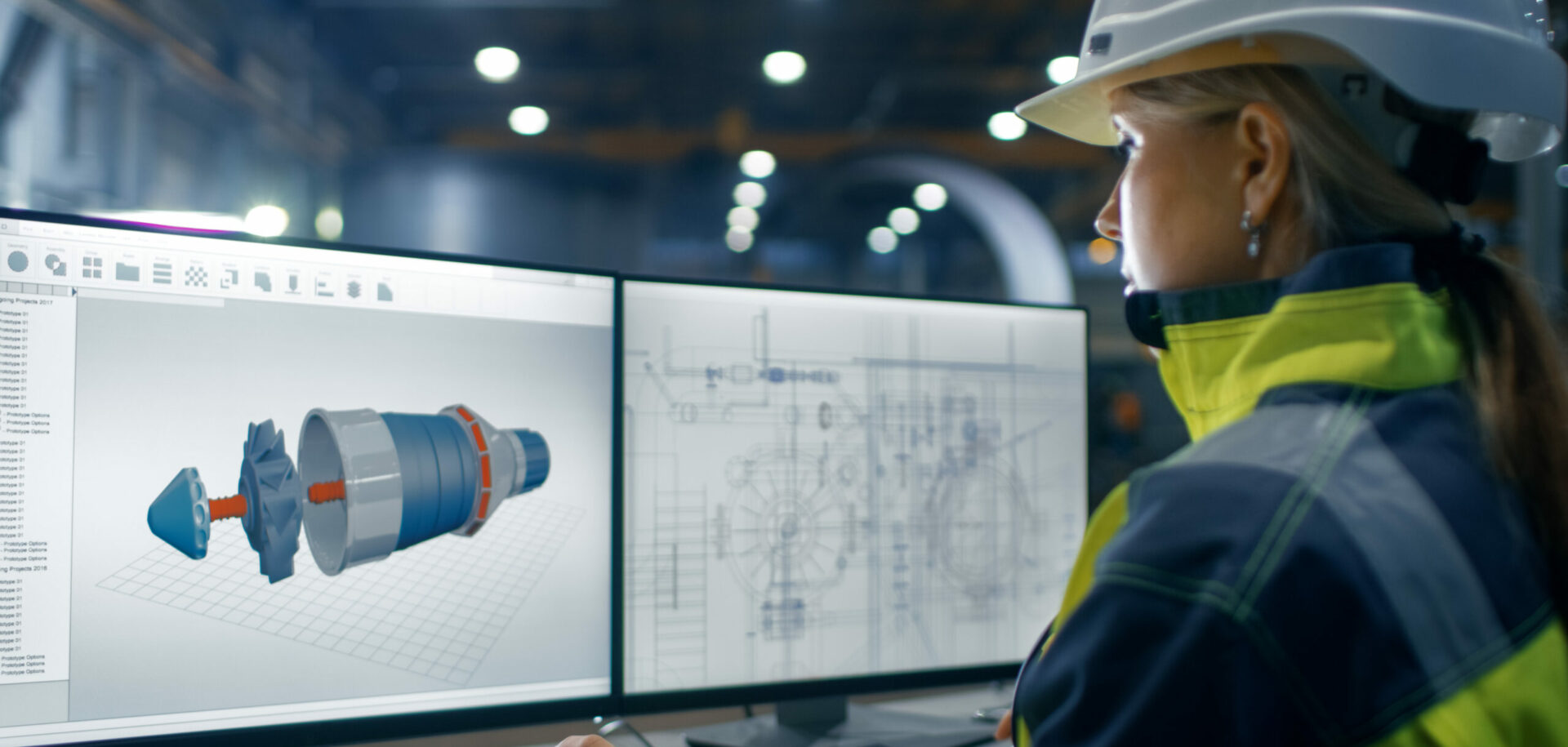
At the cutting edge
If you spend roughly half a million euros on a saw, you can expect something special. The Precision Wafering Systems division of Applied Materials Inc. makes wire saws to cut silicon into thin slices for use in photovoltaic cells.
The industry that turns sunlightinto electricity is booming. Growth has been around 30 percent a year for some time, and the trend looks likely to continue. There are many reasons for this. In contrast to fossil fuels, sunshine is an inexhaustible resource. It is environmentally friendly and freely available everywhere, and it does not have to be transported through pipelines or over the ocean from unstable or potentially hostile countries.
And because of the economies that manufacturing on an ever-larger scale make possible, and of research and development efforts that are producing improvements in the efficiency of photovoltaic (PV) cells, the price of electricity generated by the cells is steadily improving. Industry insiders forecast that it will come down to fossil-fuel levels by 2010 in some parts of the world. Government subsidies in some countries are also a powerful encouragement for the industry.
A photovoltaic module – “solar panel” is the more popular term – is made up of many PV cells that are electrically connected. Several solar panels – maybe hundreds – may then be connected to larger units, known as arrays. The main component in each cell is a thin sliver of silicon, sliced by a wire saw from a large ingot of the material, somewhat like toast sliced from a loaf – except that a silicon ingot can weigh up to 400 kilograms and is extremely hard and brittle. Cutting a hard, brittle substance into very thin slices is a tricky business.
After oxygen, raw silicon in the form of sand and quartz is the most abundant element on earth. However, to meet the needs of the solar-power industry it must first be refined – an expensive process. Solar-grade silicon has been in short supply for years, and prices have rocketed from around 9 US dollars (6 euros) per kilogram in 2000 to around 200 US dollars (135 euros) per kilogram in autumn 2007. This forces all the players in the industry to squeeze ever more energy out of every gram of silicon.
One way to achieve this is to raise the cost-effectiveness of the slicing operation, which is an essential step in the manufacturing process. Solar cell makers are clamouring for high-performance wire saws that cut ever thinner slices, cut them ever faster and with less kerf loss.
Precision Wafering Systems (PWS) is an industry pioneer and world leader in developing and making advanced wire saws to slice silicon for the photovoltaic and semiconductor industries and to cut other hard, brittle materials such as glass and quartz. Based at Cheseaux, near Lausanne, Switzerland, PWS was known as HCT Shaping Systems SA until it was acquired by Applied Materials Inc. in August 2007.
“The principle of a wire saw is simple, but its execution is challenging,” explains Cédric Thommen, mechanical engineering manager at PWS. “In these machines a very thin wire made of high-tensile-strength steel is wrapped around a series of wire guides, creating a web. The wire is 120 or 140 microns (µm) thick. That’s somewhat more than an average human hair. “
“The wire guides rotate rapidly, driving the wire web at about 15 metres per second,” Thommen continues. “As it moves, the wire is continually wetted with an abrasive liquid. A silicon ingot is pushed down through the web, and the moving wires slice the ingot into wafers. Today, wafers are between 150 µm and 300 µm thick, typically about 200 µm. PWS is developing wire saws using finer wires that are more closely spaced, so the next generation of our equipment will be able to slice thinner wafers and produce even lower kerf losses.”
Thommen points out the major features of PWS wire saws. “These high-precision machines are designed to achieve a very high degree of mechanical linearity, thermal stability and process consistency,” he says. “Their maintenance requirements are low, and reliability and uptime are high. These characteristics, along with low-cost consumables and high productivity, achieve unmatched cost-effectiveness for our customers.”
PWS, which employsmore than 200 people in Cheseaux, also makes croppers and squarers for the photovoltaic and semiconductor industries. These machines use the same basic wire-saw technology as the slicers but with a different configuration for the wires. Croppers slice tops and tails – industry jargon for ends and sides – of large silicon ingots, using a crimped wire instead of the straight wire of the wire saws. Squarers saw ingots into columns of square cross sections. Both machines serve to prepare ingots for slicing into wafers for solar cells or, in the case of the semiconductor industry, for cutting into tiny chips for electronic equipment.
Partners in excellence
In its machines, Precision Wafering Systems (PWS) relies on components that match its lofty overall standards. “Our motto is ‘Excellence is a mindset,’” says Thommen. “We only work with suppliers that share this aspiration. SKF supplies us with various bearing types for different applications in our machines, including the critical ones on which the wire guides rotate.”
There is more, however, to the cooperation between PWS and SKF than high product quality. “We expect total reliability from our suppliers in all aspects of their business relationship with us, such as deliveries and worldwide product availability,” Thommen continues. “SKF not only meets but exceeds our expectations. We have their in-depth support at all stages of machine design. They recommend the optimum bearing selection, and provide us with all bearing-related information and calculations such as bearing fits and bearing life. These are all extremely important concerns for us because bearings play a vital role in helping to minimize the need for maintenance and increase uptime and reliability in an expensive piece of high-tech equipment. In fact, SKF practically acts as a specialized engineering consultant to us.”