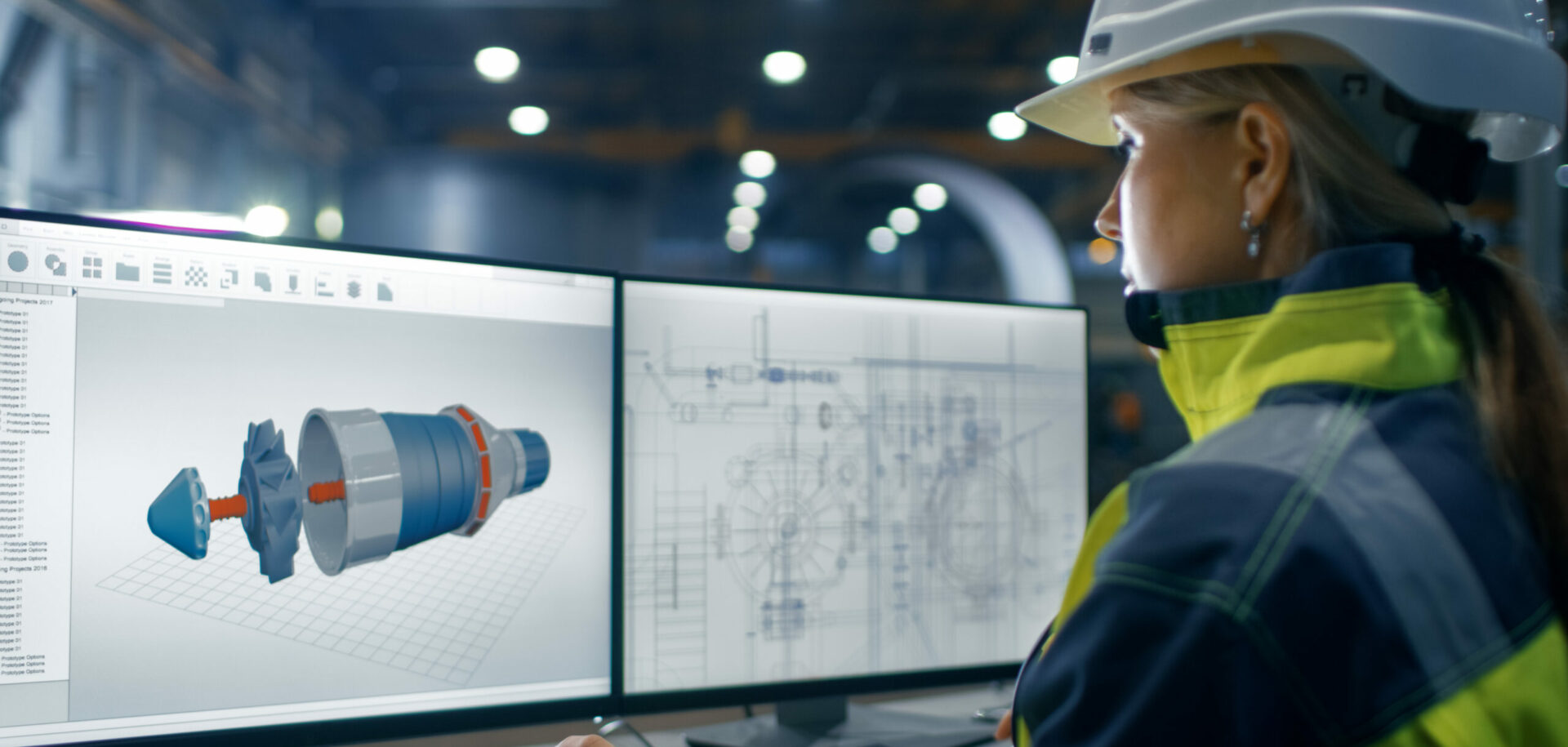
A quest for quality
The Uralelectro electrical engineering plant in Mednogorsk is situated at the foot of the Ural mountains in Russia, but its products travel far and wide, to companies in Italy, France, Germany, Spain and elsewhere.
The Uralelectro electrical engineering plant in Mednogorsk is situated at the foot of the Ural mountains in Russia, but its products travel far and wide, to companies in Italy, France, Germany, Spain and elsewhere.
Geographically speaking, Mednogorsk is situated practically on the boundary between Europe and Asia. Administratively, it is in the depths of Russia, two days’ journey from Moscow. But in terms of industry Uralelectro is a major engineering centre, accounting for about 30 percent of the Russian small and medium-size electric motor market.
Uralelectro plans to produce some 250,000 electric motors this year. Each week neat rows of bright blue motors – “gift-wrapped” in polythene, corrugated cardboard and wooden crates – are loaded into trucks and dispatched to far-flung destinations.
In fact, 60 percent of the factory’s output is exported. One of the company’s largest and most important clients is in Italy.
“We believe that the situation is going to change,” says chief engineer Alexander Tsarkov. He started work at Uralelectro 26 years ago, when he was just out of Moscow University, and is an expert on its products and their capabilities. “We believe that the domestic market has the greatest long-term potential, which is why we are aiming to increase sales in Russia.”
“After perestroika [Mikhail Gorbachev’s programme of economic, political, and social restructuring that led to the break-up of the Soviet Union], in the early ’90s, when the borders were opened to trade, the plant management realized that we couldn’t compete with foreign manufacturers if we didn’t improve the quality of our products,” Tsarkov says. “We came to the unanimous conclusion that if we couldn’t do something very well, we shouldn’t do it at all.”
It was this ambitionto be the best that drove Uralelectro to decisive action. Over the past six years, the company has upgraded a third of its manufacturing equipment. The plant now boasts machines manufactured in Sweden, Italy, the United States and Germany as well as by Russia’s best machine-tool engineering plants. Since 2003, the quality system has been certified to the ISO 9001:2000 standard. In addition to improving quality, motors with shaft sizes from 63 to 132 mm were introduced, thereby covering the entire range of medium-capacity electric motors, from 0.18 kW to 7.5 kW.
“One of the main requirements made by our European clients was that we use SKF bearings in our electric motors,” says Tsarkov. “To meet this demand, we signed a contract with SKF in 1998.”
Today Uralelectro is one of SKF’s leading Russian customers. With SKF bearings, Uralelectro’s products now meet European standards, and exports have doubled.
“The fact that SKF manufactures high-quality bearings isn’t the only reason for our collaboration,” Tsarkov explains. “SKF has a professional approach to its work. We have established good relations with one another.”
Uralelectro’s concernis not only to shift units. It works in consultation with its customers, helping them to get the most out of their products. Uralelectro’s engineers are constantly searching for ways to improve their electric motors, making them safer and more environmentally friendly. SKF is one of Uralelectro’s reliable partners in this. For example, in February engineers from both companies met in Uralelectro’s laboratories to conduct a comparative analysis of diagnostic methods used by the two companies.
“We hope that SKF’s recommendations will help
us to find optimal solutions to a number of technical issues,” Tsarkov says. “Now we have succeeded in producing the entire range of small to medium size electric motors, which means we can operate on the principle ‘everything under one roof.’ My job now is not to lose the position we have gained and to remain competitive with other manufacturers in Ukraine and Belarus. And our main byword is ‘high quality.’”