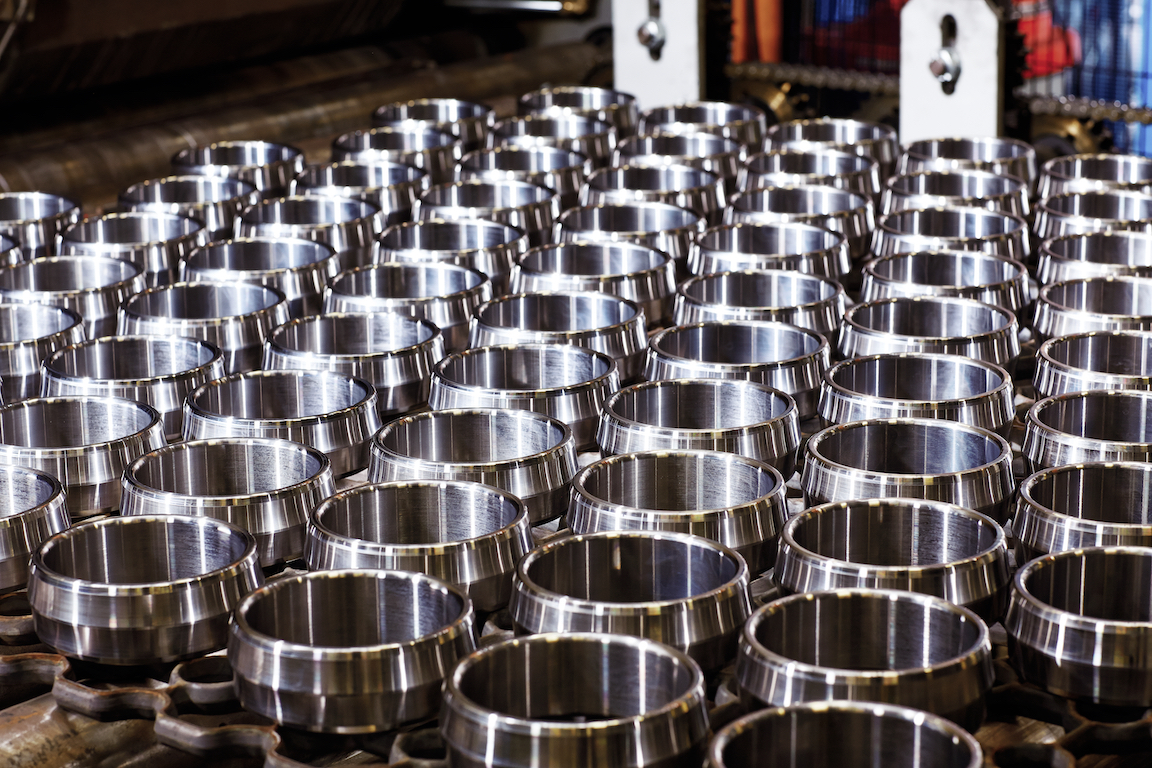
A packaging pro
Innovative packaging solutions, reliable machinery and the right kind of card are Horn Verpackung’s key to success.
Summary
Horn Verpackung in Wertheim, Germany, is one of SKF’s main packaging suppliers, providing the characteristic blue-and-red boxes for everything from mass-market bearings to bearings that weigh up to 30 kg. Factory manager
Rainer Lange estimates that 30 million boxes a year go to SKF. As part of its typical customer services, Horn, together with SKF, developed a unique heavy oil-resistant card that nevertheless could be glued, printed and folded.
Horn stores finished boxes at its plant and supplies them to SKF daily according to need. The two partners depend on each other, Lange says. “We rely on SKF to tell us accurately how many of each package they will use in a year, so that we can tailor production,” he says.
Packaging is not what you buy, but it may well be why you buy, and it may be the only reason the goods inside get to you at all.
Packaging must “package”: It must turn complicated shapes into uniform shapes that can be stacked; it must turn fragile items into robust items that can be transported; it must turn lots of items into a single item that can be hung on a hook and sold. A cardboard box may be just a folded piece of card with a top and a bottom, but it has to work perfectly in the packaging machinery. It must be economical and reliable; it must advertise and protect.
According to Rainer Lange, factory manager at Horn Verpackung in Wertheim, Germany, what makes his company special is its willingness to accept challenges. Whether a customer wants packaging fast or just-in-time, or whether a customer wants something new that no one has ever seen before – if it’s cardboard, Horn Verpackung will do its best to oblige.
Take the cleaning products manufacturer Vileda. It wanted to sell a fairly large piece of equipment – a mop – in a skin packaging. That means the product is put on a card that allows air through. A plastic sheet treated with adhesive is put over the product, air is sucked through the card, and the plastic sticks to the card where it doesn’t touch the product. The challenge for Horn was to find a card that was heavy enough for the mop but that still let air through. “Such a thing didn’t exist,” says Lange, “so we invented a three-ply card that let air through. And that’s why we’re now making millions of these backing cards for Vileda mops.”
Design first
Horn’s response to a packaging challenge starts with design. Stefan Koytek, design manager, has to create an effective box, which may include inserts to hold the product. Drafts will be created on the computer and realised on a plotter. And they don’t always work the first time. A bit of cardboard may stick, a tongue may not hold in a slot.
“When I started 16 years ago,” says Koytek, “we used to draw and cut everything out by hand. If something didn’t work, we had to go back and start again. Now, with the computer, I just change a measurement, and it’s done in a few minutes.”
Koytek sends box prototypes and plans to the customer, who adds the graphics. When it is finally approved, Koytek designs the tools that will stamp out the box shape and create the grooves along which the box will be folded.
But first the box must be printed. Horn has a 12-year-old Heidelberg Speedmaster CD 102 printing machine, which prints up to 13,000 sheets an hour with five colours and varnishes in one pass, as well as a 30-year-old MAN machine, which is slower but can take 100 x 140 centimetre sheets. Speed and reliability depend mostly on the quality of the card being used, says printer Richard Mark.
After printing, the card may be mounted on corrugated board and sent to a stamping machine. Stamping allows a flat piece of card to be turned into a functioning box, with folds already scored, slots punched out, tongues formed. Stamp operator Josef Stang points out that here too, the quality of the card is what makes the difference in the speed and reliability of the process.
Sticking together
Horn has two gluing machines: a Bobst that is 30 years old and a Saturn that is 15 years old. Both are still giving good service, due to the reliability of the equipment. The Bobst has been fitted with additional computer-controlled units allowing glue to be applied with up to six nozzles at once, as well as from a dispenser underneath. The machines fold the boxes automatically and press them together so that the glue sticks. Boxes, neatly folded flat, ready for opening and filling, are stacked into cartons ready for transportation.
“Every order is different,” says Lange. Each box requires a new setup for all the machines it goes through, and so pricing is dependent on the length of production runs. “We do any quantity from 50 to 3 million,” he says, “and each box can cost between two cents and 50 euros.” Current production is about 80 million items a year; turnover is EUR 8 million.
Horn is in the process of moving to new premises, which will give the company greater efficiency and flexibility.
———————————————THE NITTY-GRITTY
Horn Verpackung’s machines are packed full of SKF bearings, with 1,400 in the Saturn gluing machine alone. The bearings are mainly used to guide the sheets through the system, and, says factory manager Rainer Lange, although the demands made on them are not very heavy, they have to be reliable. SKF bearings offer high precision and rigidity, enabling top-quality printing at high speeds, in keeping with the high standards that are Horn’s trademark.