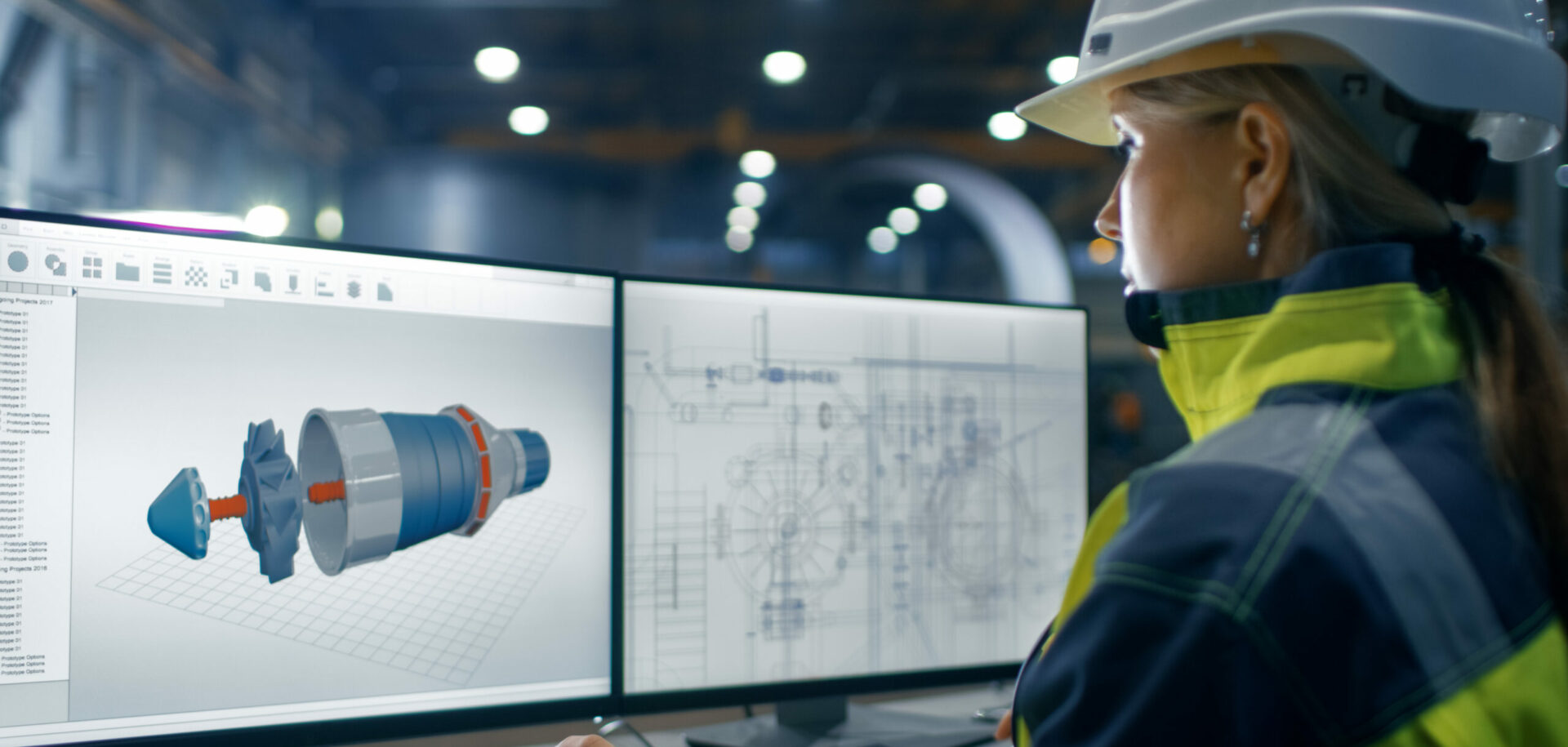
A Smashing Idea
Summary
The SKF Connection
SKF New Zealand and Barmac recently celebrated the manufacture of 1,000 bearing cartridges over two Barmac models.
SKF helped design the original Barmac bearing cartridges in the 1970s, and has become re-involved with the company over the past 10 years.
That original bearing cartridge design has remained fundamentally unchanged. SKF supplies one cylindrical roller bearing and one deep groove ball bearing per machine. This includes bearing types NU320, NU2212, NU2320, NU2326 and 6312, 6315, 6320 and 6326.
SKF New Zealand’s sales and marketing manager, Steve Haines, says that SKF works very closely with the Barmac manufacturers. “This involves close coordination in areas such as inventory management, staff training in bearing fitting and analysis of bearing failure and the like,” he says.
“SKF New Zealand’s engineers also work closely on the Barmac cartridge design and have worked on projects to improve bearing lubrication and to minimise the risk of bearing failure.”
Metso Minerals makes a rock crusher that today can be found on some of the world’s high-profile engineering projects. Timothy O’Brien reports.From the deserts of the Middle East to the oil fields of the North Sea and the massive Three Gorges dam project on China’s Yangtze River, civil engineering projects depend on the Barmac, a rock-crushing machine made by Metso Minerals Ltd in the small New Zealand town of Matamata. The Barmac is used all over the world. In addition to crushing rocks for road surfaces and concrete mixes, it can also be used for applications in mining and recycling industries.
What has made the Barmac particularly adaptable to these applications is its method of crushing and shaping stones.
The Barmac operates at the tertiary end of the rock-crushing spectrum, which means it crushes stones of less than 50 millimetres. Its special feature is that its crushing method is “autogenous” or “self-generating” – the stones crush themselves against each other.
Allan Wiles, who is manufacturing manager at Metso Minerals in Matamata, says the beauty of the Barmac is that it can be set to deliver exactly what you want.
“By changing the speeds and the feed control of the rock going in, you govern what comes out the bottom end,” Wiles says. “If you want ‘fines,’ or road chip or railway ballast, there’s quite a range there. It goes down to sizes measured in microns to make dust for paint.”
Cost-efficient
Because the rock crushes itself, the machine is also very economical to run in terms of wear. “Our wear costs can be as little as onetenth of those in competitive machinery,” Wiles says. The Barmac was designed with only one thought in mind – to provide a straightforward solution to a straightforward problem.
This problem was the shape of the aggregate in the concrete being poured into high-rise buildings in New Zealand’s capital, Wellington, during the building boom of the 1970s. The local stone tended to make a very sharp edge when crushed and was wearing out the concrete pouring tubes at an alarming rate.
Jim MacDonald was a Wellington city engineer at the time. Using the idea that stone against stone would break itself and aware that stone linings had been used to reduce machine wear in quarries for years, MacDonald created a vertical rock-crushing system in which rocks were poured into a rotor from which they were flung into a rock-lined chamber. The continuous motion of the stones against each other created the crushed product.
MacDonald worked on the invention with colleague Bryan Bartley, who provided the technical contribution that extended the operating time to make it commercially viable.
SKF was also involved closely at the beginning in assisting with development of the bearing cartridges – a crucial consideration when you have a rotor spinning at speeds up to 2,500 revolutions per minute.
In good shape
The Barmac was a significant development not only for its autogenous method of crushing rock, but also for the shape of what it produced.
In the Barmac process, the resulting particles have a cubical shape, and this makes the Barmac’s output very desirable for use as aggregate in concrete and other mixed materials.
This shaping has helped the Barmac achieve some of its greatest successes. Andi Lusty, managing director of Metso Minerals (Matamata), says the way the Barmac shapes stones and sand leads to a very high-strength concrete.
For example, the machine is used to make sand in desert areas of the Middle East. “Natural sands may not have a lot of fine material, and stones may lack the angularity. That affects the density and strength of the concrete mix, and that’s the main problem the Barmac can resolve,” Lusty says.
The Barmac also means large cost savings, Lusty says, and explains that by using Barmac-generated material, the minimum concrete strength requirements for highways in the United States can be achieved with significantly less cement than used in standard methods.
“In places like Japan where high-strength concrete is very important because of earthquakes, there are probably more than a thousand machines operating,” Lusty says.
Barmac on the Yangtze
One of the most massive civil engineering projects in the world today is the Three Gorges project in China, where massive hydroelectric dams are being built to control the Yangtze River. “Strength and density of concrete is extremely important in dam construction, and the Three Gorges project needs a very high specification of sand,” Lusty says. “We’ve got four Barmacs going full time in the project.”
Other projects show the Barmac’s versatility.
“You can describe the machine’s action as a scrubbing one, almost like a washing machine,” Lusty says. “That’s a useful image because the Barmac is also being used in the extraction of precious stones such as diamonds and opals.”
The Barmac is well suited for this, says Lusty, because, unlike conventional crushers, it doesn’t carry a high risk of destroying the stones being extracted.
Offshore oil
The Barmac is also being used in the North Sea oil fields.
“The Barmac was a solution to two problems,” Lusty says. “The stone residue produced in the drilling process was radioactive and so created a disposal problem. At the same time it was not possible to extract all of the oil by normal methods, but pumping replacement material into the wells lifted extraction significantly.”
Lusty says attempts to crush the radioactive material so it could be pumped back into the wells failed until the Barmac was used.
“It was the only machine that made a smooth enough product that didn’t resegregate in the pipes,” he says. “By crushing the stone and mixing it with sea water, the Barmac allows the on-site radioactive material to be used as the replacement fill, which increases the well’s productivity.”
Timothy O’Brien
a freelance journalist based in
Wellington, New Zealand
photo Metso Minerals