of our production,” says Carroll. To avoid this, the company has a proactive maintenance strategy. Down periods are scheduled weekly for selected pieces of equipment.
Carroll estimates that, on average, 5 percent of Mission’s operating time is lost to maintenance, scheduled or unscheduled. Anything that can help him predict possible failures in advance saves him the time of emergency repairs. “Maintenance is a major cost, so you want to do it timely and correctly the first time you do it,” he says.
As with any natural resource, prices for copper are dictated by a global market. But for such a commonplace product, copper prices seem unusually low, especially when measured against production costs. Average copper prices in the first quarter of 2000 were 1,810 US dollars per tonne, an improvement from the USD 1,410 per tonne during the same time period one year earlier.
We have no control over the selling price of our product, so, by necessity, we are a cost-driven business,” says Carroll. In some cases, he says, Asarco can export its concentrates to countries like China, Japan and Korea, and have them smelted less expensively than it can in the United States.
Rounding out Asarco’s mining operations at Mission Complex is the company’s efforts to reclaim, restore or correct the effects of its copper concentrate production. Driving around the maze of dirt roads in the open pit, one often comes across 38,000-litre water trucks, which spray the mine roads. Automatic sprinkler systems as well as wet and dry dust collectors are also used at the mills to reduce the amount of dust released into the air. To promote re-vegetation on the mine’s tailings, or waste rock, cattle are allowed to graze to stimulate plant growth.
At current production rates, Carroll says there are almost 20 years of ore reserves left at the Mission Complex. “Then it’s done,” he says, “unless a cheaper technology comes along to make some of the more marginal ores economically mineable.”
Kathleen Saal
a journalist based in Atlanta, USA
photo Asarco