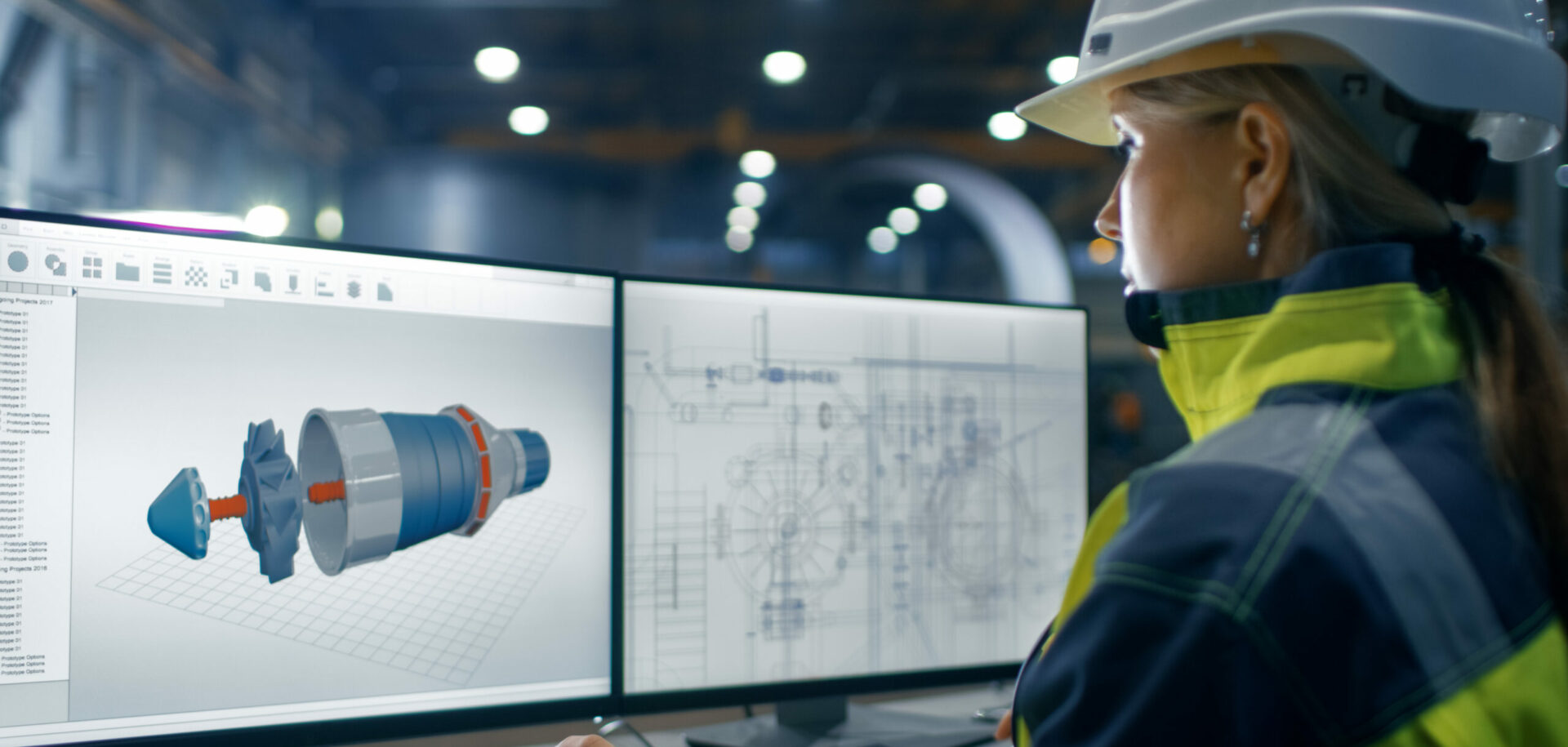
Summary
Tapers inside
SKF has often been the supplier of choice for BPW since the advent of the SKF-Norma axle of 1923, and was closely involved with the development of the ECOPlus hub. SKF supplies almost all the 33213 (65 x 120 x 41) and 33118 (90 x 150 x 45) taper roller bearings that are used in the hub. These standard bearings are also readily available throughout the world so that truck drivers need never be stranded for long.
Axles have been the business of BPW Bergische Achsen KG since 1898. Today the company keeps tractors and trailers rolling all over the world.The BPW Bergische Achsen KG factory lies stretched along the valley of the Wiehl River in the hilly country near Cologne, Germany, marking the spot where the company was started more than 100 years ago. When the Kotz family founded the company in1898, water from the Wiehl was what powered the hammers in the smithy that made axles for the horse-drawn farm trailers. In those days, BPW made and sold axles locally; it was only when the railway came snaking through the valley that BPW began to sell its products beyond its own region.
Now BPW is one of the world’s largest makers of axles for drawn vehicles. It still makes axles for farm trailers and other light applications, but now the largest part of its production is devoted to axles for heavy road trailers and semi-trailers – the workhorses that transport the goods of the world. BPW delivers a quarter of a million such axles a year, manufactured in its factories in Hungary, Italy, China, South Africa and Australia, as well as in several locations in Germany.
A company of such international scope is expected to set standards. BPW employs more than 100 engineers, who help ensure that it remains in the technological forefront of the industry. Its publicity boasts of 2,500 product innovations and 400 patents. Indeed, the company started operations with a patent axle design featuring permanent oil lubrication. And since then, innovation has been a continual part of the company culture.
A fruitful union
The company really took off in 1923, when it joined with SKF-Norma to make the first trailer axle with a tapered roller bearing, says Rupert Habersatter, BPW head of marketing. Until then, trailer axles used plain bearings, which had to be lubricated every week or so. The 1923 axles were revolutionary, providing in one move an increase of 50 percent in load for the same traction power and a decrease of 80 percent in lubricant and 10 percent in fuel. The new axles allowed higher speeds, because the roller bearings remained cool longer. And they only needed one lubrication a year.
Ten years ago, BPW developed its ECO hub. The main feature was a hub in which the bearings and the thrust washer could be removed together from the axle by releasing one central nut. At the same time the different parts of the hub, such as the bearings or the seals, could be exchanged individually. The development was taken up enthusiastically by the industry.
Jörg Ebert, BPW’s technical director, says that when he came to the company in 1996, he spent six months observing the market before proposing a new product for BPW. In January 1997, development started on what was to become the ECOPlus hub. “The aim,” says Ebert, “was to produce a hub that required even less maintenance than the ECO hub but that continued to allow for easy replacement of parts, should something go wrong.”
“We have our own test stand for bearings,” Ebert continues, “and we are the only company in the world whose main business is not the manufacture of bearings that can say that.”
But testing goes beyond the test stand. BPW tested the new hub in a dusty quarry in Australia and in deep snow in Scandinavia. It was driven through rivers, and, most important, put repeatedly through shunting manoeuvres that are known to stress a trailer axle.
“Carrying a load of tomatoes from the south of Spain to the north of Denmark on the motorway is a straightforward task,” says Ebert. “It’s the shunting at the end of the trip that puts the strain on the axle.” As the trailer is manoeuvred into position, the wheels often have to turn on the spot, creating stress on the hub.
Added to the stress of such manoeuvres are factors such as mud and washboard-like road surfaces. And trailers simply aren’t maintained as well as trucks. A tractor is expected to last about five years, but a trailer may be in service for 15.
The solution to all these problems was presented in November 1999. BPW had tried SKF’s range of Truck Hub Units, but decided to go with a solution that fitted into the traditional construction principles of the company. BPW engineers designed a BPW unit that uses standard DIN-ISO tapered roller bearings that can be bought from any good workshop, should something go wrong on the road.
The bearings, says Ebert, are generously dimensioned; there’s plenty of space, and the assembly is filled with special high-pressure grease developed by BPW together with an oil company. The dimensions ensure that the hub is less likely to overheat, even with disc brakes. BPW’s multiseal system makes sure the dust stays out and the grease stays in.
Bearing preload
A critical parameter for the life expectancy of the hub is the bearing preload. Increasing or decreasing bearing preload outside a narrow range results in reduced bearing life. With the ECO hub, the maintenance engineer had to tighten the axle nut to a precise torque and insert a split pin at an awkward angle to secure it.
The ECOPlus features a ratchet and spring washer system that ensures that the nut can only be tightened to a particular torque. After that, the ratchet takes over. And the split pin has gone too. A small wedge is pushed straight in and fastened with a ring. “We tried lots of complicated methods until we came to this solution,” says Ebert, “but simple is often best.”
The concept of the ECOPlus is “maintenance-free, but fully serviceable.” That means that the hub should never need adjustment or repair, but if maintenance is required, it can be carried out with normal workshop tools. The same principle applies to the new Airlight II suspension system, which also has the advantage of saving 25 to 31 kilograms on each axle, compared with earlier systems.
BPW is so confident of its ECOPlus hub that it is prepared to offer a five-year Europe-wide guarantee on its axles for on-road applications, without any mileage limits. “After all,” says Ebert, “it’s not the mileage but the manoeuvring that causes the problems.” After a check-up, the axle will be guaranteed for another three years.
Reliability, efficiency and low maintenance are still the keys to success for BPW’s products, a century after the Kotz family founded the company. Members of the family are still on the board, and the factory still stretches along the Wiehl River. But BPW is one of those German companies that has successfully made the transition from local shop to international success.
Michael Lawton
a journalist based in Köln
photos BPW and Getty Images