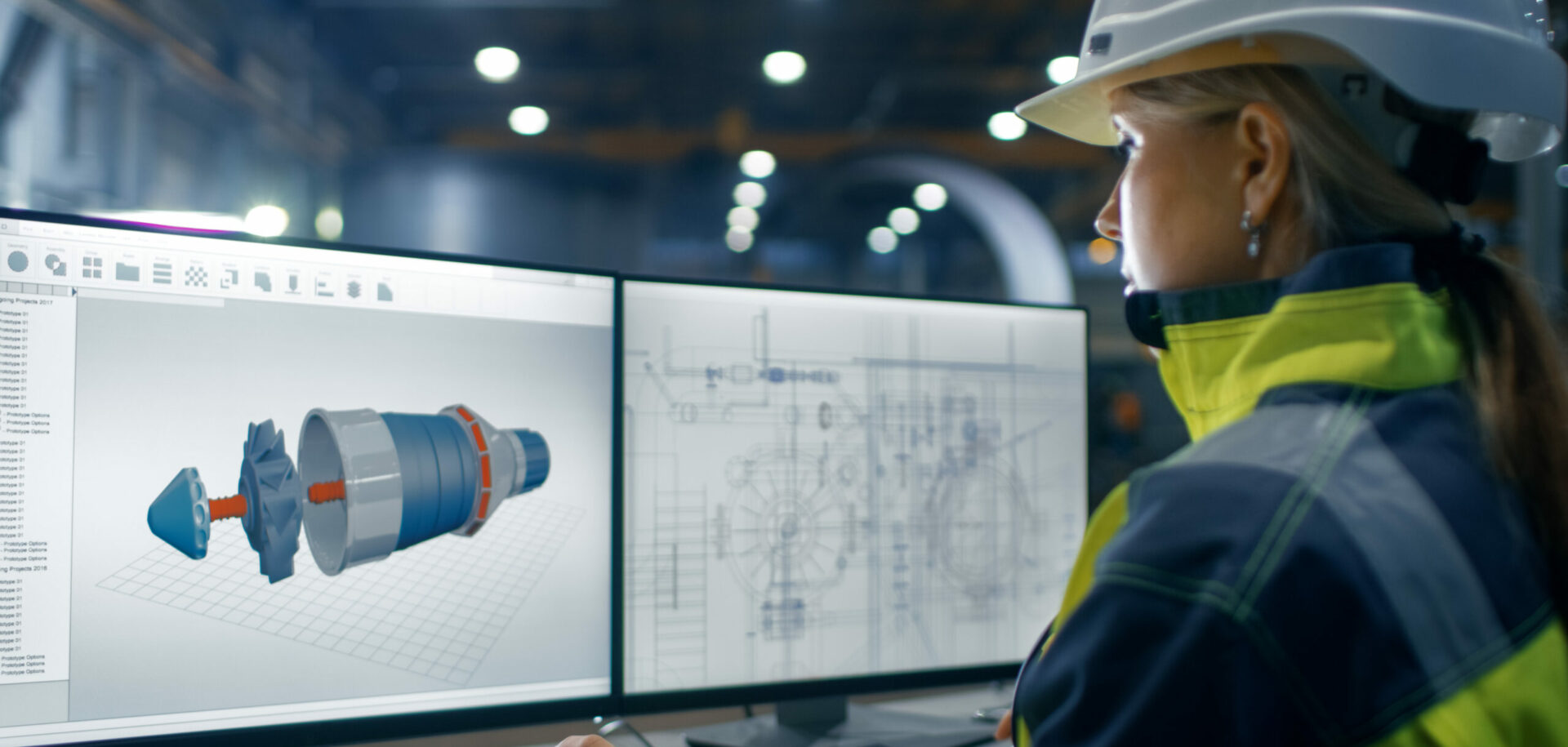
Toujours là où il faut
SKF Lubrication Systems fait confiance à Spandau Pumpen pour le refroidissement des machines-outils de son usine en République tchèque.
Pour obtenir une qualité élevée à moindre coût dans le domaine du travail des métaux, la fiabilité du refroidissement des machines-outils est essentielle. Dans l’usine SKF Lubrication Systems de la ville tchèque de Chodov, des pompes de refroidissement Spandau Pumpen (Fig. 3) ont été déployées au sein du processus d’usinage et sur un îlot de filtration modulaire (Fig. 1) intégrant un convoyeur de copeaux. Leur installation s’est traduite par une amélioration de la fiabilité et une baisse des coûts d’énergie et de production.
Spandau Pumpen
L’usine SKF de Chodov fabrique, entre autres, des distributeurs progressifs pour systèmes de lubrification. Les problèmes étaient fréquents sur l’ancienne ligne de production. Des outils à refroidissement interne subissaient des blocages répétés dus à la saleté. De plus, sur les machines relativement lentes, des solutions à station unique étaient utilisées comme dispositifs de filtration. L’équipe de projet Technologie de fabrication de SKF, sous la direction de Steffen Siegemund basé en Allemagne, s’est vue confier la mission d’améliorer la flexibilité et la qualité de la production de l’usine de Chodov tout en réduisant les coûts. Il a alors été décidé d’investir dans des centres de fraisage mono-broches rapides.
Pour déterminer comment gérer efficacement les copeaux et récupérer le fluide de refroidissement afin de le réinjecter dans le process de production, l’équipe de projet SKF et le service Achats du Groupe ont fait appel à Mayfran GmbH d’Aix-la-Chapelle, en Allemagne. Avec l’aide de spécialistes des systèmes de convoyage de copeaux et de filtration, ils ont évalué et comparé les avantages et inconvénients des différentes solutions, à station unique et îlots, et de l’alimentation centralisée. La décision a finalement été prise d’opter pour un système en îlot modulaire avec convoyeur de copeaux. Cette solution a donné pleine satisfaction à Steffen Siegemund et son équipe : « Avec l’aide de Mayfra, nous avons réalisé ce projet avec succès. »
Le système de filtration (Fig. 2) dessert deux lignes de production qui comptent chacune trois machines-outils, ① ② ③ et ④ ⑤ ⑥, ainsi qu’une solution à station unique ⑦. Ce système prend en charge le nettoyage à plein débit avec un seuil de filtration des copeaux de 25 µm, puis une seconde étape de filtration fine de 5 µm (filtration en bypass) avec un filtre papier hydrostatique ⑧. Le filtrat issu de ce process est recueilli dans la cuve ultra-propre ⑬. Le système est équipé d’une seconde cuve de protection et répond aux exigences de la loi fédérale allemande sur l’eau (WHG). Il comprend également un refroidisseur à immersion ⑨ avec une unité de commande puissante. L’usine SKF est ainsi prête pour une augmentation de la production et, si besoin, ce système de refroidissement pourra être utilisé en ligne pour maintenir le fluide de refroidissement à une température de process constante.
Assistance en interne
Il manquait encore la dernière pièce : le fabricant de pompes. C’est au sein même de SKF que l’équipe de projet l’a trouvé. Spandau Pumpen, basé à Berlin, fait partie du Groupe SKF depuis 2004. Cette entreprise développe et fabrique de puissantes solutions d’alimentation et de refoulement centralisés et de préparation des fluides pour machines-outils. « Spandau Pumpen est une marque indépendante du Groupe SKF ; la décision de s’appuyer sur des produits conçus en interne a été facile prendre », explique Martin Zverina, directeur de l’usine de Chodov.
Spandau Pumpen a ainsi fourni trois pompes basse pression série PS (b) et trois pompes haute pression série LMP (c), toutes équipées de convertisseurs de fréquence, pour la solution en îlot modulaire avec convoyeur de copeaux. Un convertisseur de fréquence a pu être facilement installé sur les moteurs existants, des modèles standard du commerce, par le biais d’un adaptateur. Les pompes équipées de convertisseurs fonctionnent en parallèle, ce qui réduit la complexité des commandes et améliore la fiabilité de fonctionnement. Certains composants sont redondants pour éviter les pannes. Le processus de nettoyage suit toujours le même schéma. Les pompes de rinçage Spandau PSH (a) refoulent le fluide contaminé par l’usinage depuis les machines-outils vers le système de filtration.
Le fluide clarifié et réutilisable est envoyé dans la cuve ⑫. Les pompes PS (b) prélèvent ensuite sous basse pression ce fluide filtré dans cette cuve, tandis que les pompes à vis LMP (c) réacheminent sous haute pression le filtrat fin vers les machines en vue de sa réutilisation (Fig. 2).
Des pompes de rinçage PSR (d) nettoient les éléments filtrants du système de filtration ⑩ ⑪. Les pompes PMS (e) transvasent le fluide du réservoir collecteur par sédimentation vers les éléments filtrants ⑩ ⑪.
Du fait du contrôle en parallèle des pompes, avec fonction maître, celles-ci fonctionnent toujours à la demande. Elles sont soumises à une charge uniforme, ce qui se traduit par une longue durée de service. Le système alimente les machines raccordées avec la juste quantité requise de fluide de refroidissement. La commande maître ou la commande alternative garantit un temps de fonctionnement homogène des pompes individuelles. Comme les pompes de process ne doivent pas toutes fonctionner tous les jours, une pompe maître différente est sélectionnée toutes les 24 heures, de sorte que tous les composants sont soumis à des niveaux d’usure pratiquement identiques. Le bon fonctionnement des pompes redondantes est régulièrement contrôlé.
Les capteurs installés dans les tuyaux mesurent la pression du process pour la transmettre en temps réel au convertisseur de fréquence. Celui-ci contrôle ensuite la vitesse de rotation des pompes de manière à maintenir un niveau de pression constant. Aucune commande de dérivation n’est nécessaire puisque les besoins supplémentaires en énergie et la transmission de chaleur au fluide de refroidissement sont ainsi évités.
Efficacité et puissance pour de faibles coûts de maintenance
L’adaptation automatique de la vitesse assurée par le variateur de fréquence permet également de compenser la possible baisse des performances due à l’usure des broches ou rotors. Le point de travail souhaité reste ainsi sous contrôle et le système est préservé de tout arrêt imprévu. La nécessité d’une réparation est détectée suffisamment tôt pour permettre la planification de l’intervention de maintenance. La mise en route en douceur du système grâce à la technologie des variateurs évite les pointes de pression. Des composants, comme les raccords, tuyaux et filtres, sont ainsi préservés et la durée de service de l’ensemble du système s’en trouve allongée. Chodov a vu ses coûts d’exploitation nettement diminuer.
Ce système est en outre particulièrement économe en énergie. « Sur la base des relevés de consommation et des volumes d’usinage, nous avons calculé que la consommation représentait seulement 40 % de celle d’un système à station unique », explique Martin Zverina – soit des économies d’énergie de 60 % (Fig. 2). De plus, quatre pompes de rinçage (série PSR) ont été intégrées au système pour le nettoyage des filtres, et deux pompes (série PMS) pour le refoulement des résidus. Deux pompes de relevage (série PSH) ont été installées dans les stations de pompage latérales des convoyeurs de copeaux (Fig. 4). Avec cette configuration, l’usine SKF est équipée de façon optimale pour répondre aux besoins.
Le système de filtration présente une conception modulaire évolutive. Il peut être complété par la suite en fonction des besoins. Le système de filtration en îlot est également flexible pour s’adapter à l’application des machines. Ce type de système peut continuer à être utilisé si, par exemple, un centre de rectification ou une autre ligne de fraisage est ajouté(e) à Chodov. Le seul élément à modifier dans ce cas serait la qualité du filtre.
La solution de Spandau Pumpen a fait grande impression dès le début auprès des responsables de Chodov. Ils ont été séduits par les courtes périodes de maintenance et la disponibilité élevée offerte pour des machines qui tournent nuit et jour. SKF avait insisté sur le fait que le process soit entièrement automatisé à Chodov. L’idée de paniers nécessitant un entretien manuel à l’avant des pompes de relevage a ainsi été écartée. Des composants comme les éléments filtrants associés ont été spécialement conçus pour ce projet.
Capacité de réserve pour d’autres machines
Le directeur de l’usine, Martin Zverina, souligne que la fiabilité d’usinage s’est nettement améliorée : « Nous sommes très satisfaits des performances de l’ensemble du système, et en particulier des pompes Spandau (Fig. 5). Elles fonctionnent 24 heures sur 24, sept jours sur sept, et alimentent en fluide de refroidissement sept machines critiques dans notre zone d’assemblage mécanique avec une grande fiabilité. La capacité restante dans les plages de basses et hautes pressions nous permettrait de raccorder encore deux autres machines. Grâce aux solutions Spandau Pumpen, l’usine SKF de Chodov est positionnée stratégiquement pour affronter l’avenir. » Si d’autres zones de production doivent être converties à un concept similaire, un autre système en îlot peut être installé et utilisé comme réseau de refroidissement. « La conception modulaire permet à tout moment d’adapter le système aux besoins », souligne Martin Zverina.